Let’s do some quick, easy math, where your basic 1 + 1 = 2.
We all know that big motors make more power than smaller motors, right? We also know that boost makes more power, too! The question on the table now is, what happens when you combine the two?
The only thing better than one or the other, is obviously both! Big or small, the power output of any internal combustion engine is determined by the amount of air (and fuel) it can process, right?
A rather simplified (air pump) equation we know, but horsepower is basically a function of the amount of air processed by the motor. The more you process (or in our case, force) through the motor, the more power you will get out of the motor. The trick to making power is getting the additional air (safely) into and out of the motor.
Given this simplistic airflow equation, one of the most popular routes to improved performance has long been supercharging. In its most basic form, supercharging involves force feeding the engine more air than it can ingest of its own accord. Like all good things, the problem with any type of forced induction is that enthusiasts tend to get greedy.
Who among us hasn’t reasoned that if a little boost is good, then more must better, right? Wrong! If you can resist the temptation, combining boost with a healthy big block can yield massive power, and, (this being the important part), do so safely and reliably.

Supercharger Basics
Before getting to the big block build, we should take a moment to better understand the basic principles of supercharging. To start, supercharging is a form of power enhancement that forces air into the cylinders. This is accomplished by installing a compressor (or more accurately an air pump-not unlike the motor itself) onto the motor and using the crankshaft to spin the compressor. The compressor is spun to provide more air than the motor could ingest of its own accord.
The only way to increase the airflow is to pressurize it, the result of which we see as boost. In reality, a naturally aspirated motor runs under pressure even without the supercharger. The pressure we refer to is atmospheric pressure (14.7 psi or one bar). Vacuum is created in the cylinder by the downward moving piston. This vacuum is filled thanks to the atmospheric pressure that exists outside the cylinder. Superchargers (and turbos) only increase the pressure above atmospheric.
More Supercharger Math
Here is a little more (but still simple) motor math to get us started. Suppose our naturally aspirated motor produced a given amount of power at an atmospheric pressure of 14.7 psi. Does it then stand to reason that if we double atmospheric pressure by having the supercharger produce an additional 14.7 psi of boost (above atmospheric pressure), we could then double the power output of our naturally aspirated motor?
In theory (and occasional application) this holds true, but the reality is that the theoretical math and the actual power output often differ. Despite what the math predicts, there are a number of factors working against the theoretical boosted power output.
The major problem with the theory is that the supercharger (any supercharger) requires an input of power to help produce the additional power. Superchargers are driven off the crankshaft and just like any accessory, driving the supercharger takes power away from the engine. Though the supercharger delivers more additional power than required to drive it, the parasitic losses associated with driving the supercharger absorb some of the potential power output.
Let’s try an example to help better illustrate the difficulty we have with the so-called power/boost formula. What happens if we take a theoretical 500 hp NA big block and install a supercharger producing 14.7 psi of boost?
According to the math, we should be able to double the power output to 1,000 horsepower, right? After all, shouldn’t doubling the atmospheric pressure also double the power output? If everything went perfectly, the motor would still not produce 1,000 hp at 14.7 psi since the blower likely required as much as 150 hp (or more) to drive the rotors. The very best you could hope for would now be near 850 hp (1,000 hp – 150 hp).
In reality, the resulting power might be even less on a typical roots blower—like our big block build.
The power/boost formula assumes a supercharger that operates at 100% efficiency (an impossibility). No supercharger runs at 100% efficiency, so in addition to the parasitic losses, we have other factors that might limit the ultimate power production (like intercooling). Despite these obstacles, positive displacement superchargers add huge chunks of power and combining them with big cubic inches is still a time-honored tradition of producing big power.
Supercharging vs. Inlet Air Temperature
One potential downside of running a supercharger is elevated inlet air temperature, as (unfortunately) heat is a natural byproduct of compression. When you install a blower on your motor and pump up the boost pressure (even to just seven psi), you will—in every instance—increase the temperature of the air going into the motor.
Pressure causes heat, and unfortunately, heat is the enemy of performance.
For any performance motor, we strive to supply cool, dense air. The cooler the air, the denser the air. Dense, in this case, means the air is chock-full of power-producing oxygen molecules. The greater the quantity of oxygen molecules, the greater the power production. The obvious answer to keeping things cool on a supercharged application is intercooling.
Many roots supercharged applications rely on an air-to-water intercooler core sandwiched between the blower and lower intake manifold. The downside is this adds even more height to an already tall induction system.
Luckily for blower enthusiasts, the inherent design of the Weiand supercharger already included its own form of intercooling. Perched on top of our Weiand 8-71 blower was a pair of Holley 950 HP carburetors. The fuel supplied by the carburetors above the blower actually helped reduce the air temperature under boost. Basically, the carburetors acted as intercooling for the supercharger.
When combined with a realistic boost level (we ran under seven psi), the combination was very safe and efficient.
The Boosted Big Block Chevy Test Motor
Enough with the theories, let’s get to our boosted big block. The best way to demonstrate the power potential of a blown big block was to combine the two and run them on the dyno.
Starting with a production 454, the four-bolt block was bored 0.060 inch over, honed, and decked to prepare for the trio of forged internals. In addition to the overbore, the displacement was increased via a Lunati Pro Series steel Stroker crank. The Pro Series featured 4340 steel construction, precision tolerances and plasma-gas nitrite heat treating. The Lunati steel 4.25 inch Stroker crank combined with the 0.060 inch overbore resulted in 496 cubic inches.
The Stroker crank was combined with a set of Probe Racing 18cc domed pistons and Lunati 4340 Pro Billet connecting rods. The forged pistons incorporated a single intake valve relief to ensure adequate piston-to-valve clearance for the COMP blower cam. The COMP 300BR-14 solid roller offered 0.652 inch lift, a 255/262 degree duration split, and 114 degree LSA. COMP also supplied the 819-16 lifters and 3110 double roller timing chain. The entire rotating assembly was precision (internally) balanced using a neutral Rattler damper from TCI.
Knowing the Stroker required plenty of airflow, we took a big swing at the induction system, starting with the heads. Airflow Research supplied a set of AFR CNC-ported 315cc Magnum BBC heads. The AFR BBC line of aluminum heads featured a number of impressive features including 3/4 inch thick head deck surfaces for maximum sealing, perfect for our supercharged application. The AFR BBC heads also featured reinforced rocker stud bosses, rolled valve angles (two degrees) to improve flow characteristics, and an exclusive combustion chamber design.
Available in multiple configurations, we chose the CNC-ported 315 heads. The 315cc heads started out life as a set of as-cast 305cc heads, but were then treated to full CNC porting including the already efficient combustion chambers. We ordered our big block heads with 121cc combustion chambers to produce a static compression ratio of just under 10.0:1. The compression choice allowed the motor to run effectively as an NA or blown big block. Though small compared to the other AFR offerings, thanks to the CNC porting, the 315cc heads flowed nearly 390 cfm on the intake and over 300 cfm on the exhaust. These are huge numbers for any performance BBC head, but especially considering the comparatively small port volumes.
NA vs. Supercharged Comparison Testing
Before installation of the 8-71 blower, we made sure to run the 496 BBC in naturally aspirated trim to establish a baseline. For the NA runs, we equipped the 496 with a single plane, Edelbrock 454R intake, Holley 950 HP carburetor and MSD ignition. Additional goodies included Hooker 2-1/8 inch, long-tube headers, COMP 1.73 ratio aluminum roller rockers, and a Meziere electric water pump.
After a few break-in cycles and some fresh Lucas oil, we were rewarded with peak numbers of 651 hp at 6,300 rpm and 579 lbs.-ft. of torque at 4,800 rpm.
Satisfied with our baseline, off came the Edelbrock intake and on went the supercharger. The blower was equipped with a pair of 950 HP carburetors, and pulley combination (59 tooth top/57 tooth bottom) to produce a maximum of 6.5 psi of boost. After dropping the ignition timing down from 40 degrees to 30 degrees, the Weiand 8-71 Street Supercharger produced 4.9 psi at 3,000 rpm and peaked at 6.5 psi at 6,500 rpm.
The boost supplied by the 8-71 increased the peak power output from 651 to 898 hp and torque from 579 to 764 lbs.-ft. Running less than seven psi, the roots blower upped the power ante of the 496 stroker by an amazing 238 hp and 185 lbs.-ft. of torque.
After adding the Weiand 871 to the 496 big block it is easy to see why the big blocks and blowers are so popular.
Dyno Chart: 496 Big Block Stroker, NA vs Weiand 8-71 Blower (6.5 psi)
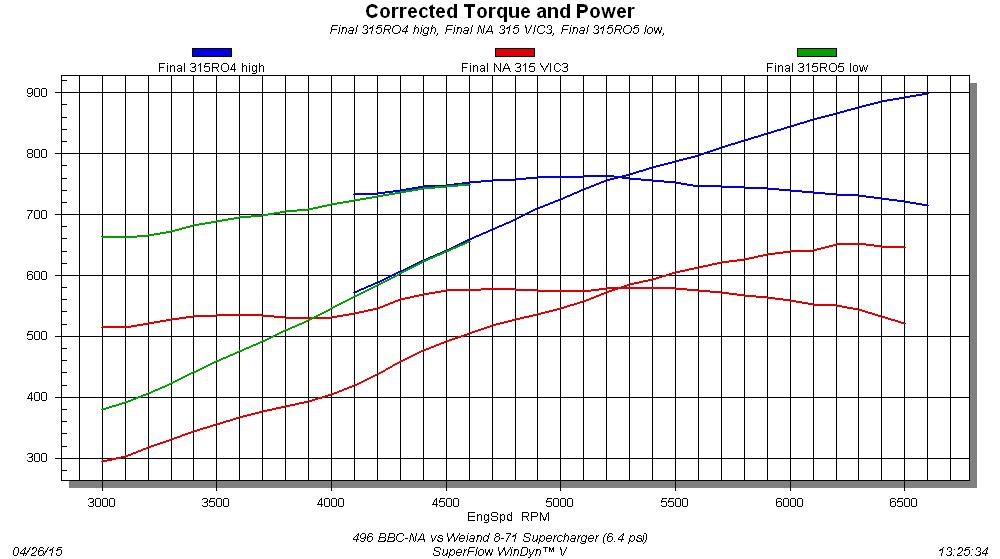
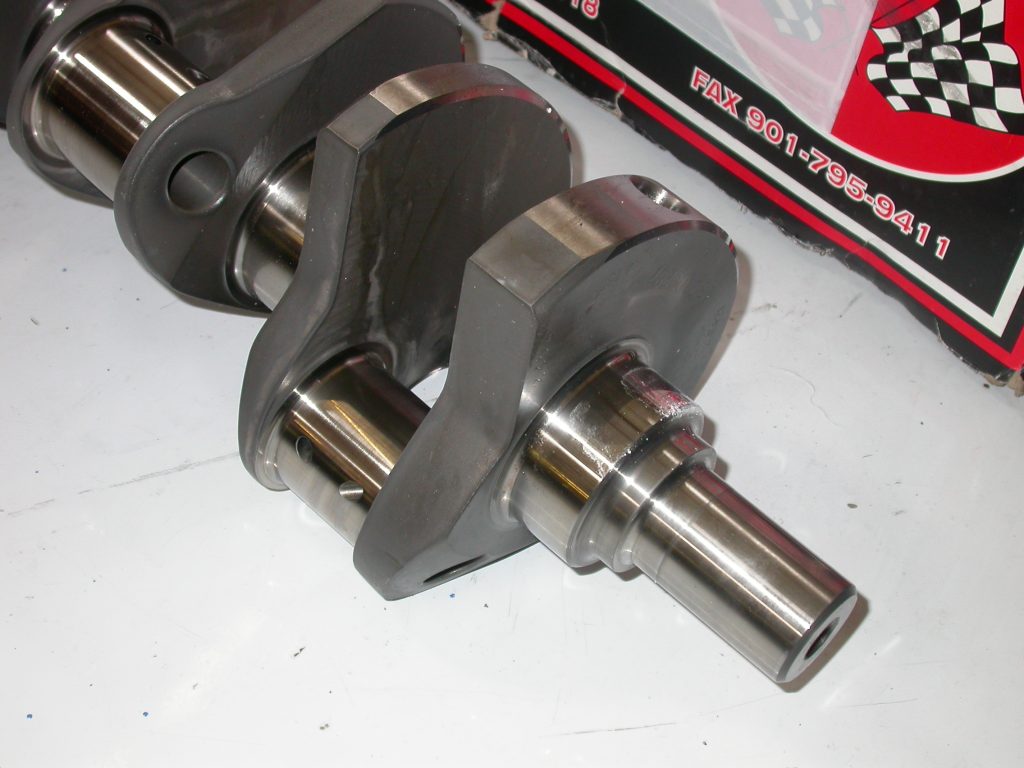
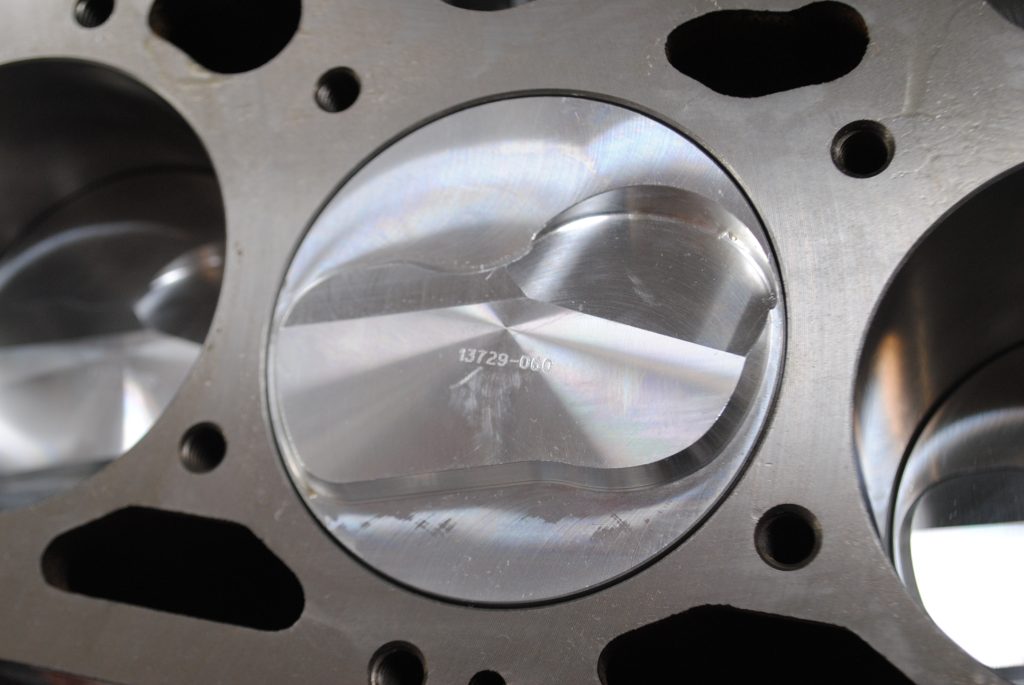
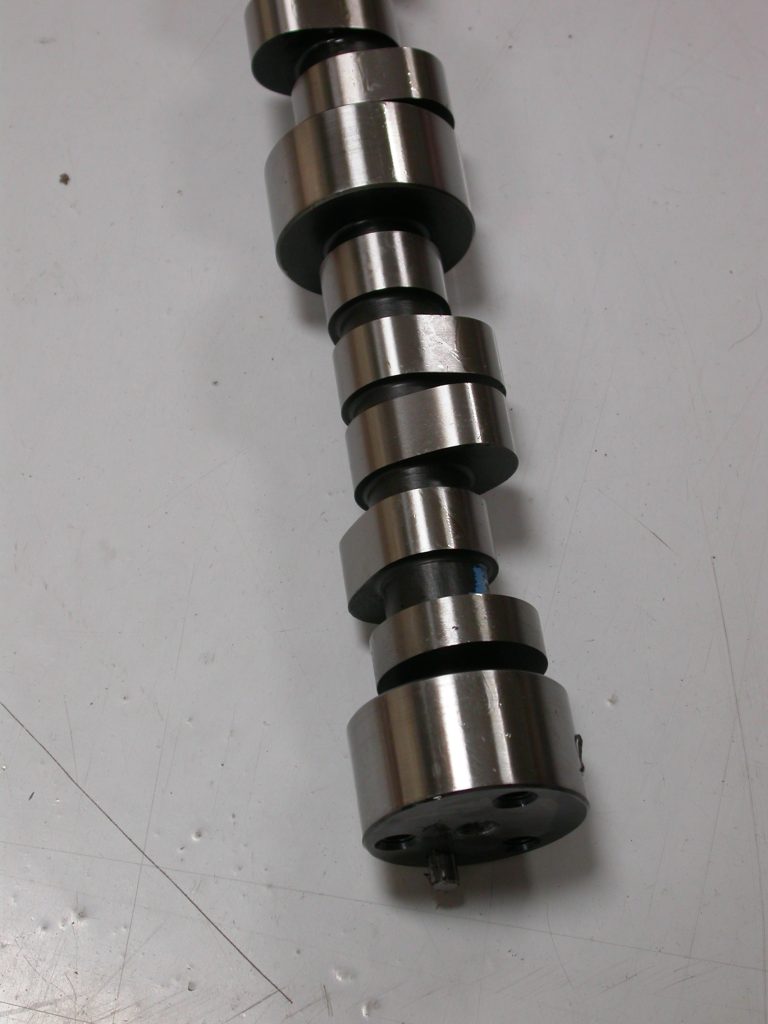
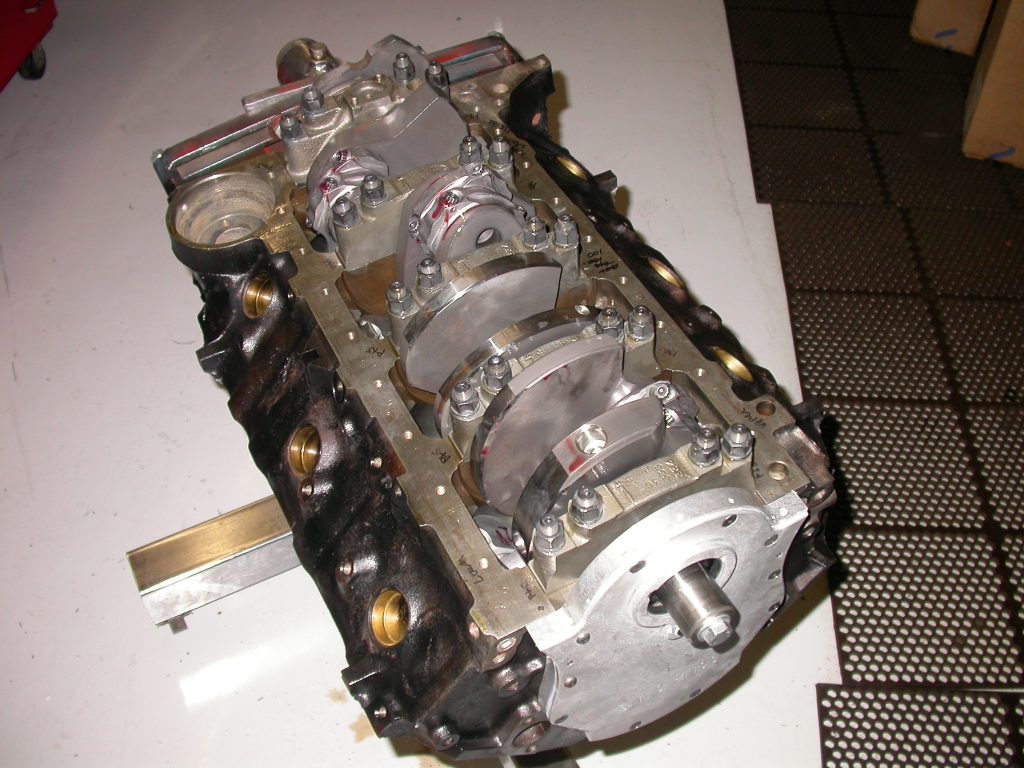
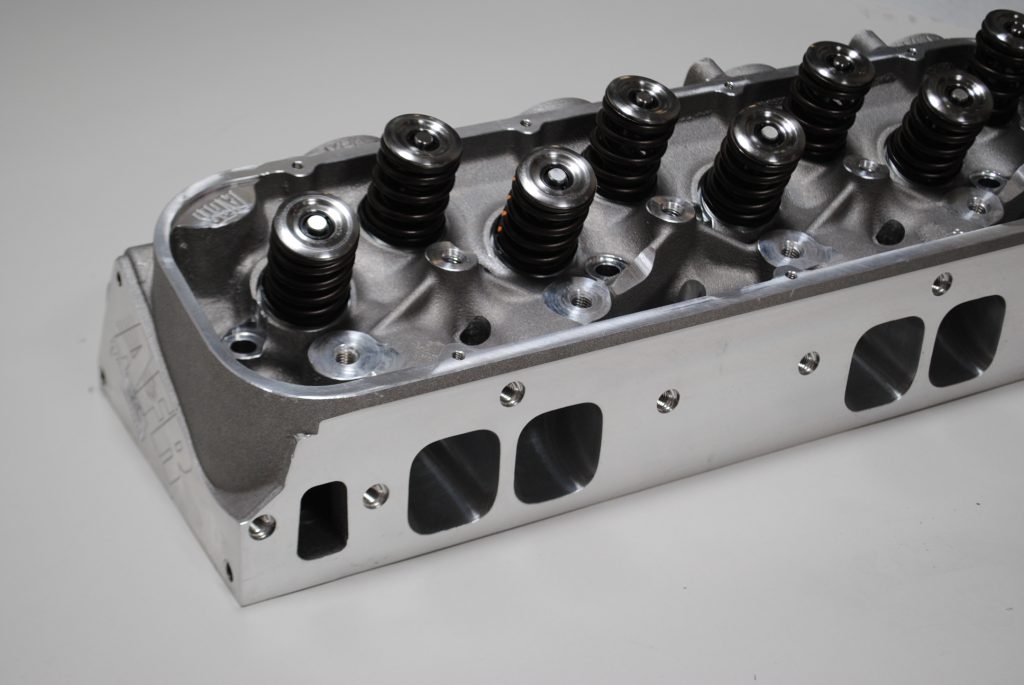
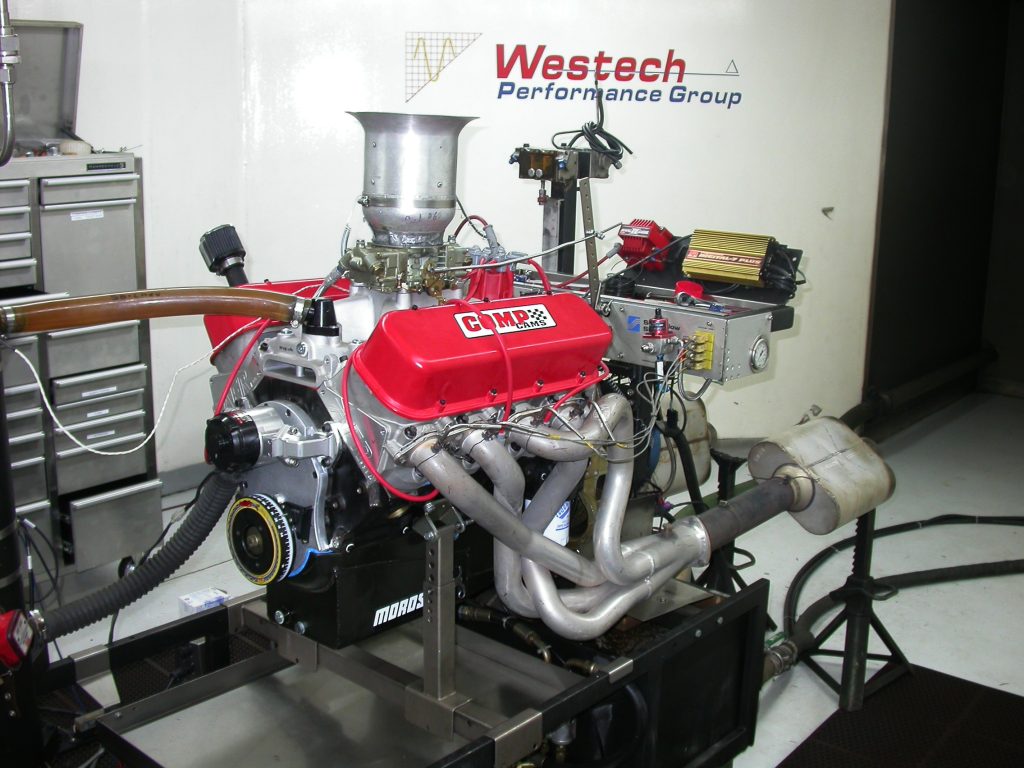
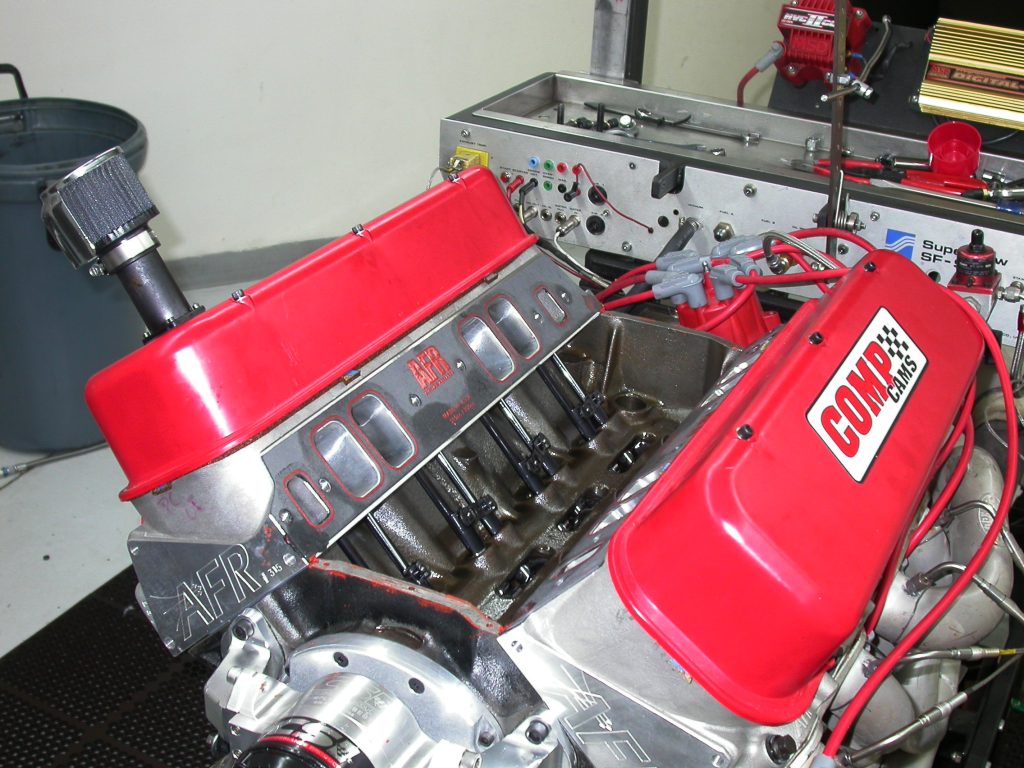
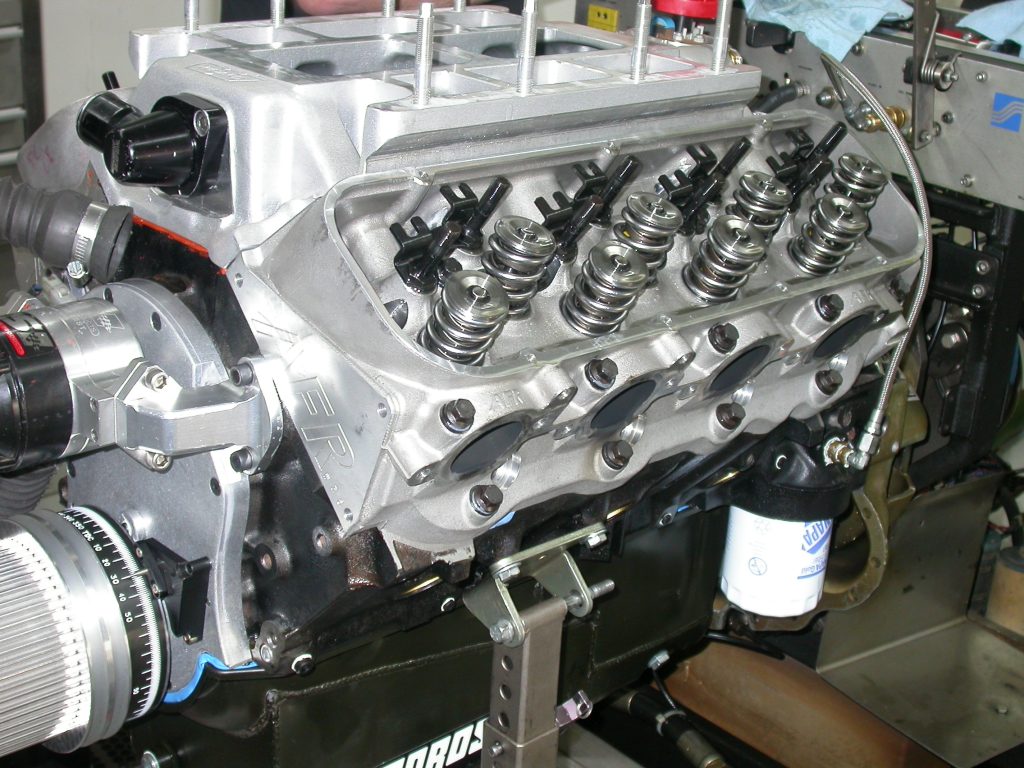
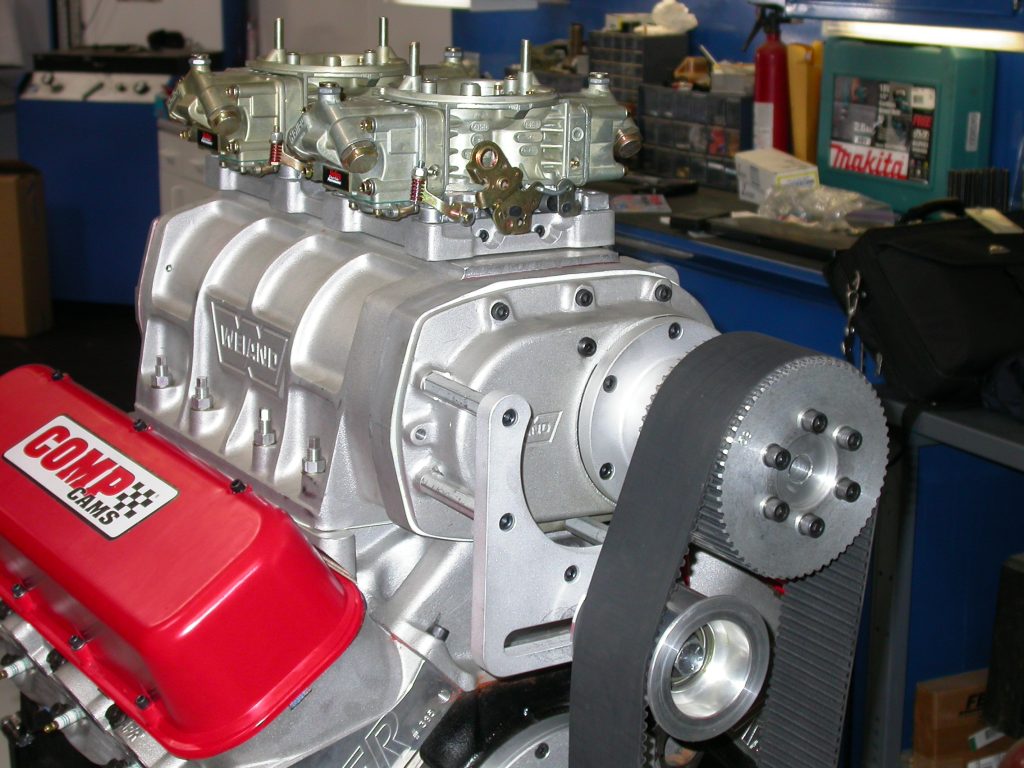
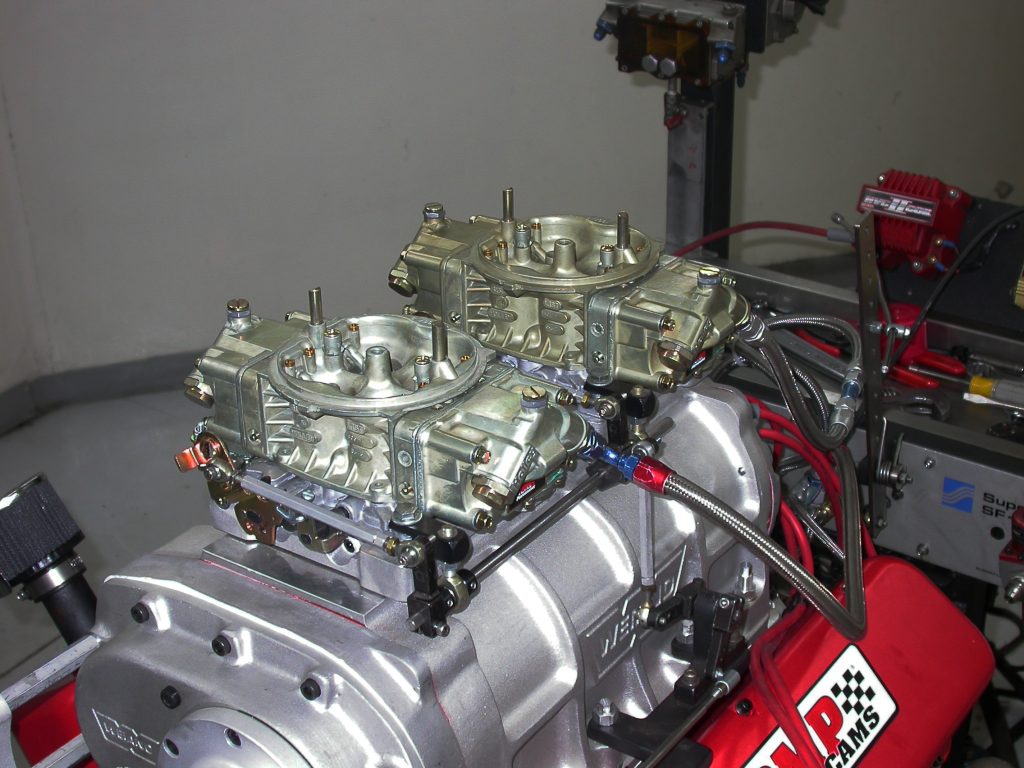
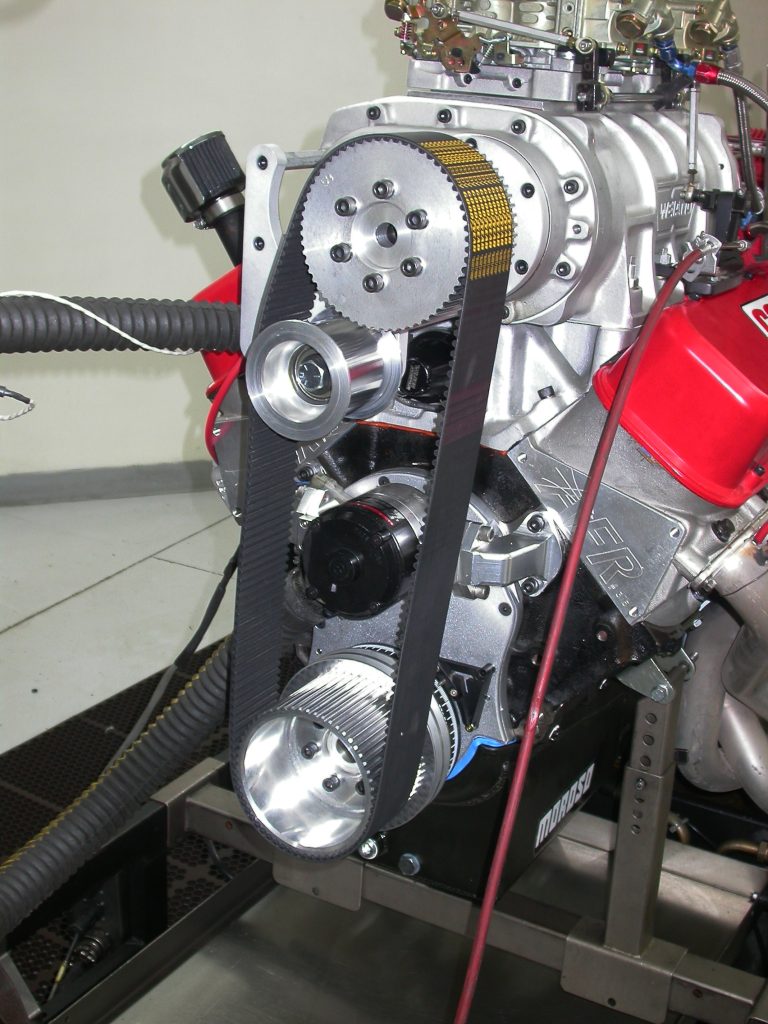
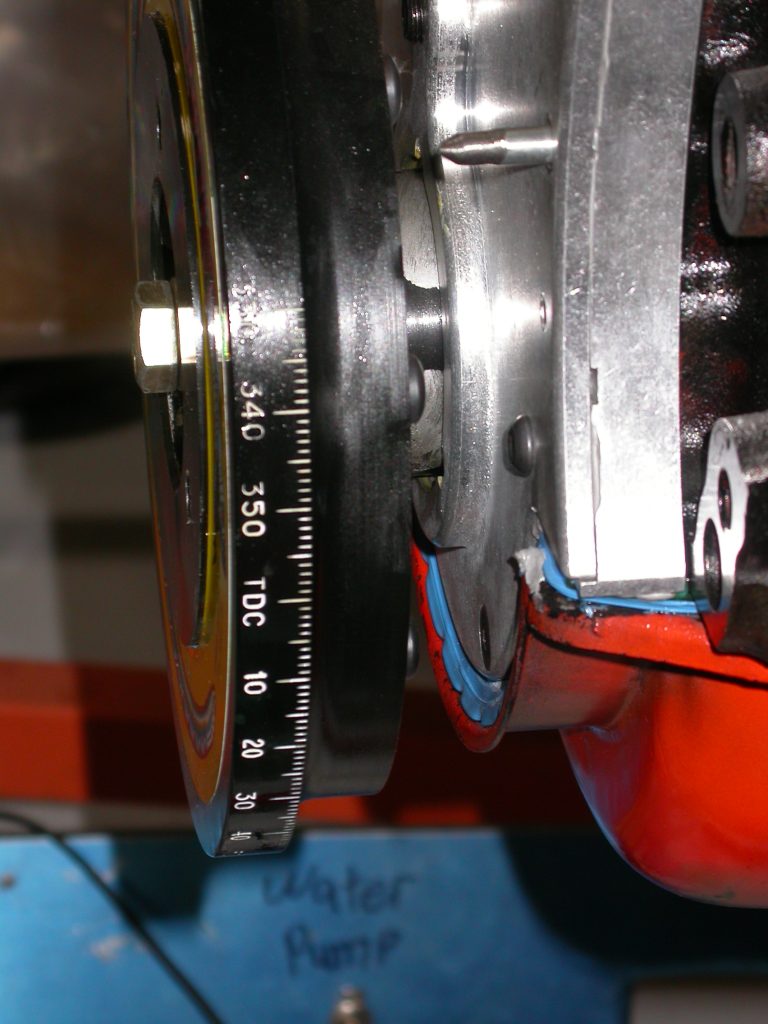
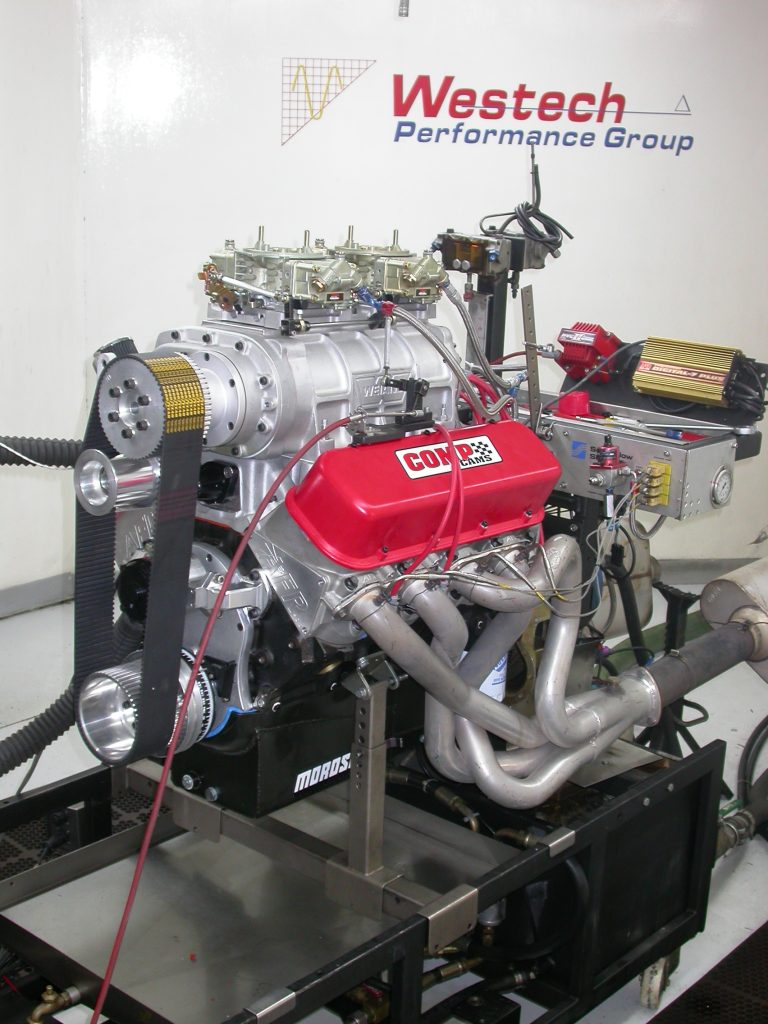
Comments