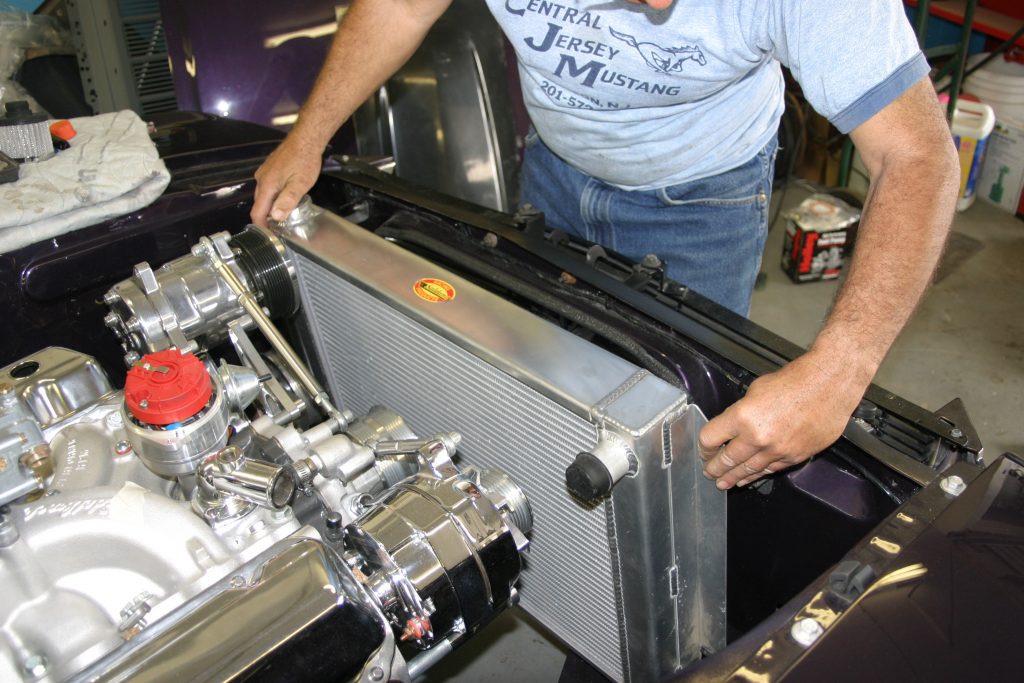
There are many myths and misconceptions about engine cooling, but the truth is your engine’s cooling system must perform a balancing act. It needs to extract enough heat to keep your engine happy, yet maintain enough heat to keep it operating efficiently. That means keeping the engine in the 180- to 210-degree F range.
To achieve and maintain optimum temperature range, a good cooling system needs the right-sized radiator and fan combo. It must also have the appropriate water pump speed and coolant flow between the engine and radiator.
Typically, when engines overheat or run too cool, it’s because of these cooling systems myths and misconceptions. Here are some of the more common myths and mistakes and why you should avoid them.
Eliminating the Thermostat
One of the greatest — or perhaps worst — cooling system myths is that you can remove your thermostat to eliminate overheating. This will only add insult to injury! When coolant never has a chance to give up heat via the radiator, it gets hotter and hotter, especially if you’re stuck in traffic. And even on the open road, coolant never has a chance to park in the radiator long enough to give up heat energy to the atmosphere.
Never operate your engine without a thermostat!
Thermostat selection boils down to application. Although enthusiasts tend to choose a 160-degree F thermostat to treat overheating issues, the 160-degree thermostat was originally intended for alcohol antifreeze back in the day. The best thermostat for classic vehicle applications today is the 180-degree thermostat. If you’re experiencing overheating with a 180, you have deeper problems with other components. Late-model computer-controlled vehicles mandate the use of a 192- to 195-degree F thermostat.
Water is the Best Coolant
Another myth is that water is the best coolant.
This is true in terms of heat conduction; however, it is also the best source of corrosion. If you are using straight water, you should always add water pump lubricant and a corrosion inhibitor. Also, use a coolant enhancer like Water Wetter, which improves surface tension and heat conductivity.
Coolant manufacturers often suggest a 50/50 mix of ethylene glycol and water, which will protect your cooling system down to -34F. If you’re expecting temperatures colder than that, you need a block heater or a warm garage. Mark Jeffrey of Trans Am Racing in Southern California tells us he runs 100-percent ethylene glycol and no water without consequence and has been doing it for many years. His logic is coolant temperature runs only marginally higher and this approach eliminates any risk of corrosion.
If you opt for the 50/50 mix, you can buy antifreeze already mixed with water for the sake of convenience. If you’re going to run an ethylene glycol and water mix, it is suggested you run distilled water to keep minerals out of your cooling system.
Summit Racing offers you another coolant option known as Evans High Performance waterless coolant. This is the last coolant you will ever have to buy because it is permanent. You run 100-percent of it in your vehicle’s cooling system. Begin your Evans regiment with new hoses and cooling system components and a system that is bone dry. If you’re servicing a system with traces of ethylene glycol and water, the Evans Coolant Conversion Kit is the best way to get started.
Improper Coolant Filling
We’ve seen a lot of people either under-service or over-service coolant.
When you are servicing a cold engine, you should add coolant to one inch below the filler neck which allows for expansion as the engine warms. Coolant can rise as much as one inch as the engine warms up. Start your engine with the radiator cap removed and coolant one inch below the neck. Then, observe as the engine warms. Allow time for the thermostat to open and for the engine to burp any stray air pockets.
No Anti-Collapse Spring
There are those, including hose manufacturers, who believe you don’t need an anti-collapse spring in the lower radiator hose. The truth is, you must have an anti-collapse spring in the lower radiator hose if you have an older vehicle with a conventional cooling system.
Because the lower radiator hose channels coolant to the water pump and engine, it is susceptible to negative pressure and collapse at high rpm. The anti-collapse spring prevents that from happening. One hose manufacturer says you don’t need the anti-collapse spring because it was used only for factory-fill purposes. This has never been true because of the positive pressure on the lower hose during fill.
Always run an anti-collapse spring in the lower radiator hose.
A Faster Fan is a Better Fan
There are many myths regarding electric fans. One belief is the faster a fan turns, the better — which is not completely true. At high speed, the radiator slipstream should be strong enough to carry heat from the radiator. When air is moving too fast, you get into boundary layer issues where heat doesn’t get carried away because air isn’t actually touching fins and tubes.
You want air to move slowly enough across fins and tubes to where it carries heat away. At speeds above 40 miles per hour your engine doesn’t need a cooling fan. This is why a thermostatic clutch fan or electric fan works best.
More Fans are Better
Some folks believe more fans are better. But that isn’t completely true, either. You don’t really need a fan both behind and in front of the radiator. Ideally, you will have a fan behind the radiator that provides cooling capacity based on coolant temperature. If your vehicle needs two cooling fans, there’s a deeper problem than fan capacity.
Improper Fan Spacing and Shrouding
One rule we see broken time and time again is fan spacing and shrouding. In most cases, cooling fans should be shrouded for proper vectoring of air velocity through the radiator. We recommend you pay close attention to what the factory does in any application.
Overlooking the Radiator Cap
Aftermarket radiators are popular upgrades, but you should also pay attention to your radiator cap.
Your coolant is under pressure to keep the boiling point as high as possible. That’s why you you want the highest pressure cap rating suitable for your application. Caps for older vehicles should be rated for 7-12 pounds; newer vehicles should have radiator caps rated to 12-18 pounds.
Cheap is Cool
It’s cliché, but you get what you pay for. When replacing cooling system components such as hoses, the water pump, and thermostat, don’t do it on the cheap. Spend good money on the best components and sleep better. Goodyear Super Hi-Miler cooling system hoses last longer than your average off-the-shelf hose, especially when paired with high-quality worm gear clamps.
You can find a wide variety of water pumps for nearly every application imaginable. Regardless of what brand of pump you choose, always opt for a high-flow water pump and be mindful of pulley ratio (pump speed).
Now that you know what pitfalls to avoid, scroll through the slideshow below for some valuable tips on choosing cooling system components.
[…] Losing Your Cool: 9 Cooling System Myths and Mistakes — and Why to Avoid Them! […]
Opening a myth’s story with a myth? The thermostat does one thing and one thing only. It regulates the MINIMUM water temperature. The “slowing down the coolant” myth is a leftover from the Flathead Ford days when it was necessary to force coolant to flow at the rear of the motor. While it is important to use the proper thermostat to ensure that the engine reaches proper operating temperature for more efficient combustion and lubrication, the elimination of the thermostat, in itself, not only will not but, by the laws of fluid thermodynamics in a closed system, CAN NOT cause overheating. What it WILL do is reduce the temperature differential between the hottest and coldest points in the system. With my regards to the esteemed Mr. Smart and the myriad of folks who will swear on a stack of Bibles that this has happened to them I shall now don my “flame suit” and return to my laboratory.
Amen. I was just about to correct them also and saw your comment first. Unbelievable they posted an article specifically to bust myths and actually included two. Their other point that is incorrect is their belief that slower air past radiator fins cools better than fast air. Where do they find this crap?
Slower air DOES cool better. Heat transfer takes time. There’s a reason a single combustion cycle in an engine is considered adiabatic; there isn’t time for it not to be.
Faster air causes turbulence as you pass the Reynolds number of about 10000, depending on the application. A turbulent boundary layer means worse cooling. Period. There’s a reason all the manufacturers shut off their fans at high speed now. You’re TRYING to keep it laminar as often as possible.
dear kyle , are you sure that laminar flow intercange is better than turbulent flow? who say you this? more speed = more air/time = more heat exchage/time = low final air temp that no mean less heat exchange , in high Reynold numbers better inter change , in laminar flow the temp in layer near the surface is similar to the temp of surfe , that mean the gradient is small that mean the exchage is more slow.
I hope its was legible , sorry for my english
Dear Kyle, because you blow the soup when it’s hot, with this it is increasing the REYNOLDS NUMBER, AND IT WOULD COOLER SLOWLY.
Although this example is far from aerospace engineering. But I think it is didactic
3 pieces of misinformation here:
1. The idea that removing the thermostat causes the coolant to move so fast that the heat can’t be disappated because the water isn’t in the radiator long enough?
One only needs to look at the engine side to expose this nonsense, if the water is going too fast for heat transfer, it’s not going to be able to extract any heat from the engine either with the result the water would stay cool and the engine heating up into a red hot block……..Doesn’t happen!
The faster the water moves through the system, the more heat can be transferred, that’s what the thermostat does, controls the rate of coolant flow. It does get to a point when no further increase in flow will create any further cooling rather than faster flow impeding cooling.
2. The same nonsense with the fan statement, faster air flow creates more cooling, always!
3. Water is not the best conductor of heat, it does however have one of the highest heat capacities of any fluid. Putting other coolants in systems that were originally designed for straight water(cars before 1970) requires either bigger radiators or increases in water pump speeds to create the same cooling when 50/50 mixes of water/glycol are used.
Good Lord. No.
As a general rule, ρAv=ρAV. So the significantly smaller tubes in the radiator mean significantly higher speed. There’s a reason the tubes are so long. It takes time to transfer heat. Similarly, metal to water isn’t the same as water to metal to air.
Faster air creates more cooling always? Go look at the Red hot space shuttle and try that statement again. Faster air creates more HEAT always. If you have shear, due to speed of the flow causing turbulence, you’ve lost heat transfer capacity. Period.
The third point is taken out of context. They say, specifically, that it’s the best COOLANT in terms of heat transfer. There are plenty of materials that have higher conductance, but they aren’t *coolants.* Especially not when used in the context of automotive engines.
ρAv=ρAV is just double talk. Surface area not constant flow rate is at issue.
Using the reentry of the space shuttle as an example of the reaction of air flow makes me wonder how much you understand what is going on. And yes, I studied physics. When a spacecraft reenters, very little heat is generated by friction (air passing by). Mostly what happens is, all the heat already in the air molecules piles up in front of the spacecraft leading edge. All air has a certain amount of heat in it, which is just another way of saying it has a certain amount of kinetic energy in all the air molecules wiggling around. Compress air quickly enough, and all the energy or heat gets concentrated in a smaller volume faster than it can radiate, conduct, or convect away. As a result, the air can get hot enough to glow caused by energy density not air flow.
If facts are of concern to you then note this chart. As the velocity of the car increases, air flow through the radiator increase is proportional. Note the increase in heat transfer performance. So in fact more air flow through a given radiator does not always mean more heat. In fact it means less. More heat is only formed when compression becomes a factor,otherwise known as the velocity boundary layer, then only when that overcomes the heat dissipation by volume.
The fact is, higher velocity will give you more heat dissipation until compression becomes a factor. The only other issue involved is the ability of the material to transfer kinetic energy. In simple terms, when air flow reaches the cores maximum ability to transfer heat, any increase is wasted.
What is not mentioned here is the fact that air flow across the engine surface also creates a cooling effect.
ρAv=ρAv isn’t double talk. At all. It literally means that at any cross section of a flow you take, that the total mass/time is constant. It’s LITERALLY one of the most important equations in fluid dynamics. Mass is conserved.
You trying to tell a literal NASA rocket scientist how space shuttles work is pretty well hilarious.
ALL drag is friction. You can’t “pile up” air in front of something if it has no friction.
Heat also isn’t synonymous with kinetic energy. At all.
Your claim that denser air means worse heat conduction is similarly hilarious.
More heat through a radiator ALWAYS increases the heating at the radiator. Compression isn’t the problem we’re talking about, it’s TURBULENCE. It’s about the Reynolds Number. Turbulent flow does NOT conduct heat the same as laminar flow.
We’re talking about a Fanno-Rayleigh flow.
The heat removed as the air crosses the engine’s surface is absolutely negligible.
Kyle, back to school for you.
You are completely confusing virtually unrelated scientific concepts, and applying them in some twisted fashion that does not resemble science.
Using the space shuttle re-entry as an example of why increasing turbulent airflow somehow increases heat at a heat exchanger, is absolutely awful.
First off,
During the
fastest/hottest part of the shuttle re-entry, a very energetic pressure wave develops at its leading
surfaces, and this energy density is enough to cause molecules
to dissociate, and ionize their atoms. It’s incandescent plasma.
Plasma largely doesn’t follow the
laws of conventional thermodynamics. The leading edges will experience extreme heating due to the pressure wave and electrostatic charging.
All of that has absolutely NOTHING to do with heat exchangers. Conventional thermodynamics apply, we are at conventional altitudes and conventional speeds. The faster and the more turbulent the air/water flow inside or outside an exchanger, the more exchange occurs. Period.
You are either a flat-out liar or have gotten very confused.
You do know know that humans can feel temp changes right? Let’s say your ac goes out and you have to use a fan. You aren’t cool so do you turn the fan up or down?
I’m an aerospace engineer. We’re uh… Pretty well trained with fluid dynamics.
You should try taking fluid dynamics past high school physics.
Your claim is that since heat cannot, if itself, pass from body to a hotter body, that elimination of the thermostat cannot mean overheating. Except the engine is ALWAYS hotter than the coolant. The entire idea is to distribute the heat throughout the cooling system, mainly the radiator, to *reduce heat in that system.* You WANT your engine as hot as possible.
The thermostat is an object in the flow. It will absolutely be a restriction. Thus slowing down the flow.
There’s a reason they hire us to design engines and cooling systems. It’s more in depth than Bernoulli.
I would like to call BS on the aerospace engineer thing, but who knows……. Not sure what rho*A*v = rho*A*V means.
When calculating heat transfer, the governing equation is Q=UAdT. Q is the rate of heat transfer (BTU/h or some other convenient units). U is the overall heat transfer coefficient (BTU/h*degF*ft2). A is the heat transfer surface area (ft2) and dT is the temperature difference between the two fluids on either side of the heat transfer tube.
U is made up of three components. There is the heat transfer coefficient from the fluid on the inside of the tube to the tube. The second is “resistance” to heat transfer through the metal tube wall. And the last is the heat transfer coefficient between the fluid outside the tube and the outside surface of the metal tube.
The resistance to heat transfer through the metal of the tube depends on the material of the tube (thermal conductance) and the thickness.
The heat transfer coefficient from either fluid to the metal surface is a function of fluid characteristics and velocity. Higher velocity results in higher heat transfer. This is primarily because there is higher turbulence at the tube surface, which constantly brings cooler (or hotter depending on which side of the tube) fluid into contact with the hotter (or cooler, depending again) metal surface.
Increasing the air velocity on the outside of the tube has a bigger effect than increasing the velocity of the water on the inside, because the heat transfer coefficient of water to metal surface is so much higher than air to metal surface.
Removing the thermostat will not make the water run hotter unless the pump begins cavitating, which is unlikely unless the pump is running at very high speed (for instance maybe in a race car engine). The other possibility is if the cooling system is a bypass system, which bypasses some coolant around the radiator when the car is warming up and the thermostat is closed. In this case removing the thermostat will result in constantly bypassing water around the radiator which will result in overheating. The rotary engines in Mazda RX7’s have this system.
This is how it works in systems like a car radiator. Heat transfer might be different with a space capsule, because of compressibility, supersonic flow and all that rocket stuff (which is as good as greek to me).
I have been designing heat exchangers in boilers for about 35 years now. I continue to have customers pay me to do this, so it seems that I have probably gotten this right a few times before.
Cheers,
Carl
You literally didn’t respond to any of my points. Utter illiteracy.
Carl is largely correct… except for the fact that removing a thermostat will decrease pressure in a system that needs pressure to help prevent DNB (Departure from Nucleatic boiling)… this basically means that nucleatic boiling (small bubbles on surface) is ok, but the moment it becomes film boiling, the steam creates an insulated surface of the block or head that is not in direct contact with the liquid coolant molecules any more. This film boiling also increases the chances of pump cavitation.
A thermostat’s role is to increase pressure, not actually to slow down flow.
personally, wihtout anythign other than basic wiht and without test, i can confirm a thermostat is required when the engine is operated in certain rpm bands for continuous times.
Wihtout a thermostat, my little toyota 4k powered jungle jeep will consistently, without fail, limb over the cpacity of my cooling system and start running away. With thermostat, everythign runs as it should. My reseach has shown that this is because at higher revolutions, the water pump will aerate the water if the water is not restricted. So i dont know whether or not this can just put all the myths to bed, but it must have some weight on teh argument.
Ive done the test about 60 times, and each time its absoultey certain that the thermostat is indeed helping keep the system wokring as designed.
Not really, radiator cap allows pressure to relieve (and build).
The pump doesn’t creat the pressure, expansion in a sealed system creates the pressure.
“True”,but a bypass thermostat (it’one of those with a DISK!!) CAN NOT,i said CAN NOT be removed; it MUST be there,or else the bypass part of the water just circles around the engine,and NEVER ,i said NEVER, getting to the radiator; true or false!
the chief has “spokin”
See Kays and London, Compact heat exchangers, pp27-29
I took mine out of my 69 Lincoln 460… Runs slightly cooler. I’ll evaluate more next summer @ 110° F
Laws of hydraulics apply here too brother. Crack a book.
I know this is old post but people still happen upon it. The thermostat also restricts the flow thru the engine which increases the pressure in the engine. The water cools the engine thru a process called nucleate boiling. https://en.m.wikipedia.org/wiki/Nucleate_boiling
The increased pressure reduces the size of the bubbles which increases surface area and heat transfer. Larger bubbles can turn into steam pockets which will not transfer heat efficiently and create hot spots. Higher water flow from a lack of thermostat will offset the lack of pressure to some extent by sweeping away the bubbles. Pressure has a larger effect on the bubbles than flow. The above forces are lost when the engine is shut down. This is why an overheating engine will pop the radiator cap right after shutdown.
No. An overheated engine will pop the radiator cap because there is no more circulation in the system to help cool it. The engine is hotter than the water at shutdown and aince the hot engine block has more mass than the coolant in the system, the coolant instantly starts heating up until everything reaches an equilibrium.
Like! I was the Global Lead for Powertrain Cooling at GM. Your statement is completely accurate.
Thank You for publishing this article. I’ve been buildings Engines for some 35+years,10 of which was in Daytona Beach;Florida.Being from New York[which was tough enough] I always believed in installing a 195 degree thermostat,not only for heating reasons but to maintain a complete balance across the whole Engine.Down south for some reason there convinced because they don’t need that much”Cabin Heat” you don’t need a thermostat.{These are the same People who refer to Engines as “Motors”}Every engine I’ve ever disassembled without a Thermostat was all “Gunked” up inside.Removal of a stuck closed thermostat along side the road is OK to get you where your going. I had myself a 440 Mopar with a stuck thermostat;in Florida no doubt, on I-4,,started over heating in traffic,, I pulled off to the shoulder,,Popped the stuck thermostat out,,,made a gasket,,,let it cool down for 45-60 minutes,filled it with water, got back on the road started cruising down the road,{traffic let up} and started it overheating,,4 Core Radiator,full of water,,,but the water was flowing to fast to allow the proper heat exchange for optimum cooling. So,YES a Thermostat is very important!
MotorHead~Ty
Just love you idiot NYers who think they’re all smarter than any southerner. Your hubris knows no end.
I’m from Las Vegas. I’ve heard guys (college educated) from LA, San Francisco, Phoenix and other places call it a motor. Who friggin cares? Does it change the meaning? No. Does it make you sound smarter to say “engine?” No.
Condescension has always been a hallmark of NYers, men especially. I guess the times I’ve heard Carroll Shelby and Jimmy Johnson say “motor,” I should have called in to correct them. Like me, though, I doubt they give a rats coolie what you think.
OK, then why don’t out board boat motors overheat?
They suck in sea water, run it through the engine and spit it straight back out. no thermostat and no pressure.
Cheers
Actually, lots of out boards have thermostats, Johnson 150 has 2
Ok. Maybe I can help with this one. How can it be that if you slow down the flow through the radiator, the engine will run cooler? Look at it this way, if you slow down the flow through the radiator, you also slow down the flow through the engine too. Therefore, the engine heats the water even more right? The 440 was an engine that could overheat in a heartbeat. I think they all had inadequate cooling systems,
Water to metal to air is not the same as metal to water
Use to install smaller size washers instead of thermostat in Stock Car, car never overheated, worked for me and the car, low cost repair.
Don’t forget air restrictions. If you are changing the grill and crowding the engine compartment in a resto-mod application, adding fans, headers and HP, any restrictions can cause big issues. All of the items above are important and each one will affect the temperature in one way or another. I put vintage air in my resto Mustang, and can watch the temp gauge climb the minute I turn the compressor on.
Thata because your engine now has to work harder to turn the compressor
195 degree thermostats exist for emissions reasons only. What a lot of people forget is that if you actually want your car to run cooler you have to adjust the fan system/ecu to account for it. Otherwise, you’re just changing the initial temp the thermostat opens at, not the overall operating temp of the engine.
No. The thermostat controls how much of that cooled coolant comes back into the engine, it doesn’t matter if there are huge fans cooling down the radiator. The water inside the block controls the operating temp of the whole engine. True the oil in the sump will not be as hot, but in most situations this is not a consideration. There are extremes of this and certainly older trucks in cold climates run radiator blinds to keep the whole of the engine warmer.
No Cameron, the thermostat does not just “open” it regulates the temperature so it is constantly adjusting the flow rate to keep temperature constant once the engine warms up after initial startup.
[…] 9 Cooling System Myths and Mistakes and Why to Avoid Them […]
hmmm.
im not an engineer but i am not an idiot.
all the i formation here ia correct except one point. the advice to fill radiator to one inch below the brim then close it up and walk away is aimply incorrect, and also purely stupid. It doeant even deserve an explanation as to why. I just think this is an accidental missinterpretation between a closed pressurized system and an ezpansion tank system. I strongly suggest you rewrite that bit Jim. Inteoducing air into the pressurized cooling system is going to cause lots of damage around the world, as you post is now at the top of googles search result for coolant information and people will take it as gospel.
There is no problem with air in a pressurized system such as this. What do you think happens as your coolant gets low? I have run with a leaking water pump for 6 months now and am often down a gallon of fluid and just top it up every so often without problem. ( I did finally get the pump fixed this week)
what happens when you coolant gets low, is your system is unable to pressurise propperly and the boiling point comes down, and you end up with air bubbles, cavitation, and lack of flow.
Yup, a poorly designed fitting on the manifold of the Vortec engines allowed air to be sucked in when the engine cooled off, this put air pockets in the Vortec heads, and had 2 major consequences
1: it caused that antifreeze (red kind) to turn acidic and
2 : the heads would get hairline cracks normally between the middle cylinders.
Enough to give a guy a headache…
I have 30+ years working on cars in Phx 4 years of which was in a radiator shop..
IF there was ever a place to test any of this, that would be the place (could be why several manufacturers choose to have proving grounds there…
My observation is both sides are right.. It is my guess that it all goes back to how the system is engineered.. How well are the parts matched in the first place.. I have seen cars (BBC) overheat without thermostats and as soon as a restriction is added, they start running cooler.. On my 98 chevy truck with a small block, it simply wont heat up….
My guess? Some systems are more balanced than others.. Yank a tstat out of a car that has an internal bypass port..
The real talent? figuring out why a car is getting hot and fix it.. Certainly can not match theory with a group of engineers that never worked in the field.. Sometimes you don’t know what you don’t know..
“Mark Jeffrey of Trans Am Racing in Southern California tells us he runs 100-percent ethylene glycol and no water without consequence and has been doing it for many years. His logic is coolant temperature runs only marginally higher and this approach eliminates any risk of corrosion.”
That might work in California, but “100-percent” ethylene glycol will freeze at about +20 degrees F. It sounds odd but it is the addition or mixing with water that depresses the freeze point of glycol antifreeze to -34 degrees F below zero. By itself, not so much.
This is really bad advice for anyone who lives where it gets cold, which is most of the country and Canada.
Something that explains slower coolant flow better. Keep in mind that your desire is net heat removal from engine. Slower coolant flow does absorb more heat and exit engine hotter. But that hotter coolant sheds heat much faster in the radiator due to the higher temperature differential with the outside air. So your net result is higher heat removal. Sounds weird but that’s one of the pieces of heat exchanger engineering/design.
Removing a thermostat from the cooling system can cause higher engine temperatures due to a not so obvious behavior. Gases are a poor conductor of heat. For there to be low thermal resistance between the cylinder head coolant passages and the coolant, the coolant must stay in a liquid state. If the coolant changes to a gaseous state, the thermal resistance goes up massively.
If you model the pressure drops around the cooling system in a loop, using the fluid dynamics equivalent of Kirchhoff’s Voltage Law, you will find that removal of the thermostat results in a much lower average pressure in the cylinder head coolant passages. This allows the coolant in the cylinder head to boil. Once the coolant is in a gaseous state, very little heat transfer occurs.
This is why some racers install flow restrictors in place of the thermostat. It creates the required pressure drop, to keep the fluid behind it at a high pressure. I learned about this requirement from an OEM engineer who measures engine behavior with 20+ coolant temp and pressure sensors installed throughout the cooling system. In 30 years of automotive work, that was the only person I’ve ever run across that could explain this behavior.
Restrictors in place of a thermostat, was because in a vertical radiator, ie top to bottom flow radiator, a race engine running super fast water pump, say 6k rpm, will actually force water out of a 16lb cap if not kept in check, with a thermostat, or in this case a 1/2″ hole in the restrictor in place of the thermostat. It is not put there to slow the coolant down for better cooling, only to keep water from “opening” the cap and spilling out. True story.
There were some interesting ideas presented. Personally, I generally trust the experts, and there are some differences between modern designs and the pre-FI engine.
Yes, the thermostat is in place to regulate water flow, and allow the engine to reach its proper (minimal) operating temp. With it removed, engine temps run lower and you computer thinks it needs to keep a richer fuel mix than otherwise necessary.
Small/thinner radiator tubes allows heat to conduct quicker, and allows room for additional tubes. To protect these delicate radiators, modern cars often have sealed systems. Little/no air is introduced when flushing these systems with the proper equipment. Your coolant will also last longer. With heavier cooling needs, the manufacturer adds additional cooling surface.
Water is the best fluid for cooling an engine… but not the best fluid for long-life health in your family auto.
At freeway speeds, you engine does not require a fan. Manufacturers moved to electrics to eliminate the power consuming engine-mounted fan and belt. The shroud can also be closer to the blades, which improved efficiency.
Water is a better coolant than any antifreeze and if you are racing it is the proper liquid to use. If you blow a head gasket while using water it does not necessarily kill the bearings and crank, antifreeze will. As far as coolant speed, coolant needs to periodically almost stop flow in a street car to give the radiator time to do its work, not because coolant flowing faster doesn’t remove more heat but because the radiator cannot keep up. In some situations you can flow air too fast and cause a boundary layer that hurts cooling, but, in the case of a street car it is much more likely you are just losing efficiency and wasting power. Also, in a lot of cases in muscle cars or older hot rods your biggest enemy is a high pressure area in the engine compartment that holds the heat instead of allowing it to exit under the car. Mostly it seems to me you have to address these problems as a system, one system, and if you do that you will find each of you have a good handle on one piece.
the thermostat may not only open the top hose. it may shut off the bypass. if you remove the thermostat, water can short circuit the radiator.
Unfortunately this article is itself falling prey to a myth…
“…coolant never has a chance to park in the radiator long enough to give up heat energy to the atmosphere.”
Ouch.
The heat transfer inside the rad occurs actually very quickly… the faster and the more turbulent the water flow, the more heat is exchanged. The slower and the more laminar the flow, the less overall heat is removed from the system.
Just a few points to add to the conversation. What we experience can be explained by heat transfer.
Firstly, most automotive water pumps are centrifugal pumps (https://en.m.wikipedia.org/wiki/Centrifugal_pump). When a centrifugal pump operates on the right side of its curve it will cavitate. Decreasing the outlet pressure of the pump will drive the pump to operate on the right side of the curve and, if the pressure is sufficiently low, it will cavitate. This can happen when the thermostat is removed depending on how the system is designed (i..e., bypass system design, pressure drop through the system with/without a thermostat, radiator size, coolant flow rate, etc). When a pump cavitates, it will not be able to pump as much water as it did when it had more restrictions in the outlet (operating more to the left side of the curve). This lower water flow will reduce the heat transfer in the engine and radiator. Also, the higher pump suction due to operating the pump at a higher flow rate could collapse the water pump inlet hose if it does not have a system to prevent the hose from collapsing. As an aside – for industrial centrifugal pumps, lower outlet pressures could make it operate outside its best operating point leading to premature seal/bearing failure.
Secondly, unless you are traveling very slowly, the air flow through a radiator is turbulent (which promotes better heat transfer).
Lastly, the more water flow through your engine can increase heat transfer, to a point. Cooling is a function of the change in water temperature multiplied by the flow of the water multiplied by the specific heat of the fluid: http://hyperphysics.phy-astr.gsu.edu/hbase/thermo/spht.html. It is just not the increase in water temperature that drives the amount of energy removed.
Each vehicle is somewhat different and we may not be able to apply what works for one car to another car that is designed differently, but the physics/engineering principles do apply to all vehicles. The real difficulty is finding the root cause of the problem.
Thank you.
This “discussion” has been something. I envision all these little heat hoboes trying to jump on and off the coolant train but it’s too fast.
I’m not an engineer or a rocket scientist. I like to try to have a basic understanding of how all automotive systems work. The point people are saying about coolant not having enough time to cool without a thermostat-in laymans terms-picture the radiator as a heat exchanger, which I think it is basically, lets say coolant is flying through the radiator really fast well the air is not going to cool off the coolant dramatically in a quick time so the hot coolant goes right back in to the block and heats up some more. The coolant keeps flying through the exchanger just to regain heat again. That would be why it doesn’t have enough time to cool. I’m not sure why some op’s couldn’t grasp that. However, in typing this the opposite could be true, the coolant doesn’t stay in the block long enough to get as hot as it normally would so it could get hotter. The thing is though heat is a guarantee in a running engine. The engine will continue making heat without fail so the limits of the cooling capacity will kick in sooner with no thermostat than the limits of the heat generated by the “engine” ,(I call it a motor sometimes, as a motor does work) so I would agree that the system would not cool properly without a thermostat. Basically you will get more heat than cooling running with no thermostat. That obviously has factors such as ambient temp and rate of speed, etc… Will the car overheat, probably not but I do know a modern car will burn more fuel and not run as healthy during the longer warm up period caused by not running a thermostat. If you rocket engineers want to respond to me please don’t because I probably won’t understand you. This is for people that couldn’t grasp the simpler things that I am associated with.
If it’s going too fast to get rid of heat, isn’t it going too fast to GAIN more heat?
in other words, the coolant would never boil or show high temps on the gauge, and the block would melt, without the coolant slowing down to pick up that heat.
Right. That’s just silly.
The thermostat in most cases is diverting coolant to the block when it closes. You dont want to try and just close the flow or you can damage the pump. Much older engines it might be the case that they literally just close the flow off somewhat but not so in modern engines.
As a result if you remove the thermostat you can have a condition where you recirculate the coolant flow rather than forcing it to the radiator.
This whole faster coolant flow reduces heat transfer is nonsense. There is no laminar flow in an engine or a radiator air or water. This you can be sure of.
To get laminar water flow in a garden hose for example the fluid flow has to be very very slow on the order of a small fraction of m/s. You can look up how to calculate Reynolds a number and prove to me I’m wrong if you want.
You want turbulent flow for heat transfer it reduces the thermal boundary layer where the flow speed is low so you have to rely on the fluids conductivity rather than mixing (turbulence) to transfer heat. If you take water thats boiling and and ice cold water. The fastest way to transfer the heat from the cold to hot water would be to mix them as quickly as possible (turbulent flow)
The ability of the radiator to transfer heat to the air passing through depends on the temperature of the radiator which is basically the temperature of the water inside the radiator due to the high thermal conductivity of the metal and the turbulent heat transfer of the water to the metal also being high.So more flow is better if you have a condition where the water leaving the radiator is cold you can increase the cooling capacity with more flow. Now if you still think I’m wrong I have some examples or statements about the situation to isolate whats going on.
Forget about the application as a whole for a second.
No one would argue that if we make the radiator hotter it will transfer more heat in a given situation. Yes? Forget if has different temperature in one spot or another just saying if the whole radiator was twice as hot it would be transferring double the amount of heat. Thus anything we do to increase the average temperature of the radiator will increase the amount of heat we transfer.
Now for a second lets imagine we have a tap, its outputting water at a given rate and we send it through a radiator and then we dump it. If we flow the water at a very very slow rate it will cool off quickly. The overall temperature of the radiator is thus low. If we keep increasing the speed of the water going through the radiator the temperature of the water leaving the radiator might start to rise. But so does the temperature of the radiator. So we MUST be increasing the heat that we are getting out of the radiator even though the water leaving the radiator is increasing temperature.
Now. An engine is not a magic tap that produces 200F water. It generates a certain amount of heat. Not a temperature. If we increase the flow we might see the delta T between the inlet and outlet of the radiator drop but we know that its the temperature of the radiator that matters. It doesn’t matter that the water “didn’t have time to release or absorb the heat”. What we want is for the air to be able to take more heat out of the radiator. If the temperature of the radiator decreases from inlet to outlet then it has a lower temperature and heat transfer to the air is less which is what matters. Thats the exit for the heat.
Another good reply.
In an automotive forum I moderate, I equated this goofy idea to “heat hobos not being able to jump off the train because it’s going too fast”. There is still a lot of nonsense floating around out there, and everyone has an analogy to prove it “right”.
We might not change the mind of the person we are replying to, but it might help educate other people who stumble across these misguided articles that “debunk myths”.
Have a stone stock ’79 400 Ford.
Runs like crap when its cold. Needle doesn’t even move on gauge. It “acts” like a cold carb’d motor. Choke isn’t acting reliable, fuel economy is deplorable.
Runs quite good when its warm out, but starts to think about overheating at a prolonged idle in the 80f’s.
You can watch the needle creep up and up, until you start driving again.
Dialing a carb in is about impossible when your vehicle is swinging wild operating temps.
I live in the south, and in spring it can be 34f one evening and 82f the next day.
You need steady operating temps.
I decided I’d put in a new thermostat.
Guess what? No thermostat in the motor. This= wild swings in operating temps.
Put in a 190-195 thermostat, as recommended by Ford, and presto, it hovers in the middle “NORMAL” area of the gauge now.
Behavior of the motor is as it should be.
I suppose if I were driving 500 miles straight and non-stop at a constant speed, eventually in that length of time, a balance of temperature would eventually take place, regardless of outside temp without a thermostat, due to the eventual heat soak of the cast iron block, intake, manifolds, crankcase oil temp, etc.
In addition to the absorption potential of the coolant, and its flow rate, and the radiators capabilities.
Eventually, without a thermosat there would have to be a maximum threshold obtained for a given set of conditions.
Would it work? maybe. Would it not work? equally maybe.
Depends on conditions and capability.
For jutting around 8, 10, 20 miles or so, (in uneven conditions and capabilities)the thermostat is needed in my jalopy.
As far as air flow. Good grief. Hasn’t anyone ever put cardboard in front of their radiator? That’s maximum slow air flow. How does that cool? Work your way back.
I have a small block chevy remanufactured engine that at about 200 miles starting heating up only on the passenger side under a load or while accelerating. The drivers side stays around 190 degrees, at idle the passenger side cools down. I have changed clutch fan, thermostat, radiator cap, checked timing, fuel mixture, valve clearance, replaced head gaskets.
Have you weighed your passenger ? Could be workin’ a bit too hard on that side.
Cracked head.
For many reasons already described by others, the information presented here is fairly strong evidence that the author’s name is an oxymoron.
He could hardly have crammed more bad information into one write- up.
responding to stan gray make sure you dont have restricted exhaust flow on the hot side or a lean carberator on one side intake air leak or problem o2 sensor if injected the cat pluged do to prior engine failure
– I’VE AINT NEVER HAD ANY PROB COOLING MY MOTOR AT MACH 2.1! YA’LL GOT ISSUES! ~
I have enjoyed this discussion with many valid points whether they apply or not. I think we all agree that you should have a properly operating t-stat. The statement from the article about eliminating the t-stat “When coolant never has a chance to give up heat via the radiator, it gets hotter and hotter” is misleading at best. I have heard it applied to hydronic heating and cooling many times. The concept would suggest that more flow = less heat transfer. Wrong-O.
As applied to this conversation I say: More flow = higher leaving water temperature back to engine but higher heat transfer in both the engine and radiator. Less flow = lower leaving water temperature back to the motor but less heat transfer in both. Is this not how a t-stat works? Coolant temperature rise causes t-stat to allow more flow by proportional opening. Temperature drop causes t-stat to allow less flow.
Kudos to the mentions of cavitation. If you remove the t-stat restriction and increase the flow rate above design the pump can cavitate which = Less flow with bubbles = much less heat transfer.
High School Dropout, Retired HVAC, Plant Operations, Dumb As’t Boiler Operator.
Holy Crap. We have guys here who’ve sent rockets to the moon and others who’ve handed thesis’ to professors but not many that have had much to do with cooling systems of motors ! Facts are inhibitor/glycol is needed for any motor using any aluminum to stop serious corrosion. Also needed for any motor that gets down to freezing to stop ice destroying it and it also limits the insulating rust buildup inside any iron block motor. So who gives a damn what theory you want to believe, you need to be using it so get used to it. Yes a thermostat should always be in there too to control the temperature by controlling water flow. AND because without a thermostat many engines will overheat because the water goes thru the radiator too fast to cool sufficiently so it actually does two jobs. AND even if your engine doesn’t overheat with the thermostat missing it will be a pig on cold mornings because it takes too long to heat up.
Give it all the damn theories names you want, thems the facts assuming the radiator is the correct size for the application?
And for the guys who have radiators approaching mach speed and worrying about laminar or turbulent flow … go buy yourself a new rocket ’cause you’re clearly from a different planet to the rest of us mere motoring mortals.
Goodday
What are the advantages of using boiled water that’s cooled and filled into the radiator
too many idiots on here. come it isnt how fast the coolant is transfered its the tempature of the coolant going back into the motor so yes a thermostat is needed its also a restriction. if you dont like thermostats the make a restrictor plate looks like a big washer seal that sob up in your engine and you should be fine
Adding another argument to the mix….. With an electric fan, could you achieve the same results if you put the fan switch on the cool side of the radiator instead of the hot side of the radiator, providing you used a lower temperature switch? Just wondering. It seems like if you controlled the temperature going into the engine, it would still cool the engine about the same as a higher temperature switch on the hot side. Any thoughts?
Yes, this is done in some factory systems, and you can find aftermarket parts as well.
I forgot to add: some systems have down-flow radiators but the thermostat in the lower return. (not to be confused with a “reverse flow” with the thermostat in the lower hose).
2003 wrx subaru is one.
Well I think there is enough information from the geniuses to us shade trees that we understand alot more of the dynamics of how the cooling system works to figure out what is best for ours. Thank all of you for the very informative but over my head schooling. I truly appreciate you educated folks taking the time to explain in laymen terms how thermo dynamics works. Once again, thank you
Ray Lawrence
You can prove anything is right with internet research.
thank you for the lesson
Quote: “When coolant never has a chance to give up heat via the radiator, it gets hotter and hotter, especially if you’re stuck in traffic. And even on the open road, coolant never has a chance to park in the radiator long enough to give up heat energy to the atmosphere.”
This is one of the fallacies/misinformation that continues to spread. There aren’t 2 types of population inside the cooling system; however, following that misconception used, wouldn’t the population staying for a longer period of time in the engine also become hotter?
A common misconception about cooling systems is that if the coolant flows too quickly through the system, it will not have time to cool properly. Because automotive cooling systems are a closed loop, coolant allowed to stay in the radiator longer will also stay in the engine block longer, producing increased coolant temperatures. This can easily lead to “hot spots” and, ultimately, engine failure.
Delta T
The hotter the coolant leaving the block the more heat, in BTUs is transferred to the air through the radiator. For the same reason as the cooler the air is the more heat is transferred. For ultimate heat shedding, vapour phase cooling is the most effective. This is because you are taking advantage of the latent heat of evaporation. Running a condenser instead of a radiator recoups that latent heat by condensing the vapour back to a liquid – and then running it through a secondary “radiator” to cool the liquid. The problem is using a water based cooling medium results in the TEMERATURE of the engine being too hot to run safely on gasoline (without detonation/pre-ignition etc) This is the principal that refrogeration works on – and if we were running an ammonia loop instead of water/glycol the engine would likely run too cold – – –
I have a 1992 Chevy Camaro with a 305 cu in engine. I recently had A 3 row aluminum radiator with 2 12 in fans with 1400cfm each .Should i have a better water pump put in them the factory one it has.
I have a 1957 chevy belair with the original 283 power pack engine which is totally rebuilt.The heads ,block and intake were all thoroughly cleaned (hot tanked) .There is a new heater core , new high flow waterpump .new high flow thermostat,new aluminum large tube radiator and all new hoses and a factory 4 blade fan and a shroud.Why is it that when I am standing traffic the temperature start to climb immediately.I’m running a 50/50mixture of coolant and water.Engine timing and carb.setting are right on the money.The sender is new and the gauge is working properly.I have a thermo gun.Please help thanks.
Hey Bob, if you’re heating up at idle, it usually points to airflow (AKA, the fan). I assume you checked the flan clutch (as it would be obviously be spinning at low RPM anyway), so let’s look beyond that. You mention fan shroud, so I’m wondering if it’s in good shape and sealing completely around the radiator. In my experience, a proper seal is absolutely vital to ensure the fan is pulling enough air across the radiator. So if you’re running an aftermarket aluminum radiator, start by checking for visible gaps–and perhaps the seal can be enhanced by the strategic use of high-temp weatherstrip?
I would like to comment on cooling systems in general, what data is required for sizing the cooling system and some aspects of testing the systems.
My experience comes from 25 years of producing and testing industrial power packs from 50 hp to 800 hp.
Thermostat.
Its main function is to maintain the coolant temperature at a minimum temperature to ensure that engine components operate at their correct tolerances. Its fully open temperature will be well below the maximum top tank temperature for the engine. Maximum Top Tank temperature is the maximum temperature of the radiator top tank, which is the same as the water temperature that is exiting the thermostat. This figure is governed by the design on the engine and the Engine Design Engineers.
It also ensures that the engine oil operates in its correct temperature range for multiple reasons which would be part of a difference discussion for a later date.
Most, if not all modern engines use a thermostat that has the bypass function that directs the coolant back to the water pump inlet to ensure even consistent coolant flow around the engine when the thermostat is closed. As the thermostat opens the coolant bypass flow is reduced as the flow the radiator is increased. At the fully open position there not bypass flow.
During cooling system testing the thermostat must be installed in the engine and should blocked fully open. This is to ensure that is does not affect the coolant flow the radiator and hence its performance.
A side note here, the testing I conducted required the removal of the radiator cap as this would be testing under the worst case senior. On some modern car engines the removal of, or a faulty radiator cap can cause overheating, this is due to the fact that cooling system have very little cooling margin up their sleeve as the saying goes. This is all about cost, size and design constants.
The parameters that are required to design a cooling system
Engine heat rejection to coolant
Coolant flow at designed maximum engine operating RPM. You can also add coolant flow at peak engine torque as this can create challenges due to heat rejection versus coolant flow at lower engine speeds
Maximum ambient temperature the vehicle is to operate at. In automotive applications (cars) this figure has several parameters that the will affect the final outcome. The use of Full HP for long periods, Towing Trailers, Increase cost of cooling systems in hot areas of the world.
Area allocated for the size of the radiator, e.g frontal area available to direct airflow.
Operating road speed as the ram air onto the radiator has a large effect.
Radiators
Coolant flow through the radiator must be not be laminar, it must be turbulent as this ensures that all of the coolant will make contact with the surface of the tube as it passes though the radiator, failure to achieve this limits the amount of heat rejection to the tube.
The restriction of coolant flow must be low, around 5 PSI Delta max. This also ensures the coolant is not in the radiator longer that required, and hence not create water pump restriction issues (water pump cavitation).
Air in the cooling system is your worst enemy for cooling performance.
Coolant tube spacing.
Number of tubes per row, number of tubes rows, and the number of fins per inch governs the air contact area for heat removal. Like all things this is a trade off as the more fins per inch, the easier it is to block (fowl) the radiator core. The less number of fins the less heat can be rejected to ambient.
Increasing the number of rows becomes a law of diminishing return as the rear tubes will see a higher core on temperature which will be higher than the ambient temperature and therefore reject less heat from the coolant.
Coolant
Depending on the type of coolant used, is ability to absorb heat for the engine and then reject it to the air will very. An example of this is the difference between straight water and 50/50 water and Ethylene Glycol is about 3 deg C. That is an engine running a set rpm and load with a fully open thermostat will run slightly warmer. The other benefits of 50/50 water Ethylene Glycol are not discussed here.
Fan and shroud
Fan operation and selection also affect the air flow.
Fan to shroud clearance and insertion will have an effect at slow road speed under high engine loads.
Thematic fans that do not operate when the engine is at idle and the car is stationery can aggravate high coolant temperature and then place operating aircon on top of this can produce over heating in stationary traffic.
Air conditioning condensers can have a large effect on the radiator performance they increase the air on temperature to the radiator which reduces the ambient temperature capability of the radiator.
Engine performance
Modifications and increases to horse power without changing cooling system components and or no correct technical data to allow for the correct changes to components to achieve an acceptable cooling system performance.
I hope this helps to explain the challenges of cooling system design and performance.
The US Army considers anything more than 10 fins/inch a FILTER
to me it is really simple.
Manufacturing engineers are under extreme pressure to cut cost where ever possible.
If no thermostat worked better or even close to as well as no thermostat….. it wouldn’t be there
Is it still running ? Yes !
It does not have enough features.
The US Army has Engineering Design Handbooks. One of which is “Military Vehicle Power Plant Cooling Handbook” #AMCP 706-361. Mine is dated 1975.
It was given to me by a dear friend, Lt. Colonel John Martin, RIP, that I worked with daily at AiReserch/Garrett/AlliedSignal/Honewell in Phoenix AZ. We and a small group of other Engineers and Scientists Designed, Fabricated, and Tested one of a kind Whiz Bang engines for the Dept of Defense. We blew up stuff, but every now and then something worked !
The US Army knows a thing or three about engines and how to keep them running in VARIABLE conditions.
The UnClassified Hanbook might be available on the NETS, or in Libraries (remember them ?), or even from a friend in the US Army. You can see it here : https://apps.dtic.mil/sti/citations/ADA013769.
There will be a TEST later . . . LouAZ
And this is the 1998 Update to the US Army Cooling Handbook –
https://apps.dtic.mil/sti/pdfs/ADA537530.pdf
All 661 Pages !
Good info on T-stats and bypass and . . . LouAZ
Interesting. My 2 cents after reading thru most of this. Since there are people who have experienced better cooling with the thermostat removed and people who have experience worse cooling with the thermostat removed it seems likely that the root cause of the reduced cooling is something OTHER than removal of the thermostat, that is, removing the thermostat results in some other factor becoming important.
What might that be… my guess is that removing the thermostat, which changes the pressure profile in all parts of the cooling system, changes the relative amount of water going to the block versus the heads. For example, assume that with the thermostat in place equal volume of water flows thru the block and heads and the car runs at 180. Then, when the thermostat is removed, and the pressure profile changes, the amount of water thru the heads decreases while the amount thru the block increases. With reduced from thru the heads the heads start to “runaway” whereas the block just stays about the same temp it was before. Net result from the change in flow pattern is an overall hotter running engine. Not specifically due to “higher flow” but because the flow pattern has changed due to the change in pressure profile. This would mean you can make no general statement about what happens with versus without a thermostat, it’s going to depend on the specific engine, the size of its water passages, etc.
99.9% of water-cooled engines have thermostats, also boat engines, two stroke even. Why do you think engineers designed the thermostat to be there, for fun?? It has two things to do, first ,speed up the warming of engine, second to keep the engine temperature stabile. In closed cooling systems it gives the coolant in radiator time to cool down in radiator. FACTS!
I own 7 PWC’s all of which have two stroke boat engines and not one has a thermostat. No PWC manufacturer of that era (80’s-90’s) of which I am aware made two stroke boat engines with thermostats. So much for your “facts”. But they were all designed with some manner of engine outlet restriction to keep the water pressure in the engine high enough.
Another fact is that in a closed loop system if the water is given more time in the radiator to cool down, you are also giving it the same amount of longer time in the engine to heat up.
Which DEFINITELY improves the cooling efficiency – Delta T. The difference in temperature between the block and coolant – the higher the delta T, the more heat is transferred – and the delta t in the radiator – the higher the delta T the more heat is shed to the air. IF the cooling capacity is marginal the engine temperature will increase, but if the cooling capacity is adequate, enough heat will be removed to prevent engine over-heating. Increasing the EFFICIENCY of the cooling system will ALWAYS reduce the operating temperature by increasing the CAPACITY of the system. The engineering target is acheiving a BALANCE – – getting the efficiency of the system high enough to provide adequate capacity in a small enough and light enough system at a low enough cost to satisfy the engine, the engineer, the stylist, AND the accountant. This ballancing act often means a lower cooling efficiency and larger volume system to reduce costs.
Maybe the PWC:s are within the 0.01 percent that not having a thermostat, usually all have it. The fackt is that engines needs a thermostat to manage engine temperatures. Having a thermostat control engine temperatures assume the the radiator is big enough to handle cooling water in a given time. Still my earlier writing counts.
lol With all this tech from rockets to engeneers mix it up any way you want and a old model chevy runs between 180 to 200 on avg .This is getting like our goverment aproches projects .Just my oppion Thanks Eddie
195 degree thermostats… all of the naturally aspirated high performance engines which I have run on the dyno, make more power at 220F than they do at 180F… the forced induction engines may start to see some benefits at 180 vs 220… but the problem with 220+ is the fragility of the water based cooling system which was just barely addressed with the Evans propylene glycol type solution… and also shows the need for a higher PSI cap for water type antifreeze. Don’t fear the 220-240 zone if you have a robust cooling system. Look at F1 an MotoGP and the temps the engines are designed to run, it’s very high not just because they make so much heat. Running a lower T-stat or lower temp for the fans, causes other issues and doesn’t really reduce overheating risk, another startegy is needed for overheating… although its a commonly accepted process to lower t-rtat and fan on temps. I think that running with a thermostat also increases the pressure behind the water pump, which in turn increases the performance of the cooling system reducing steam pockets and boilovers.
[…] Quote from the source: … […]
This is all good in that it causes U to think about a specific problem & reason it to a conclusion. [a thought process ]
U will be smarter the more U use this reasoning. this can be appealed to life experiences or problems. maybe use mutable ideas
to a usable result that fits your needs. Best of luck 2 U all.
I would like to suggest that what people are not remembering with thermostats in a standard car are there to ensure that the engine warms up as quickly as possible without pushing the heat away from the combustion chamber helping to limit the condensing of fuel on valves and pistons also “bore washing” and the incomplete combustion, reducing pollution and carbon build up on those parts.
As for race engines each to there own.
Have a SBC in a street rod without a stat. It runs about 170 degrees on cool Minnesota days. It heats up to about 180 degrees on hot days with the single shrouded 13″ electric fan operating on an aluminum 14″ X 28″ Be Cool radiator. Been attempting to make it run cooler at all times before I install a stat. Want to make sure the cooling system is capable of cooling the engine no matter what the temps are. Have installed and air dam under the radiator and plugged all the passages around the radiator. The fan moves a lot of air but a second fan will fit on the lower 1/2 of the radiator and will be the next mod. Last improvements made were to reduce the pump pulley and alternator pulley. Engine came with a 5″ crank pulley, 7.5″ pump pulley and a 2.5″ alternator pulley. Now has a 5″ pump pulley and a 2″ alternator pulley, better RPMs.
Have always pulled the stat to make an engine run cooler, after all when the engine is as hot as it gets the stat is wide open providing maximum coolant flow to the radiator, with some restriction.