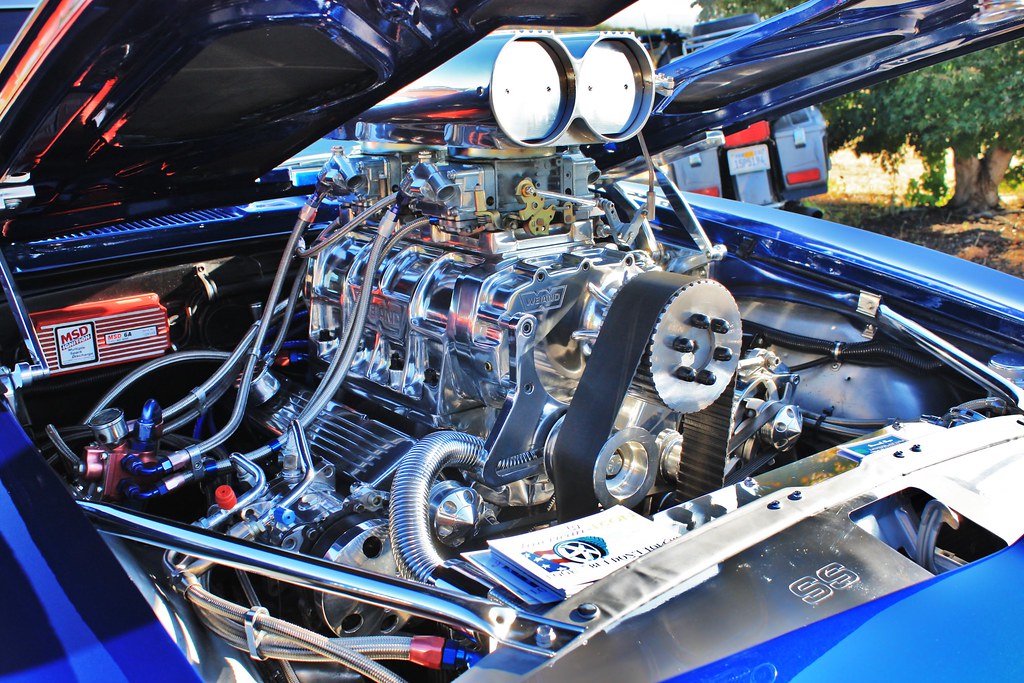
Can I put a blower on my balanced and blueprinted 383 c.i.d. stocker motor that has 10:1 compression? I just want it for looks, not to race. – G.H.
…
Jeff Smith: At first, my gut feeling was to answer no—it’s not a good idea.
The only way this will really work is to set up the blower to spin very slowly and make less than 5 psi of boost—which defeats the whole purpose of having a supercharger in the first place other than the visuals.
But then I thought about it more, and there are several approaches to this question that would make it feasible.
While you say this is strictly for looks, we both know that once you bolt a blower on the engine—you’re going to run it with your foot buried in the throttle. There’s no way to avoid that!
The idea is to avoid running into detonation problems from excessive cylinder pressure. There are ways to avoid detonation, but require making sacrifices or investing in additional systems to make it work. On the plus side, with 10:1 compression—that motor will be crisp!
You didn’t mention whether this engine is carbureted or runs EFI.
We’ll assume it’s carbureted but that really isn’t critical.
Any engine with a 10:1 static compression ratio is right on the edge of working with 91 to 93 octane pump gasoline, assuming an aggressive timing curve intended to maximize power.
If we now add a supercharger even with just a small amount of boost (let’s say 7 psi), this is roughly equivalent to raising the static compression ratio to 14:1 at full boost.
Conventional wisdom holds you can’t run an engine on pump gas with a 14:1 compression ratio. Having said that, this is the effective compression ratio at that amount of boost.
At part throttle running around town, you probably could get away with running a blower very slowly and the engine might not detonate. But you’d never be able to go to wide-open-throttle (WOT) because the engine would detonate badly unless the timing was severely retarded.
At that point, it might actually make less power than it would normally aspirated because of the combination of retarded timing and the power it takes to turn the blower.
Consider an E85 Conversion if Fuel is Readily Available
One option would be to convert to E85 fuel. This is a pump gas—but its availability is rather limited outside the Midwest. This fuel is 85 percent ethanol—essentially grain alcohol. The other 15 percent is a cheap grade gas—likely something not quite as good as base grade gasoline. Combined, these two fuels are worth an octane rating somewhere in the neighborhood of 100 to perhaps 105 which is equivalent to a mild race gasoline.
The downside to E85 is you can’t just pump it in the tank and run. It’s not that simple. Ethanol creates about 70 percent of the heat per pound of fuel compared to gasoline. Which means you would have to burn more fuel to make the same power.
This means an E85-dedicated carburetor, or—if the car is fuel injected—a dramatic 30- to 50-percent increase in the injector size.
Of course, you could run your engine on 100-octane race gasoline and accomplish the same thing with no conversion costs, but at $7 to $8.50 per gallon that quickly gets prohibitively expensive.
We have run a 10:1 compression 4.8L (293 c.i.d.) LS engine using a blow-through carburetor and a Vortech centrifugal supercharger.
With 6 lbs. of boost, we made 500 rear wheel horsepower. But this was using 100-octane race gasoline.
It’s possible that you could also mix pump gas 50/50 with 100-octane fuel to produce a 95- to 96-octane fuel that might allow the engine to run cleanly but still with retarded timing.
Another idea would be to convert this engine over to run on E85. This fuel not only increases the octane but also adds inlet air cooling benefits that would likely offer benefits that would allow us to make even more power.
A major problem is that E85 is possibly not available where you live. Next, this conversion, even if you have an EFI engine still requires some sophisticated tuning techniques to get it right. From your question, we’re going to guess this may not fit into our plans.
Consider Part Changes to Lower Static Compression Ratio
Another alternative if you still want to run a blower on your 383 c.id. engine, would be to change parts to lower the static compression ratio. You should be able to run a 7-8 psi blower with a 9:1 static compression ratio and the engine might run fine on 91 octane fuel.
Changing pistons is the best way to affect this change, but it might be possible to reduce compression ratio by switching heads and adding a larger combustion chamber.
It depends upon the existing heads’ chamber size. If the chambers are already large, then you may have to go to lower-compression pistons.
Water/Methanol Injection Could Work Too
As yet a final option would be water injection. Running a water/methanol injection system like that offered by Snow Performance, combined with keeping the timing conservative, might reduce the inlet air temperature sufficiently to keep the engine out of detonation.
Water does a great job of reducing the inlet air temperature. The engine benefits because for every 25 degrees of reduced inlet air temperature, the engine’s octane requirements are reduced by one full point—from 96 to 95 octane, for example.
Methanol combined with the water further reduces inlet air temperature but also adds its own octane to the mixture, so this type of system has some real advantages. The key is to add the water into the airstream as far upstream as possible because it gives the water the time needed to reduce the temperature.
Plus, water also tends to slightly reduce cylinder temperatures during combustion. Tests have shown that water injection alone will reduce inlet air temperature roughly 50 degrees, which is equal to reducing the octane requirement by two full points.
All of this combines to improve the chances that the engine won’t detonate.
…
The bottom line here is—you could get a blower to work. But it will take more work than simply bolting one on your engine and driving away.
It would take professional-level tuning skills and careful attention to detail, but it can be done if you’re conservative.
The key to making this a successful venture would to become fanatical about preventing detonation.
Option #2? https://www.streetmusclemag.com/news/video-we-dare-you-not-to-laugh-at-this-fake-supercharger-system/
What else do you want to know? That was pretty mind boggling!
Very nice job of looking at this from many different angles or perspectives. My initial answer is no. But the difference you nicely pointed out is what could be done and what should be done.
Hi there can i put a small block blower on top my standard engine in my commodore v6 vy 2002 model if i can what size blower can i use
No you can’t. I don’t believe it will line up to your blot pattern and it will probably be too big for the V6 intake manifold
Like all the information great write you answered a great deal of questions. My question could you run thicker head gaskets to reduce compression?
I would say yes I’ve read that just a small increase in head gasket thickness can decrease compression quite a bit problem solved I would try to be precise with what compression I was left with though with precise measuring
Compression and boost is only limited to the quality and octane of the fuel you are using,you can also use a boost reference timing retard box such the MSD to retard the timing as boost goes up.the same applies to your fuel,use a boost reference fuel system to increase the fuel pressure and volume as boost increases.
Certainly appreciate the logic of this conversation. Always thought you had to run low compression for forced induction. However I recently put a supercharger kit on my E 92 M3which runs 12.0 static compression. Over 2000 of these kids installed. Don’t know how it works but somehow this motor stays together he and makes insane power
This is what happens when an uneducated person has a podium to speak from and tries to sound educated. Positive displacement blower vs a non positive displacement matters. How about camshaft timing? By extending the centerline in the exhaust that cools the spent charge and reduces detonation as well. There are far more factors that come into play. But I do not have an internet platform so I must be an idiot.
I totally agree with “im non educated” in that this is old wives tale myths. Actually it was a product of the time, or years ago. There are plenty of high compression (SCR) engines, 10.5:1, 11, 12, 13:1 SCR & higher, & are also boosted.
Of the rip, Dynamic Compression Ratio (DCR) should have been mentioned, because this can completely affect the “so called” compression ratio the engine sees at specific points thru rpm powerband. Camshaft mechanical timing, & each of the timing events, then how the electrical timing is set accordingly & in conjunction with the complete engine as a whole, can make all the difference in how not only this is done, but getting optimal performance, good gas mileage, & longevity from any engine.
These are all still very misunderstood subjects, including properly match all of your engines components accordingly, & to specific end results, or what are you really even trying to build? A street machine or torquer, something that will see over 6k rpm much, making most power lower in the power band, or some all out track high RPM. Horsepower racer? Or something in between?
After deciding this, then building an engine & matching all the components correctly for these results. This sounds like it should be common sense, that i shouldn’t have to point out, yet this is so misunderstood, & parts all mismatched in all directions.
As far as higher compression & power adders, such as turbos, superchargers, NOS, on top of what i briefly mentioned above, with the advancements in EFI, & EFI systems, and tuning, the ability to run high compression with power adders has become all that more possible.
Higher SCR & with the correct DCR for that specific engine combination, when coupled with a turbo or supercharger (SC), but especially with a SC, can have alot of benefits when done correctly. Higher SCR & DCR will give you that low end torque & snappy pedal. Even tho any power adder if matched right, but I will focus on the supercharger in this case, & specifically due to them being somewhere limited to the others in the amount of available variables. In other words for example, there is an abundance of different types of turbos & how they can built, or customized. From T3, T4, T3T4 hybrid, T45, inducer/exducer, AR’s of either compressor &/ or turbine, etc etc etc. Sure there are different types of superchargers, Roots or centrifugal, small, medium or large, can change pulleys to lower or increase boost. Of course they can be customized more, but nothing like turbo options. Regardless they are linear to RPM. More RPM more boost. But more RPM’S equals more HP needed, & more boost equals more heat. Remember the faster we turn the rotors in the SC & the more air it compresses, this makes more heat. Just as making power is linear, the loss of power at high rpm/rotation starts to become linear also. It just compounds.
And so…. by having real low compression, translates to less low end torque, until the SC spools up & makes power, & the high the RPM’s the more power, but at the sacrifice of more hp loss & more heat, which kills more HP, & increases detonation possibilities. So it’s kinda a catch 20/20 .
So now, we increase the compression, obviously accordingly to a specific build, & hopefully by an experienced engine builder, but we no longer need to push the SC as hard to get the same target results, & really much better results over all. Depending upon the build, we either leave pulleys, or even change them so the SC rotates a little slower at low RPM, reducing possible detonation if applicable, & either way, have immediate low end torque & responsiveness, & as RPMs increase so does boost, with less HP loss to the less moving mass of compressing air & less heat. Not to mention, less abuse on the SC,
I built a highly modified C4 Corvette (91 Coupe), that besides custom body, interior, i reworked almost everything else, chassis, suspension, brakes, etc in that it can run with any C6, C7, Mustang, etc. Of course, no matter the amount of serious reworking of the C4 overall handling, chassis -frame (uniframe, unlike a unibody), & suspension to bring it up to C7 standards, the C7 will still be Superior to a degree due to some limitations of the C4. But its damn close. However, it was a massive undertaking & i have years into it, & it’s almost complete.
& are running a 10.8:1 SCR / 8.2 DCR 384 Stroker SBC with twin turbos pushing 10 PSI of boost.
740 HP / 835 TQ, and barely breaking a sweat. Again it can be done, its all in the build, & by understanding the build, & then building it properly. I could increase the boost, it is a Dart block with forged internals, etc etc. But was built most as a street machine. And without abusing her, Redline at 6.2k, 10 PSI, & at 2k RPM i am over 500 ft lbs of torque & it just climbs. And she is gone!
I want to build a street rod need to know what I need to run 383 stroker with a 144 blower safely on the street while having fun foot to the floor. Need the details what pistons,heads,can, crank,rods,rocker arm size using roller cam to achieve this level of fun?
00321 crower solid tappet .. Afr heads 195 cc 1095.716 head cam and head match perfect . Roller rockers 1.6.. oil pan scraper .. valley tray… 10thou deck.. 30thou gasket .. 18cc pistons with egale kit … you get 9.61 compression ratio /.. 3.8 lbs boost … static compression 12.1 ..l timing 13 -34 total.. 3inch spacer .. 850 double pumper … 83 front 93 back,jetting,, need good set exaust l use 2 inch hooker ,, 3in exaust pipe can run 91 octane ,Ngk plugs 5 heat range.. 1206 intake gasket… ~have good 600… mine idles at 550 cold ,,, 850 worm … red line 68 .. msd 6.. revs unbelievable fast …
I really like your topic, I was wondering about compression on my bbc. I’m running 9:1 with a 871 blower but now I’m having second thoughts. It’s on a boat and I sure don’t like what you said about detonation. So I guess what I’m saying is do you think all be alright with my application?
Can I put a blower on a 2000 Silverado v6
What about the original engine question at an elevation of 6500 amsl?
I’m building a 350 ,4bolt mains ,small block chev for a hotrod what size supercharger do you recommend and what compression ratio , looking for 450 -500 hp cheers jack
I have 305 engine in Chevy Camaro 87 and my setup is:
compression 10:1
edelbrock performance intake
edelbrock 1406 highly modified (including secondaries air valves weights modification – drilled away part of it), 70×37 rods, primary 0.098 jets, secondaries 0.105 (over table), orange springs, marine accelerating pump
underlay carb 1 inch spacer – opened style all barrels together
choke removed
two blow by valves – one was not enought to blow all the air away when cruising-idling
blow-through setup “paxton style”, carb is box
air-water to water cooling with high pressure pump
cam performed stage 3
roots blower from Jaguar 4.0, Eaton M116, original pulley
flowing 0.3 bar = up to 7 PSI
AFR runs IDLE 14-16, low power/cruise 12-13, high power no boost 15, high power boost 12-13, WOT 13
distributor with high voltage coil
HEI from Turbo TransAm 79 with pin detecting pressure (pressure switch) = dropping timing of 5 degrees
distributor lock in half movement = low advance when cruising
vacuum distributor connected to timed port
high flow oil pump installed
needed due to compression also starter with gearing to pull more torque
Without modification of distributor and locking it, it was almost impossible to make this setup without pinging/detonation. Engine runs well also with total lock of advance. I went also with water injection, but left this setup and removed it from engine. Also important is using HEI from T TransAm
2 years of modification process!!!! never again
next parts in car:
ceramic clutch
clutch pusher stage 3
transmission TR5060 from Camaro SS2012 – modified tunnel in car
unique shaft concept to fit to 87 camaro
differential with locking from LS1 5.7 96
Fuel: Europe, so 95
Have the blueprint 383 stroker power adder. Compression is 8:9:1. Considering installing the Weiland 177 supercharger. How harsh is the 7″ pulley on engine vs 6″ pulley. It’s not driven often and this add on brings investment up to around $11,000. It’s in a 6″ lifted 74 K20 so vehicle weight is substantial. Hoping to keep this engine in one piece for next 15 to 20 years.
I want to build a 632bbc. I have 10-71 blower with mechanical injection on methanol. Want to use 12-12.5 compression with 360 cam heads. Have solid roller cam with .800 lift range. Was going to start with 1 to 1 on crank and blower pulleys. What are your thoughts and any info appreciated
TY