Summit Racing has its own line of Pro LS Camshafts designed specifically for GM/Chevy LS and Vortec engines.
The camshaft development team told us they did their homework when designing these cams, and that they offer significant benefits over other LS camshafts on the market.
For starters, every Pro LS Camshaft features lobes that were designed to be aggressive, but not too aggressive as to be hard on the valvetrain.
Then, each cam’s valve lift was optimized to work with factory rockers and quality spring packs, so installers wouldn’t have to endure more upgrades and expense to get their cams to work.
And for exact, repeatable engine behavior, specific valve opening and closing events were placed in logical increments.
Want more information on the nuances of camshaft valve events? Check out these articles:
Comparing Camshafts: A History of Camshaft Specs and Choosing the Right Cam
Comparing Camshafts (Part 2): Consider Individual Timing Events When Choosing a Cam
Summit Racing’s Pro LS cams are 100% made-in-the-U.S.A., and every Pro LS Camshaft begins with American 5150 bearing quality steel.
But, as they say, the proof is in the pudding, and the Summit Racing folks were nice enough to give us a behind-the-scenes tour of the factory making its Pro LS Camshafts.
***
How a Camshaft is Made
Step One: The Lathe
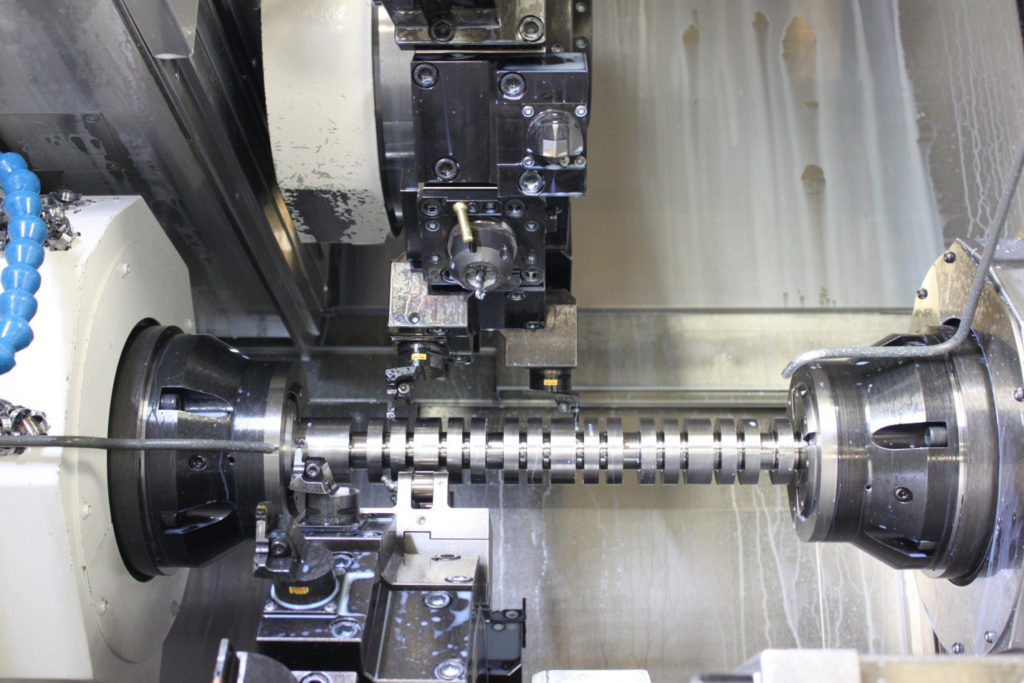
The camshaft is first installed on a lathe which will define the cam’s lobes, journals, and grooves.
(Image/Summit Racing – Brian Nutter)
One of the first operations is to spool the material on a brand new state-of-the-art lathe with live tooling.
This one machine turns the ODs of the journals and the lobes, does all the grooves, the front face where the cam bolts will go, and the sensor ring—all in a single process.
Any time a blank doesn’t need to be moved to a different machine for the next operation, it increases accuracy.
Step Two: Gun-Drilling the Camshaft Core
Let’s back up a moment.
Before it arrives at the factory, the camshaft material is vacuum degassed and spun on a vertical caster. High-density steel moves to the outside of the bar for a more durable surface.
This is an important step, because the process removes any inclusions and impurities on the material’s surface. Those impurities could lead to cracks once the camshaft is installed.
The lightest parts (e.g. the impurities) move to the center of the bar and are removed when the long drill bit drives through the camshaft core during the gun-drilling process.
Once the core has been drilled, the cam is ready for roughing.
Step Three: Roughing the Cam
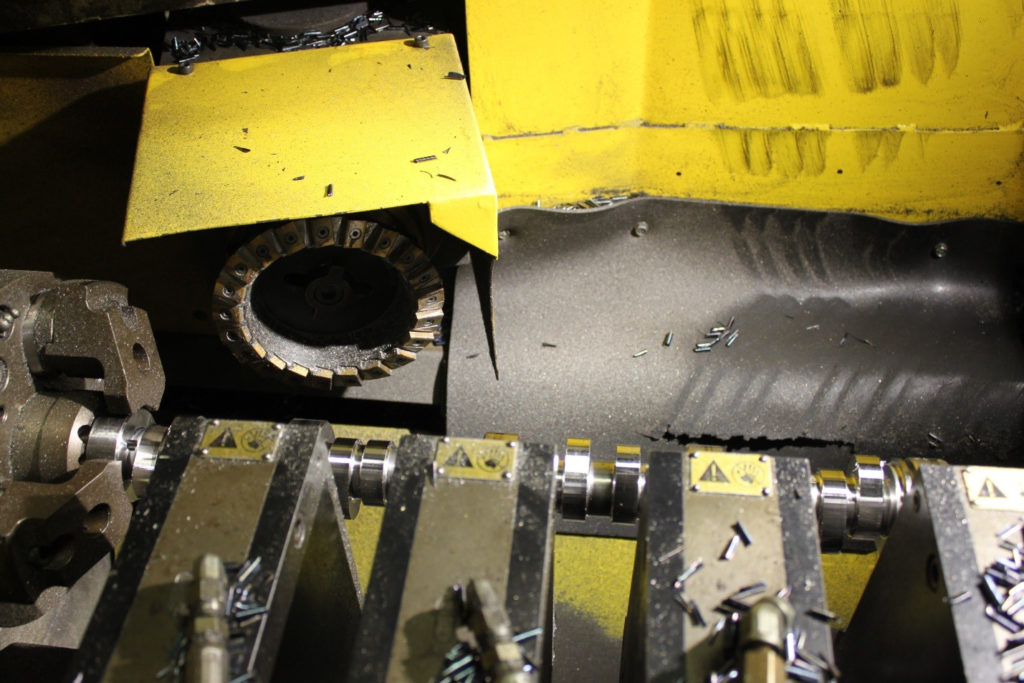
Here, excess material begins to be shaved away to start giving the cam its proper profile. (Image/Summit Racing – Brian Nutter)
Because Summit Racing’s Pro LS Camshafts are already tailor-milled specifically for individual part profiles before they reach this step, the most that will need to be ground away in the finishing operation is .015 inch. This creates a more uniform part with more case depth.
Why is that important? Some cam manufacturers use a standard core for multiple part profiles, which may require as much as .050 in. of material to be removed.
This could cause localized hot spots on the cam lobes—spots that may lose temper and eventually fail.
Step Four: Heat-Treating the Cores
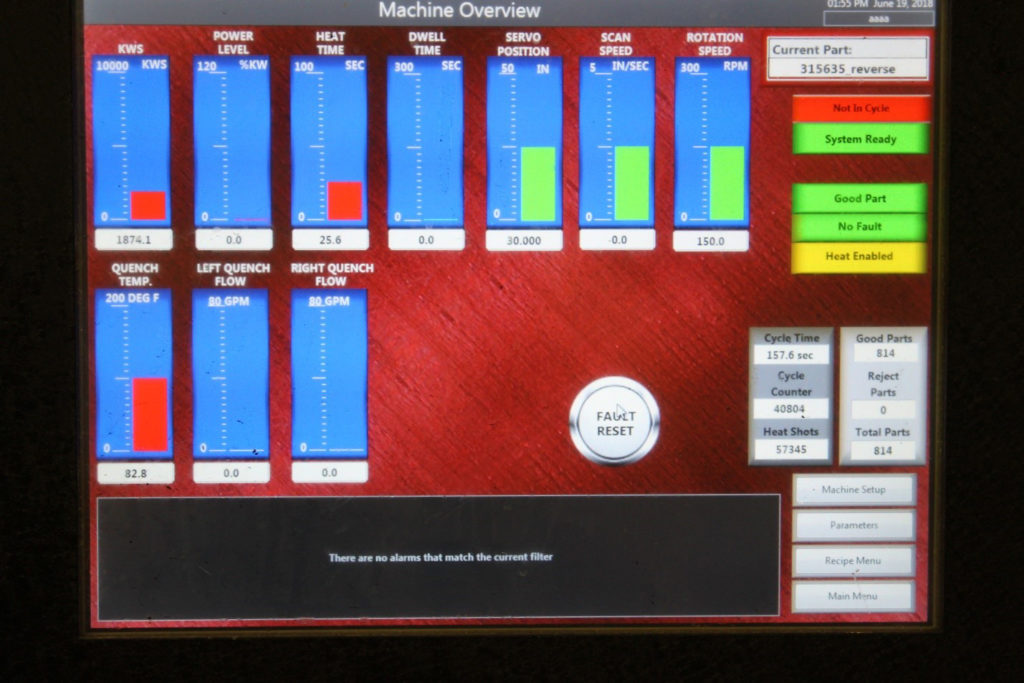
Each core endures a heat-treating process to ensure camshaft durability. (Image/Summit Racing – Brian Nutter)
Next, the roughed-in cores are heat-treated with a specialzed proprietary process.
The process is strictly controlled to ensure the right amount of heat, frequency, time, quench, and tempering in every part.
Step Five: Grinding the Camshaft Journals
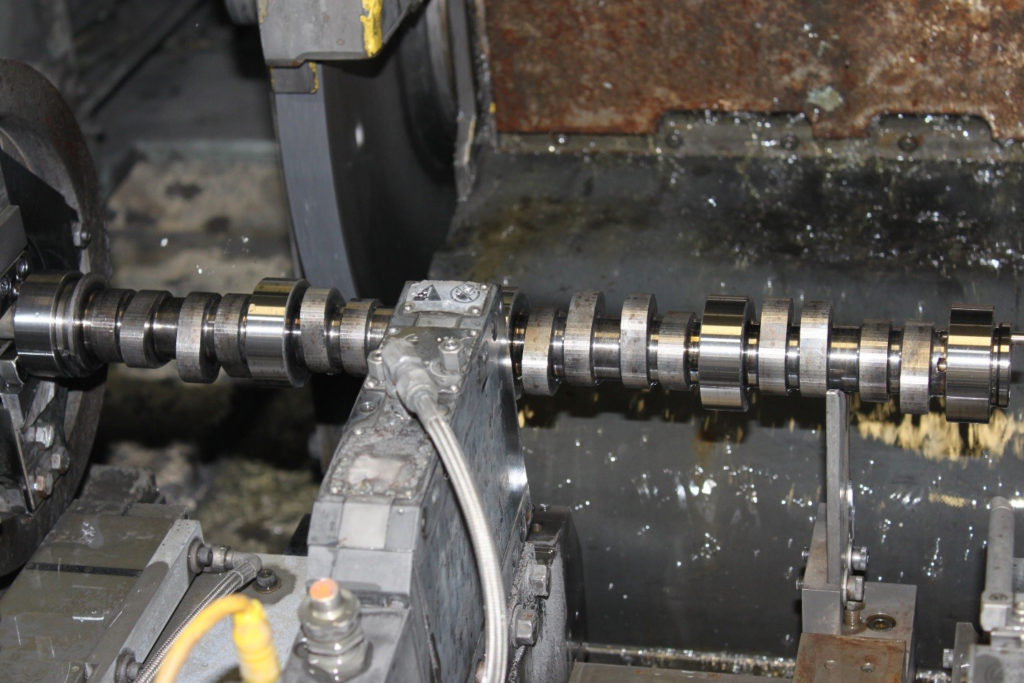
A diamond grinding wheel gives each journal a precision surface. (Image/Summit Racing – Brian Nutter)
This is a Landis Model 3LB Cylindrical CNC Grinder using a CBN diamond grinding wheel to precision-grind each camshaft journal. This process results in superior cam roundness, eccentricity, and runout.
Step Six: Finishing the Camshaft Surface
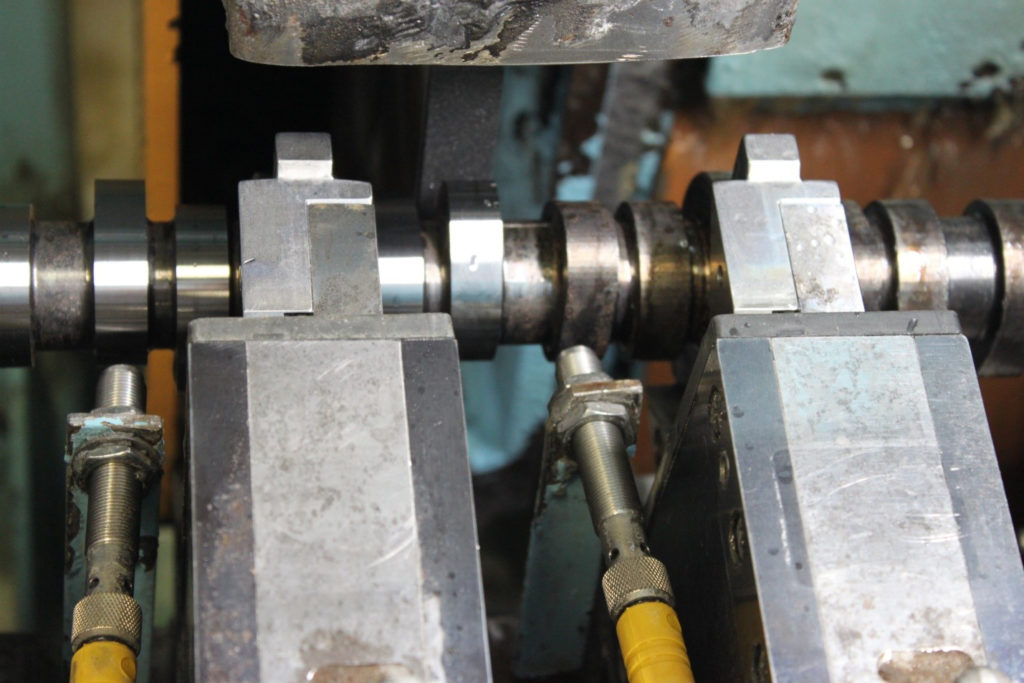
Each camshaft lobe is precisely ground to exact specifications. (Image/Summit Racing – Brian Nutter)
Finally, Summit Racing’s Pro LS cams are finished on a Landis 3L Cylindrical CNC Grinder using a CBN (diamond) wheel.
This gives each camshaft a smooth finish, with a superior angle, velocity, taper, and center deviation.
Some companies use older Okuma and Berco grinders, often with stones rather than diamond wheels. The problem with that process is that it can leave deep grooves that require heavy abrasives or other techniques to remove in the polishing operation. Compensating for a sub-par finish with excessive polishing can significantly distort the cam profile. Check out the profile graphs below for evidence.
Step Seven: Final Quality Testing
Visual standards for grinding chatter have proven ineffective in measuring a cam’s potential to set up harmonic vibrations in the valvetrain. Those harmonic vibrations manifest in noise that actually sounds like whistling when the valvetrain is spun at high speed.
Summit Racing Pro LS Camshafts are tested by precision Adcole equipment. This sort of testing is much more accurate and the machines use special algorithms to ensure the lobe has been ground correctly.
Because the parts are so smooth right off the Landis grinder, only minor polishing is required to finish the part providing a more accurate profile.
Here’s a good comparison.
These are the test results from a typical LS cam that’s been ground with stones on an older machine.
Note that every square on the graph below is in .0002 inch increments with the 16 lobes toward the bottom.
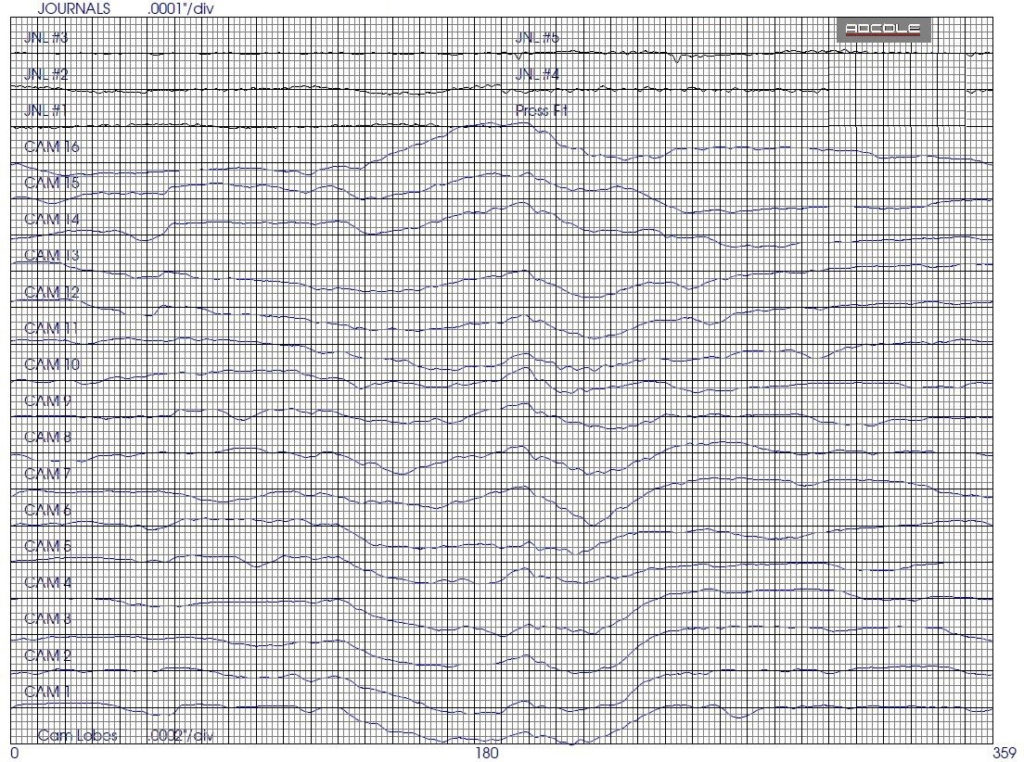
These are the Adcole test results from a camshaft ground with stones on an older machine. (Image/Summit Racing – Brian Nutter)
Not so good.
Now, here are the results for a Summit Racing Pro LS cam:
The results are much smoother and accurate than the first cam tested. These better results are thanks to the precision Landis grinder using a diamond wheel.
[…] Want to see how these cams are made? Check out this story on manufacturing the Pro LS Camshafts. […]
[…] Want to see how a camshaft is made? Check out this factory tour. […]
“They” may say that the proof is in the pudding, but the saying is actually:”The proof of the pudding is in the eating.” I think the cam manufacturing process looks like a wonderful recipe.
In the medical field a 5150 is placing a person on a 72 hour physiological hold.
Great explanation of hi grade engineering and manufacturing execution. Very uncommon is today’s mostly made off shore world. Bravo.
[…] Want to see how a camshaft is made? Check out this factory tour. […]
[…] To learn more about how the Summit Pro LS cams are made, read How a Camshaft is Made: A Tour of the Summit Pro LS Cams Factory. […]
[…] If you want to learn more about the manufacturing process and quality of the Summit Pro LS cams, check out Manufacturing Summit Racing’s Pro LS Cams. […]
[…] If you want to learn more about the manufacturing process and quality of the Summit Pro LS cams, check out Manufacturing Summit Racing’s Pro LS Cams. […]
Do you have a can for the Dakota 4.7 motor ?
So who is making the cams, clearly summit does not own and run a cam grinding facility.
Interesting point of using diamond wheel on a ferrite material. I would imagine those diamond wheels would prematurely wear out because of irons nature in dissolving carbon quite readily. I have always seen other materials used for machining ferrite based metals. Ceramics mainly. So how are you able use diamond on ferrite metals?