The go-to tool for tightening and loosening fasteners is the common ratchet. Everyone has at least one, but most have lots more. I myself have over a dozen. But like any other tool, you need to use the ratchet for the task at hand. It’s really not the best idea to use a big 1/2-inch drive ratchet on something like a 1/4-inch fastener. You just know there’s a mistake sitting there waiting to happen.
The most common automotive ratchets drive sizes are 1/4-inch, 3/8-inch drive, and 1/2-inch. There are larger drives available but most of those are reserved for bigger machinery. If you’re using a 3/4- or one-inch drive ratchet in an automotive application, it’s like swatting flies with a sledgehammer.
The size of the drive is typically in proportion to the size of the socket used. Typically, a 1/4-inch drive will find use in electrical, small panel and interior work. A 1/2-inch drive is perfect for suspension and internal engine use. The 3/8-inch drive is useful for just about everything else.
The tooth count in the ratchet head is important too. Tooth count refers to the number of teeth on the drive gear. With more teeth in the drive gear, the less you have to move the handle in order to engage the next tooth. This means a ratchet with more teeth requires less swing to operate.
Sometimes a ratchet sticks or jams up and won’t operate. The trouble here can be caused by dirt, shop debris, or even corrosion getting into the mechanism. The fix is to disassemble the ratchet and clean any dirt or debris. Lubricating ratchets is important too. Some folks use a light general purpose machine oil such as 3-In-1 while others use ATF, moly lube or even engine assembly lube. Most pros will tell you to use a lubricant that won’t attract dirt and dust. And don’t over-lube, either. That will only attract more dirt which in turn starts the jamming cycle over again.
Ratchet mechanisms do fail. Sometimes it’s the gear in the ratchet head. Other times, it’s the pawl. These are the small teeth inside the ratchet head that engage with the gear. If they’re worn heavily, the ratchet might skip. There are usually repair kits available for the higher-quality ratchets.
With conventional ratchets, you simply pull the socket off the mechanism. If it’s tight, a small flat blade screwdriver can be used to pop off the socket. Some ratchets have quick release mechanisms. They have a button on the top of the mechanism that releases the internal ball detent that secures the socket. What’s the best setup? Your choice. I personally don’t use ratchets with quick release buttons simply because you can accidently release the socket or socket and extension at the worst possible time.
Straight handle ratchets are available with various handle lengths. The length does affect how much torque you can apply to a fastener. A stubby handle ratchet is easier to swing in close quarters but won’t apply as much torque as one with a longer handle.
Some straight handle ratchets have flex head that allow you to adjust its angle. Some simply swivel. Others use what’s often called a “roto head”. Roto heads provide roughly 270 degrees of head rotation. That allows you to get the ratchet into really tight spots and still get a decent amount of swing to the tool.
One version of the flex head configuration is the dedicated spark plug ratchet. It has a handle with a serious curve in it to help you reach difficult-to-access spark plug locations.
Finger or palm ratchets are another variety. Here the ratchet handle is round. It allows you to get into tight spots and turn the fastener with either the palm of your hand or your fingers. Most of these ratchets have a 1/4-inch drive.
As you can see, there’s a lot more to ratchets than first meets the eye. For a closer look, check out the accompanying photos.
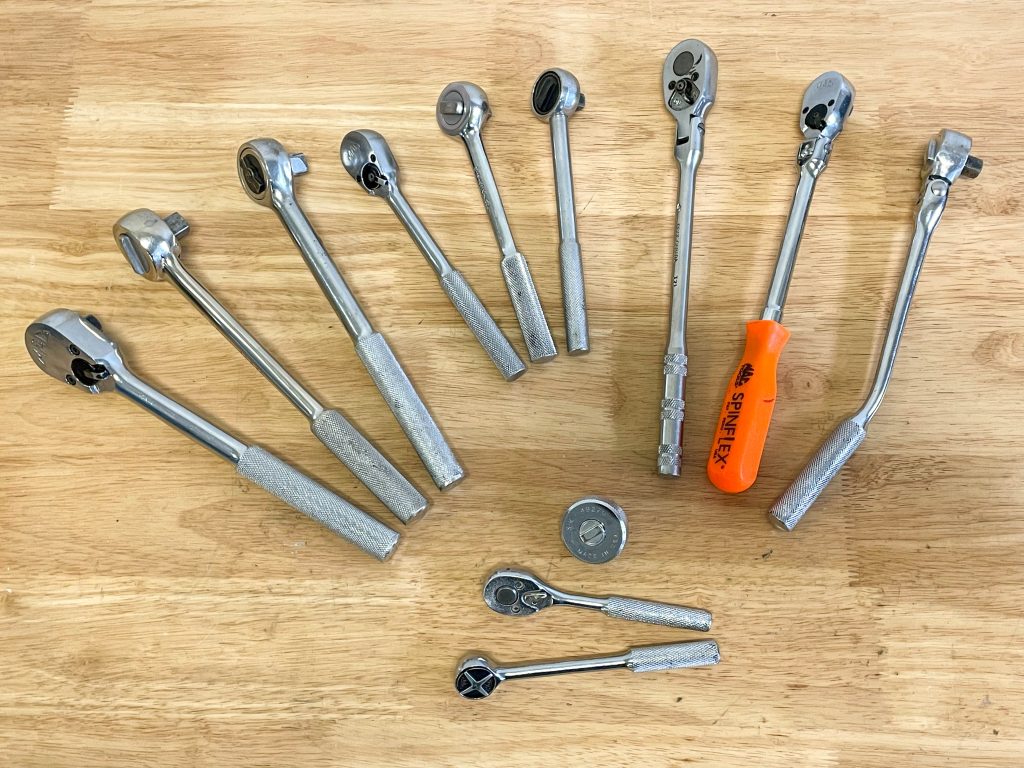
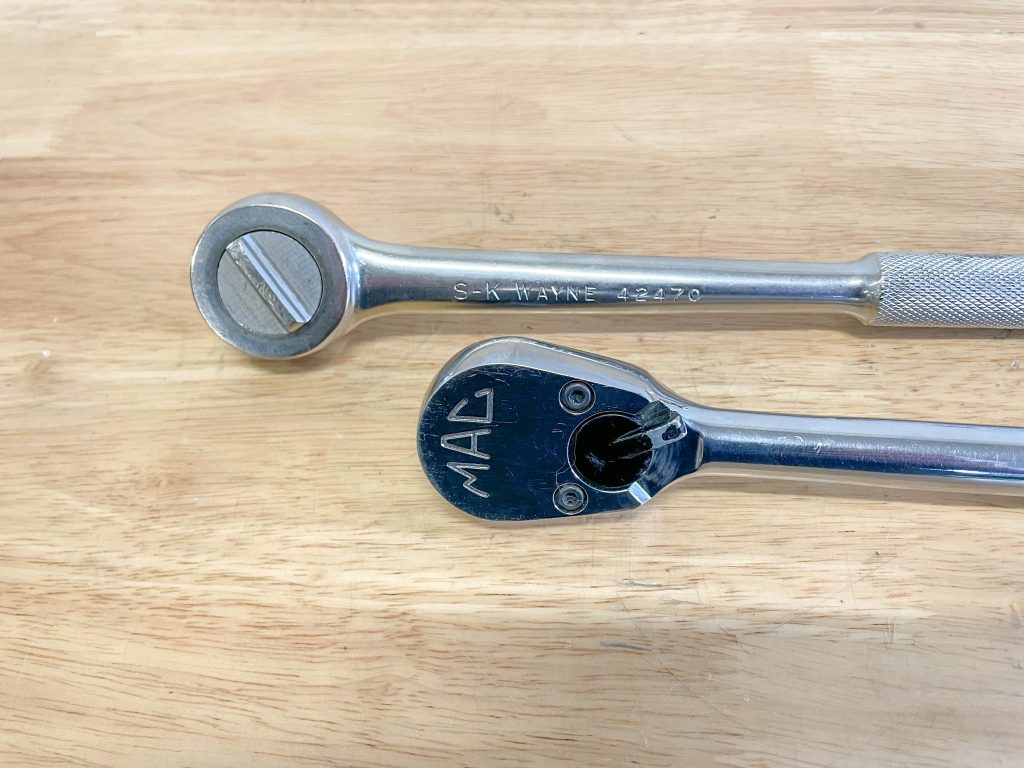
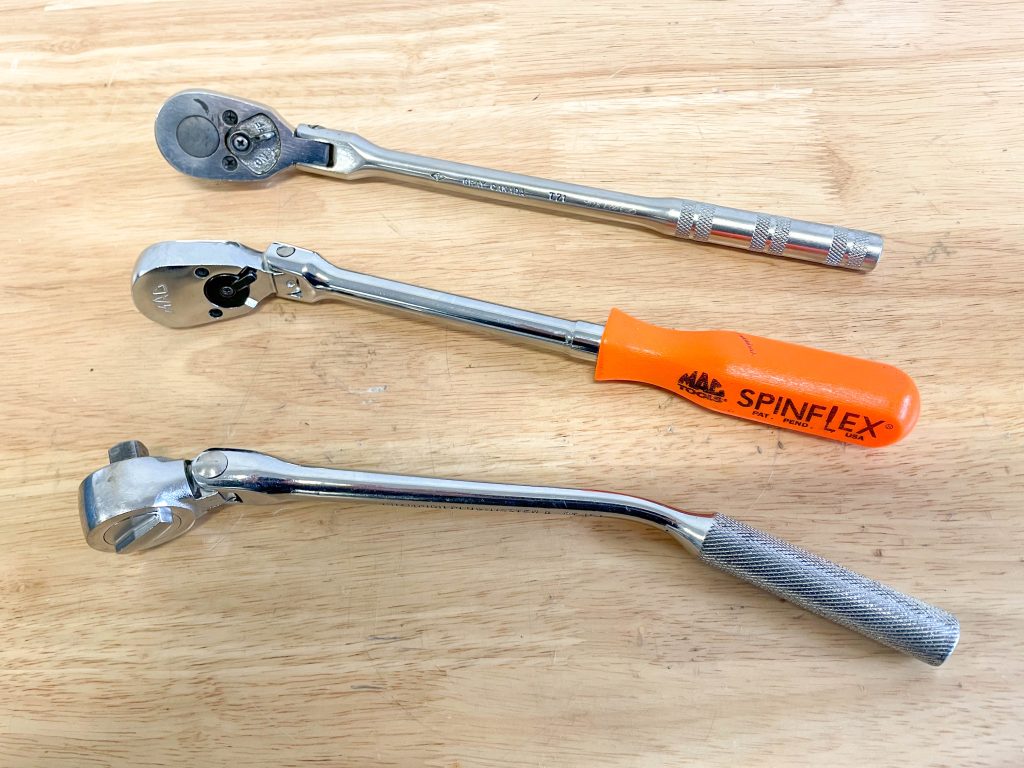
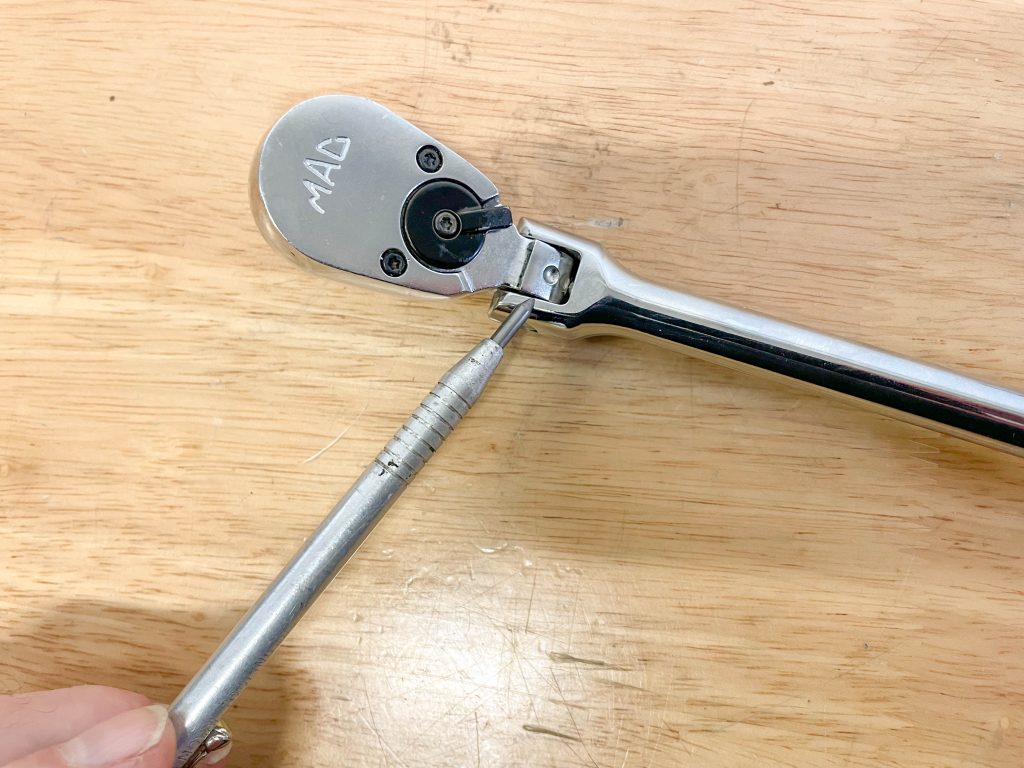
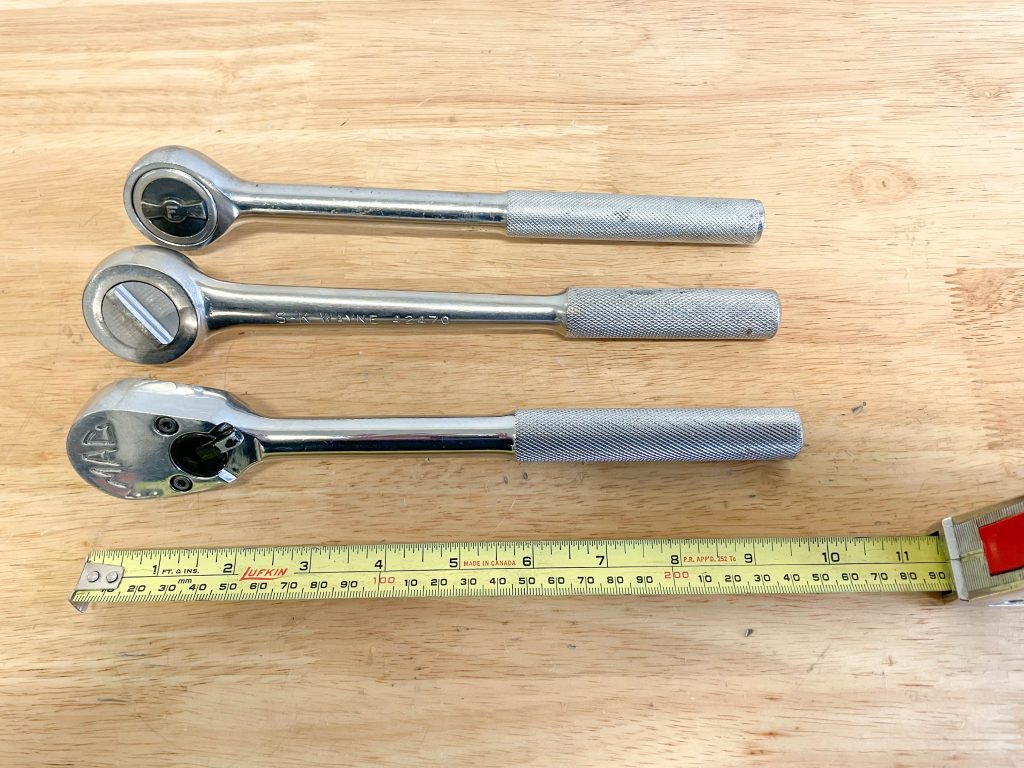
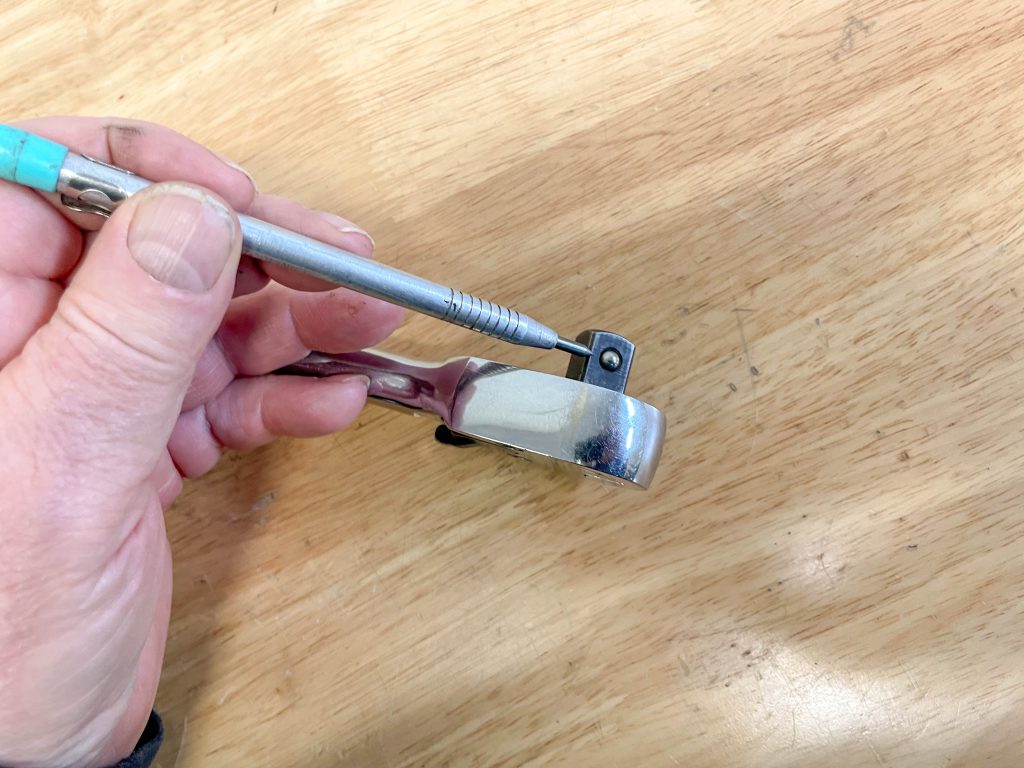
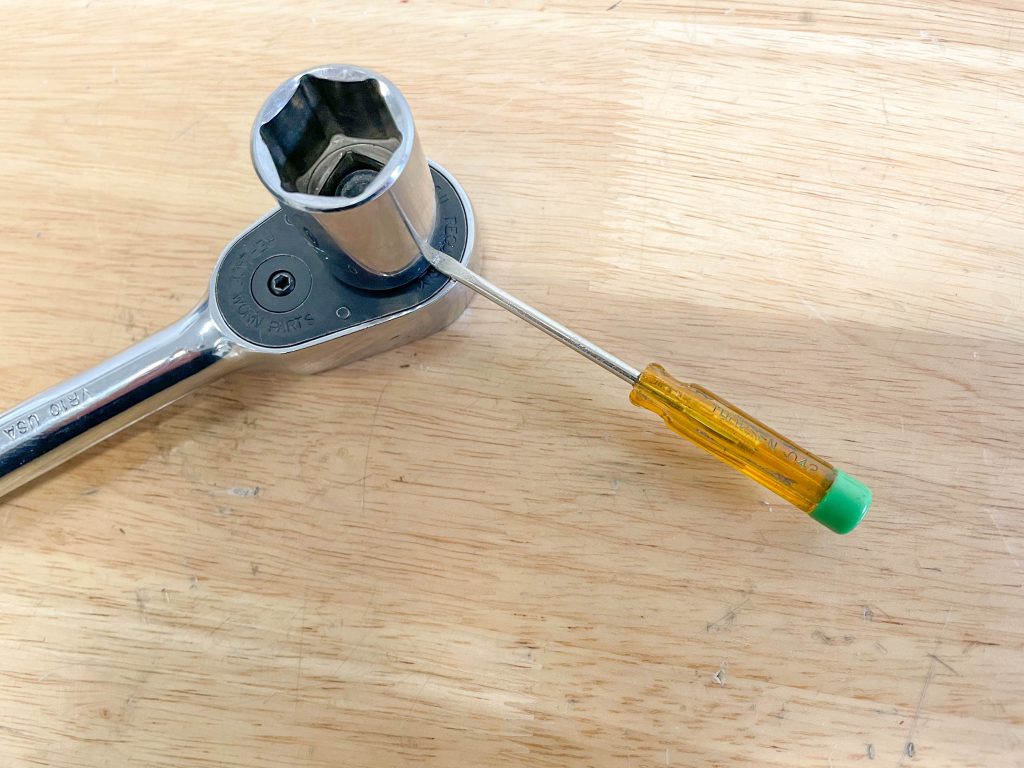
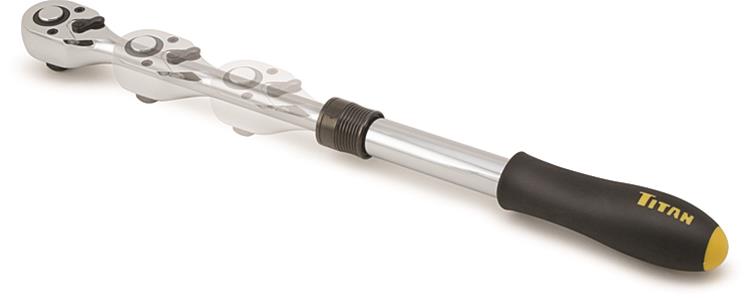
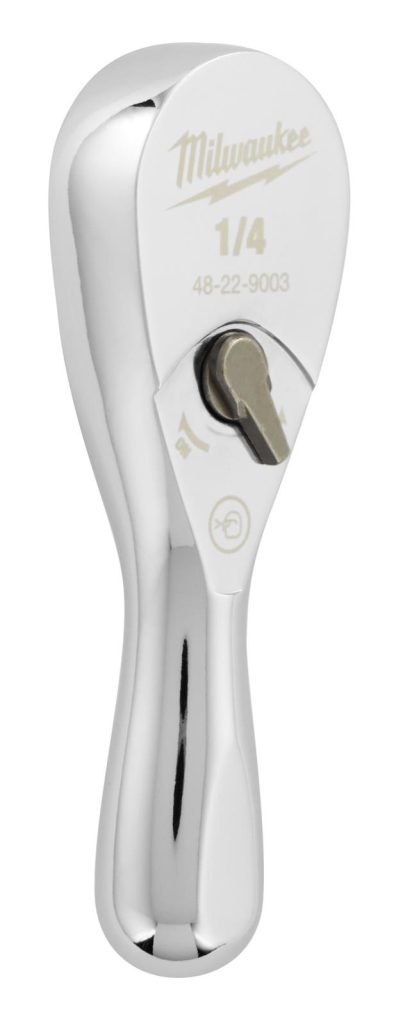
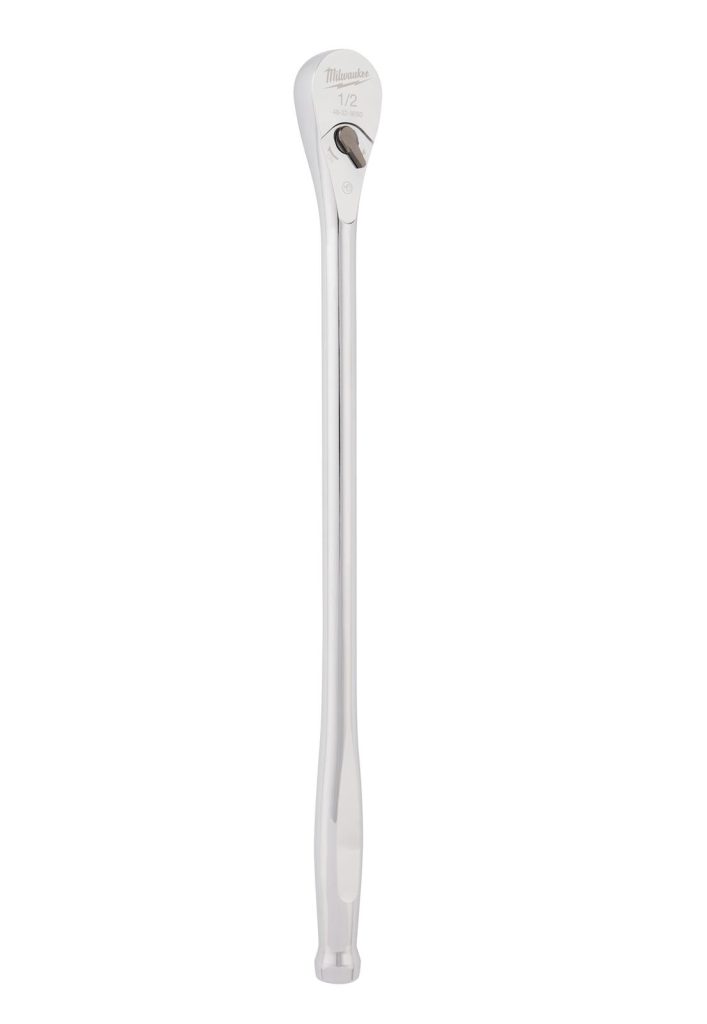
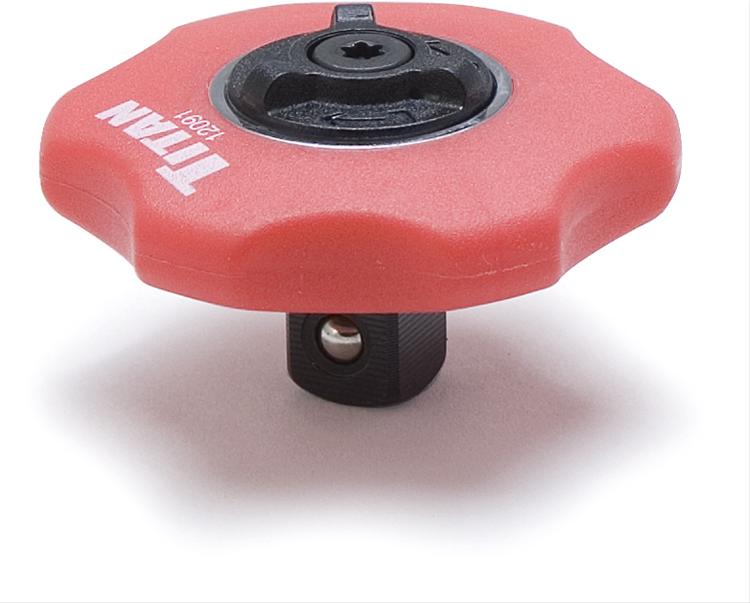
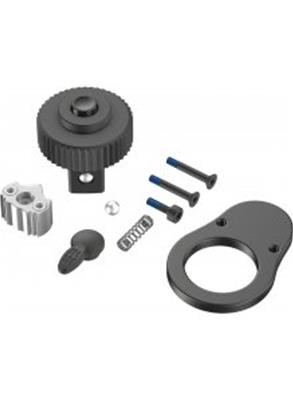
Comments