I don’t know if this is the right spot for a question but will a 16-inch electric fan cool a 1993 C1500 in the summer?
J.P.
Jeff Smith: The easy answer to this question is a qualified yes, but we’d be selling you short if we simply left it at that. The real answer to your question involves a bit more detail. After you’ve chosen the fan you want to run, we have to start with the fan’s location.
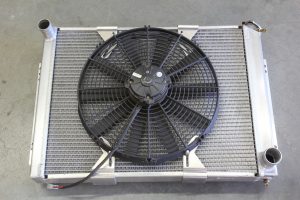
Here’s a photo of a typical 16-inch fan mounted without a shroud on an aluminum radiator. You can easily see that the fan will only pull cool air through the portion of the radiator covered by the fan. If we install a fan shroud in between that covers the entire radiator, the fan will be able to pull cool air through the radiator’s entire core. Simple, no?
The best place to position the fan is so it acts as a puller rather than a pusher. Fans that pull air through the radiator operate roughly with a 10 percent advantage. Sometimes however, placing a single large fan in the middle of the radiator creates clearance issues with the accessory drive – generally the water pump pulley. You might be able to offset the fan slightly on the radiator, which can produce the clearance necessary. As a last resort, you can place the fan as a pusher. Be aware that electric fans are sometimes designed strictly as either pushers or pullers. Dedicated pusher or puller fans use a blade that will be most efficient in their intended direction.
In addition to making the fan a puller, typically a single large fan will not cover the entire face of the radiator. The whole idea behind any fan is to create a low pressure area behind the radiator which then uses atmospheric pressure to push the air through the radiator, which transfers heat away from the cooling tubes and fins. The best way to maximize the efficiency of any radiator is to pull air through every square inch of the radiator’s core.
A typical crossflow radiator might measure 22 x 18 inches which equals nearly 400 square inches of cooling surface area. A 16-inch round fan covers only 201 square inches, which is only half of the total surface face of the radiator. If the fan is affixed directly to the core’s face, this will only pull air across half of the radiator in low-speed driving when you need maximum cooling.
The solution is to find a shroud that will cover the entire face of the radiator core that can then mount the cooling fan. This will allow the fan to create low pressure over the entire back side surface of the radiator’s core. For example, Summit Racing offers a universal aluminum shroud that measures 22 inches wide and 19.5 inches tall that would come very close to a perfect fit on the above example radiator core. You could then mark a position for the fan and mount the fan directly to the shroud. These shrouds are constructed of sturdy 0.125-inch (1/8-inch) thick aluminum and can easily accommodate mounting an electric fan.
Another consideration you might want to keep in mind would be to add pressure-relief flaps to this shroud. The shroud is designed to help pull air through the entire radiator face at low speeds when the car is in traffic. But at highway speeds, the solid shroud could cause overheating issues because it can block air from efficiently exiting the shroud. By adding rubber flaps roughly 2 inches tall x 3 inches wide in all four corners of the shroud, the flaps will allow air to exit at freeway speeds yet will remain closed when the fan is running. If you look at dual electric fan shrouds like those from Spal for example, you can get an idea of how this simple solution works.
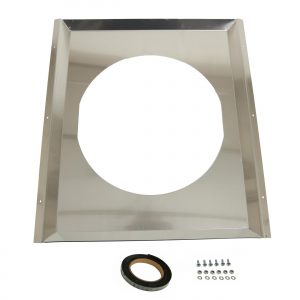
This Summit aluminum fan shroud is designed to mount a single 16-inch electric fan to a radiator. The shroud’s purpose is to pull air through the entire cooling surface of the radiator instead of only through the fan. Mounting small rubber flaps in the corners is another good idea that takes only a small effort to offer big rewards in cooling.
So now that we have an idea of how to mount the fan, perhaps we should also look a little closer at how to properly wire the fan. Many old school installers prefer to wire the fan directly to a switch under the dash. Spal engineers told us a story about a customer complaint that illustrates this point. The customer had installed a pair of 12-inch fans in his car but said his engine would die at idle when he triggered the fans. Questions from the engineers revealed the customer had wired the hot side of his switch directly to the fuse box. When both fans were triggered by the switch, the instantaneous electrical load was so great that the voltage dropped so far that it cut out the ignition.
The engineers first suggested that he wire each fan separately through a 30-amp relay and then use a 185 degree switch mounted in the engine to trigger the first fan. The second could be wired the same way to a 195-degree thermal switch. This way, only one fan would be triggered at a time and the load could then be easily carried by the charging system. All electric motors pull high instantaneous amperage when first triggered until the motor speeds up and the voltage increases.
This, of course, brings up the topic of your charging system. Even a single 16-inch diameter electric fan will pull upwards of 30 amps. This load by itself isn’t all that daunting. But add an electric fuel pump, a heater or A/C blower fan, headlights, and a few other electrical accessories and the charging system may need to be upgraded. That description could easily outstrip the output of an older ‘60s alternator that can barely put out 60 amps at 2,500 rpm engine speed. Current late model alternators are designed to deliver roughly 80 percent of total output at idle, which is often when the electrical load will be the highest.
Here’s a quick test you can perform to see if your charging system is up to the task. Start your engine and allow it to idle and measure the voltage of the charging system at the battery. It should be 14.2 to 14.5 volts. Now turn on all the electrical devices on the car including the electric fan(s). Measure the voltage again at the battery. If the voltage now had dropped to 13.0 or less volts, the charging system is struggling to maintain the proper voltage because of the increased amperage draw.
Now check the voltage at the alternator with the load still applied. If the voltage is more than 0.40 to 0.50-volt higher at the alternator than at the battery, the charging wire from the alternator to the battery is either too small or has high resistance. As an example, let’s say the alternator is cranking out 14.2 volts at the output terminal but the voltmeter reads only 13.2 volts at the battery. This means somewhere in the charge wire circuit (or its connections) there is excessive resistance between the alternator and the battery. This resistance is reducing the voltage supplied to the other electrical accessories.
This may not seem like a big deal, but if you reduce the operating voltage from 14 volts to less than 13, any electric motor will run slower and less efficiently. That means if this were an electric cooling fan. It will not be able to cool nearly as well as it could if there was 14.0 to 14.2 volts available at the fan.
As you can see, there’s quite a bit to remember when it comes to installing a simple electric cooling fan and why this answer has so many complex connections. Addressing all these issues will not only create a more efficient electric fan, but it will also mean you will keep your cool this summer when the heat is on.
Ok…. I’m going to ask a common question… I have serious cooling problems in my v8 vega. I need a radiator 25×18.5 with a trans cooler. Which one is best for me??? Engine is a 350 aluminum heads .480 lift cam 2500 stall with a hughes performance turbo 350…. psychological. Air-conditioned…
IF you are using an aftermarket serpentine system i.e. March make sure that you are running the full size bottom pulley not a smaller under drive pulley. I found out the hard way, under drive runs at 66% while the large will turn the water pump at 100%.
thank you ,your article answered my question pertaining to my issue
I have about 1/2 inch or 1 inch gap between Schroeder & radiator. Is that ok
Hi I’ve been told by a cooker engineer that we need a fan installed between our kitchen and our conservatory as we have received a safety warning with regards to our gas hob.
yes kathy, you need to cool down your hob.
I have a 405 blower motor in my truck it seems to be running hot i have a fan/shroud on the back the front have a trans cooler mounted i am wanting to install a fen on the front. will this help it run cooler?
Thanks
Gary