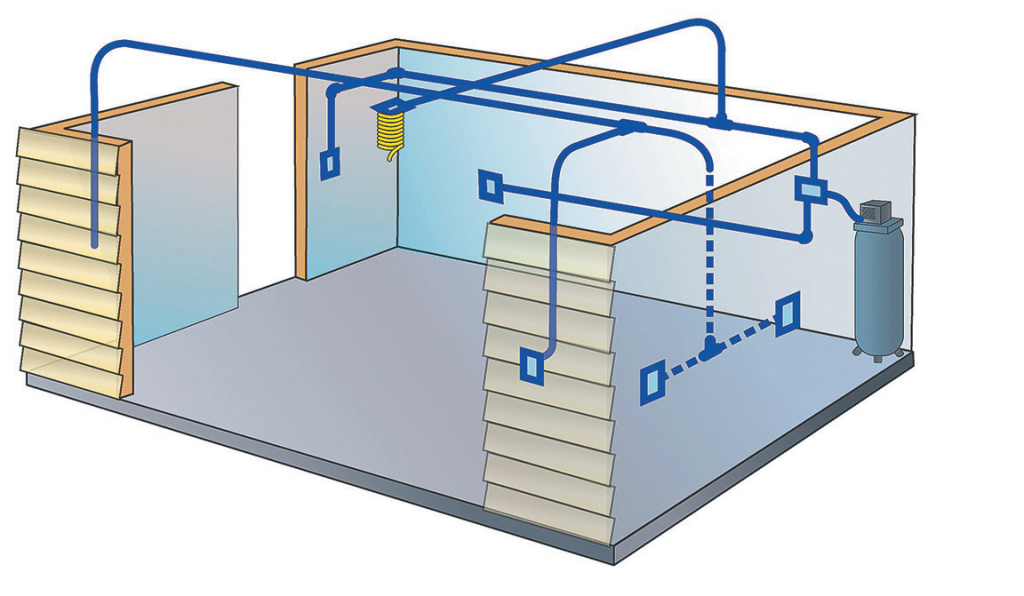
Q. I just built a 40 ft. x 60 ft. shop for automotive restoration and repair. I installed a new two-stage 5 HP air compressor that produces 19 cfm @ 100 psi. At times there could be three people working in the shop, using an assortment of air tools. How do I choose the size of my air lines?
A. Choosing the correct line diameter is based on your compressor’s cfm (cubic feet per minute) output rating, and how much flow is required to adequately supply all of the air tools simultaneously in use. Additionally, flow rates diminish as the line’s length increases; the longer the runs are, the larger diameter line you will need.
There are two ways to run air lines. Single-run systems have an individual air line from the compressor to the farthest point of use. Looped systems go all the way around the shop using a tee fitting at the compressor (or regulator/filter). This lets air travel in two directions, which balances airflow and doubles flow capacity.
Single-user shops or home garages typically will not require a looped system.
Use the charts below to determine the diameter line required for your application; round up in diameter size.
***
Air Tools Estimated Air Consumption
Tool | Air Consumption | Tool | Air Consumption |
---|---|---|---|
1/4" Die Grinder | 4 - 5 cfm | Ratchet | 4 - 5 cfm |
Drill | 4 - 5 cfm | Blow Gun | 2 - 3 cfm |
3/8" Impact Wrench | 3 - 4 cfm | Air Hammer | 4 - 5 cfm |
1/2" Impact Wrench | 4 - 5 cfm | Orbital Sander | 6 - 9 cfm |
Air Tool CFM Flow Chart
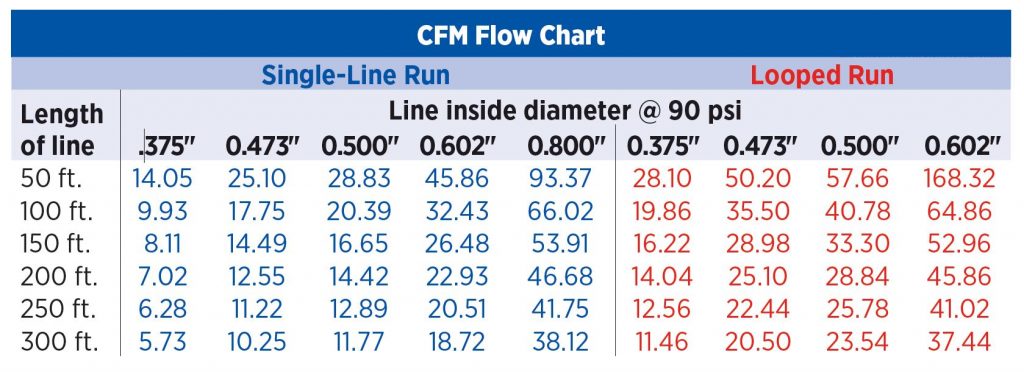
Comments