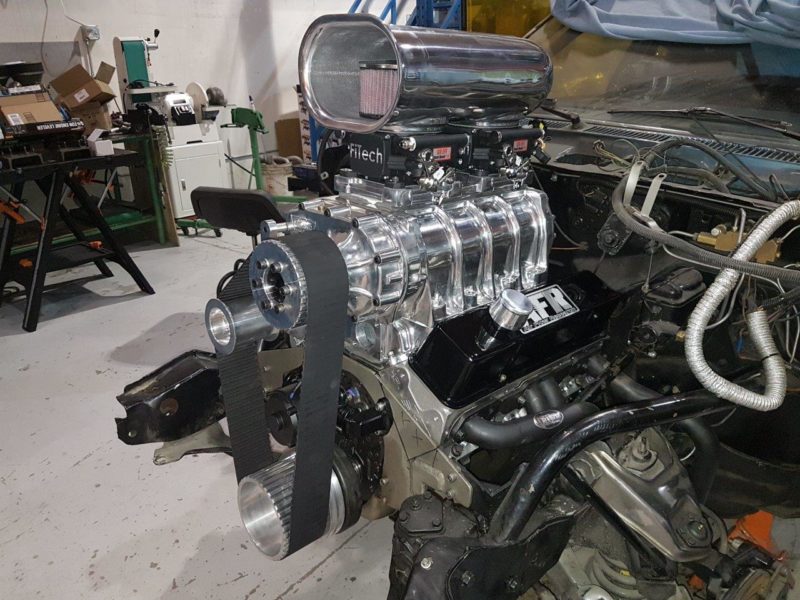
I am building a 355 cubic inch small-block Chevy with AFR 1065 220cc Race Ready AFR heads, an Erson roller cam, and FiTech fuel injection. Can I use a wet nitrous system injected under the fuel injection and then into a Weiand 6-71 blower?
D.W.
Jeff Smith: From your photo, it looks like a great project.
Can you run nitrous with the blower? Sure.
The question might be: Why? But there are advantages to that setup.
Typically, the older design 6-71 Roots type blowers make a lot a heat. By injecting nitrous into the blower, that will tend to cool the discharge temperature. I don’t have any actual hands-on experience with a system like this, but I can add my two cents, along with a few cautions.
The FiTech (and several other self-learning throttle body systems) offer the opportunity to combine a wet nitrous system with self-learning EFI. The first point is that we emphasize a “wet” nitrous system injecting both nitrous and fuel underneath the two throttle bodies. This adds fuel to the engine when the nitrous is engaged. The advantage of using this along with the EFI is that once the nitrous is engaged, this triggers a specific nitrous air-fuel (A-F) ratio target with the FiTech computer that is different (generally richer) than the target air-fuel ratio specified when the engine is at wide-open throttle (WOT) without nitrous.
Let’s say that you choose to run the engine under boost at a 12.8:1 A-F ratio, and once the nitrous is engaged the nitrous target A-F ratio is 12.2:1.
Once the nitrous is engaged, the EFI uses feedback from the wide-band O2 (WBO2) sensor to read the A-F. With a carbureted-plate nitrous system, you could use a WBO2 to indicate the A-F and after the run, come back to the pits and manually tune the system with jets or fuel pressure.
With the FiTech system, you merely spec the A-F ratio you desire and the system will automatically trim the A-F ratio either by adding or subtracting fuel from the throttle bodies. If the added fuel for the nitrous is too rich, the ECU will lean out the overall ratio. Conversely, if the A-F is lean, it can add fuel. This results in a closed-loop system that will automatically trim the A-F. Ideally, the system will make only very minor changes because your tune is very close.
However, there are plenty of ways to screw this up. So you must be careful with both the setup and tuning to ensure everything is correct.
Let’s start with the fuel delivery system. Let’s assume that you will “tee” off from the main fuel delivery system for fuel for the plate nitrous. This will demand a separate fuel pressure regulator to pull the pressure down from 58 psi to the typical 5 psi that plate systems use. The best way to do this is to create a full return system back to the tank for this fuel pressure. That way, you can tune the fuel pressure for the nitrous separately.
This also assumes—and this is very important—that your pump and delivery system can support the kind of power the engine will make.
A healthy 355 cubic-inch small-block Chevy with even single-digit boost numbers can easily make 600 to 700 horsepower. Plus, the pump must be capable of supplying that fuel volume at 58 psi, which is harder to do compared to the same volume at a lower pressure. Then, you’re adding additional load with nitrous. Let’s assume for a moment that you want to add another 200 hp of nitrous. That places the power at roughly 900 hp.
Feeding 900 hp with 700 hp worth of fuel at 58 psi and another 200 hp at 5 psi is no small task. Let’s use brake specific fuel consumption (BFSC) to evaluate what the engine needs.
A normally aspirated engine will use between 0.4 and 0.5 pounds of fuel per horsepower per hour.
This means if we make 500 hp (multiply 500 hp by 0.45, which equals 225 lbs. of fuel per hour. This is the bare minimum amount of fuel the pump must deliver at the rated pressure.
However, for a supercharged EFI system, we must use a less-efficient BSFC number between 0.60 and 0.70, which means we must deliver more fuel per horsepower per hour.
One reason for that is to ensure we can deliver enough fuel to create the power, but also because with a supercharged engine, we have to deliver enough fuel to cover the power required to drive the supercharger. That may not sound like much, but that could easily be 50 hp or more. That 50 hp (at 0.5 BSFC) demands 25 lbs./hr. of fuel just to spin the blower! Rather than add this to the total, we’ll just use a less-efficient BSFC number like 0.65.
So 900 hp multiplied by a BSFC of 0.65 = 585 lbs./hr. of fuel.
We can convert that to gallons of fuel per hour since that is the scale often used to rate fuel pumps.
To do so, we divide 585 by 6.25 lbs. since that’s the common weight of a gallon of gasoline.
This results in 585 ÷ 6.25 = 93.6 gal./hr. of fuel.
We must now find a fuel pump capable of delivering a minimum of 100-120 gal./hr. of fuel. We need this extra capacity because we need some head room to account for flow losses in the delivery system. Also remember, we must deliver that much fuel at a minimum of 58 psi. That’s a big task.
We won’t go into actual fuel pump recommendations, but just know that the typical electric in-tank fuel pump probably won’t be capable of supplying the volume of fuel this combination demands.
This package will demand a big fuel pump—something like an Aeromotive A1000 or one of the Holley big twin electric pumps.
An alternative idea (and the method we’d recommend) would be to build two separate fuel delivery systems—one high-pressure system to feed the EFI, and a separate low-pressure system for the nitrous.
We would make both of them return-style systems. That makes it more complex, but also easier on each system.
This also puts you into a smaller main fuel pump and there are multiple reasons why a smaller main pump is advantageous. But if we go into that—this will turn into a small book!
Another critical point:
It is imperative that, under load, the pumps receive a minimum of 13.5 volts.
The lower the delivery voltage, the slower the pump will turn and fall way short of its capacity. This is where many car builders screw up. Pumps that don’t receive this minimum voltage run hot and fail sooner.
And yet another important point:
Use a large-surface-area filter to prevent clogging and capacity reduction.
This is another common mistake we’ve seen with big-power street combos where the builder uses a big pump and tries to squeeze the fuel through a tiny filter.
The reason we are harping on this fuel-delivery point is that it is the key to making a big-power system work properly.
A fuel-delivery system that can’t deliver the volume will suffer a significant pressure loss under load. The very last thing you want with a supercharged or nitrous combination is an under-performing fuel delivery system. That will grenade an engine pretty darn quickly.
In tuning this combo, we would encourage you to set it all up first with just the supercharger and run it on a chassis dyno to make sure the supercharged tune is good. Get your fuel delivery up to speed, set the air-fuel ratio safely at 12.0:1, retard the timing under boost and make sure all of that functions smoothly before you attempt the nitrous.
Then, with the nitrous system, start with a very small tune-up, no more than a 100-hp shot for about two seconds.
Your chassis dyno tuner should be able to data log the details like fuel pressure, A-F ratio, and how much timing was retarded.
Run that test, then pull the spark plugs and study them closely. If all of that works and the fuel pressure is steady, then increase the amount of nitrous and test again. Be sure to monitor the nitrous bottle pressure as well since that’s a major factor that many overlook.
If this is your first time with nitrous, we would highly recommend finding a nitrous tuner who can help you.
We recommend Steve Johnson at Induction Solutions, but there are probably dozens of quality nitrous tuners out there who can keep you out of trouble.
We cringe at the thought of a nitrous backfire on a supercharged engine because you inadvertently set the rev limiter below the nitrous cut-off rpm. If the rev limiter starts dropping cylinders—that will create a very big, very expensive bang. So be careful.
We recommend not engaging the nitrous below 4,000 rpm under any circumstances.
Roots blowers make instant boost and the combination of boost plus nitrous at low rpm can be abusive on pistons. Let’s also hope that the top rings have a very wide gap, because you’re going to be making some heat. A spec of 0.018-inch is too tight. The recommendation would be a minimum of 0.022 to 0.024-inch.
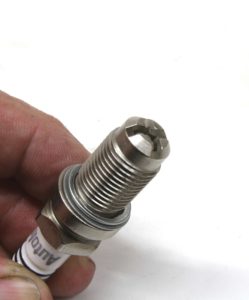
We also suggest using a spark plug with a non-projected nose—which means one with a very short ground strap. Just a supercharged engine alone makes much more heat, so avoid spark plugs with a long projected center electrode because that requires a long ground strap. That ground strap gets really hot and ends up glowing—and that can cause pre-ignition.
This kind of glow plug in the chamber can cause the fuel to ignite way too early, which can cause the engine to backfire. On a 6-71 engine, a backfire is really dangerous. With nitrous and a supercharger—it can cause a catastrophic engine failure.
To be safe, we recommend a surface gap spark plug to eliminate that possibility. Autolite offers a plug called the X-plus which is a spark plug with no ground electrode. Instead, they have milled a pair of slots in the end of the plug that creates four sharp points for the spark to jump across from the center electrode. I’ve tried these plugs on several supercharged engines and they work exceptionally well. The AR3933X plug would probably work well.
There is certainly a lot more we could talk about with this combination, but these recommendations will set you on the right path.
Let us know when you get it running. It sounds like a real screamer!
Hi im doung my first blower motor its a 9:1 383 stroker aluminum heads (Edelbrock e force) and were gunna run the weiand 144 at 5-6 lbs ive done two fitech installs thiscwill be the first with a blower im A bit nervous about my inital settings as far as braking in the cam etc wondering if the safe way would be to use a carb to brake in the cam ? I no the afr should be around 12 I just dont wanna havevsny coughs or mishaps n not be able to keep it running long enough to get the cam broke in any help with enitial set up #s would be greatly appreciated were using the 50001 kit that supports up to 600hp ive heard if you adba pump like the aromotive 1000 the unit will support 700+ hp your thoughts and suggestions would be greatly appreciated thank you! Chris
I have magma charger on my 99 Corvette with methanol injection just prior to throttle body. For the first time, after driving car the supercharger has water condensing on outside of supercharger body. What is going on? The first 1/2 of supercharger is cool and wet (not experienced this ever before). It is humid and hot outside. Do you think something with my methanol spray has changed (too much methanol?) to cause this? Any suggestions?
That’s exactly what is happening. The methanol is cooling the outside of the throttle body adn blower so much that it pulls water out of the air and it condenses on the outside of those components. If you ever watch a methanol supercharged engine idle, the entire blower case will condesne water if the humidity is high enough.
I recently put my super gas fb on the street..it has a 671 bds..is there any way to use a bug catcher instead of carburetors
Hello very nice to have someone so knowledgeable in the Fi tech system I run a super competitive nova and it is 496 strokes 871 blower and Fitch system your info is very valuable cause I am not so knowledgeable the car runs 520 s in the 1/8 but not consistent enough not so familiar about system I also use msg view for ignition is there any way to get this to run consistent 5s thank you for your time KC