At first glance, it doesn’t seem like there are a lot of fasteners in an engine. But think again! Looking at it from the carb studs down to the oil pan and from the water pump to the crank flange, there are more nuts and bolts than you might have guessed.
For example, in our sample big block Chevy, we counted well over 160 individual bolts, studs and nuts (plus a whole bunch of washers we didn’t count). That’s a lot. Certainly, many enthusiasts pay attention to the “important” ones like rod bolts, but for the rest, plenty of folks use what they have on hand from previous builds or what they removed from an engine core. No big deal.
Or is it?
Should You Re-Use Engine Hardware?
In many cases, it’s entirely possible to re-use engine hardware. But there are limits to everything. It all depends upon the condition of the fastener. Sure, it’s easy enough to detect a bolt with physical damage (for example, corrosion or if the threads are galled or if there is wrench damage to the head), but the reality is, you can’t see inside the fastener.
Some (and that’s the operative word here) Torque-to-Yield fasteners found on later model engines are limited in the number of times they can be used. What this means is the previously used bolt has already been “plastically deformed.” If you use it again, you might not be able to establish a reliable clamping force. Eventually this can lead to fastener or component failure. For a closer look, check out this article on Torque-to-Yield fasteners by fellow OnAllCylinders contributor, Jeff Smith.
Understanding Common Engine Fastener Materials
If you’re building an engine from scratch, of if you prefer to use all new hardware, what are the options? The fastener folks from ARP offer the following tech on more common bolt, stud and nut materials:
- 8740 CHROMOLY: Until the development of today’s modern alloys, chromoly was popularly considered a high strength material. Now viewed as only moderate strength, 8740 chromoly is seen as a good, tough steel, with adequate fatigue properties for most racing applications—but only if the threads are rolled after heat-treatment, as is the standard ARP production practice. Typically, chromoly is classified as a quench and temper steel, one that can be heat-treated to deliver tensile strengths between 180,000 and 210,000 psi.
- STAINLESS STEEL: Ideally suited for many automotive and marine applications because stainless is tolerant of heat and virtually impervious to rust and corrosion. ARP “Stainless 300” and Custom 450 materials are specially alloyed for extra durability. Both are polished using a proprietary process to produce a beautiful finish. Tensile strength is typically rated at 170,000 to 190,000 psi.
- ARP2000: ARP2000 is an alloy steel that can be safely heat treated to a higher level, producing a greater strength material than 8740. While 8740 and ARP2000 share similar characteristics, ARP2000 is capable of achieving a clamp load at 220,000 psi. ARP2000 is used widely in short track and drag racing as an upgrade from 8740 chromoly in both steel and aluminum rods. Stress corrosion and hydrogen embrittlement are typically not a problem, providing care is taken to protect the parts from moisture and the parts are kept well oiled.
- L19: This is a premium steel that is processed to deliver superior strength and fatigue properties. L19 is a very high strength material compared to 8740 and ARP2000, and is capable of delivering a clamp load at 260,000 psi. It is primarily used in short track and drag racing applications where inertia loads exceed the clamping capability of ARP2000. Like most high strength, quench and temper steels, L19 requires special care to avoid hydrogen embrittlement. This material is easily contaminated and subject to stress corrosion. It must be kept well oiled and not exposed to moisture.
- AERMET: With a typical tensile strength of 290,000 to 310,000 psi, Aermet is a new martensitic super-alloy that is stronger and less expensive than the super-alloy austenitic materials that follow. Because it is capable of achieving incredibly high clamping loads, it is ideal for short but extreme environments like top fuel, funny car, and some short track applications. Although Aermet is a maraging steel that is far superior to other high strength steels in its resistance to stress corrosion, it must be kept well oiled and away from moisture.
- INCONEL 718: A nickel based material that is in the high temperature, super-alloy class, it is found to be equally suitable in lower temperature applications. This material delivers tensile strengths in the 210,000 to 230,000 psi range and exhibits improved fatigue properties. Best of all, Inconel 718 is completely immune to hydrogen embrittlement and corrosion.
- ARP3.5 (AMS5844): While similar to Inconel 718, these super-alloys are found in many jet engine and aerospace applications where heat and stress attack the life of critical components. The high cobalt content of this alloy, while expensive, delivers a material with superior fatigue characteristics and typically tensile strength in the 260,000 to 280,000 psi range. The immunity to hydrogen embrittlement and corrosion of these materials is a significant design consideration. These materials are primarily used in connecting rods where extremely high loads, high RPM, and endurance are important factors—think Formula 1, NASCAR and IRL applications.
- CUSTOM AGE 625 PLUS: This newly formulated super-alloy demonstrates superior fatigue cycle life, tensile strength and toughness—with complete resistance to atmospheric corrosion and oxidation. ARP is the first to develop manufacturing and testing processes for fasteners with Custom Age 625+. Best of all, it is less expensive and expected to soon replace MP-35 as the material of choice in the high strength, super-alloy field. Typical tensile strength is 260,000 to 280,000 psi.
- TITANIUM: ARP now offers special-order fasteners made of an alloy (Ti6Al-4V) that is specially heat-treated (a process developed by ARP’s own Russ Sherman) and provides superior strength to other titanium alloys employed in racing and aerospace. The material has a nominal tensile strength of 180,000 psi, and is very corrosion resistant. The main advantage of titanium of course, is its weight—which is about 40% lighter than a comparable fastener made of steel. Head studs and accessory bolts are ideal applications for this lightweight material.
Fastener Material Cross-Reference Chart from ARP
ARP has a great chart that allows you to see the yield and tensile strength of various fastener materials. With it, you can see the differences in those materials and why they’re used in specific locations. Before checking out the chart, keep this in mind:
When you’re talking engine hardware, “Yield Strength” is the point where a fastener exhibits a permanent deformation (basically, where it takes a set). Once the load (in this case, that usually means torque) that created the stress on the fastener is removed, the fastener will not return to the original dimensions. ARP advises that if the yield strength of a fastener is exceeded, then the fastener is damaged and it must be replaced. That’s why we pointed out earlier that you really might be able to tell how good a used fastener is, just by looking at it.
Meanwhile, “Tensile Strength” or “Ultimate Tensile Strength” of a fastener is the maximum stress that it can support without snapping. Tensile Strength is expressed in terms of pounds per square inch. The maximum force (in pounds) that a test fastener can support is divided by the cross-sectional area (square inches) of the fastener. The result is ultimate tensile strength in pounds per square inch or PSI.
Engine Fastener Material Strength & Applications
Material | Yield Strength | Tensile Strength | Uses |
---|---|---|---|
Grade 5* | 90,000 psi | 120,000 psi | Accessory bolts & studs |
Grade 8* | 120,000 psi | 150,000 psi | Accessory bolts & studs |
Stainless 300 | 140,000 psi | 170 – 190,000 psi | Accessory bolts & studs |
Custom 450 | 150,000 psi | 170 – 190,000 psi | Accessory bolts & studs, head bolts |
8740 Chromoly | 180,000 psi | 190,000 psi | Rod bolts, head & main studs & bolts |
A286 | 170,000 psi | 200,000 psi | Head bolts, accessory bolts |
ARP2000 | 200,000 psi | 220,000 psi | Rod bolts, head & main studs |
L19 | 200 – 230,000 psi | 260,000 psi | Connecting rod bolts |
Inconel 718 | 190 – 210,000 psi | 210 – 230,000 psi | Head bolts, case studs & bolts |
Custom Age 625+ | 235 – 255,000 psi | 260 – 280,000 psi | Head studs, connecting rod bolts |
ARP 3.5 | 220 – 250,000 psi | 260 – 280,000 psi | Connecting rod bolts |
AerMet | 260,000 psi | 290 – 310,000 psi | Special applications |
Titanium | 160,000 psi | 180,000 psi | Head studs, accessory bolts |
*Shown for reference only. Grade 5 & Grade 8 fasteners not recommended for engine applications. |
Should You Use Bolts or Studs?
With the fastener material choices out of the way, you should also consider the type of fastener you wish to use along with the type of wrenching format. Most certainly, there are personal preferences involved here along with a lot of practical issues. For instance, ARP sheds some light on head studs versus head bolts:
“ARP’s factory Tech Representatives are often asked which is better, cylinder head studs or bolts. The answer, invariably, depends on the installation. On many street-driven vehicles, where master cylinders and other items protrude into the engine compartment, it’s probably necessary to use head bolts so that the cylinder heads can be removed with the engine in the car.
“For most applications, however, studs are recommended. And for good reason. Using studs will make it much easier to assemble an engine (especially a racing powerplant which must be serviced frequently and quickly!) with the cylinder head and gasket assured of proper alignment.
“Studs also provide more accurate and consistent torque loading. Here’s why. When you use bolts to secure the head, the fastener is actually being “twisted” while it’s being torqued to the proper reading. Accordingly, the bolt is reacting to two different forces simultaneously. A stud should be installed in a “relaxed” mode – never crank it in tightly using a jammed nut.
“If everything is right, the stud should be installed hand tight. Then, when applying torque to the nut, the stud will stretch only on the vertical axis. Remember, an undercut shorter stud will have a rate similar to a longer, standard shank stud. This provides a more even clamping force on the head.
“Because the head gasket may compress, check with your gasket manufacturer to see if retorquing is required.”
Aside from cylinder heads, you’ll also find studs downstairs on main caps (obviously not on the outboard side of splayed caps), oil pans, timing chain covers (or belt drives), up top on carburetors, distributor clamps and sometimes on valve covers. The reason for using studs in some of these locations can prove to be a matter of practicality. For example, a stud provides a means to hold a gasket or gaskets in place while you’re installing components.
Choosing the Right Engine Fastener Head
When it comes to fastener head styles, it’s pretty much a matter of personal choice. Often, you’ll end up with a mix of conventional hex head and 12-point fasteners.
12-point fasteners offer a little bit better wrench access, and that can come in handy in tight spots like header bolts. The downside to 12-point fasteners is you’ll likely need a set of 12-point sockets for use in some locations (where a wrench won’t work or where you need to establish proper torque).
Most ARP fasteners are designed with a reduced wrenching hex coupled with a wide flange under the hex. This provides for superior wrenching clearance in many locations. In fact, on head bolts, the smaller wrenching hex sometimes allows you to remove the head without completely disassembling the valve train.
Advice on Tightening Engine Bolts, Nuts & Studs
So what about tightening bolts? If you don’t tighten a fastener correctly, then the clamp load on whatever you’re tightening won’t be correct. Clearly, not enough torque can (and probably will) result in component failure. Too much torque (and consequently, too much fastener stretch), can also result in failure.
ARP points out there are generally three ways to determine how much tension has been applied to a fastener. These include a conventional torque wrench, a stretch gauge, and finally, a torque angle meter. We don’t have space to get into the whys, wheres, benefits, and stumbling blocks of each, but in many cases, it boils down to what equipment you have in your tool box and what you’re comfortable with.
The Importance of Lubricating Your Hardware
When dealing with fasteners, one thing you should absolutely positive about is lubrication.
True story: I bought a fancy set of big stainless steel body mount bolts for my car. The radiator support bolts came with equally fancy nyloc nuts. I was installing a new big block rad support in the car and I wanted to test fit everything. The radiator support was installed and I loosely ran the lock nuts up on those fancy stainless bolts by hand. When I tried to remove them, they didn’t budge. Because I had not used any lubricant (in this case, anti-seize), the threads galled.
To get them off (and keep in mind they were merely finger-tightened), I first tried a 1/2-inch breaker bar. Nothing. Next I fired up my big two-stage air compressor and dragged out a 1/2-inch drive impact wrench. With the compressor turned up to max and a tool with huge breakaway torque capabilities, the nut didn’t break free. In the end, I had to cut both nyloc nuts off and purchase new hardware.
The moral of the story? The appropriate lubricant for specific fasteners is critical. That’s why companies such as ARP include assembly lube with many of their fasteners.
Inspect Your Threads!
The final thing you should consider with fasteners is the condition of their threads. ARP notes:
“In addition to the lubricant used, friction is affected by the surface finish of the fastener itself and the condition of the threads. For example, black oxide behaves differently than a polished fastener so it’s important to follow the torque recommendations with each fastener kit. Then there’s the very real problem of burrs and debris in the bolt holes that can significantly affect the amount of torque required to achieve the recommended clamp load. All bolt holes should be thoroughly cleaned using thread chasers to clean the threads before installation.”
Aww Nuts? Maybe So.
As you can see, there’s a whole bunch more to the nuts and bolts inside and around the engine than you might ever considered. For a closer look at many of them, check out the pics below:
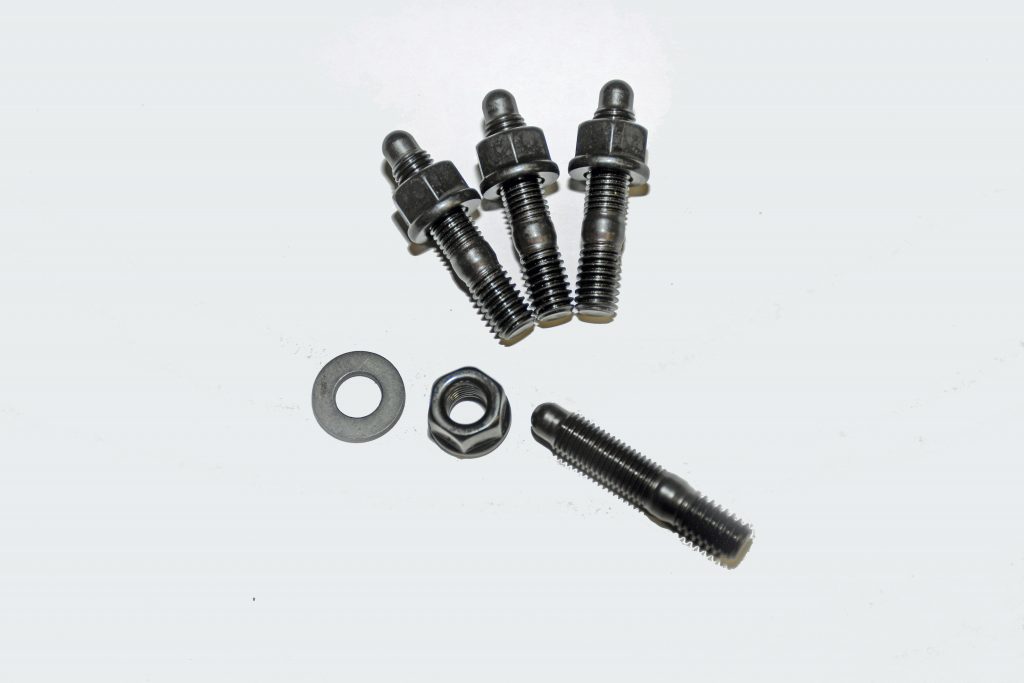
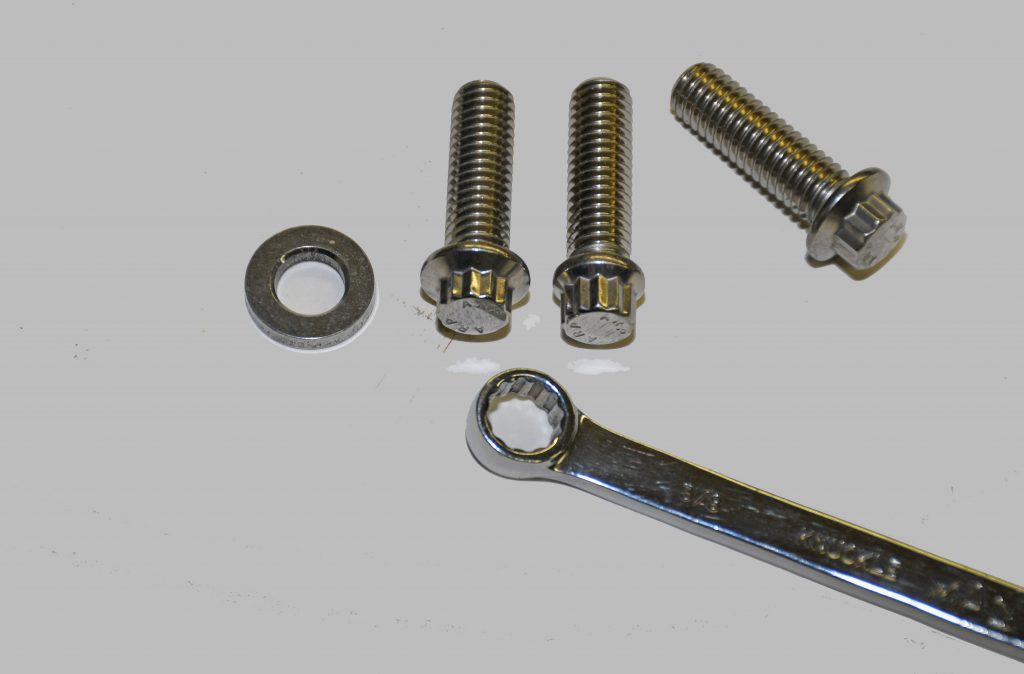
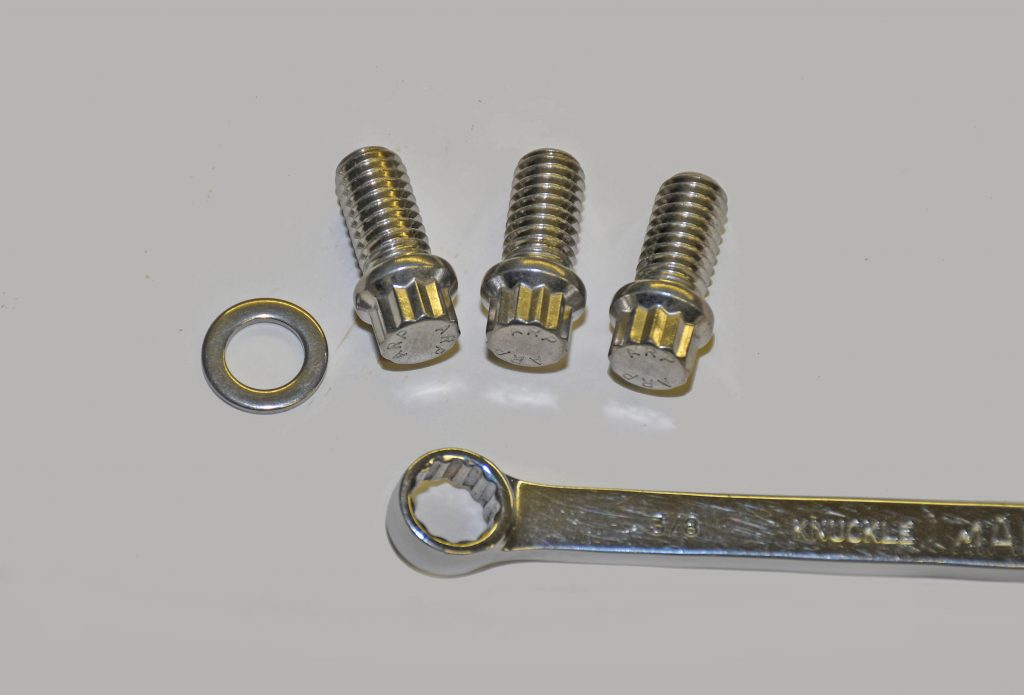
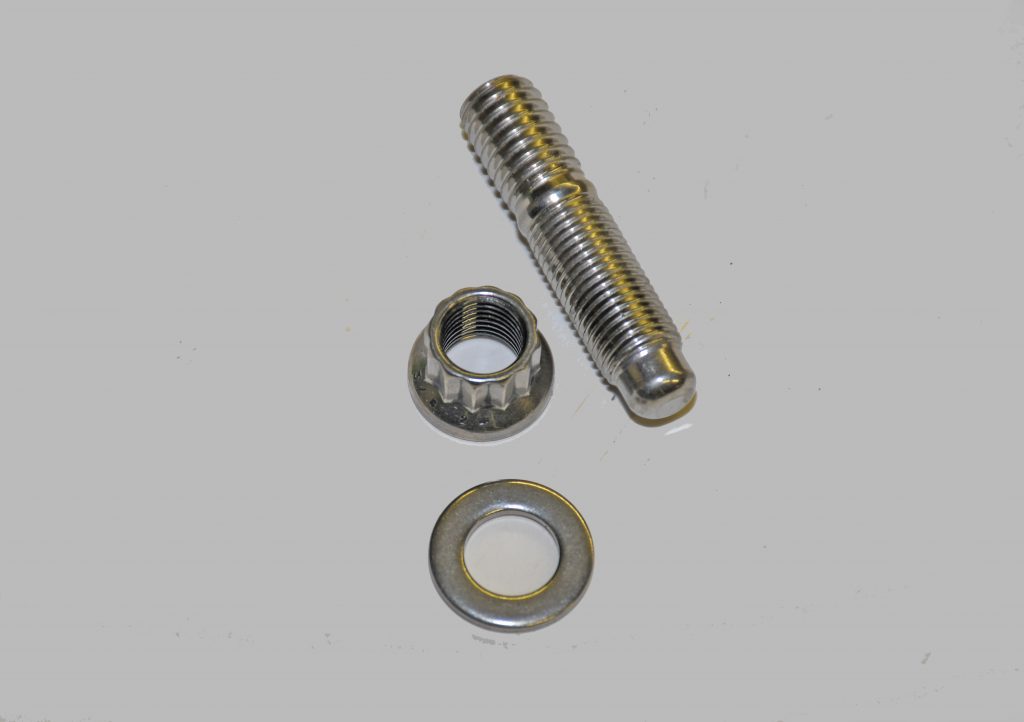
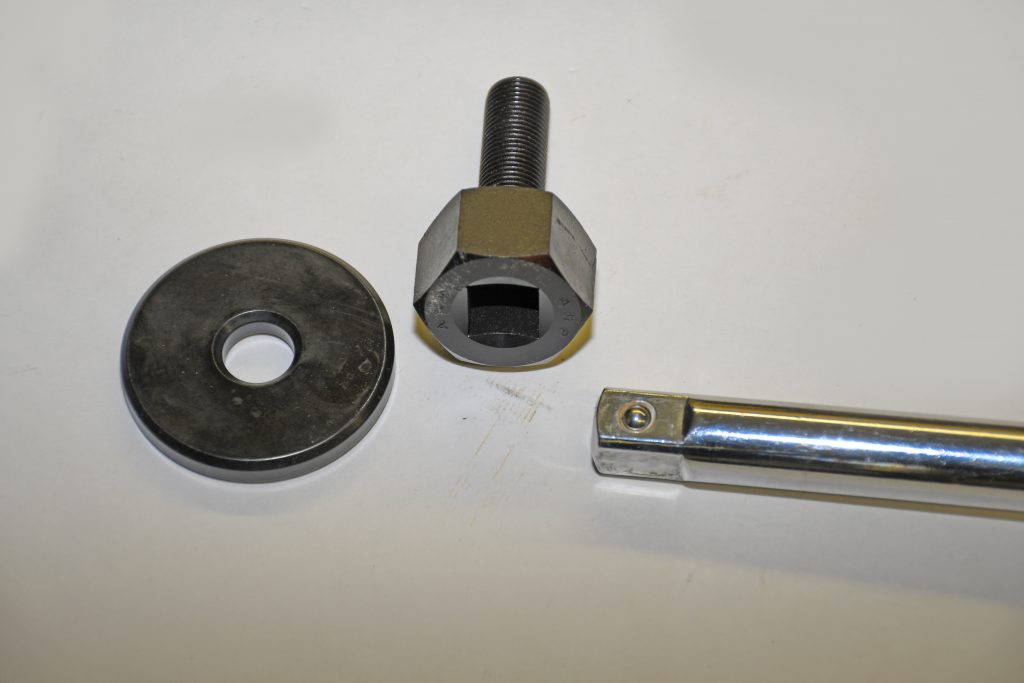
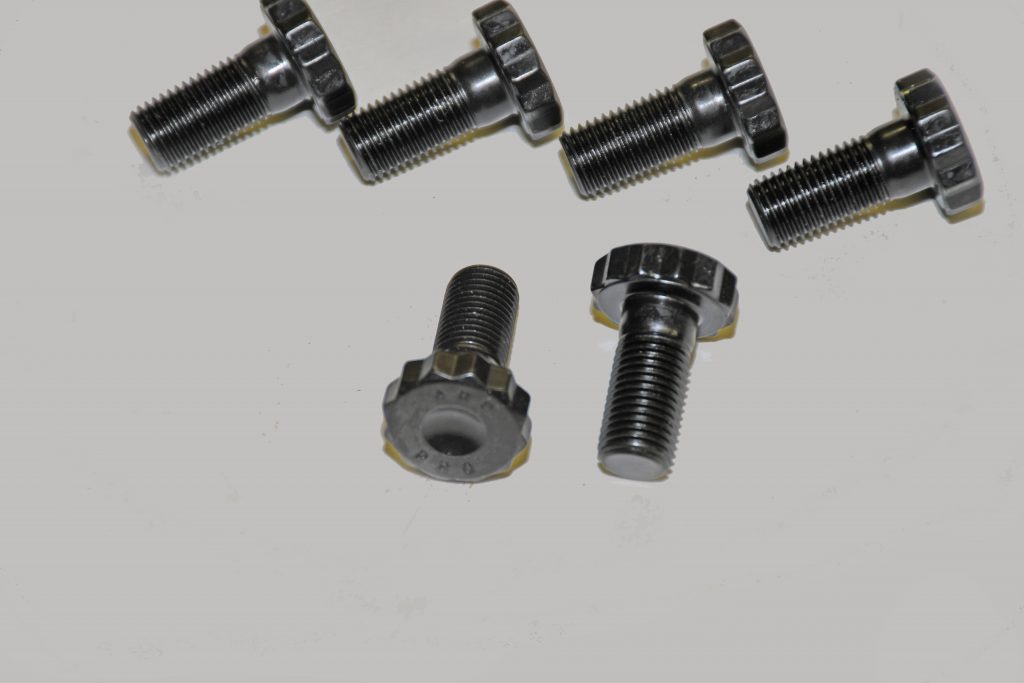
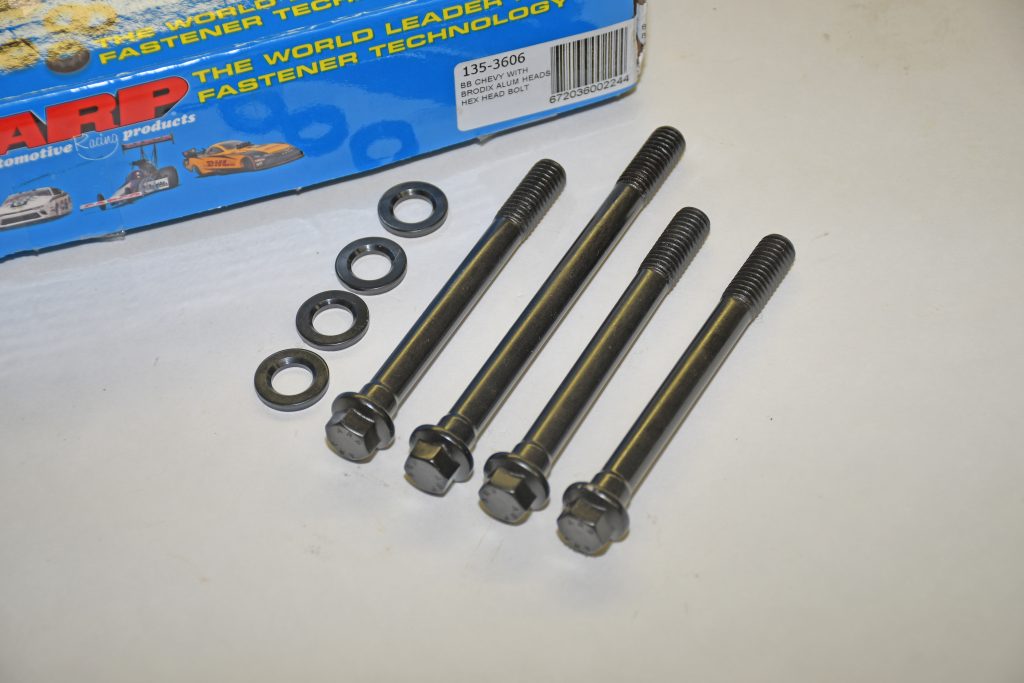
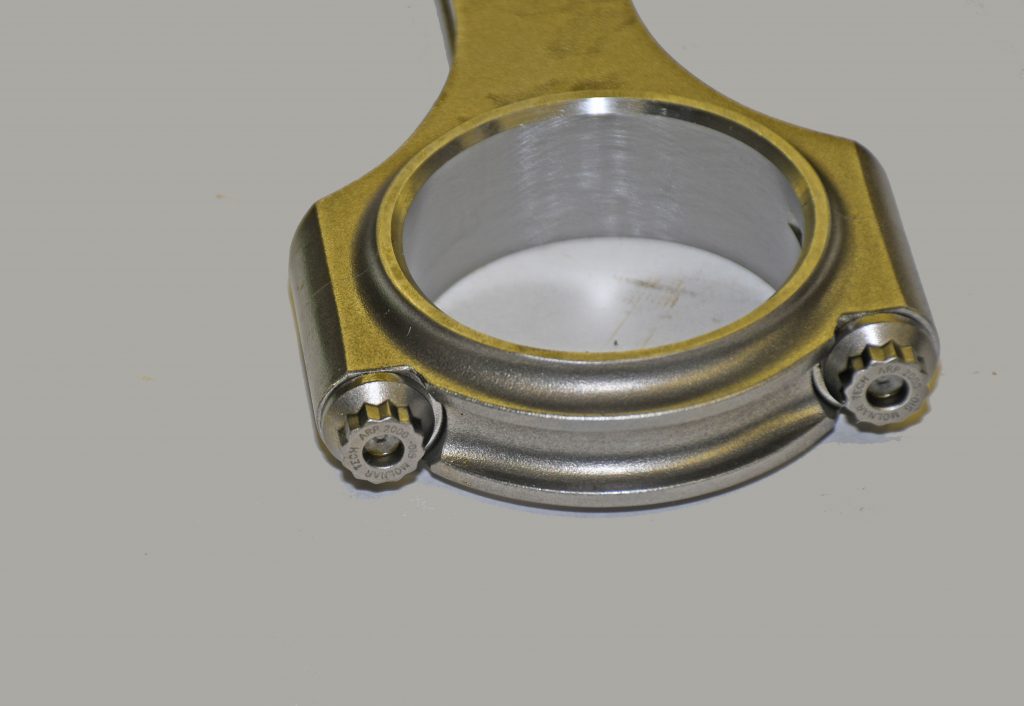
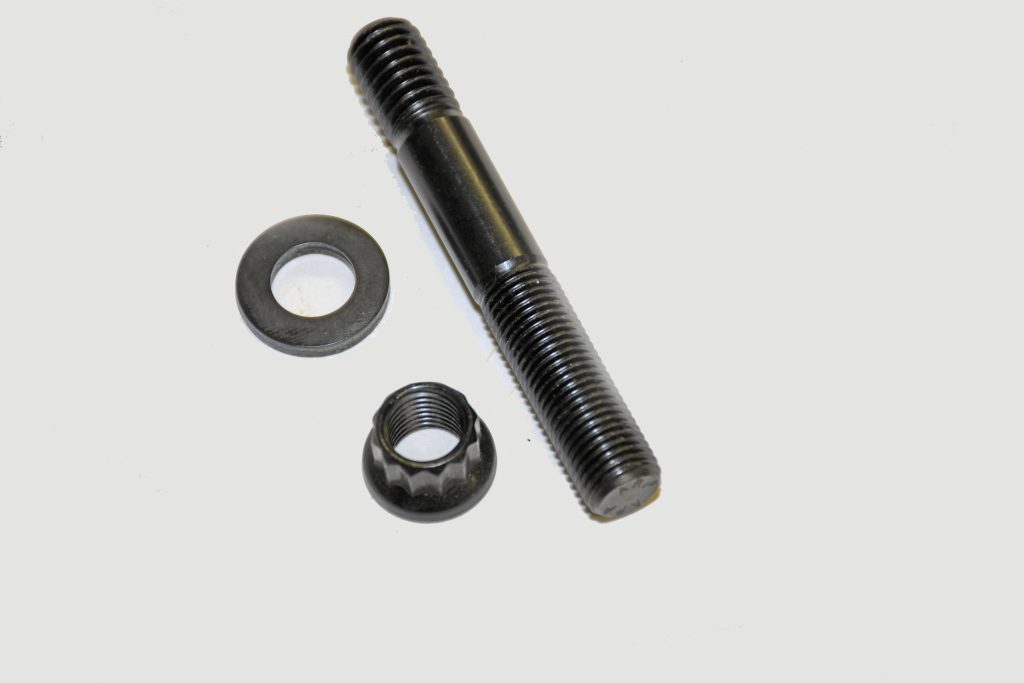
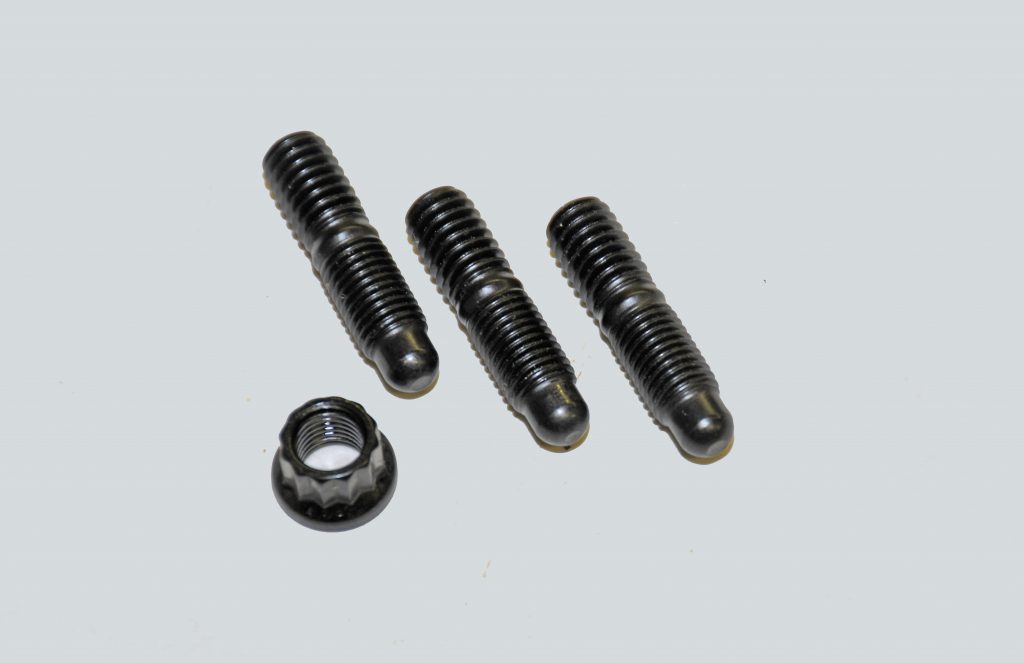
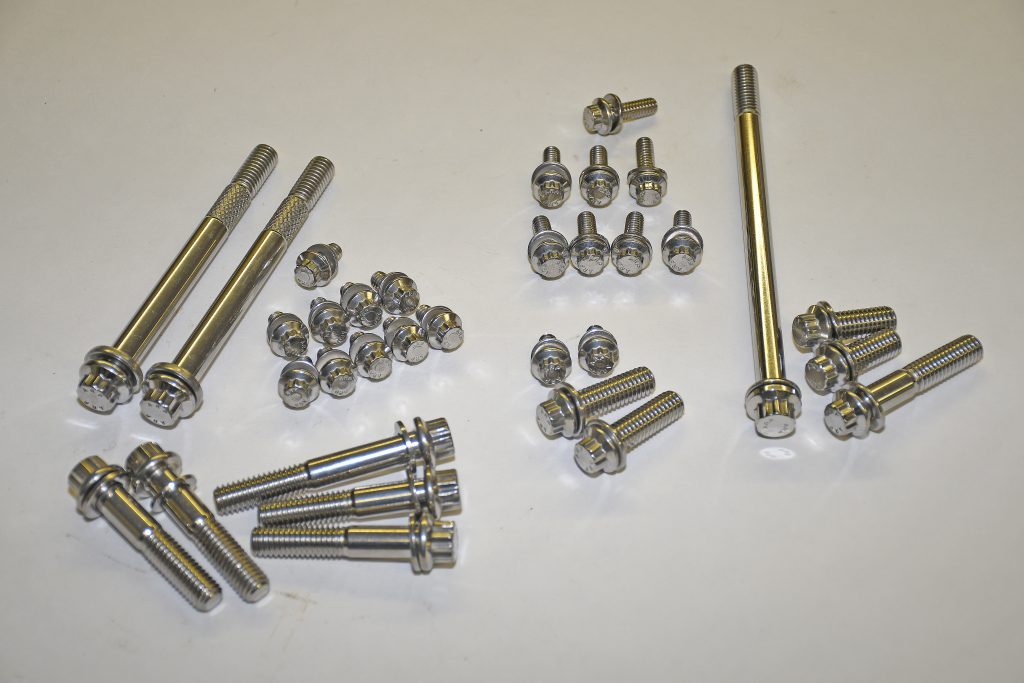
Comments