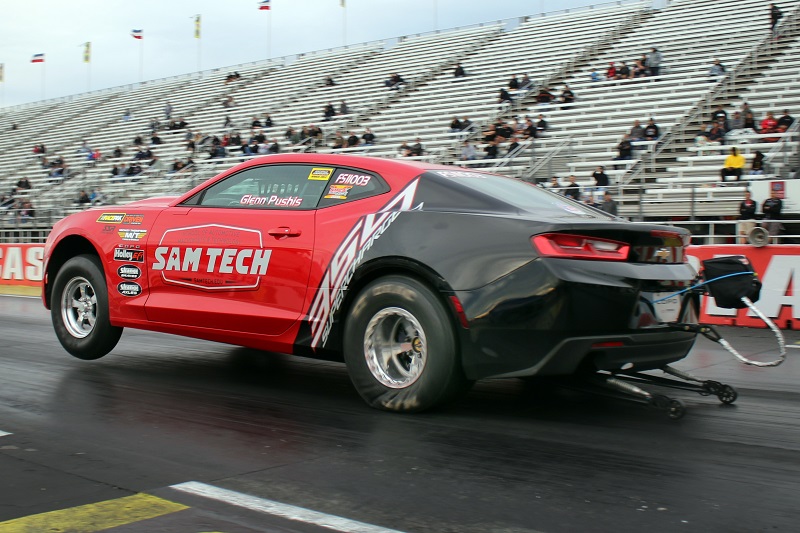
(Image/Stephen Kim)
EFI tuning, as we know it, is over. Stick a multimeter probe in it.
Gone are the days of simply setting the fuel and timing maps, then calling it good. These days, it’s all about vehicle computer calibration. All of a sudden, the OEs are kicking out highly sophisticated engine combinations that utilize direct-injection, variable valve timing, factory turbocharging, drive-by-wire throttle, traction control, and torque modulation systems.
Likewise, the newest crop of performance engines incorporate both direct-injection and traditional multi-port EFI systems. But wait, there’s more.
To complicate matters further, each onboard control module communicates across a complex electronic network, sharing and comparing information on the fly.
Consequently, today’s calibrator must not only tune the engine control module, but also know how to integrate the transmission control module, fuel control module, and body control module tuning seamlessly into the overall vehicle calibration. Considering that all of these systems are computer controlled, anyone hoping to maximize horsepower, torque, and drivability needs to have a good handle on exactly how to calibrate all of these different tuning variables, modules and other advanced systems.
Which is why SAM Tech established a new EFI Calibration program to add to its well-established portfolio of coursework. For decades, the school has earned a reputation for offering an industry-leading engine building curriculum that encompasses block machining, cylinder head porting, and CNC machining.
Its graduates walk straight out of the classroom and into championship-winning NHRA, IndyCar and NASCAR teams. SAM Tech’s vision is to bridge the gap between the current state of EFI tuning and the calibration demands of today’s sophisticated powertrain electronics.
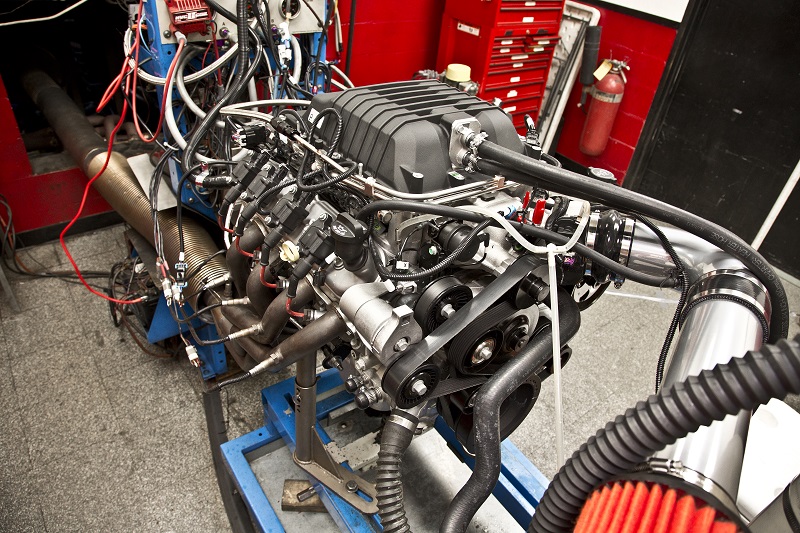
Learning to tune for power adders is a large component of the SAM Tech curriculum. Since centrifugal, roots, and screw-type supercharger all compress and heat the intake charge differently, the calibration strategies must be adjusted accordingly. (Image/Stephen Kim)
“There’s a big disconnect in the industry between people who want to learn about tuning, and what tuning actually involves. The calibration process is not for everyone,” said Jason Haynes, EFI Calibration Program Director at SAM Tech. “Calibration is a very intense process because you have to understand how EFI works, how the ECM logic works, and ultimately what the ECM is trying to control. Moreover, you must also have a thorough understanding of airflow and engine dynamics.”
In less than 10 years, the tuning arena has changed dramatically.
“With the advent of the new Ford Coyote small-blocks, you can move the intake and exhaust valves independently of each other. If you don’t have an understanding of valve events, and how moving the cams in a certain direction—and by how much—affects airflow, then you’re going to be lost,” Haynes said. “A two- or three-day weekend seminar does a good job of teaching the tuning process, but they assume that you already have the background knowledge in engine theory, airflow dynamics, valve events, camshaft design, turbos, superchargers, and nitrous. At SAM Tech, our curriculum teaches students all of that background information, as well as the math and physics behind it, to truly understand what the ECM is trying to achieve and control. We then roll that knowledge into making calibration changes in different software platforms to optimize performance as well as drivability and reliability.”
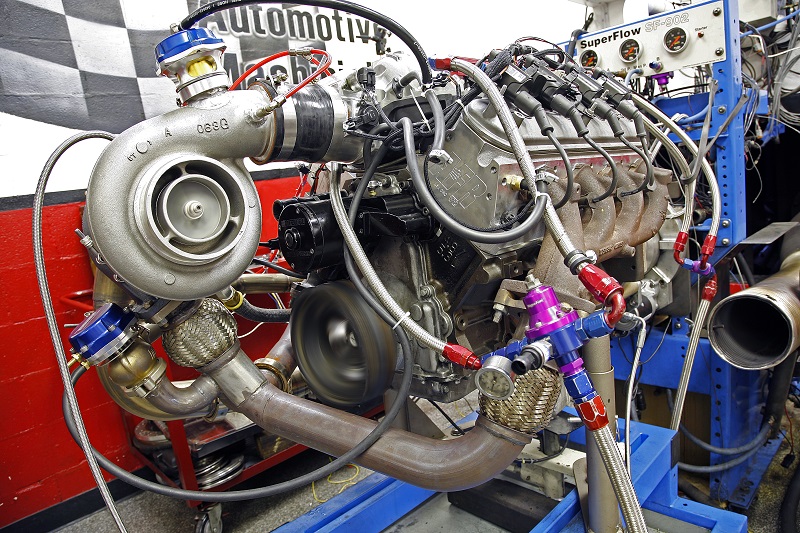
Pushing a turbo too hard can increase intake air temperature so much that it actually decreases power output. Learning how to read a compressor map is an essential tool for calibrating any turbocharged or supercharged engine combination, something all SAM Tech students are trained in. (Image/Stephen Kim)
To an unprepared tuner, the enhanced sophistication of today’s electronics—and the fear that comes with it—present a significant barrier to performance.
To a trained calibrator, however, conquering the opportunity offered by this same sophistication yields tremendous power potential.
“On a new twin-turbo, direct-injected, variable valve timing engine found in the latest Cadillac ATS-V, we can easily gain 100 hp and 100 lb-ft of torque at the wheels through calibration changes alone,” Haynes said. “Some of that gain is attributable to controlling the electronic wastegates on the turbos, but a lot of it is attributable to managing the valve events and airflow modeling as well. We can build pressure where we need to with the turbos, and alleviate pressure where we need to through the valve events.”
That’s just one example. Prior to joining SAM Tech, Haynes served as the Senior Calibration Engineer at Hennessey Performance Engineering as well as the Lead Instructor for HPE’s Tuner School. He’s also traveled the world teaching tuning seminars, and worked as a contract calibrator for renowned shops and race teams throughout the country.
As such, with the release of every hot new vehicle platform from GM, Ford and Chrysler, Haynes was called upon to crack the electronic brains of these new beasts.
His resume includes many firsts.
His calibration expertise helped Late Model Racecraft build the first supercharged C7 Corvette, the first twin-turbo C7, the first 1,000 rear-wheel-hp C7, and the first 9-second C7. Other achievements include calibrating the first supercharged S550 Mustang, and setting new records for hp and quarter-mile performance with the S550 platform. The body of knowledge gathered through these experiences offers insights into the forefront of EFI calibration, as well as a glimpse at what students learn inside the classroom and dyno cell at SAM Tech.
Calibrating vs. Tuning
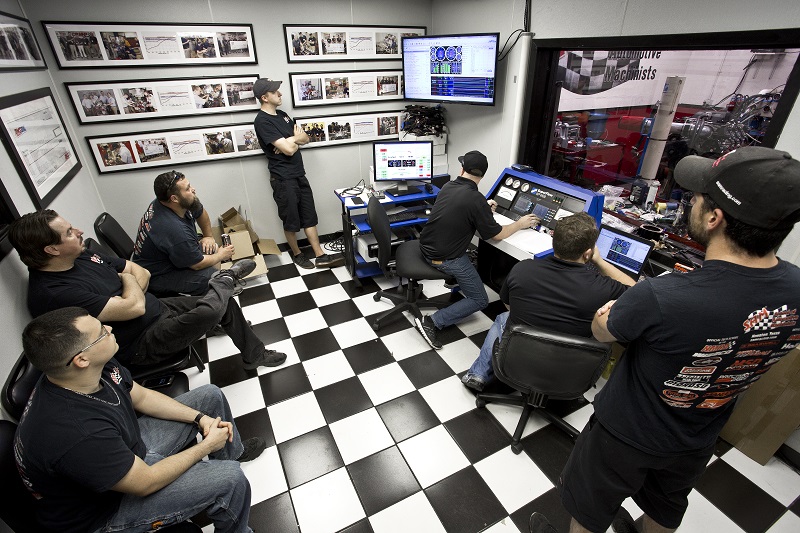
In the classroom, on the dyno and at the race track, SAM Tech students learn a versatile calibration process that can be applied to any software platform. By the time they graduate, students are well-versed in navigating the most popular EFI systems on the market from Holley, Fast, BigStuff3, HP Tuners, SCT and DiabloSport. (Image/Stephen Kim)
So what exactly is the difference between calibrating and tuning? It’s all about depth.
“In the near future, there will be a large separation between tuners and calibrators,” Haynes said. “Anyone with HP Tuners or an SCT programmer can call themselves a tuner. In comparison, calibrators must not only have a thorough and intense understanding of engine and airflow dynamics, but also understand the math and physics that govern the dynamics, control functions, and calculations the computer is performing. A one- or two-day seminar can give you a general overview, but to have a complete A-Z understanding of how to calibrate, you need to learn engine and airflow dynamics to understand all the equations and calculations the computer is doing behind the scenes.”
That might seem like overkill, and in some scenarios that assessment may be true. However, every tuner has run into situations where they’re left scratching their heads.
“A good example are the torque management systems on modern performance cars. With electronic throttle-bodies and torque modulation, the computer can shut the throttle to limit torque output and also limit ignition spark delivery,” Haynes said. “A lot of tuners run into this problem. If you understand how torque calculations and models work in modern engines and the math equations the computer performs behind the scenes to calculate and anticipate airflow and torque, then you can solve the problem.”
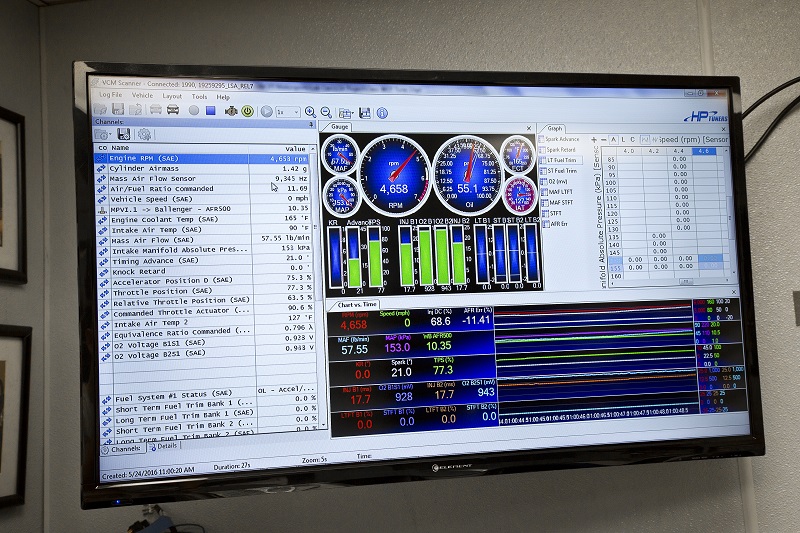
From intake manifold pressure to long term fuel trim, there’s real math and physics behind every tuning function at a calibrator’s disposal. Instead of merely plugging in random numbers based on internet banter, SAM Tech students calculate which values to enter based on the same math equations the computer relies upon. (Image/Stephen Kim)
Of course, knowledge is nothing without practical application.
“Once you’ve calculated and analyzed all the data, you then need to make calibration changes to improve all-around performance. This isn’t just about making dyno numbers, but also maintaining drivability as a car transitions from stock to modified to heavily modified,” Haynes said. “Lastly, it’s important to understand and consider emissions with performance modifications and calibrations as well. It’s kind of taboo to talk about in our industry, and everyone wants to sweep it under the rug, but now is the time to discuss and consider limiting emissions with performance enhancements. Paying attention and understanding it now will help separate your business from the rest of the pack.”
Valve Timing
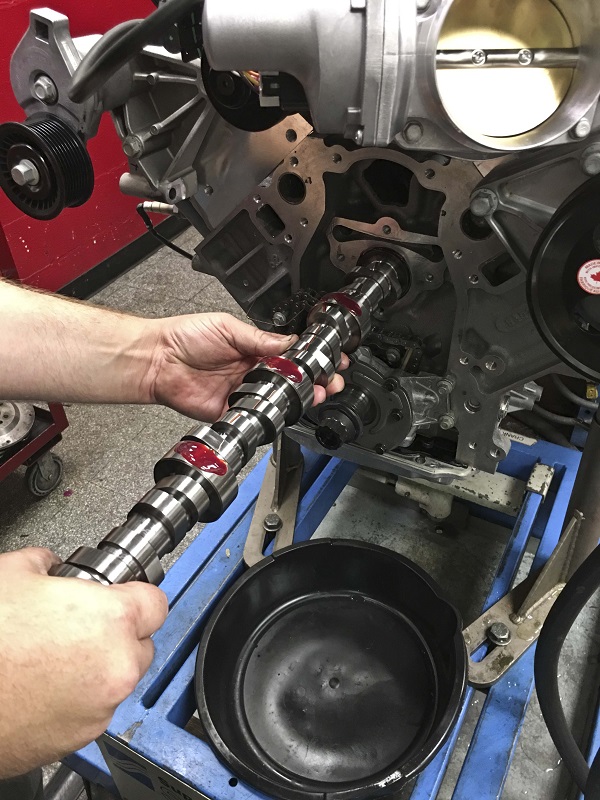
SAM Tech students spend several months learning about how duration, lift, lobe-separation angle, and valve timing affect engine performance and drivability. As such, students already have the background knowledge they need when it comes time to calibrate an engine’s valve events and cam phasing electronically by altering an ECM’s variable valve timing parameters. (Image/Stephen Kim)
Not long after GM introduced variable valve timing in the L92 and L99 small-blocks in the Cadillac Escalade and 2010 Camaro, respectively, engine builders quickly learned the benefits of retarding the cam at high rpm in naturally aspirated applications. Instead of power output falling off a cliff, retarding the intake valve closing point in these motors allowed stabilizing the shape of the power curve after peak torque.
That was just the beginning.
Once Ford introduced variable independent cam timing on the DOHC Coyote small-block, thus enabling independent intake and exhaust cam phasing, it opened up a new frontier into the performance potential of variable valve timing. Taking advantage of this, however, requires a fundamental understanding of how valve events impact horsepower, torque and drivability.
“The computer controls the engine, but as far as performance goes, the camshaft is the brain of the engine. Understanding valve events is paramount, especially in engines like the Coyote that have independent intake and exhaust cam control,” Haynes said. “The tables in the calibration files control the intake and exhaust valve opening and closing events, but you have to know which direction to go in and exactly how far to go when making changes. If you don’t understand valve events, then you can’t properly calibrate any new motor with variable valve timing.”
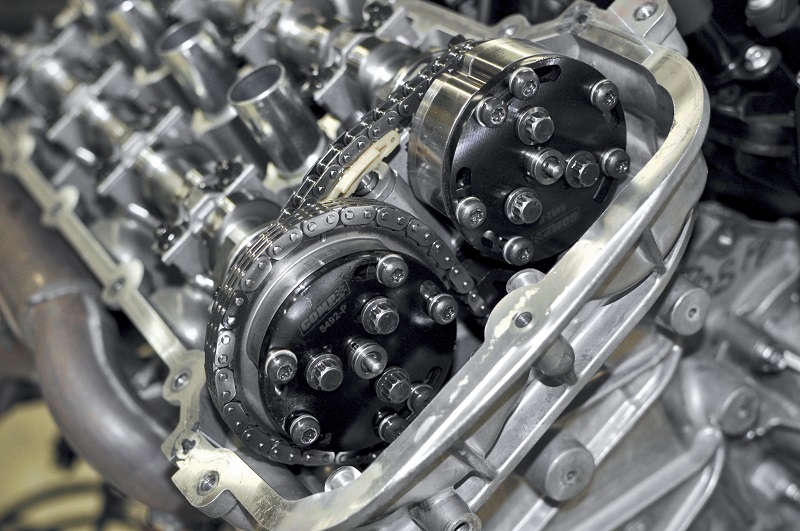
According to Comp Cams, although variable valve timing systems in OHV motors work extremely well, a DOHC motor offers hp and torque gains that are 25-50 percent greater than in a pushrod motor. The ability to phase the intake and exhaust lobes independently is a great calibration tool that’s only limited by a calibrator’s knowledge of how valve events impact airflow dynamics. (Image/Stephen Kim)
When the 5.2L Voodoo engine powering the Mustang GT350 first hit the scene, Haynes was the first to figure out how to alter the calibration strategy to play nice with forced induction.
“Everyone was scared to put a supercharger on these motors because they have 12.0:1 compression, but just because you have 12.0:1 static compression doesn’t mean you have 12.0:1 dynamic compression,” Haynes said. “If you know how to utilize the dynamic compression by changing the valve events, then you can safely apply boost on top of 12.0:1 static compression even on pump gas, up to a certain point.
“With the GT350, we swung the cam around to induce overlap to bleed off two psi around peak torque. At high rpm, we swung the cam back around to maintain boost pressure. If someone saw how flat the boost curve was they wouldn’t believe what they were seeing,” he said. “It’s all about figuring out where you want to build cylinder pressure, and where you want to alleviate some of that pressure. Lots of people struggle with that concept simply because they don’t understand engine dynamics and valve events, and how you can control and harness its potential.”
Harnessing the potential of valve events isn’t just limited to forced induction applications.
“A typical Gen V Dodge Viper will make 600 rear-wheel hp with a set of headers, a cold-air intake, a pulley and a tune. These are naturally aspirated pushrod motors, but they have a cam-in-cam design that lets you alter the lobe-separation angle,” he said. “By simply changing the valve events, these motors will pick up an extra 30 hp. We have seen 630-640 rear-wheel hp with stock heads and a stock cam.”
Direct-Injection
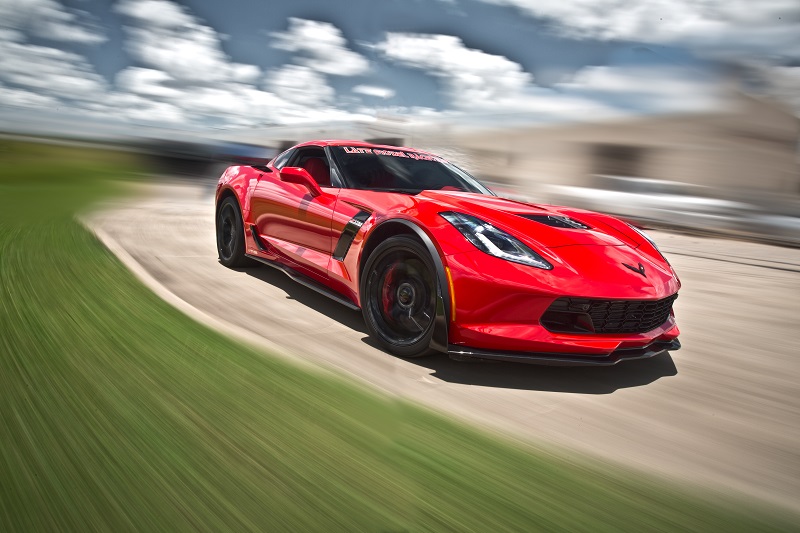
Just how far has the aftermarket’s mastery of EFI come in the last two decades? In the ‘90s, burning a new EPROM chip was considered high-tech. Today, performance shops are installing aftermarket multi-port EFI systems on top of factory direct-injection systems to meet the fueling demands of C7 Corvettes pushing well over 1,200 rear-wheel horsepower. That’s two separate computers and EFI systems working in harmony together. (Image/Chevrolet)
Just like the history of carburetors is filled with Holley 4150s, Carters, and Quadra-Jets, the method through which EFI systems deliver fuel is evolving at an alarming rate.
Simple throttle-body injections systems became multi-port systems before direct-injection rendered all of them obsolete. Or did it?
The OEs and aftermarket are now building motors that utilize both direct-injection and multi-port EFI. So how on earth do you tune it all?
For starters, tuning a direct-injection motor like a port-injected motor is a recipe for disaster.
“When the new GM Gen V LT1 first came out, people tuned them just like they’d tune an LS motor. Those calibration strategies didn’t work because the fueling strategy and torque modulation were drastically different. You’d end up with an air/fuel ratio that’s too rich and a wavy dyno sheet,” Haynes said. “Direct-injected motors don’t like the same air/fuel ratio as port-injected motors, and they can also skew wideband O2 sensor readings with varying fuel temperature and combustion chemistry. People can end up chasing their tails with direct-injection because it requires a different understanding and strategy behind delivering fuel to the cylinder.”
With direct-injection, merely managing the volume of fuel entering the combustion chamber isn’t enough. To direct fuel to just the right spot within the chamber depending on engine load, the ECM controls injection timing, in relation to the location of the piston within the bore, as well as fuel pressure. This means that a calibrator must have a handle on all these variables to properly fuel a direct-injected motor.
“The fuel systems in these motors have a low-pressure pump in the tank, and a high-pressure pump driven off a cam lobe. You have to understand the dynamics of the entire fuel and injection system to develop a calibration strategy for direct-injection,” Haynes said. “You have to study the injector spray pattern to make sure that you don’t end up with lean pockets and to ensure that the fuel properly mixes and atomizes. Adding boost disrupts that spray pattern, so you have to adjust the calibration to compensate.”
Direct + Port Injection
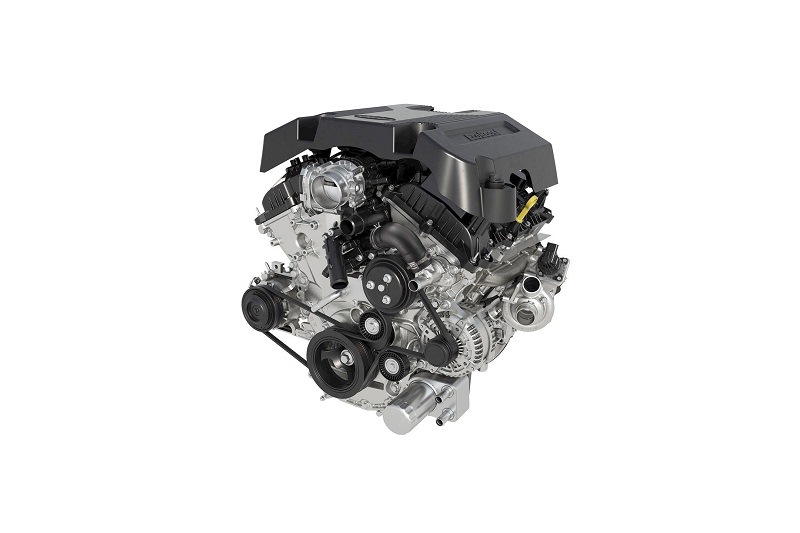
As engines become more sophisticated from the factory, having solid fundamental knowledge of how to tune direct-injection, variable valve timing, and electronically controlled wastegates is becoming even more important. In addition to all of the aforementioned features, the Ford Raptor’s 3.5L EcoBoost V-6 is also equipped with both direct-injection and multi-port injection. (Image/Ford Media)
In recent years, both OE manufacturers and the aftermarket have introduced fuel delivery systems that utilize direct-injection and port-injection, but for very different reasons.
“One of the downsides of direct-injection is that placing the injector in the combustion chamber means that you can no longer rely on fuel to clean the back of the intake valves. The early adopters of direct-injection had a lot of warranty claims from valves dropping, or oil and carbon build up on the valves,” Haynes said. “To address this, Japanese manufacturers came up with motors that use both direct-injection and port-injection. Ford followed suit with the twin-turbo V-6 in the Raptor, and the Gen III Coyote in the 2018 Mustang. GM is doing so as well.”
While the aftermarket has also embraced this dual fuel-delivery approach, it’s for vastly different reasons.
“Cars equipped with direct-injection and port-injection from the factory primarily rely on the direct-injection system at wide-open throttle. You can control the blend of the fuel delivered through the port- and direct-injection systems through the ECM,” Haynes said. “As you increase the boost in cars like the Raptor, you can increase fuel flow through the port injection system. On direct-injected motors like the LT1, you have a very short window of time for the injectors to spray fuel into the chambers at high rpm. To meet the fuel demands to support 1,400 rear-wheel hp, many tuners turned to a secondary methanol injection system.”
Nevertheless, this type of arrangement is far from ideal.
“Methanol injection is somewhat of a bandaid fix. It’s not very practical to rely on a different type of fuel and twin methanol nozzles for fuel delivery,” Haynes said. “A much better solution is leaving the factory direct-injection system in place, then installing an aftermarket port EFI system to assist with fueling at WOT. This gives you the best of both worlds. With this type of setup, a C7 Corvette can make 1,200-plus rear-wheel hp on race gas or E85 without any methanol injection. In addition to providing extra fuel at WOT, the port injection system cleans the valves, more evenly distributes fuel, and can even reduce emissions in some cases.”
Factory Turbos
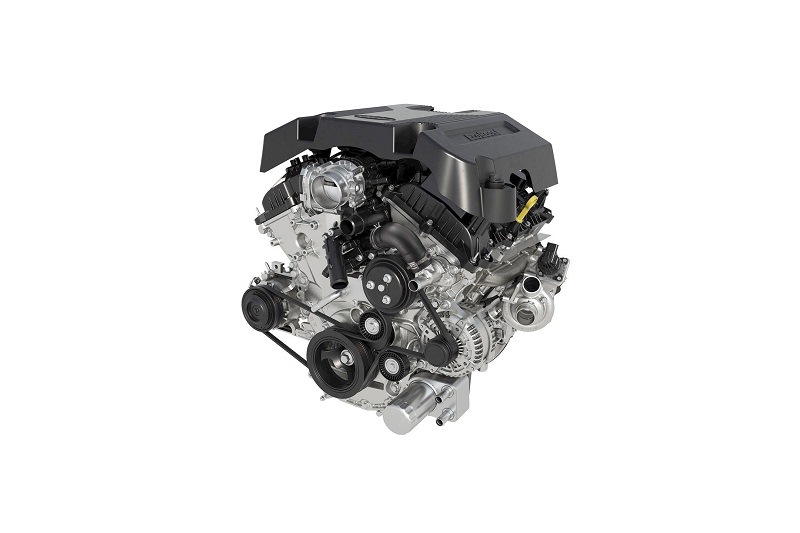
As engines become more sophisticated from the factory, having solid fundamental knowledge of how to tune direct-injection, variable valve timing, and electronically controlled wastegates is becoming even more important. In addition to all of the aforementioned features, the Ford Raptor’s 3.5L EcoBoost V-6 is also equipped with both direct-injection and multi-port injection. (Image/GM Media)
Factory forced induction is a beautiful thing, especially when you can crank up the boost through electronically controlled wastegates. The twin-turbo V-6s powering the Ford Raptor and Cadillac ATS-V are prime candidates for extra boost, but as with variable valve timing, there are several pitfalls to avoid in order to maximize power output.
“With these cars, you can control the frequency going to the wastegates. This increases boost, but you have to understand the airflow limits and modeling of the motor, and the torque calculations associated with them,” Haynes said. “If you command too much boost, the computer will try to control the torque output by limiting airflow. Some systems will close the throttle blades, and others will start dumping airflow out of the wastegates. Learning how to control all these variables allows a calibrator to maximize power, drivability and reliability.”
As always, the million-dollar question is, how much power is all of the effort worth?
“A stock Raptor motor will put down 360 rear-wheel horsepower. Most tuners will adjust the air/fuel ratio and timing, and maybe stumble around making more boost, but if the throttle blade shuts on you, the motor will be stuck at around 390 hp,” Haynes said. “These days, we now have the knowledge and software capability to turn up the boost and keep the throttle blades open, which will take a Raptor up to a consistent 430-440 rear-wheel hp.”
All of the Above
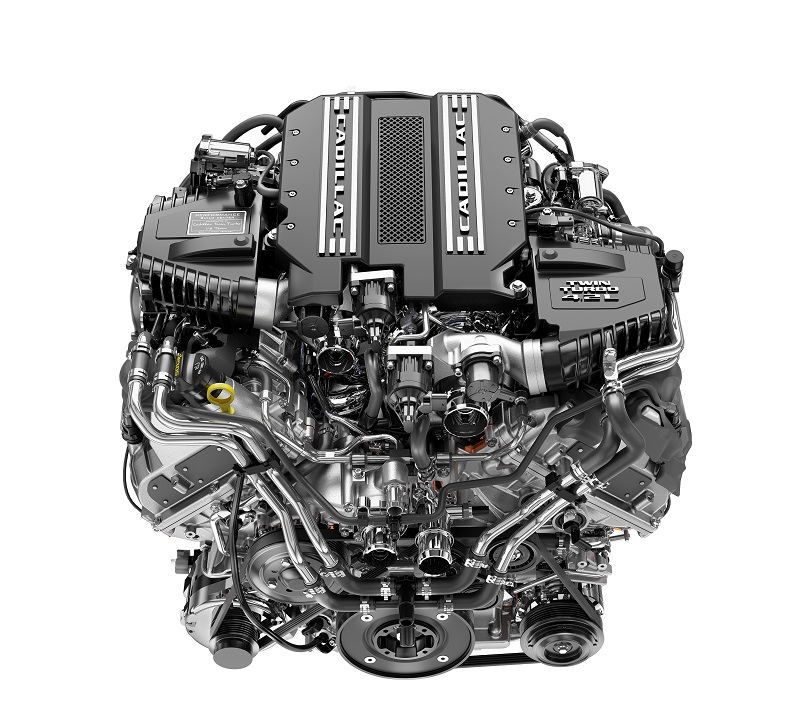
Cadillac’s transition from corporate GM engines to its own unique powertrain development program has created some very exciting engine combinations. The latest is the CT6 V-Sport’s all-new 4.2L twin-turbo V-8 that kicks out 550 hp and 627 lb-ft of torque. Unlocking its tremendous performance potential requires an intimate understanding of direct-injection, variable valve timing, and electronically controlled turbos. (Image/GM Media)
Just like the first TBI systems seem laughably archaic by today’s standards, it’s even more laughable to think how terrified hot rodders were of relatively simple technology they weren’t familiar with. The variable valve timing, direct-injection, torque modulation and electronically controlled turbos in new OE platforms may seem equally terrifying, but like it or not, it is the way of the future. Those who refuse to embrace it will get left behind.
Fortunately, there are substantial power gains to be had by learning how it all works.
“When you look at the technology in the Raptor and ATS-V, a lot of OE engine development is moving in that direction, so understanding how these variables work and how to control them are paramount to maximizing performance, drivability and reliability. You can pick up over 100 rear-wheel horsepower on an ATS-V just by calibrating the factory electronics,” Haynes said.
Even in large displacement applications, as more technology is incorporated into these motors, the need for calibrators will continue to grow.
“The new C8 Corvette will most likely have a four valve per cylinder twin-turbo engine with independent variable valve timing. The typical GM tuner will be lost when it comes out,” he said. “Horsepower knowledge is no longer confined to the basics of engine building and yesterday’s tuning practices. Having a solid foundational knowledge of engine and airflow dynamics, understanding the math and physics that govern those dynamics, and knowing the equations and control modulations of the ECM are essential tools that will allow a calibrator to apply these concepts to any engine and software platform.”
…

(Image/Stephen Kim)
The Wizard Behind the Curtain
Quite possibly the best tuner you’ve never heard of, Jason Haynes’ passion for teaching stems directly from learning about the needs of the industry firsthand while working as a performance calibration engineer for countless high-profile shops and clients. Early in his career, Haynes operated his own performance shop before performing R&D work and authoring technical tuning guides for The Tuning School in Odessa, FL. His reputation as an in-demand calibrator led him to Hennessey Performance Engineering, where his efforts helped catapult the company’s Venom GT supercar to a top speed of 265 mph, besting the Bugatti Veyron by over 11 mph.
Applying the same knowledge that he teaches his students every day, Haynes was instrumental in calibrating one of the first modified Dodge Hellcats, helping HPE revive its Dodge program. He also helped Forza Tuning become the first shop to break 1,000 rear-wheel horsepower in a Dodge Hellcat. A testament to the universal applications of ECM calibration, Haynes has even worked on the highest hp Polaris Turbo S.
In 2017, he jumped at the opportunity to bring his many years of expertise as a performance calibration engineer to SAM Tech. Haynes and the entire team at SAM Tech have big aspirations for the school’s EFI Calibration program: “There’s no set standard in our industry for performance calibrations like an ASE certification, and there’s no four-year degree you can get for performance calibration engineering. We want to set that standard at SAM Tech.”
I admire the curriculum developed by SAM Tech. If I were students, I would immediately turn to https://www.aresearchguide.com/edubirdie-review.html because the level of complexity is quite large. Although, on the other hand, not a single edubirdie review will save if students lose their desire to learn, or rather, make efforts to gain knowledge. So I wish you all good luck!
Great!
http://infomarket.md/ro/infomarket/NewFlatfyro_a_lansat_un_catalog_de_imobiliare_noi_Aici_vei_gsi_toate_Ansamblurile_Rezideniale_din_Romnia
2018 FORD GEN 3 5L high pressure injector crossover between heads.
Could that pipe be too small causing that Bank 2 to run a bit Lean and shifting the Long Term Table Rich about 5% just for that bank?
I see the Pressure sensor is located on the Bank 2 side of the line.
Engine is total stock in the F 150.
Thanks.