Is it Necessary to Align the Bellhousing for a Transmission Swap?
Q: I’m installing a new 5-speed transmission and bellhousing in my 1993 Mustang. A friend of mine asked me whether I aligned the bellhousing. All of my parts are new, so is it actually necessary to align the bellhousing?
Yes—Bellhousing Alignment is Essential
A: Bellhousing alignment is essential for proper clutch function and making sure all related components are working properly.
Aligning the bellhousing is simply getting the transmission input shaft centerline and engine crankshaft centerline in perfect alignment with each other. The manufacturing tolerances of engine blocks and bellhousings can vary. Misaligned input shaft/crank centerlines cause the following problems:
- Hard shifting
- Pilot bearing wear
- Transmission main shaft bearing wear
- Clutch disc hub failure
- Loss of horsepower to the wheels
Engine machine work, such as the line bore or hone can also affect alignment.
Determine Bellhousing Alignment in 3 Steps
To determine whether the transmission input shaft and engine crank fall within allowable specifications, follow this procedure:
1. Install the flywheel (only) on the assembled engine, then install the bellhousing on the back of our engine using your existing factory bellhousing dowel pins.
2. Attach your dial indicator to your flywheel and adjust the plunger until it’s in contact with the register bore of the housing. It doesn’t matter where you start.
3. Rotate the engine, noting the dial-indicator reader. Misalignment is one half of the indicator reading with a .005-inch maximum runout allowance. If runout exceeds .005 inch, you’ll need to install offset alignment bushings.
The good people at Lakewood assembled this offset dowel sizing chart to help you order the correct offset dowel pins you’ll need to achieve proper bellhousing alignment. All Lakewood dowel pins come with detailed instructions on how to achieve perfect alignment.
Total Indicator Reading | One-Half Total Indicator Reading | Dowel Size to Use | Lakewood Offset Dowel Pt.# GM .625″ | Lakewood Offset Dowel Pt.# Ford/Mopar .500″ |
---|---|---|---|---|
.012″-.020″ | .006″-.010″ | .007″ | LAK-15920 | LAK-15950LKW |
.022″-.034″ | .011″-.017″ | .014″ | LAK-15930 | LAK-15960LKW |
.036″-.052″ | .018″-.026″ | .021″ | LAK-15940 | LAK-15970 |
For steel bellhousing applications that are routinely removed for clutch service, Lakewood offers fixed weld-on dowel pin kits for GM and for Mopar/Ford. These pins permanently locate the bellhousing to prevent the need for realigning it every time it’s removed.
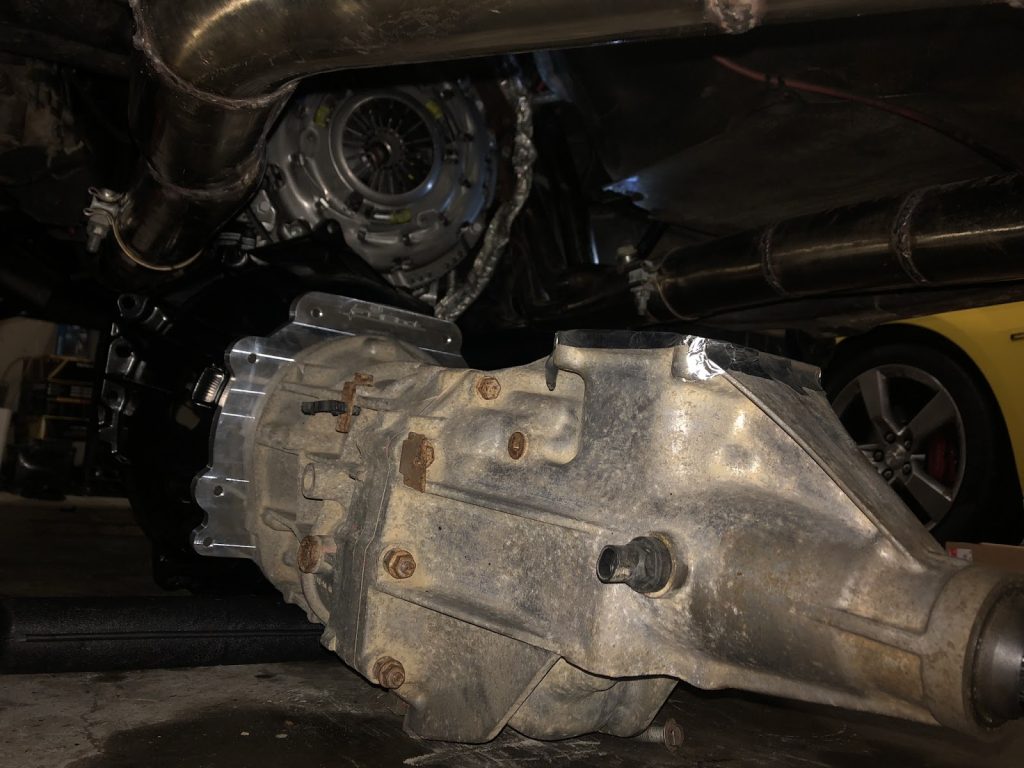
you say doesn’t matter where you start just to get reading….what i don’t get is which reading do i use since i will get at least four different readings say at 12o’clock…3o’clock…6o’clock and 9o’clock. so which one is considered THE measurement to divide by half?
if 3 o’clock is .006 and 9 o’clock is .004 you need to make both of them .005. when you are done the indicator reading should not change as you turn the crank shaft and watch it spin around inside the hole in the bell housing.
some dial indicators will show a different reading when turned upside down. it is important to check your indicator before using it in a procedure where it will be both inverted and right side up. you can check it by sticking the mag base to a piece of steel then adjusting the indicator against it to simulate the position it will be in. then turn it over and look at it from underneath. I have seen indicators move .001! this is something that must be checked in order to get real data. one way to check your work would be check the bell housing run out then turn motor upside down in the engine stand and check it again. but then you have to think… did the crank shaft move in the bearing clearance when you turned the motor upside down?
Hi, i think that i saw you visited my site so i came to “return the favor”.I’m trying to find
things to enhance my website!I suppose its ok to use a few
of your ideas!!
What is the “register bore on your housing”?
Can someone explain that please?
They are talking about the hole that aligns the trans with the crank. It’s the center hole in your bell housing. You want to note where the high and low readings are on the dial indicator, (they should be opposite each other) and that will be the line you want to match with the offset on the dowels. Make sure you re-check afterwards to make sure you went the right direction and amount. Off set dowels should be 1/2 of the difference high to low, but come .007, .014, and .021. You can find charts to help you get the right size.
Once I have aligned my aluminum bell housing with the correct pins, can I remove the bell housing for easier engine installation without realigning the bell housing?
My 12 oclock is .000
my 6 oclock is .011
my 3 oclock is .015
my 9 0clock is .008
What offset bushing do I need to center my bellhousing?
You need .007 offset dowel pins pointed at about the 5 oclock position. Your 12 oclock-6 oclock measurement is just .001 too large necessitating the correction.
Fantastic beat ! I wish to apprentice even as you amend your web site, how can i subscribe
for a blog web site? The account helped me a acceptable
deal. I have been tiny bit familiar of this
your broadcast provided vibrant transparent concept
My bell is .000 at 12 o’clock.012 at 3 o’clock .035 at 6 o’clock an .024 at 9 o’clock if im understanding this correctly I need a .014 offset dowel pin pointing at roughly in between 6 an 7 o’clock
Help here please , mine is at 12 -.004 3 -.007 6 .0012 9 .022 what dowls do I use ? It’s a sbc mated to a Offenhauser bell housing to adopt a 39 Ford tranny. Thank you for your help how long
Is this the same procedure if I have a C -4 automatic transmission
Why is it that no one explains how to center the dial indicator base on the pilot bushing of the crank. You can’t check bellhousing runout until that is completed. Everyone seems to gloss over this step like its unimportant, when it is the most important aspect of this measurement.
Because its unnecessary. The distance off center of the crank is the same no matter where the crank is in it rotation assuming you do not move the mag base during the 360 degree sweep. The indicator and the crank in static alignment to each other, Only the rotation is changing.