I have a small-block 350 street/strip engine that I continue to play around with. In my last session at the track, it seems like the engine doesn’t pull as hard above 5,500 rpm as I think it should. The engine is running an Isky hydraulic roller cam with 252/254 degrees of duration at 0.050 with 0.550 inch valve lift using 1.5 rockers.
I was thinking that perhaps the hydraulic roller lifters are pumping down and causing the weak top-end. I read a story in Hot Rod where the writer mentioned running solid roller lifters on a hydraulic roller cam. I’d be interested in your opinion of this idea.
J.D.
It used to be that attempting to run a mechanical roller lifter on a hydraulic roller lobe would meet with disaster. This had to do with older cams with large lash numbers. The latest generation tight lash mechanical cams can allow you to run a hydraulic roller lifter. This might work for a competition engine but I’m not convinced it’s practical to run this combination on the street.
To address your specific question, it’s possible to run a tight amount of lash of around 0.006 inch using a mechanical roller lifter on a hydraulic roller cam with the engine fully warmed up. However, you will need to check to make sure that when the engine is fully cooled down that clearances don’t tighten up to the extent that the valves are held open. If so, you will have to increase the lash to compensate.
But this effort will first require purchasing a set of mechanical roller lifters in order to test your theory that the lifters are pumping down. Before you make the investment of several hundred dollars to check your theory, we’d suggest attempting a simpler experiment.
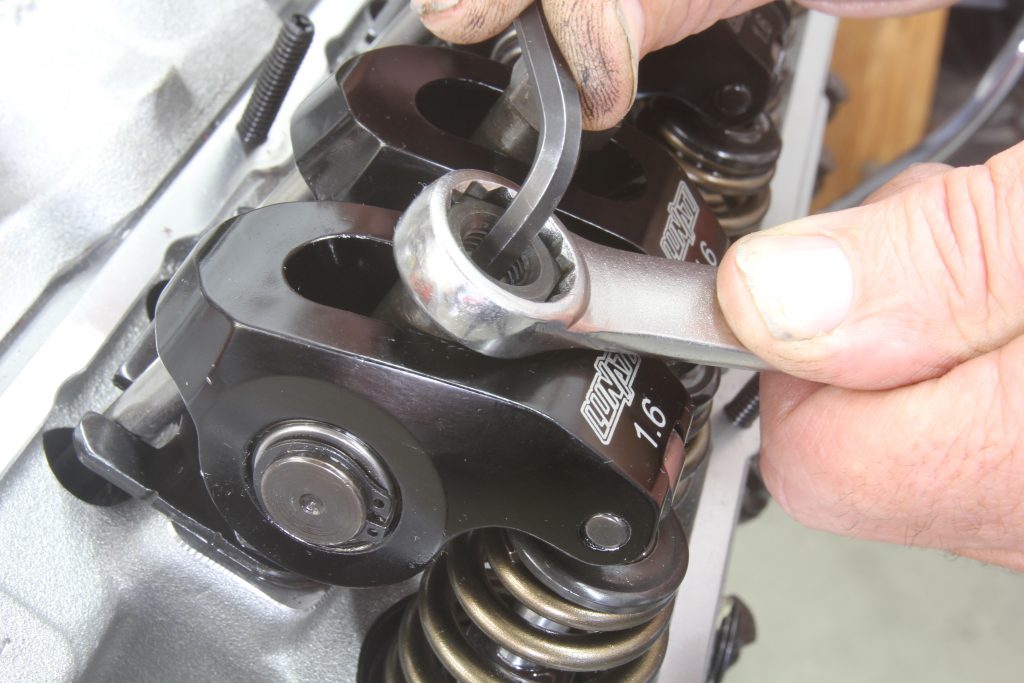
We’ll assume for the sake of this discussion that when you set the preload for the hydraulic lifters that you set them at zero preload and then an additional 1/4-turn on the adjuster. We will also assume the use of 7/16 inch rocker arm studs with a 7/16 x 20 threads per inch thread pitch. A full turn at 20 threads per inch would push the lifter piston down by 0.050 inch. This would make a 1/4-turn adjustment worth about 0.0125 inch of preload. The total travel of a typical hydraulic piston inside the lifter is between 0.100 to 0.120 inch.
This means that preloading the lifter only a 1/4-turn is only preloading the piston inside the lifter only about 20 percent of the distance. The idea behind this practice is that if the valvetrain loses control, the lifter will only “pump up” 0.0125 inch as opposed to a much greater distance. If the preload was set deeper, this would hold the valve open and not allow it to seat and power would be lost.
However, the problem with the above scenario is that this creates a greater volume of oil below the piston in the lifter. All engine oil contains captured air bubbles due to foaming. While all modern engine oils come with anti-foaming additives, these do not eliminate the air from the oil. With air in the oil, the load on this piston is more than enough to compress the air and sacrifice valve lift.
Our suggestion would be to increase the preload to the hydraulic lifters to reduce the amount of oil volume below the piston in the lifters. By reducing the volume, there will be less oil and therefore less air entrained in the oil and the hydraulic system will begin to perform more like a solid lifter. So increasing the preload to 3/4-turn may produce better performance. The beauty of this approach is that it does not cost anything except a few minutes of your time.
You may have heard about short-travel hydraulic roller lifters. These hydraulic lifters are designed with a much shorter overall travel of less than 0.100 inch. Because they use a much smaller volume below the piston, these lifters should be adjusted closer to the 1/4-turn adjustment just to keep the piston away from the floor of the lifter. This is important because otherwise the system will bind and cause damage. Short travel lifters need to somehow be identified externally on the engine to prevent an error when adjusting the preload.
Readjusting your lifters on the engine may make the engine run rough for a few minutes until the oil is pumped out of the lifters, so be aware that the engine may not be happy at first. Once it stabilizes, then you can run it through your test procedure to see if the engine pulls harder. If it does, then you might want to try slightly more preload, but keep it to around one full turn of preload.
Our friend Richard Holdener has actually performed a lifter preload test on an LS engine to evaluate any changes that might occur. He used a 383 stroker iron block LS engine with a big 232/243 degrees at 0.050 cam with Trick Flow cylinder heads and an Edelbrock single plane intake and Holley 750 Ultra HP carburetor. The engine made well over 500 horsepower in its baseline configuration.
Because the LS engine uses a net lash system, he adjusted the preload by adding pushrod length. By adding 0.050 inch of length, this preloaded the lifters this additional amount which put them probably near 0.075 inch worth of preload. This single change increased peak power by over 10 horsepower but did cost some power at the very bottom of the torque curve.
You may wonder why this loss of torque occurred at the lower engine speed. By decreasing the volume of oil below the hydraulic piston, this effectively makes the lifter act more like a solid lifter, which reduces the compliance in the lifter and essentially makes the camshaft appear to have more duration. We all know that adding duration to cam timing tends to hurt power down low while improving power at the higher engine speeds. This is exactly what happened in Holdener’s test—you can watch the video here for more details.
This is probably a far lengthier explanation that you were expecting, but it’s possible that you could get most of the benefit of mechanical lifters without the expense of purchasing them. Of course, if the experiment does not work, you’ve spent nothing and can move on to a different solution to the problem.
Adjust the lifters 1 full turn off bottom, i have isky cam in my car and i turn it 7500 rpms, my car runs 8.38 ET, at 157 mph in a 1/4, i run nothing but hyd roller cams, i designe my own cams with 4 way split. My engine is 472 cu.in. small block all aluminium.
I would like to receive newsletters and all tips and tech please
Hey Flip–click here to subscribe to the RSS feed.