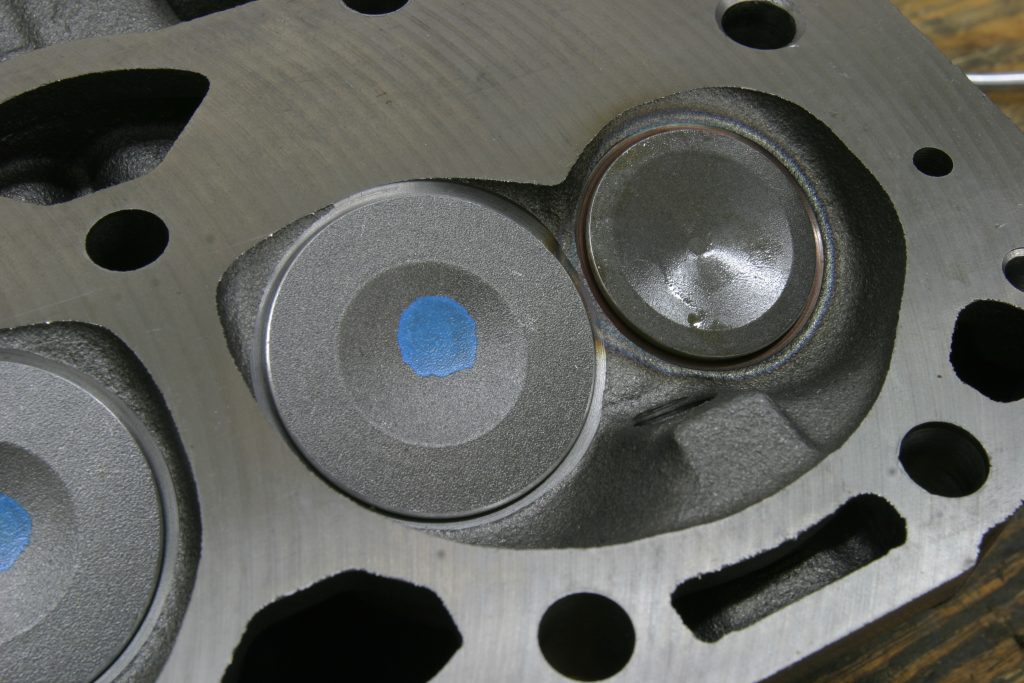
I’ve seen a couple of posts where the discussion is about how much compression to run and still use a supercharger. There were lots of ideas kicked around but it seemed to me that the easiest solution was not mentioned. Is there some reason why if you want to reduce compression on an engine that you can’t just use a thicker head gasket? It seems to me to be the simplest and easiest answer. For example, on a small-block Chevy if you are running a 0.030-inch thick head gasket, why couldn’t you run a gasket measuring 0.053-inch? I’ve seen MLS gaskets that are as thick as 0.061-inch! — J.R.
…
Jeff Smith: The simple answer to your question is — yes you can. But it comes at a cost that has nothing to do with the price of the gaskets. We need to back up a bit to explain this so it will make sense.
All wedge-style combustion chambers (which can be loosely defined as anything that’s not a hemispherical chamber) rely on something called quench to improve combustion efficiency. Quench is basically a flat portion of the combustion chamber and is basically an extension of the head’s deck surface.
This flat portion is usually (but not always) matched in position by an equally flat portion of the piston surface. In the case of a pure flat top piston, it is the entire top surface of the piston.
When the piston reaches top dead center (TDC) or its maximum travel point in the cylinder, these two flat portions come very close together. When this occurs, the air and fuel mixture captured between these two flat surfaces is very quickly squeezed, exiting into the chamber and creating a hurricane of motion in the chamber.
This motion turns out to be extremely important to help homogenize the air and fuel in the chamber. This motion drastically improves combustion efficiency and improves how quickly the combustion process occurs.
This process is not an explosion as you may think. Instead, this combustion event has been likened to a prairie fire burning across the top of the piston — albeit at a highly accelerated rate. Combustion analysis has shown that the more homogenous the mixture, the faster it burns — which can and does improve power. With more efficiency, the engine also requires less ignition timing which is also beneficial.
By now you’re probably wondering what the head gasket has to do with all of this. Our more engine-astute readers have probably already figured this out. The distance between the piston and the cylinder head quench area is directly affected by head gasket thickness. But first we need to address piston-to-head clearance.
Smart engine builders pay close attention to the piston-to-head clearance even when building a low-compression engine. This is because the closer the quench area of the piston is to the head, the more mixture motion is created in the chamber. However, there’s a limit to how close you can put the piston to the head.
Generally, clearances of 0.038- to 0.040-inch are considered tight. Some engine builders move this even closer, but they must take into consideration how much piston rock occurs across TDC. Most production engines are far looser than this so this is an area where improvements can be made.
So if we have a piston that is even with the deck surface, the only clearance is created by the head gasket. So with a small-block Chevy with zero piston deck height, we’ll need a 0.039-inch thick head gasket to establish a proper piston-to-head clearance.
In the instance of a supercharger where you would want to lower the compression ratio, just adding a thicker gasket will accomplish the goal of reducing the static compression ratio. But this will add piston-to-head clearance and reduce the effectiveness of the quench area.
Increasing the piston-to-head clearance can contribute to creating an engine that is more detonation sensitive. Ironically, closing the quench area
— making the piston-to-head clearance tighter increases the static compression ratio but often contributes to reducing an engine’s detonation tendencies.
So the result of all this is an engine with poor quench at 9.5:1 compression might be more prone to detonation than the same engine with a tighter piston-to-head clearance and a static compression ratio of 10.0:1. We’ve seen this happen several times.
Newer-generation engines with more efficient (and generally smaller) combustion chambers are less sensitive to detonation than engines with older, poorly constructed chambers. This is why LS engines at 10.5:1 compression require less timing and are therefore less sensitive to detonation than an early ‘60s iron head small-block Chevy with 9.75:1 that will rattle on the same octane fuel.
To answer your question as to why some LS engine head gaskets are much thicker, it’s very common to find that an LS engine will use an MLS head gasket that is 0.053-inch thick but the piston generally protrudes above the deck surface by as much as 0.005- to 0.008-inch or more. This reduces the overall piston-to-head clearance to something closer to around 0.045-inch, which is a common clearance for a production engine.
Let’s turn this around and use an older production small-block Chevy with a piston that is 0.023-inch below the deck surface. A composite gasket of 0.039-inch would produce a piston-to-head of 0.062-inch which is really terrible. Conversely, Fel-Pro makes a rubber coated steel shim head gasket that is only 0.015-inch thick (PN 1094). Adding 0.023 + 0.015 = 0.038-inch. This is tight but if the engine is not going to be revved much beyond 6,000 rpm, this would likely work really well depending upon where the static compression ratio would fall.
As an example of how all this affects compression ratio, a 350 small-block with flat-top, four-eyebrow pistons that are an average of 0.023-inch below the deck equipped with a 0.039-inch thick head gasket and a 76cc chamber would have 8.68:1 compression ratio which is weak for a normally aspirated engine. But substitute just the Fel-Pro shim head gasket with no other changes and the compression jumps to 9.09:1. This is still not a great ratio for performance, but much better than 8.7:1.
So then, what is the best way to lower compression for a turbocharged engine ? And keep the efficiency needed.
I’d recommend opening up the combustion chamber by further unshrouding the valves. This may also help the head’s air flow. You can use the head gasket to draw a circle on the cylinder head to give you a target. Keep in mind not to go bigger than the cylinder bore, because this will create a lip that the air will have to flow around once the engine is assembled.
I made a career out of engines, dynamometers, and experimental cars and I wish I had a couple of those Iowa farmers with journalism degrees to work with. Mr. Smith is a definite asset to the organization and contributes immensely to the technical department. Makes me wonder what he would have been like with a real degree in Engineering.
Thanks Sam for the kind words. I actually aspired be an engineer but the math was a little too steep a learning curve for me!
So the way I see it is that when the manufacturers Started putting dishtop pistons in their engines to lower the compression rather than making the combustion chambers larger it really put the hurt on engine performance!
Also they didn’t seem to understand what cam profiles would make low compression engine perform better!
A half-dish piston with a flat quench area that is kept tight to around 0.035-0.040-inch piston-to-head is actually very good. Chamber shape is very important. You cannot replace compression as a way to improve performance – even fuel mileage is better with more compression – within the octane limits of the fuel you are using.
The ’59 Dodge six ran 8 to 1.
The Hudson Hornet 7.5 to 1.
With hardened seats, and stainless valves, is no lead 87 okay ?
So, let me see if I can extrapolate a few things then. I’m assuming that you’re talking about the classic OHV style engine, because with the quad-valve DI turbo engines (plus spark plug) you almost have no extra deck as most of the head space is taken up by the valves/plugs/injector.
How would you go about putting in a quench design? I’m not really sure you could in this instance. This is also probably why the large V8’s (Hemi’s, Chevy LS, and now Ford’s Godzilla) are sticking with the ‘antiquated’ 2V cam in block design.
That being said, does that mean that the 4v engines are less ‘quenchy’ or do they just have a more advanced/complicated piston design to accomplish the same task? Or perhaps the pressure induced by the turbo helps the swirl/turbulence that used to be accomplished by the extended deck in the head?
There’s a whole bunch of science there that I must admit I’m not completely up on.
I try to work with the few tools and materials I have. Had a 350 sbc from a 69 Corvette. It was the 300hp version, slightly dished pistons. Used some true flat tops from a 350 Impala, installed, and even with flat tops, measure low compression when using the .031 gasket thickness, plus being .015 below the deck at top dead center. However, using the .015 steel shim head gasket, achieved a total quench @ .030. After running for a while, I did notice a few spot where the pistons left witness marks on the bottom of the head. However, it probably needed an overbore, at least .010. so, .030 will work if on a freshly machined, or with tighter piston to wall clearances.
On my 05 LQ4, 6 liter, the Pistons protrude out of the block. I plan to use some 706/862 heads, mill them @ .020″, to achieve close to a 58cc chamber. Will have to break out the calculator and ensure I get the proper gasket to achieve the proper quench.
Good info! I might have missed it, but readers need to remember also not to just add up the numbers of the gasket thickness, one has to consider how much the gasket will be compressed once the head is torqued down, it will be about 4 or 5 thou thinner than advertised (for example, an .039 gasket once tightened down will be around .035).
I have a question: How does a tighter quench area reduce the possibility of detonation? That sounds counter-intuitive to me–tighter quench means more turbulence, which would accelerate combustion. I thought the whole idea behind high octane fuel was to slow down combustion so as to (a) prevent the unignited zone outside the flame propagation bubble from “dieseling” before the flame front reached it, and (b) allow the piston to “get over the hump”, IOW past TDC and headed down the cylinder where it can impart BMEP to the crankshaft.
why would you put low compression heads on a C-15 cat?