Is the carburetor dead and gone?
Not by a long shot, but that doesn’t mean we haven’t come a long way with EFI. Sure, carburetors have been used to provide air and fuel for millions of vehicles for decades, but there is obviously a reason that all the OEMs eventually made the switch to modern fuel injection.
While carburetors perform well when paired with a specific motor, changes made to the motor can sometimes play havoc with the metering. This is especially the case when you toss boost into the equation. Although blow-through carbs have been made to work well, they almost always work well at cruise, part throttle, or WOT—but rarely do they work perfectly for the myriad of combinations of load, rpm, and boost.
This is where electronic fuel injection (EFI) shines.
The key to success is that precise fuel metering from the EFI system is not dependent on the air supply of the motor. This means not only will the EFI system provide precise metering at idle, but that precision will continue regardless of engine speed, load, or boost.

The Value of Charge Cooling
To take nothing away from the carb contingent, the one area carburetion offered an advantage over fuel injection was in charge cooling. On a typical carburetor, the fuel delivered by the carb has always been a function of the air being pulled through the venturis in relation to jetting. The introduction of the fuel supplied into the air stream provides a cooling effect that ultimately improves power.
On most port fuel injection systems, where the fuel is introduced down near the cylinder head, this charge cooling is minimized. Thus, a comparison between a carburetor and port EFI on the same manifold will usually result in the carb showing more power from the charge cooling (assuming the proper AF mixture can be produced with the carb).
This all changes when the fuel injection system introduces the fuel into the air stream from a throttle body located on top of the intake manifold, similar to a carburetor. The charge cooling offered in this manner is especially important for blow-through, boosted applications. The charge cooling offered by the introduction of fuel on a boosted application acts as a form of intercooling, offering both more power, and, as extra security against harmful detonation.
A FAST XFI & EZ-EFI Supercharging Combo
Not surprisingly, the folks at FAST obviously recognized the benefits and limitations of a blow-through carburetor, and so, decided to offer a powerful alternative. By combining an XFI Sportsman ECU with their already popular EZ-EFI throttle body, they were able to come up with a combination capable of supporting over 1,000 supercharged horsepower.
For ease on installation, the 4150 throttle body bolted in place just like any 4-barrel carburetor, including linkage and carb bonnet mounting.
Unlike a conventional carburetor, the EFI throttle body featured a total of eight injectors and all the necessary sensors built right in. The throttle body featured sensors for TPS, IAC and IAT, as well as an integrated map sensor. While the throttle body can be run with a 1-bar map sensor designed for a naturally aspirated combination (with greater resolution), we opted for a 2-bar map sensor that allowed us to apply boost. The one important sensor not part of the throttle body was the ECT, or engine coolant temp.
Meet the “Gladiator 2” Test Engine
For this test, we elected to install the ECT in the intake manifold of our small block Chevy test motor. The throttle body was combined with the powerful FAST XFI Sportsman management system, which allowed full control of the air/fuel and timing, as well as providing data logging capability.
Naturally we needed a suitable combo to properly test the merits of the blow-through FAST EFI system, and the 372ci small block affectionately dubbed the Gladiator 2 by the good folks at Westech Performance was the perfect choice.
How did the Stroker small block earn the nickname, you ask?
The original Gladiator was the go-to small block for literally hundreds of tests and thousands of dyno pulls. It continued to soldier on, and be victorious in every battle, regardless of what we threw at it. This G2 version, offered every bit as much fight, in a much stronger package.
Thanks to a Dart SHP Stroker short block with a 4.125 inch bore, the Gladiator 2 was sporting forged internals and 372 cubic inches. For this test, the G2 was equipped with a Comp Xtreme Energy cam that offered 0.540/0.562 lift split, a 242/248 degree duration split, and 110 degree LSA.
Finishing up the G2 was a set of free-flowing, CNC-ported AFR 195 Eliminator heads, Edelbrock Performer RPM Air Gap intake, and FAST dual-synch distributor.
Testing the System with a TorqStorm Supercharger
The game plan was an easy one, first we (meaning David Page) would tune the 372 G2 in naturally aspirated trim, then again after the installation of a TorqStorm supercharger. The TorqStorm supercharger was perfect for this type of test, as it allowed easy installation and was sized perfectly for power production near 700 hp.
As we expected, Mr. Page had the small block up and running in no time, and whipped up the tune to produce optimum power production. Run on the dyno with 1-3/4 inch dyno headers, the FAST-injected small block produced peak numbers of 501 hp at 6,200 rpm and 473 lb.-ft. of torque at 4,800 rpm.
After scaling the tune for the TorqStorm supercharger, we were rewarded with 681 hp at 6,500 rpm and 601 lb.-ft. of torque at 5,100 rpm.
The blower was pumping out a peak boost reading of 8.3 psi, which we knew was plenty safe thanks to the fuel cooling provided by the 8-injector throttle body. Our thanks to David for taking the time during his visit (for a FAST Seminar) to toss the tune on our small block, and to the guys at FAST for supplying the XFI Sportsman EFI system to Westech for testing.
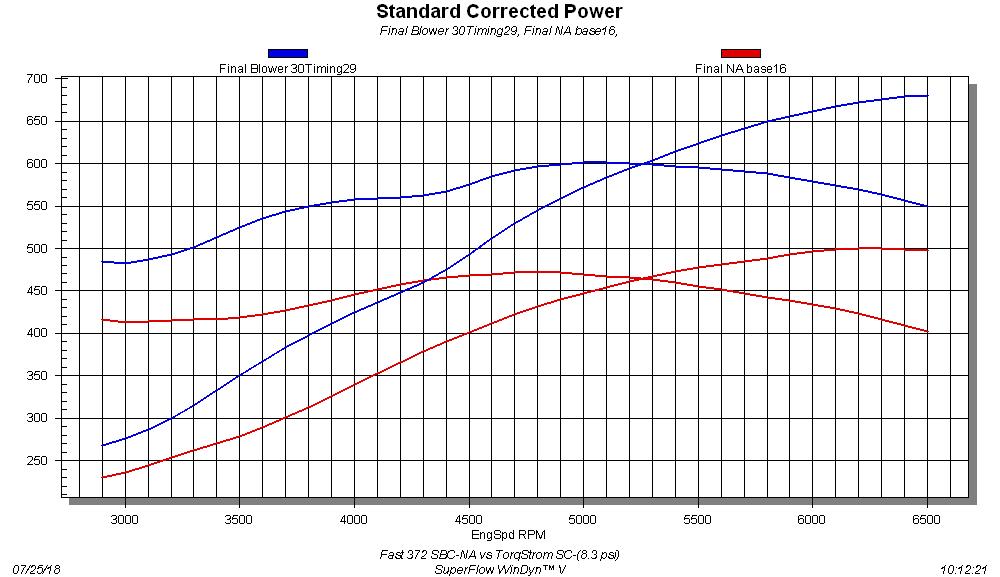

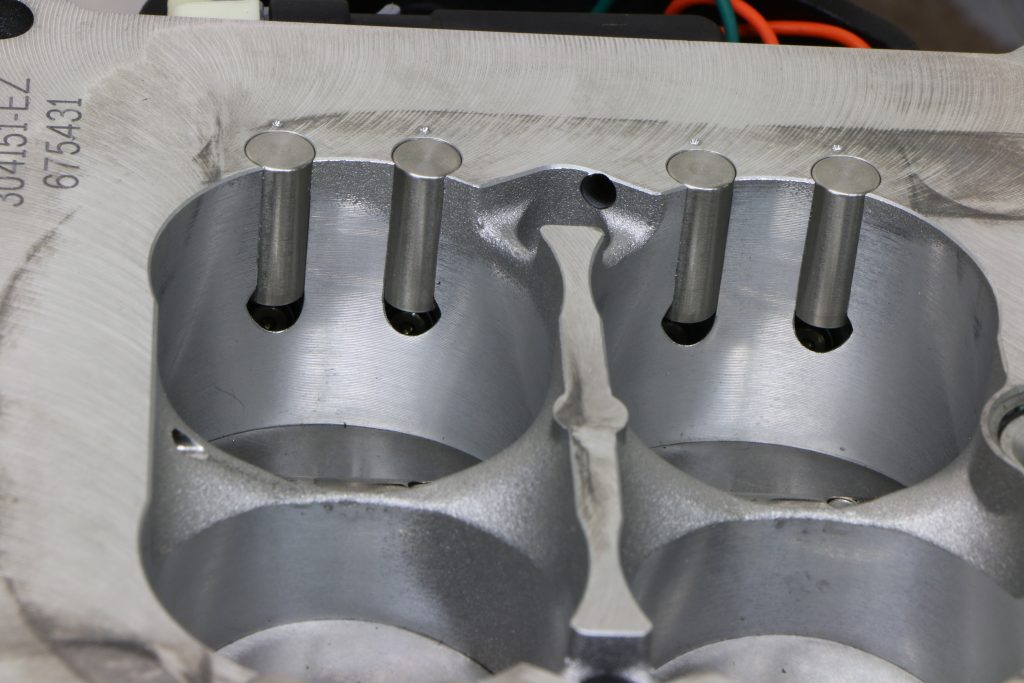
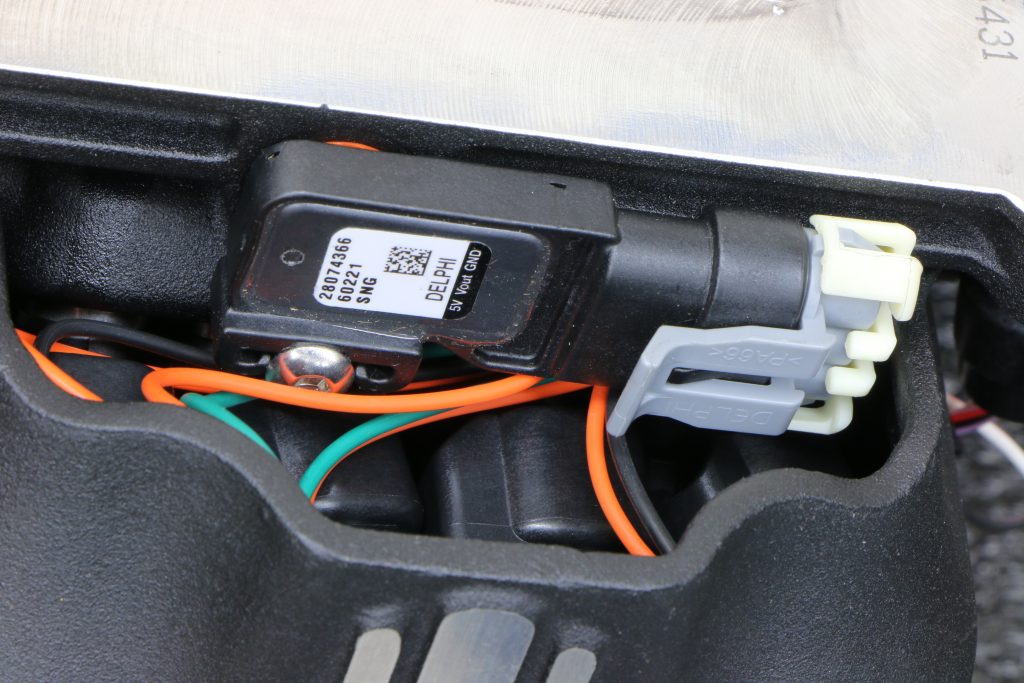
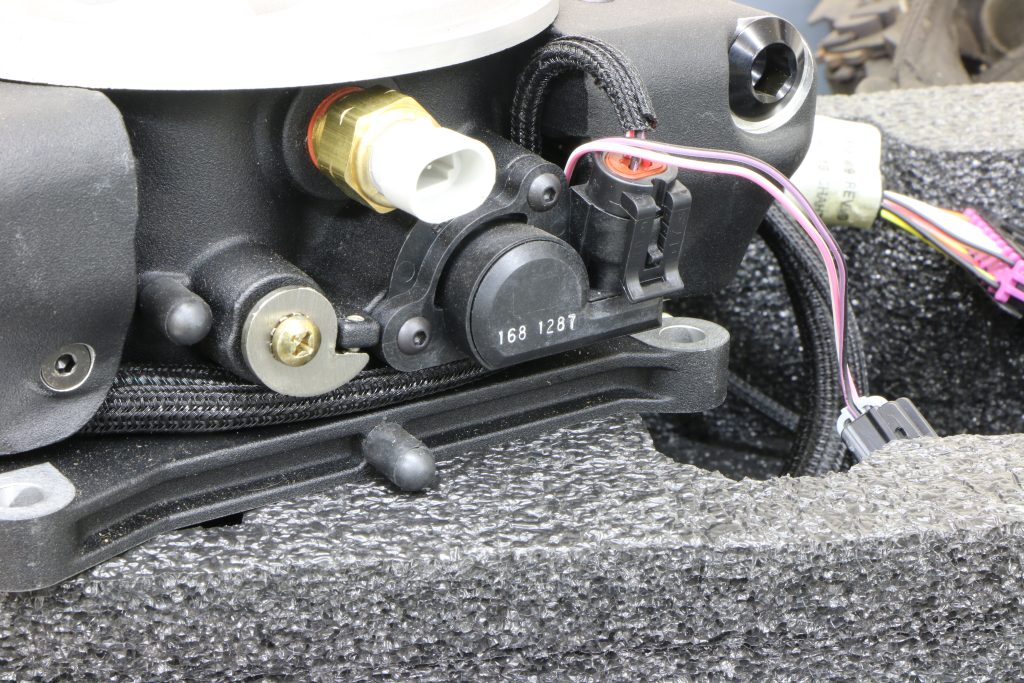
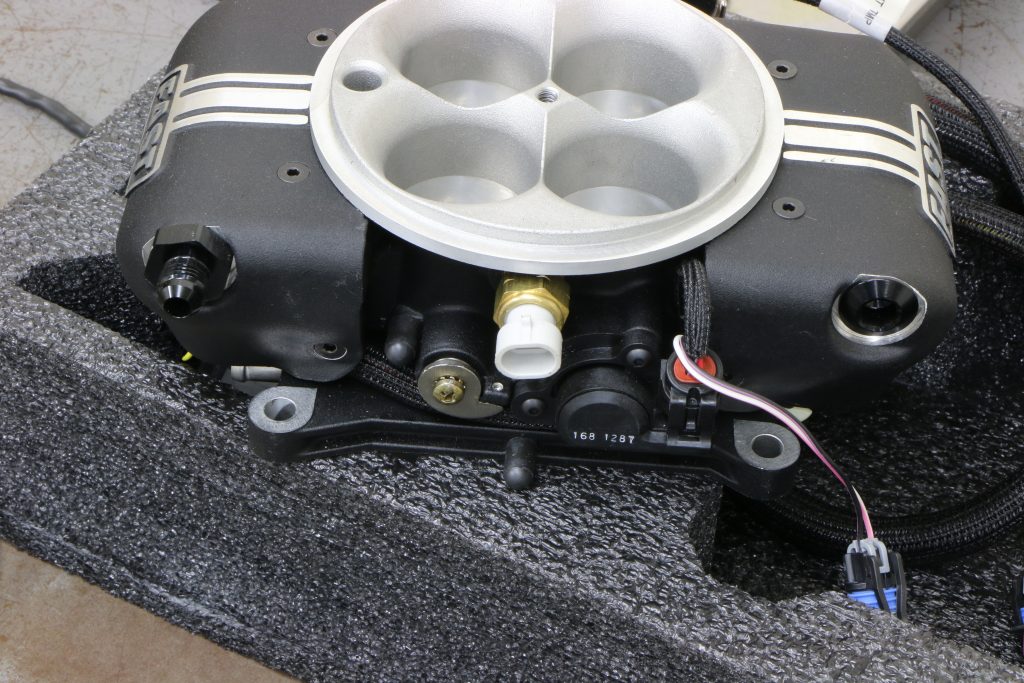
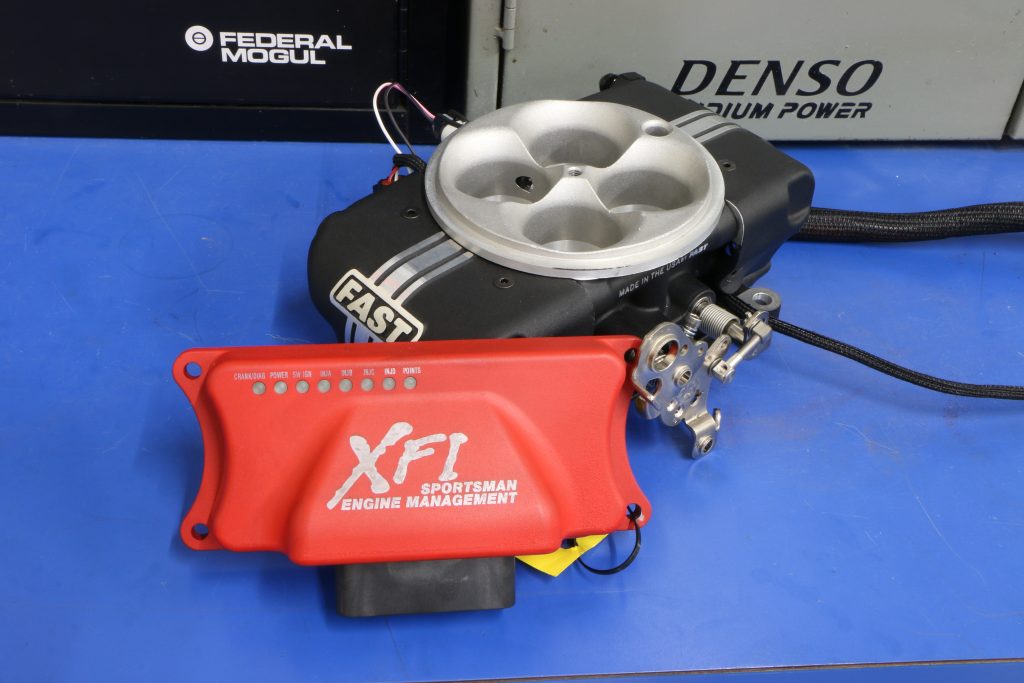
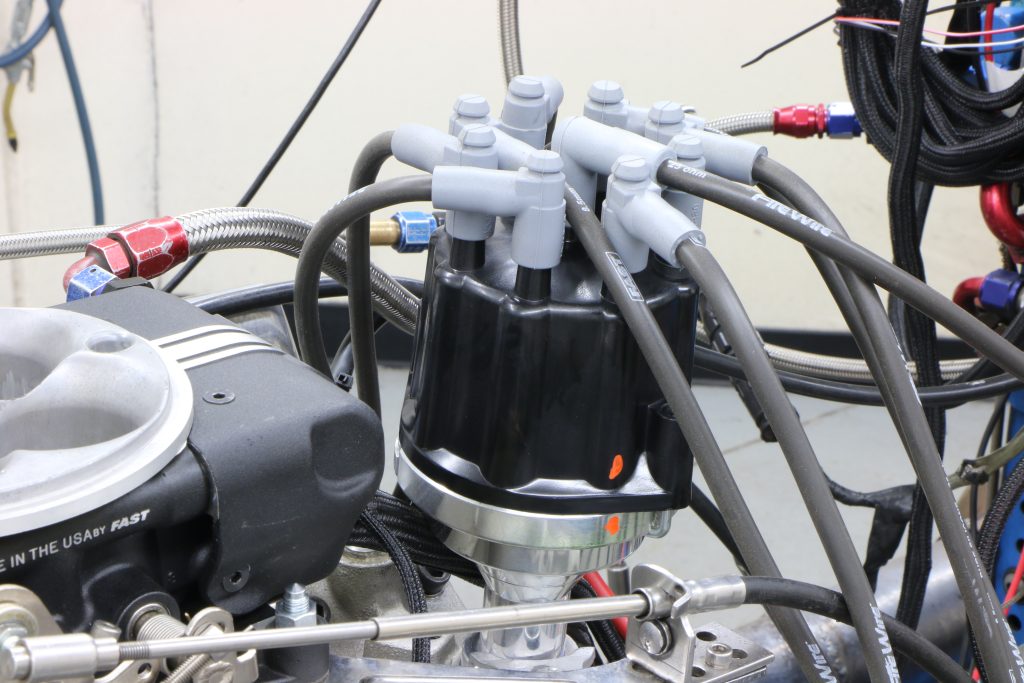
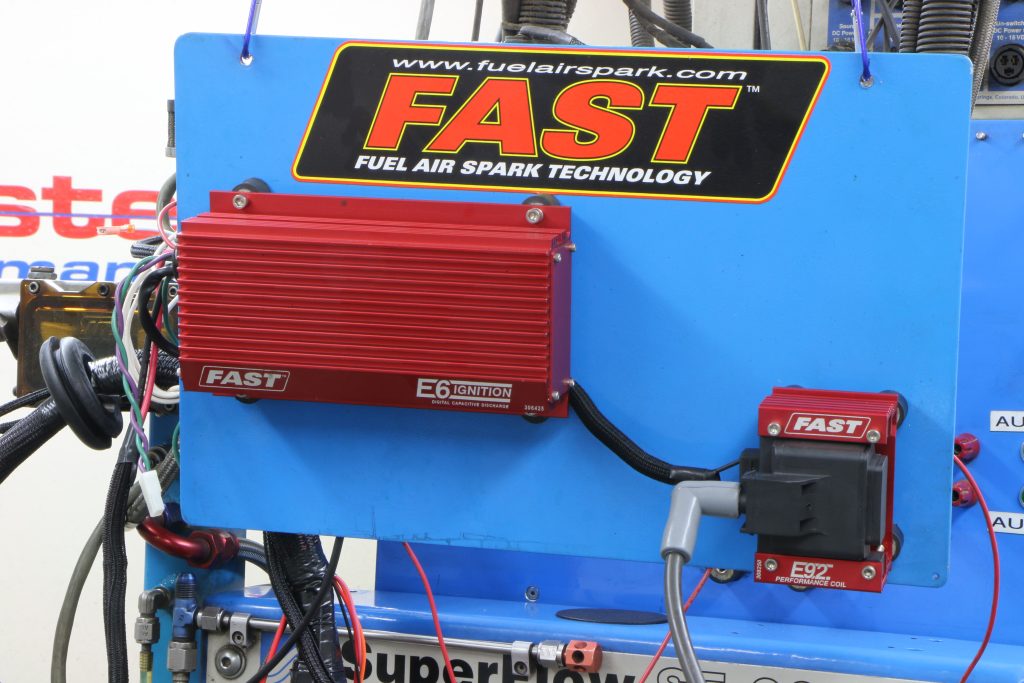
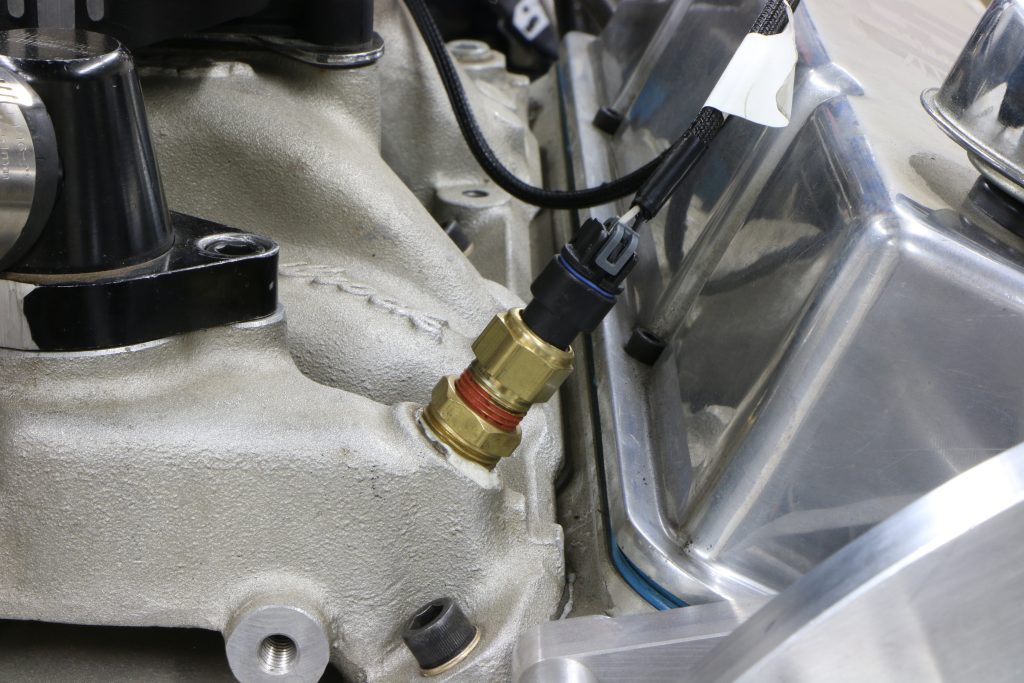
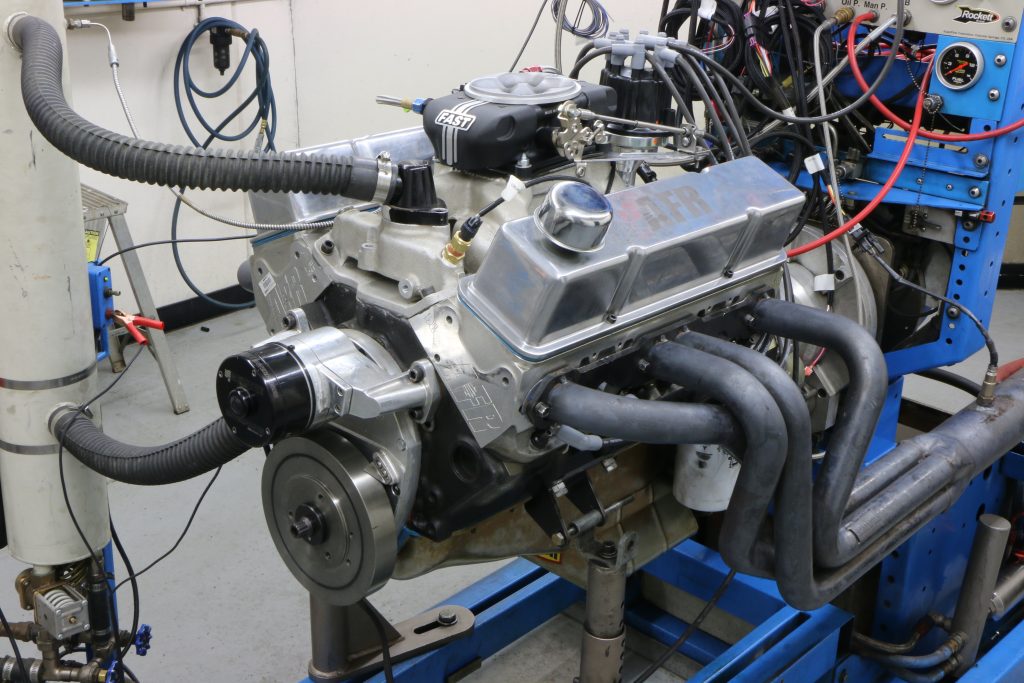
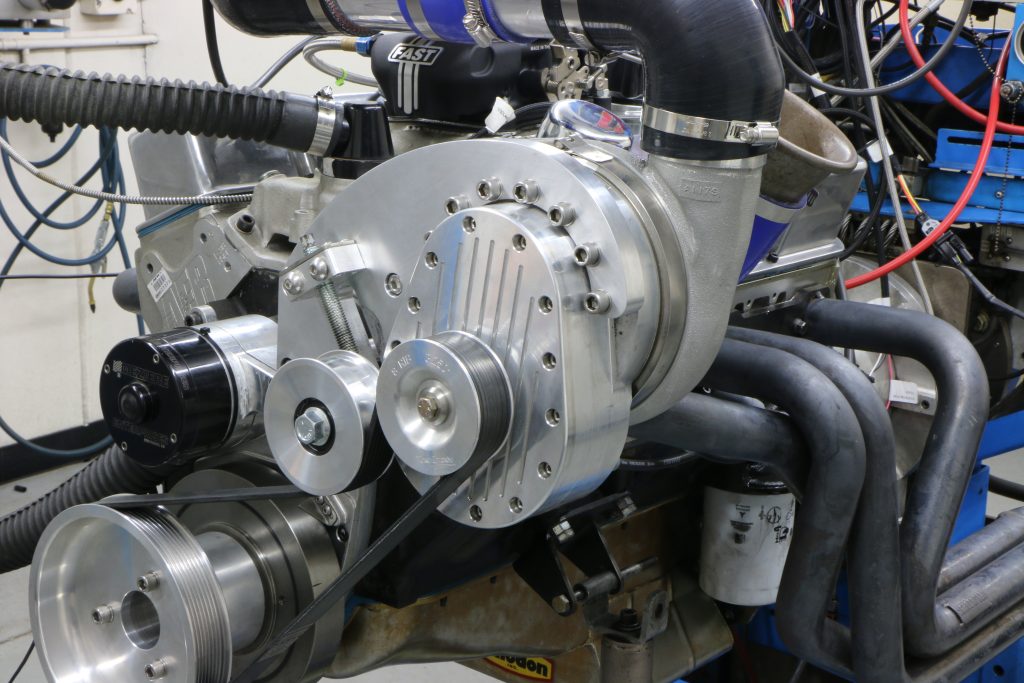
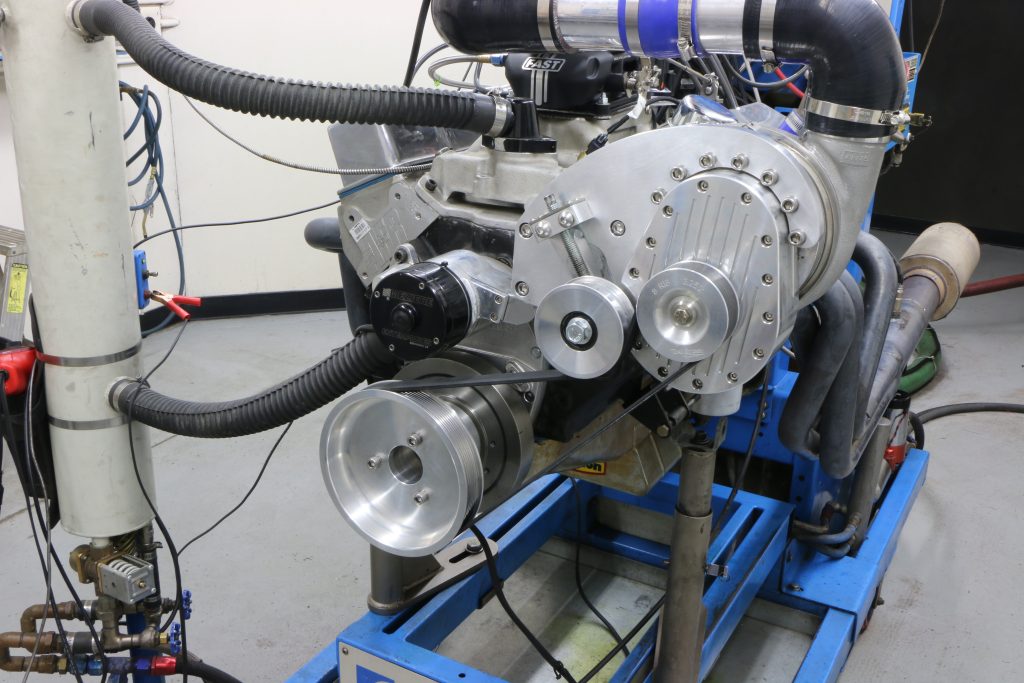
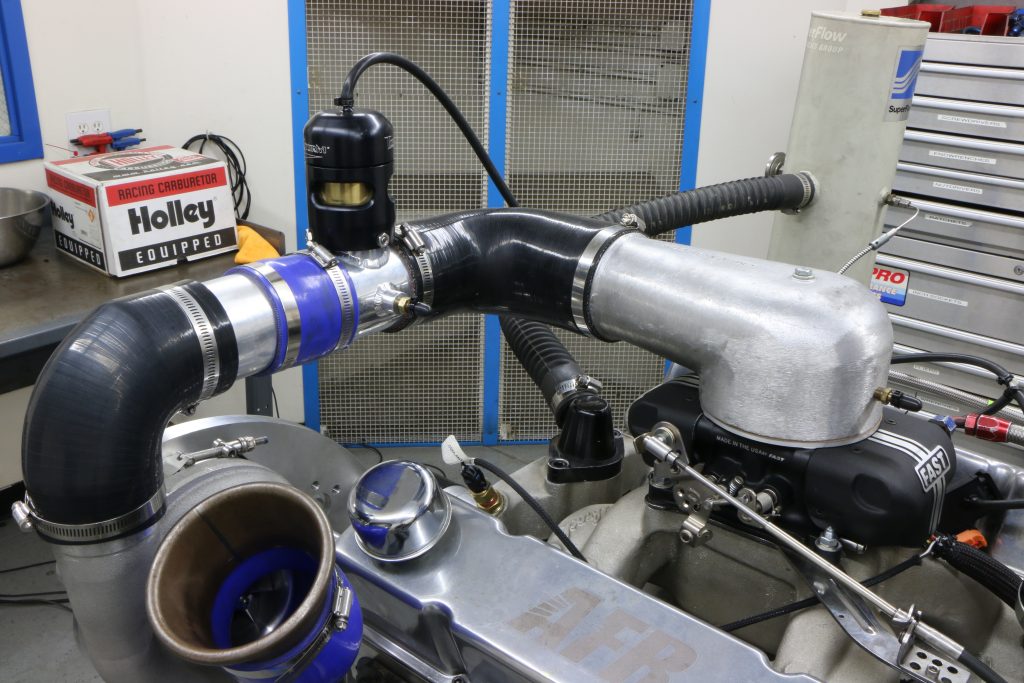
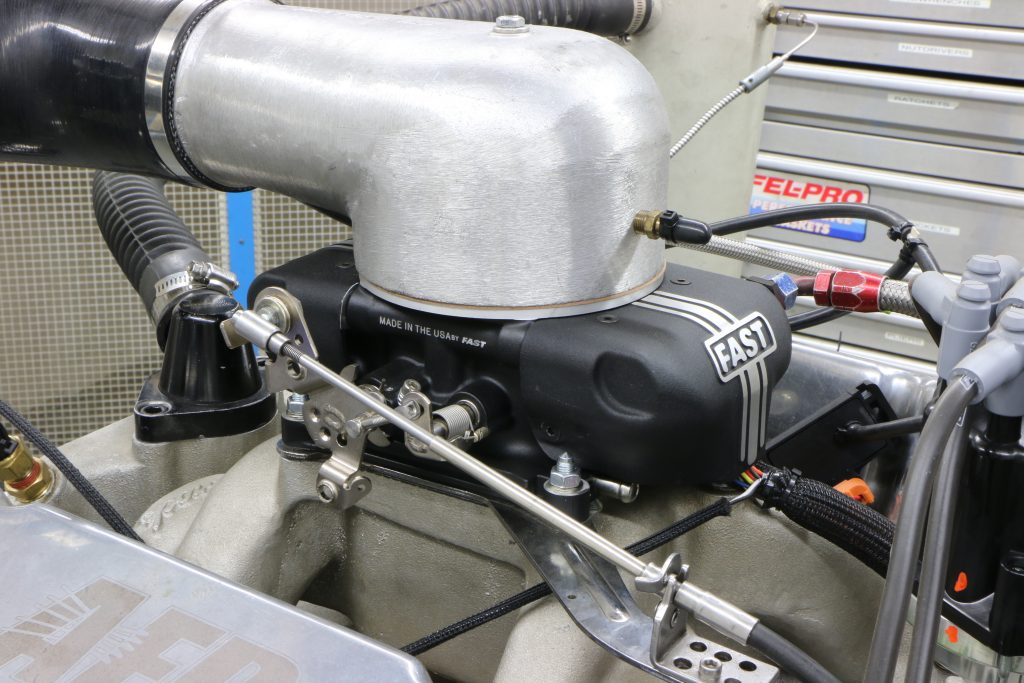
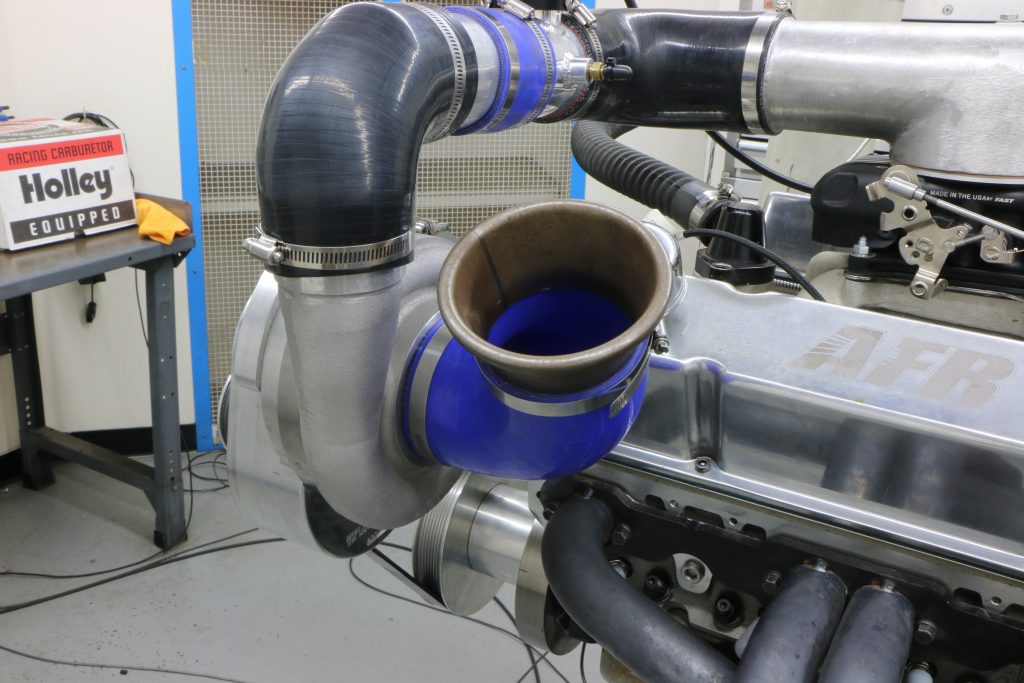
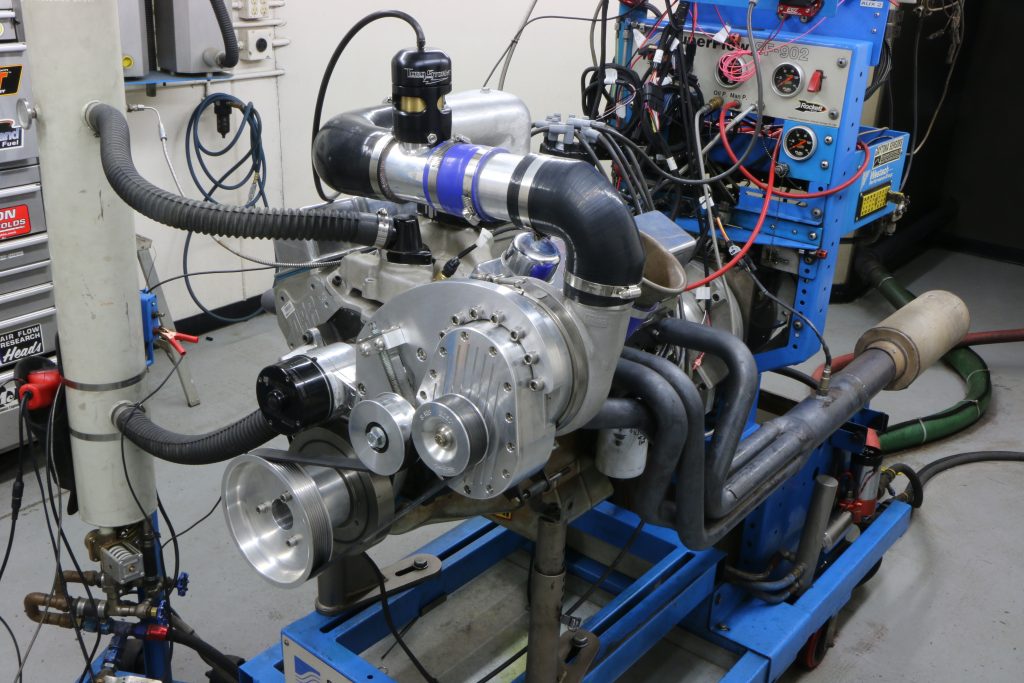
Comments