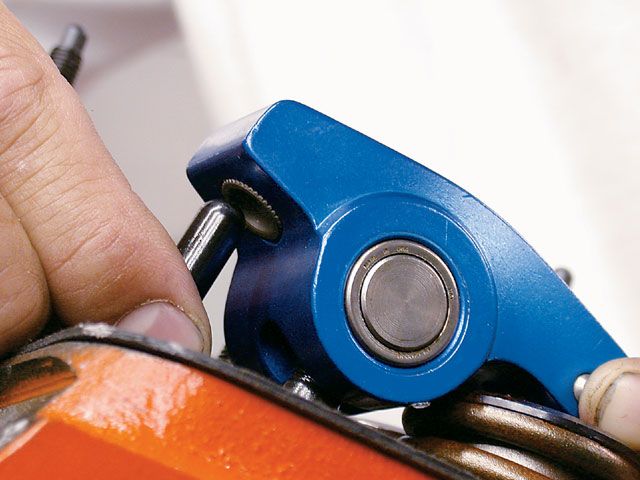
(Image/Super Chevy)
I just bought a cool ’70 Camaro with a 396 motor in it. The guy I bought it from said it had a “hot rod” camshaft in it. It idles like it has a big cam but it also ticks like there are one or two valves that might be loose. I don’t even know if the camshaft is a solid or a hydraulic. Since somebody else put it together, how would I know if this is a solid or a hydraulic cam? Any suggestion on where to set the valves? I know a little about engines but with no information, I’m at a standstill.
T.F.
Jeff Smith: I think this happens a lot more than people realize as cars are bought and sold with little documentation.
Let’s start with some basics that should allow you to figure out first whether the cam is a hydraulic or a mechanical lifter, and then how to adjust them.
The first thing to do is warm up the engine to a normal 180-degree water temperature, then shut it down, and remove one valve cover. The parts will be hot, so work carefully.
You’re looking for rockers that may appear to be loose with clearance between the rocker and the valve tip. You might want to bump the engine over (disable the ignition first), and check at least half of the rockers when the individual lobes are on their base circle (valve fully closed).
If all the valves appear to be loose on both sides of the engine, then it’s possible the engine has mechanical lifters and the looseness is the clearance or lash that is required with the engine warmed up. Next, use a feeler gauge and measure several valves to establish if the clearance is close to 0.018- to 0.020-inch. If so, then there is a good chance the engine has mechanical lifters.
Use of roller rockers does not indicate mechanical or hydraulic as roller rockers can be used with either type of camshaft.
If, on the other hand, the rockers seem tight on all the valves (with the valve fully closed) then it’s more than likely that the engine is equipped with hydraulic lifters. Hydraulic lifters use what is called a preload that eliminates clearance between the rocker and the valve when the valve is closed.
This means, on older engines with an adjustable valvetrain like your big-block Chevy, your preload must be set. Afterward, there’s no subsequent adjustment required unless the rockers are removed.
Hydraulic lifters use preload to compensate for growth as the engine warms up. An all-iron engine might expand as much as 0.006-inch or so from cold to hot while an all-aluminum engine might expand twice that distance, or roughly 0.012 to 0.015-inch!
For mechanical lifters, the clearance, or lash, is partly used to compensate for this growth.
Hydraulic lifters use a small piston inside the lifter that travels up and down inside its bore. Preload pushes the piston down roughly 0.025-inch, or slightly more. This moves the little piston closer to the bottom of its travel, but this is more than enough to compensate for a cold engine so that the valvetrain doesn’t rattle when the engine is cold.
Engines with a fixed valvetrain, like the LS engine family for example, bolt the rockers down to the cylinder head with no adjustment. There is still hydraulic lifter preload, but it is set by the length of the pushrod. A longer pushrod would depress the lifter more than a shorter pushrod. So pushrod length becomes very important on these engines. For example, changing the head gasket thickness would alter the preload on the lifter!
The EO – IC Method
On an engine with an adjustable valvetrain and hydraulic lifters, you can set the preload easily through a simple procedure that doesn’t require running the engine with the valve covers removed. This makes a mess because the oil goes everywhere.
There are several ways to accomplish this, but we prefer a method we call EO – IC. This stands for Exhaust Opening and Intake Closing.
Start at the front of a fully warmed engine on one side with the valve covers off. Have a friend bump the engine and watch the rocker arms. We like to start at the front of the engine and work our way rearwards, one cylinder at a time. As the exhaust rocker begins to open (EO), you can adjust the intake lifter on the base circle. Adjust the rocker until you eliminate all vertical clearance between the rocker and the pushrod.
This is considered zero lash. Then, tighten the adjuster a quarter-turn.
Now bump the engine until the exhaust runs through its full lift-cycle and the intake opens past maximum lift. Turn the engine slightly more until the intake is roughly half-closed (IC).
At this point you can set the exhaust preload.
Run down each cylinder like this until you’ve adjusted all the valves. If you’ve never done this before, it may take 30 minutes or more. I prefer to take my time and make sure all the valves are adjusted properly. It’s worth the time to do this correctly.
Sometimes, finding zero lash is the hardest part of the exercise because some used lifters collapse easily against even the slightest bit of pressure.
If the cam uses solid or mechanical lifters, the procedure is the same, except—instead of setting preload (which can’t happen since there is no plunger on these lifters)—you will set a clearance between the rocker arm and the valve with a feeler gauge.
The lash should be set to the spec by the cam manufacturer. If you don’t know anything about the cam, start with 0.020-inch for both the intake and exhaust. That’s a common lash figure.
Note how well the engine idles—you might even use a vacuum gauge and take a vacuum level reading. Long-duration cams with lots of overlap produce lower intake manifold vacuum at idle. Setting the lash evenly will measurably improve idle vacuum.
Properly adjusting the lash or the hydraulic preload should eliminate that annoying ticking sound which often stems from a loose adjustment. This can also occur due to a bent pushrod, which will obviously change the pushrod’s length and affect the adjustment.
It’s a good idea to check all the valves for any potential problems before you go through the effort of adjusting them. If you find a bent pushrod, look for obvious clues as to why the pushrod was bent. We’ve seen badly worn rocker studs that allowed the pushrod to slide off the edge of the valve tip and cause problems, so look for any obvious signs of wear or damage.
Should you follow this procedure, your engine should not only run quieter, but better as well.
Hello there.
I have a foxbody mustang with a 351 windsor. Has 10 to 1 pistons, aluminum heads, comp 292 H cam, comp hydraulic lifters, comp roller valve train, hardened comp push rods, 780 cfm carb.
Car runs strong. However the last time I drove it and stepped on it, the engine had a different sound to it. A bit of a rattle sound is a strong word but did sound different.
Because it’s a hydraulic cam, I would thing the valves should not need adjusting but I think that is what I’m hearing.
Could they need adjusting even with hydraulic lifters?
With 10:1 compression the rattle you hear could be detonation if the gas your using is sub 91 Octane or if you have carbon deposits building up.
JEFF, I HAVE A GM 350 H04 290 HP FLAT TAPPET CAM ENGINE AND NEED TO KNOW FROM 0 LASH HOW FAR DOWN ON THE ADJ NUT TO GO. CANT FIND THE INFO ANY WHERE THANKS MUCH
Steve
A 1/2- to 3/4-turn on the adjustment nut will properly preload the lifters. This is from zero preload with the lifter on the base circle of the cam.