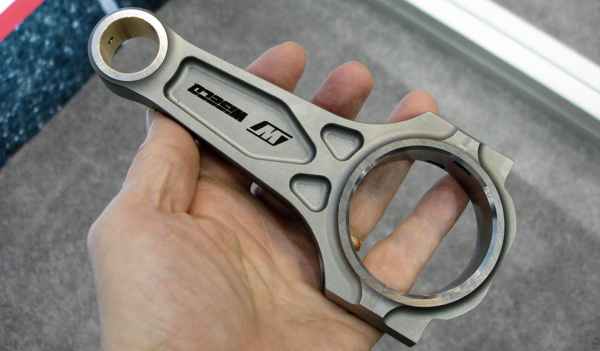
Steel or aluminum? H-beam or I-beam? And don’t even get us started on rod length and rod ratios!
Yes, there are a lot of factors that go into choosing the right connecting rods for your engine. Proper rod selection is undoubtedly one of the most important decisions you can make when building an engine. Connecting rods not only affect how your engine fits (or doesn’t fit) together, they also play a role in engine performance and longevity.
That’s why we turned to the experts at Eagle Specialties, Lunati, and Callies Performance for tips on how to choose the right connecting rods for your engine and application. Not surprisingly, horsepower and torque are major factors in the equation. According to Alan Davis of Eagle Specialties, it’s not just about overall power and torque levels, but also the way power is made.
“Horsepower, torque, and rpm are all things to consider,” Davis said. “But you must also consider the application and the environment the engine will be used in and how the power is made. For instance, a 600-horsepower, naturally aspirated engine that turns 10,000 rpm will have far different stresses than a 600-horsepower, supercharged engine or a 400-horsepower engine with a 200 shot of nitrous.”
Depending on the application, different types of stresses are applied to the connecting rods. For example, large amounts of torque will yield heavy compression and bending loads on the rods. High rpms, on the other hand, cause mostly tensile-loading or stretching forces. In most cases, connecting rods don’t fail on the compression stroke; rather, they break apart on the exhaust stroke at high-rpm operation due to tensile loading.
“This (tensile loading) is also much harder on rod bolts than horsepower and torque,” Davis said. “Other factors to consider are piston weight and the stroke of the crankshaft. Also, different fuel and nitrous use will have a different effect on combustion and how the load is delivered to the rods.”
In addition to engine power and rpm levels, other factors important to connecting rod selection are:
- Application: street, drag race, endurance racing, etc.
- Engine dimensions: stroke, rod ratio, piston height, etc.
- Rod weight vs. reliability
- Budget (for most of us, it plays a role)
All of these things will help determine the rod length, material, and configuration that’s best for your application.
I-Beam vs. H-Beam
There are two basic styles of connecting rods: I-beam and H-beam.
Most stock connecting rods are I-beam. Stock V8 connecting rods can handle upward of 400 horsepower and 6,500 rpm. Once you exceed those performance levels, you’ll need to consider aftermarket connecting rods. Depending on the type of steel used (we’ll get more into that below), aftermarket I-beams can handle hefty compressive loads, offer good tensile strength, and are often more lightweight than H-beams.
The connecting rod’s ability to handle compression loads and tensile loading is dependent on the cross-sectional area of the beam. Therefore, aftermarket I-beam rods typically have a thicker cross-section in critical areas to increase strength. H-beam connecting rods, however, use a completely different design to increase stiffness and strength.
H-beam connecting rods incorporate two large, flat sides with a thin section in the middle. This design makes these rods more rigid and able to handle compression forces.
“H-beam is a stronger design when bending stress is considered,” Davis said. “H-beam rods are more difficult to machine, so they are often more expensive. I-beam rods are easier to produce and can sometimes be lighter than H-beams. All other variables being equal, H-beam rods are the strongest design.”
Whether you choose H-beam or I-beam, overall strength and reliability is dependent upon the material, weight, and cross-section of the rods, said Nick Norris of Callies Performance Products.
“All of our I-beam, and some of our H-beam rods have a tapered beam design,” he said. “Our H-beam design is a very good part that is typically 20 grams lighter than our I-beam in the standard configuration. We consider our I-beam to be the heavy duty rod due to larger material cross sections and pin support structure.”
So what about materials?
Steel vs. Aluminum vs. Titanium
When it comes to connecting rods, the main material options are steel, aluminum, and titanium. Again, the right choice for you will depend on the variables (power, rpm, application, etc.) above.
Steel connecting rods are made with various types of materials and manufacturing processes. For example, cast steel connecting rods were used in many 1960s and 70s vehicles, but they are not great for any type of performance applications. Most aftermarket steel connecting rods are made from forged steel.
There are different types of forged steel based on the grade of material. Eagle Specialties, for example, uses a 5140 steel for its entry-level rods. For more highly modified competition applications, most manufacturers, including Eagle Specialties, utilize high-carbon 4340 or 4330 steel.
“For high-end competition, our rods are forged and heat-treated to SAE/ASTM specification 4340 steel,” Davis said. “This specification allows for some variation in alloying elements. Eagle has held our steel to a tighter tolerance and have achieved a slightly higher yield strength than ‘typical’ 4340 steel.”
Depending on the specific material, steel connecting rods are suitable for most applications.
Aluminum rods can be as much as 25-percent lighter than steel rods, making them a popular choice with racers. The lighter weight reduces the overall mass of the reciprocating assembly, allowing the engine to rev faster and higher. According to Davis, aluminum is also a great choice for supercharged applications.
“Aluminum, while not as strong as steel, is often used in very high power blower engines,” he said. “This is due to the fact that aluminum ‘gives’ slightly under violent combustion and acts like a ‘shock absorber’ so that the harmful shock of combustion does not propagate to the rod bearing and cause a bearing failure.”
The downside to aluminum rods is their fatigue life. Aluminum connecting rods have a more limited service life than steel and can begin to stretch, especially when they’ve made many passes down the dragstrip. However, many aluminum connecting rod manufacturers argue that a good set of aluminum rods can last up to 100,000 miles in street applications. So it really comes down to your application and budget. If you’re a racer and can afford to change out rods more frequently, aluminum is a good choice. If you’re on a budget or if your engine is a high-torque, low-rpm mill, steel may be a more cost-effective option in the long run.
Titanium is a third option.
Titanium connecting rods combine the lighter weight of aluminum with strength that’s more comparable to steel. That makes them a viable option for drag cars or sprint cars that require quick throttle response. However, they are very expensive.
“Titanium is slightly weaker than steel, but due to the extremely light weight, far less stress is realized,” Davis said. “So effectively, titanium can be considered stronger as far as the entire system is considered. It is a tricky material, though; and it doesn’t come without a price. And I’m not just talking about dollars.”
Special Treatments
Connecting rod material is the only thing that determines strength.
“These are important factors, but don’t even come close to telling the story,” Davis said.
You’ll also want to make sure the rods have been heat-treated, which is required for a material to meet most SAE/ASTM specifications. Shot peening is common and an absolute must for machined or forged parts, according to Davis. Polishing helps reduce microscopic pits, inclusions, and lead to extended fatigue life; however, it must be done properly. Aggressive grinding or polishing can actually do more harm than good.
Cryo-treatment is another finishing process. This can be thought of as an extension of the heat-treatment process. Cryo-treatment essentially cools the material to a much lower temperature than room temperature right after the heat treatment ends. According to Davis, the benefits of this process is a marginal strength increase by about 2-3 percent and increased wear resistance.
Rod Length and Rod Ratio
Rod ratio is the length of a connecting rod (center to center) divided by the stroke of the crankshaft. This number can have a direct effect on power, torque, engine efficiency, and piston wear.
Here are some common stock connecting rod lengths:
CHEVY
FORD
As a general rule of thumb, lower rod ratios are associated with lower-rpm engines. Higher rod ratios typically work with high-revving, high-rpm engines. Generally speaking, the rod ratio for gasoline-based, automotive engines operating in typical rpm ranges will be about 1.45:1 –1.7:1, with some race engines up to a 2.1:1 rod ratio.
There are a couple schools of thought with rod ratio.
“The higher the maximum rod angle (and lower the rod ratio), the more piston side-loading you will have,” Davis said. “This results in higher friction, and accelerated piston skirt wear. However, before you throw the longest rod in everything you build, understand that lower rod ratios tend to “mix” the air/fuel better in the cylinder due to more aggressive piston acceleration. This can result in higher efficiency, torque, and power can be the result.”
According to Norris: “It’s still more typical to use the longest rod available to work within the stroke, the deck height, and available piston-compression heights. This helps keep the piston weight down, and in turn, the stresses on the connecting rod. An instance where that may not hold true would be a boosted or heavy nitrous application where the piston would need more compression height to allow the ring pack to be moved down.”
Most agree that rod length/rod ratio selection should be part of a larger equation.
“The length of the rod has an effect on the dwell time of the piston at TDC,” Norris said. “In cases where the stroke is short enough to allow some flexibility in rod selection, it can be factored in with port flow, valve timing, and rpm range to optimize the engine for a specific application.”
A Quick Word on Rod Bolts
It is imperative that you pay attention to the connecting rod bolts when you purchase and install your new connecting rods. These bolts are the single highest-stressed fastener in your engine, according to Davis.
“We use ARP 8740, 2000, L19, and Custom Age 625+ materials,” he said. “Just like choosing the correct bolts is important, following manufacturers’ instruction for tightening, lubrication, and care is also vital to the bolt (and your engine’s) life.”
Avoid over-stretching the rod bolts during engine assembly. When new rod bolts are installed and tightened down to fit bearings, make sure to use the right lubricant on the threads.
By choosing the right connecting rod material, size, and style (and don’t forget the right bolts, too), you’ll ensure maximum performance and reliability from your engine.
What more could you ask for?
Hello
I agree that many factors influence the selection of the right connecting rods for my engine. It is good that there are special books that help with the study of such issues. So as not to read bad books, I read the reviews on these books first. I buy reviews from the company http://www.uk.papersowl.com; then I read reviews on books, then I choose the best book and read it. After reading the book, I become a guru that knows all about questions that interest me!
I like it
Like it)
http://blog.rismedia.com/2019/viral-marketing-real-estate-agent/
https://mamsouq.com/ to win free products like bluetooth earphones and luxury watches
I love to read about farming and all those things. Well, nowadays I am writing an article based upon the work of veterinary and farming or fields. For this, I am using the services of Edu Birdie website and they asked me to gather some information about the farming or veterinary.
https://www.onallcylinders.com/2015/09/11/rod-school-how-to-choose-the-right-connecting-rods/
I have knowledge of this because I have done the course of auto designing and I write on this rod and made a design of this. But now I have left the designing work because I am not earning huge money in this. Thanks, Gustavo Woltmann
Hi there Sir
Tks for sharing the fundamentals of Conrad design, and bolts
Thank you this is a lot of wonderful info.
I am building a dodge 360 30over n looking for best forged pistons n rods for my build, can you help?
As far as rod length goes, honestly it is less important than people make it out to be. People have over-thought this subject to death, actual dyno tests show that the gain in HP is small, if any. The theory that short rods make more low-end torque has been debunked(i.e. Engine Masters). The short rods actually made more power up top in there testing, I know the keyboard commandos know more than pro engine builders. I will tell you this, if you want to make great power think: induction, cylinderheads, camshafts and exhaust.
thanks! that’s useful
I want buy a connecting rod but I don’t know what size I should. Bc my broken one “ ave” “28 31” from craftsman riding mower LT3000 20 hp And how do I choose number ?can buy same size. Your truly Tony