When it comes to properly tightening automotive fasteners, there are several methods you can use.
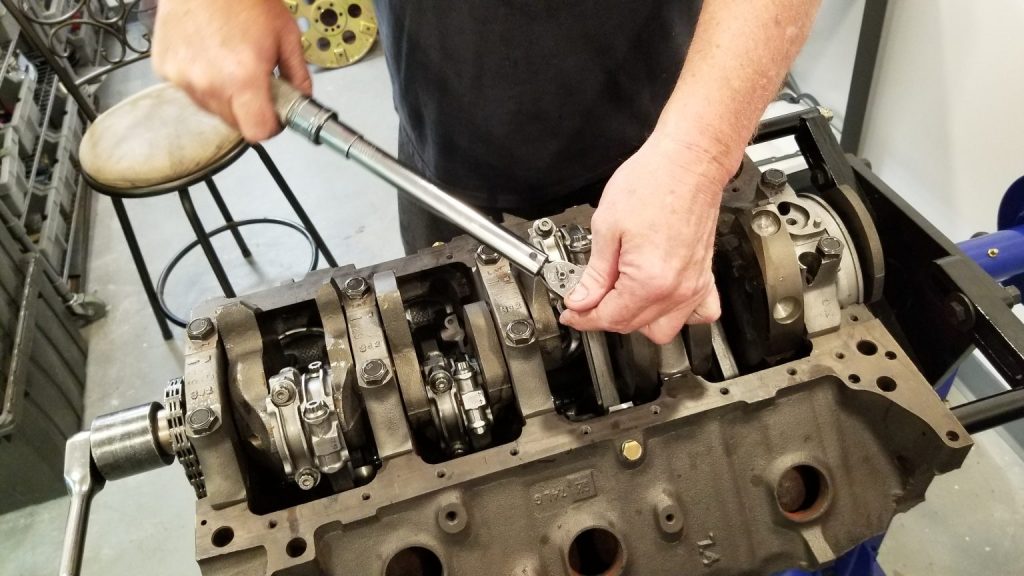
The most accurate way is to use a stretch gauge to measure the overall stretch of a fastener. This ensures the bolt has been stretched to achieve the proper amount of clamping force without being over-tightened. The problem is most bolts aren’t accessible at both ends—a requirement for using a stretch gauge. Consequently, most of us rely on our trusty old torque wrench for properly installing fasteners.
And that’s where the “friction factor” comes into play.
The “friction factor” is the amount of friction present when tightening bolts and hardware. When using a torque wrench, this factor can change dramatically each time you tighten or loosen a fastener, lessening each subsequent time. The difference between the amount of preload achieved on the first installation of the fastener and the amount of preload achieved on subsequent torque/loosen/re-torque cycles is known as “preload scatter.” According to ARP, it is not uncommon to see preload scatter in the range of 4,000-8,000 pounds between the first and tenth pull on a new fastener. Without locking in the proper preload, the fastener will be susceptible to failure.
The “friction factor” has a direct effect on the amount of preload scatter. Eventually, the friction levels out and preload scatter diminishes from cycle to cycle. According to ARP, there are three elements that contribute to the amount of friction present.
Assembly Lubricant
The main factor in determining friction in a threaded fastener is the lubricant used for a particular installation. Again, friction is at its highest point when a new fastener is first tightened, and this friction inhibits the fasteners ability to achieve the required preload on the first several cycles. In fact, ARP’s in-house Research and Development department has proven that new fasteners using motor oil and other commonly used lubricants such as Moly and EPL typically require 5-7 cycles before final torquing to level out the initial friction and achieve the required preload. While slicker lubricants may reduce the torque required to achieve optimum preload by as much as 20- to 30-percent, ARP says they also compromise preload repeatability and increase preload scatter.
Preload repeatability and preload consistency from a fastener to fastener perspective should ultimately be the number-one consideration when choosing a fastener assembly lubricant. Preload repeatability is the foundation for maintaining round housing bores, and preload consistency ensures the same preload from one fastener to another across a large area, such as the deck surface of a cylinder block. That’s why ARP offers its own fastener lubricant, ARP Ultra-Torque, that offers a combination of friction reduction, preload repeatability, and preload consistency.
Fastener Surface Finish
Automotive fasteners come with a variety of finishes, including black oxide, polished, chrome, zinc-plated, and anodized. Each one of these finishes behaves differently during torquing and loosening, and can affect the amount of friction involved. It’s important to follow the manufacturer’s recommendations with each fastener.
Receiving Thread Condition
The condition of the receiving threads also affects the amount of friction. Burrs and debris in the bolt holes can make a huge difference in the amount of torque required to achieve optimum preload, so all bolt holes should be thoroughly cleaned using special “Chaser Taps” to optimize the threads.
By taking into consideration the three factors above, you’ll achieve proper fastener preload time after time. We’d also be remiss if we didn’t stress the importance of taking care of your torque wrench and having it checked for accuracy every so often. Even the most-expensive torque wrenches can lose accuracy after a while.
Comments