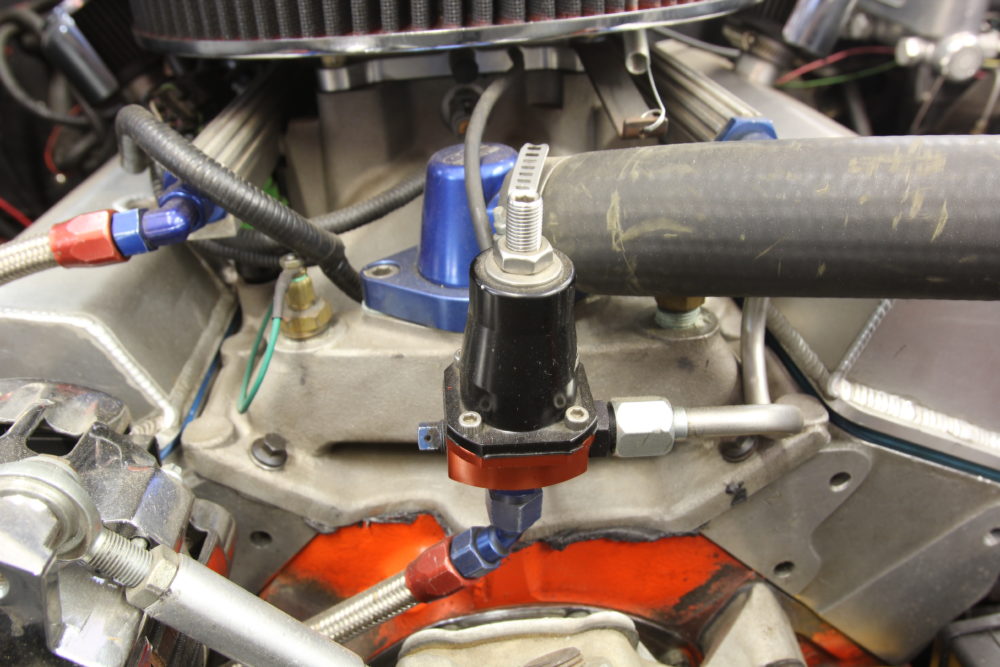
I am making plans for an LS-swapped Chevelle with all kinds of cool parts, so I’m building the car in my head. I’ve seen lots of people use that Corvette factory fuel pressure regulator and fuel filter in their cars and I got to wondering why I should place the regulator up front near the engine. What if I placed it back near the rear of the car and save the trouble of routing a new fuel line all the way to the rear for the return? Would this work? It seems like a good idea.
B.F.
My first reaction to your question was that if you placed the regulator all the way in the rear of the car near the fuel tank (assuming it’s a normal front-engine, rear-fuel-tank vehicle) that this would dramatically slow the regulator’s response time.
In other words, the fuel pressure regulator would always be trying to catch up to the demands placed on it by the injectors.
But rather than just guess, I decided to ask an expert and sent your question to Brett Clow, the technical director at Aeromotive, and his answer was so complete that I’ve decided to share it in its entirety below. There’s a reason Aeromotive is one of the premiere fuel delivery companies in the aftermarket.
The following answer is from Brett Clow, a true fuel systems subject matter expert:
This is a question that is frequently asked and generally you’re correct regarding the response rate. We often refer to this as “latency.”
I normally respond to this question like this:
Technically, we can put the regulator anywhere in the system and it will regulate pressure. The thing to keep in mind is the regulator only knows, and reacts to, the pressure inside itself. While we could argue that the pressure in a hydraulic system should be even across the entire system, in practice, that’s not always the case. Ultimately, the pressure fluctuations (oscillation in the form of peaks and valleys) that accompany the opening and closing of a fuel injector in a fuel rail are transmitted through the system, including the fuel rail and any adjoining fuel rails that might be attached.
The fuel pressure regulator’s job is to both absorb and dampen these fluctuations, while adapting to the general trend of fuel flow through the injector, returning more or less fuel to the tank depending on engine load, in order to maintain the proper baseline (base with vacuum or boost) fuel pressure. The farther the regulator is from the fuel rail, the later (latent) and muddied the fuel pressure fluctuations will be at the regulator, which in turn reduces the regulator’s ability to absorb and or adapt to them. This means fuel rail pressure control will be degraded and the fuel flow through the injectors when they’re open will be less consistent.
The OEM does, and has since 1999, run many vehicles in a “returnless” fuel system. This is seldom understood, both as to how it works and why the OEM does it.
Bottom line: The OEM builds cars with returnless systems to pass EPA evaporative tests that became much more restrictive in 1999.
The downstream consequences of this were increased fuel line and fuel rail temperatures resulting in a whole new class of hot fuel handling problems related to the fuel no longer being recycled which meant cooler fuel wasn’t delivered to the engine all the time.
This was addressed by raising fuel pressure from a normal of 38-43 psi to 58 psi and, when that wasn’t enough, the development of what we refer to as “fly-by-wire” throttle bodies. The issue was when the engine is hot and fuel is bubbling in the fuel rail, an aggressive/fast throttle opening resulted in a bog or a hiccup that would have new car owners taking their cars back to the dealer as lemons. Slowing down the throttle rate of change when the engine is hot reduces the chances of a stumble or poor drivability, and so there you have it, no more direct throttle-to-foot connection!
One side note, the Corvette filter regulator that is so popular for EFI engine swaps is frequently used with the intent to locate the assembly at the back of the car.
It’s okay with smaller pumps of up to 190 liter per hour (lph), but that filter/regulator really begins to struggle handling higher-flow pumps in the 200-600 lph range. It’s common to see our 340 Stealth pumps damaged by these components as they seem to quickly clog the built-in filter, dead-heading and damaging the pump before there’s any real sign of a problem.
We strongly recommend Aeromotive fuel pumps be used with the recommended Aeromotive fuel filters and regulators, and that the regulator be as near the engine as is reasonably possible if engine performance is at all a focus of the build.”
That’s about as concise an answer as you can expect. Clearly, there’s a benefit to placing the regulator close to the engine so it can react quickly to sudden throttle changes that will cause the fuel pressure in the fuel rail to drop. The farther the regulator is from the injectors, the longer it will take for the regulator to respond. Clow’s information on fast throttle action hesitation might at least point tuners in a new direction when addressing part-throttle acceleration problems that have been difficult to overcome.
The bottom line is: Put the regulator up near the engine and your engine and EFI system will be much happier.
Well… this guys is trying sell Aeromotive fuel pressure regulators and expensive pumps. There’s no reason why the GM filter regulator would clog up faster than any other filter – and it’s going to clog up no matter where you put it in the system. Many of the 99 and newer LS fuel rails only have one inlet and no return – so you’re stuck using the Vette filter regulator – unless you want to buy a whole new fuel system. I think the better answer is to retrofit an older supply/return fuel rail system from a 98/99 F car LS1. Then you can use whatever pump and filter regulator you like. And we are pretty much stuck with drive by wire TBs unless you want to throw the GM computer and wiring harness in the trash and start over. Or again, you can try to use the original LS1 F car computer and harness (they used a normal cable TB)
[…] we learned in a recent Jeff Smith Ask Away! column, the increased use is due in part to tightening federal environmental […]
The illustrated fuel pressure regulator clearly states it’s a mpfi intake with a fuel rail and return line. However, that’s obviously a carbonated intake with a throttle linkage return spring and 4bbl intake air cleaner.
More accurately, it is an MPFI manifold with a 4150 style throttle body, multi-point injectors and fuel rail just like any other EFI system. The fact that the throttle body uses a 4150 Holley style bolt pattern has no bearing on how this fuel regulator system operates. It’s just a different way of using a throttle body. The fuel system operates exactly the same.
I’m trying to understand what are “safe limits” to fuel pressure oscillation, if any?
I have that corvette setup with all 6an lines. the regulator is about 18″ from the fuel rail, off to the side. It holds at 63psi in idle. The gauge is right at the rail.
when I blip the throttle, the pressure spikes in either direction by 3-5psi. If my math is correct, that’s about 2.5% in either direction. so say, 5% oscillation?
Should I be concerned?
What about before or after the injectors? Seems it got real popular to plumb the rails then out of the rail into regulator and return to tank.
So what i got out of this article, is that the 5 micron filter in the vette regulator-filter clogs sooner than say all the 10 micron inline filters, and taxes the pump.