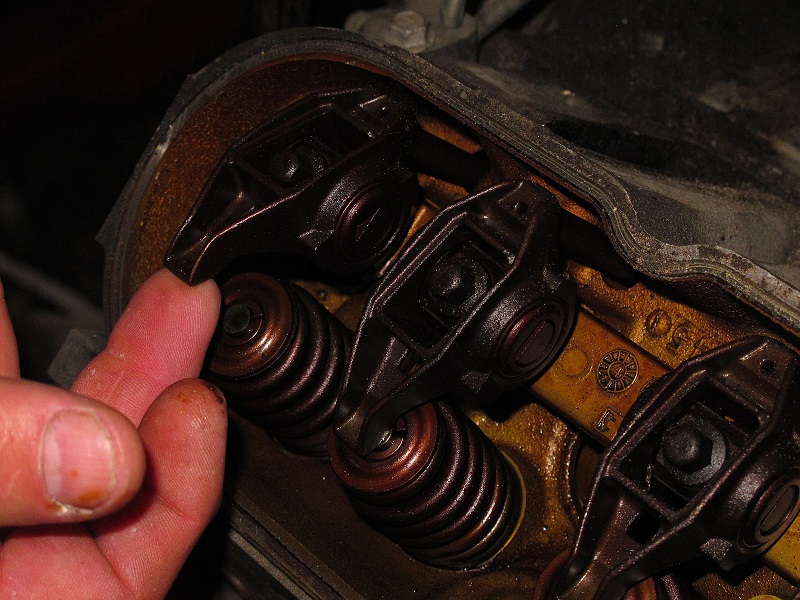
(Image/OnAllCylinders – Patrick Hill)
I just bought a used 5.3L LS engine out of the junkyard and after we got the engine back to the shop and mounted it on an engine stand, we decided to do a leakdown test. We checked all eight cylinders and the average was close to 40 percent. We removed the oil filler cap and it sounded like most of the air was coming from the oil pan—which means the rings are weak. Should we take this apart and put new rings in the engine or do you think it would be okay to run it as it is? — F.D.
…
Jeff Smith: If I remember correctly, David Reher of Reher-Morrison Racing Engines said he doesn’t put much stock into leakdown tests, so let’s drill a little deeper into your question.
If you want to start a big discussion on any engine-building forum—ask about leakdown testing. Everybody offers opinion but few facts. Let’s deal in facts.
A leakdown tester can point out problems that a compression test won’t.
First, I would run a compression test looking for weak cylinders. You didn’t mention whether there were a couple of cylinders that were greater than 50-60 percent. Let’s say that they were all within 10 percent of each other in pressure with a peak of around 150 to 170 psi. Those are pretty good numbers. Compression ratio is not necessarily an indicator of high cranking pressure, because there is no direct relationship between static compression and cranking psi due to cam timing.
When you’re cranking the engine over at around 350 rpm, the valve overlap period has a great influence on cranking pressure. Valve overlap is where the exhaust valve isn’t quite shut when the intake valve begins to open. So for a period of a few crankshaft degrees, both valves are open. Given this situation, it should be obvious that the cylinder cannot begin to build pressure until the exhaust valve closes.
So if we have an engine with a high static compression ratio—say 11.5:1 but it is also equipped with a very long duration camshaft with a tight lobe separation angle (LSA) that determines overlap, then the cranking compression could in fact be lower than the same engine with a 10.5:1 static compression ratio with a much shorter cam with a wider LSA.
There’s much more to this if someone wants to ask a question about dynamic compression versus static compression.
To get back to your question, as long as the cranking compression is relatively equal, I wouldn’t worry much about the 40-percent leakage. One test you could try is to pump a shot or two of engine oil into a cylinder, crank the engine over for a dozen rotations or so and try the compression test again. This works on engines that haven’t run for a long time. You mention that this was an engine that had just come from the junkyard where it might have been sitting for a year or so. If that is the case, then this test will help.
If the compression increases, or if the leakdown is reduced then it’s clear that the rings are worn. This is evidenced by the fact that you can hear the air leaking into the crankcase. That indicates that the air is leaking past the rings. But a 40-percent figure does not mean that the actual cylinder pressure will be lower by 40 percent. The reason is that the pressure rise and push on a running engine piston takes place very quickly. In order to lose 40 percent of the cylinder pressure there would have to be a small hole in the piston to accomplish that. I think this is at least partially why Reher made that statement.
Would your engine run better and make more power with new rings? The answer is closer to a ‘Probably’ than an outright ‘Yes!’
That’s because simply stuffing new rings into an engine with glazed cylinder walls will only help the seal slightly. Doing this job correctly requires boring the cylinders, a precise honing procedure, new pistons, and fresh piston rings.
On the opposite side of this ledger is how good late-model engines are these days.
I purchased a used, but complete, iron block 6.0L engine a couple of years ago. I took it apart, cleaned it, and then put it back together with the original rings and pistons—not touching the cylinder walls except to clean them. After a couple of hundred dyno runs, that engine tested recently with less than 20-percent leakdown. I have no idea how many miles were on it, but it’s a 1999 6.0L so it’s had a solid 15 years to rack up miles.
If your goal is to make lots of horsepower, then yes take it apart and put in new pistons and rings. It does not make sense to just put new rings on the old pistons. This is because much of the leakage from the rings results from lost sealing between the rings and the ring grooves.
I’m not aware of any testing that proves this, but it’s a good possibility that there is greater leakage past the ring grooves than there is between the ring and cylinder wall. I base this assumption on the fact that aluminum pistons are softer than cast iron cylinder walls, so the wear will likely be greater in the ring groove between iron rings and an aluminum piston.
Great answer sir
Great answer covering the bases!
Jeff I have a question concerning the leak down test. If you test at top dead center(and you have excellent results) what about pressuring the cylinder with the piston at bottom dead center. I know you would have to back off the rockers to do this, but would it be worth the effort to check for cracks in the cylinder? Or is this a waste of time?
I would think that the results might be similar, but a better question might be why this would be important. I think that leak-down would most critical when cylinder pressure is the highest. But a 20 percent leakdown doesn’t mean that the cylinder loses 20 percent of the pressure – mainly because there probably isn’t time for that to occur. So leak-down is really just an indicator of a potential problem. For example, Bill Jenkins once said along the lines of that a 20 percent leakdown from an exhaust valve isn’t nearly as detrimental as that same leakdown located at the intake valve. There’s probably much more to that that would bear investigating.
Bill was corect about in take valve ver. Exhost. The first engine I built,348 chev I over wound it and bent an intake slightly, down about 25 lbs on test. It would backfire and dropped from 15 mpg to 5mpg
Can you do a leak down test with intake off injectors out and a smog pump that vents into cylinder head?
Yes keep in mind that a leak test is really intended to be used as a comparison between cylinders instead of using the leak percentages as a go or no go number. With intake off the numbers will probably be higher.
Jeff, it’s funny to me that you opened with a reference to David Reher. I did not know what a leakdown test was until, as a young Car Craft subscriber in the mid 70s, I was reading a most entertaining Rick Voegelin story about life on the road with R-M-S and their D/MP-E/MP, 288 CI Stingray. With the engine apparently going away, they leaked it down. Rick wrote that, when fresh, the engine leaked 3%, (!!-I was astounded by this!), and now they had one cylinder leaking something like 70%. The engine was found to have ingested a single needle bearing from an unknown source. “It may have had some help”.
I got 3% leakdown on an engine with only 5 or 6 hand turns on it. Plateau honed with torque plates, custom CP pistons with steel rings, 5 angle valve job.
An ex race car champion claimed that once their engine reached 10% leakdown, they tore it down.