Starting in the early 1980s, the mass adoption of modern electronic fuel injection systems was a watershed moment in the history of automotive engineering. While fuel injection had certainly been around for a lot longer than that, these new computer-controlled EFI systems represented a quantum leap in both reliability and performance when compared to the outgoing carburetor—and even the earlier electronic and mechanical fuel injection systems that appeared in the decades before.
But like any nascent tech, electronic fuel injection went through a few design evolutions—and that trend continues today with the growing popularity of direct injection. So we’ll discuss and compare the three main types of fuel injection systems you’ll encounter nowadays, and give you some pros and cons of each setup.
***
The 3 Most Common Types of Fuel Injection Systems
***
Port Injection
Perhaps the most common form of fuel injection on the roads today is what’s known as port injection. This setup really hit its stride in the 1970s, and by the late 1980s it had almost entirely replaced the carburetor.
Fun Fact: The last carbureted street vehicle sold in the United States was the 1994 base model Isuzu pickup truck. The stalwart Jeep Grand Wagoneer SJ was another solid holdout, which lasted until 1991 with its carbureted 360ci AMC-era V8.
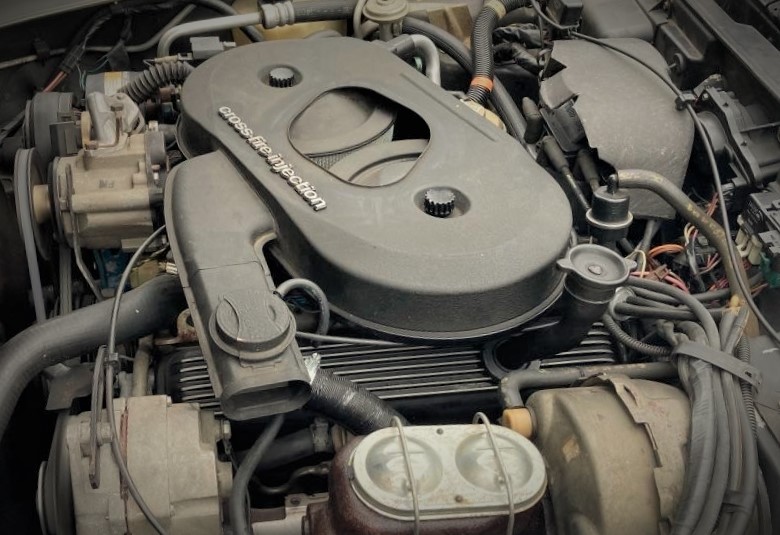
The setup puts a fuel injector into the intake plenum, immediately ahead of the intake port on the cylinder head. This allows the fuel to atomize and mix with the oxygen before it enters the combustion chamber for ignition.
Again, it didn’t take long for folks to realize the advantages of electronic fuel injection—namely in the form of cold weather startup. Gone were the days of fiddling with a choke and feathering the throttle, you could now simply turn the key and the engine would fire right up.
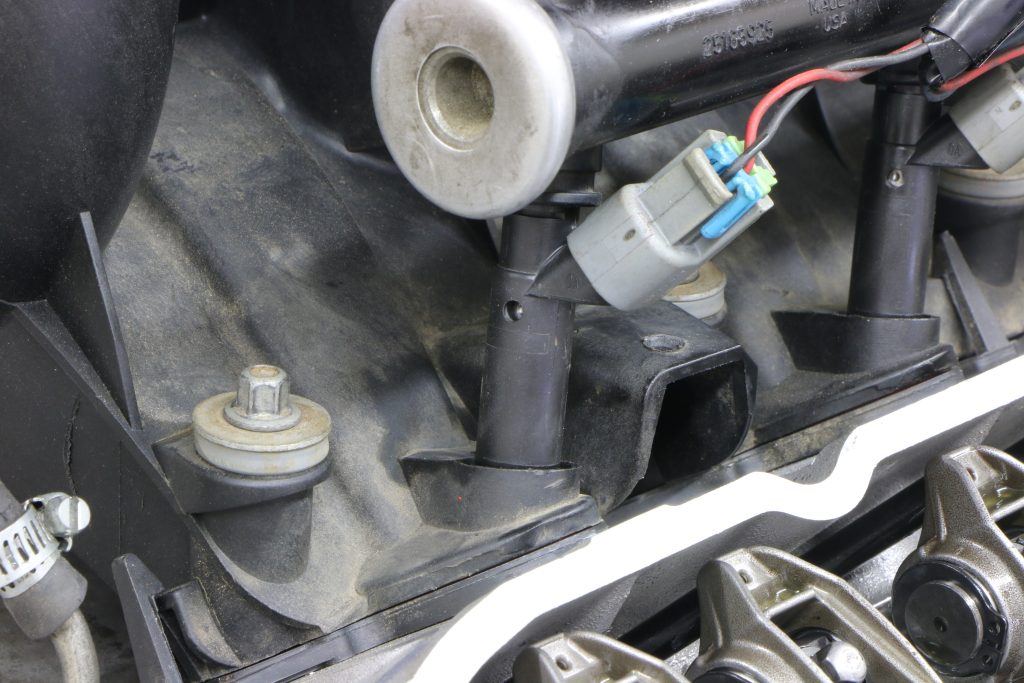
The performance world took note too.
Though there was a learning curve with early fuel mapping systems and software, engine builders soon figured out how to precisely tune fuel delivery based on engine speed.
That benefit alone unlocked a whole new level of power production capabilities.
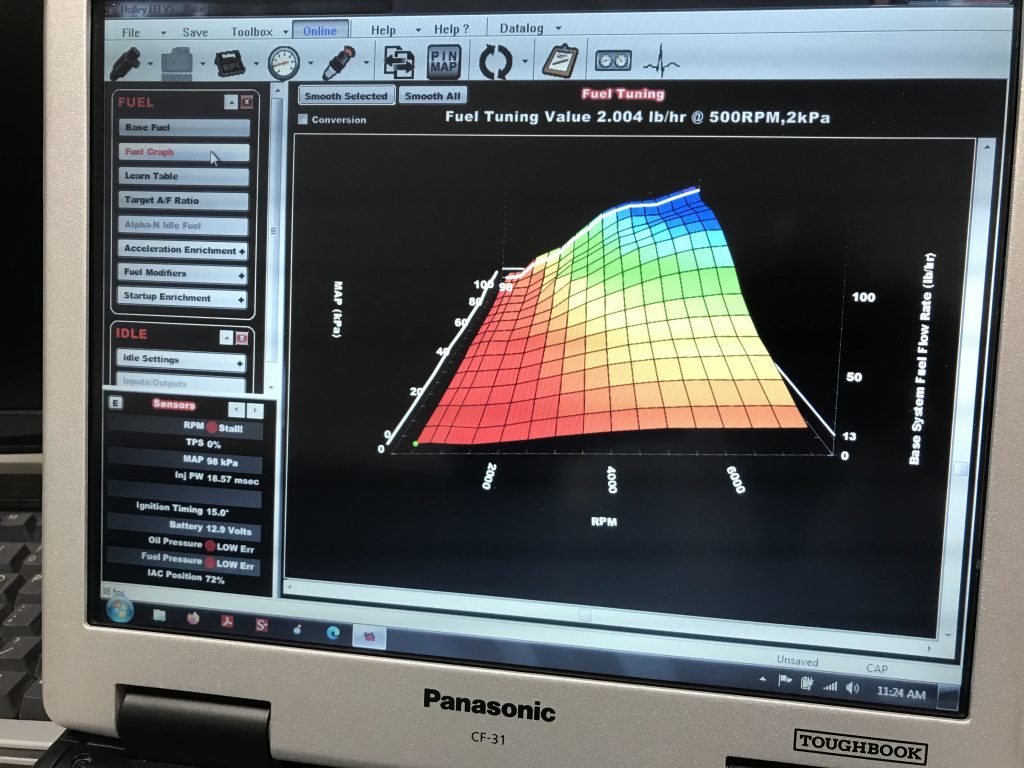
The main drawback of EFI versus a carburetor is complexity—though depending on who you ask, that’s a relative term.
Generally speaking, a carbureted fuel system was pretty straightforward, you had a fuel pump feeding a carburetor from the fuel tank, and that’s pretty much it (with the obvious caveat of carburetor jetting, float adjustment, linkages, and all that associated fun).
In contrast, a modern EFI system relies on an array of sensors and discrete fuel injectors to deliver the precise amount of fuel. This obviously requires an engine computer, tune, and stable electrical power too.
There are also two distinct ways in which these systems receive and interpret data to calculate the precise amount of fuel needed. We won’t spend much time on them now, because we’ve got a whole article on the topic here: EFI 101 – Mass Air vs. Speed Density
Direct Injection
Gasoline direct injection (GDI) has been around in various forms for decades, and several automakers have experimented with the technology over the years with some success.
But nowadays, thanks to the ever-improving reliability of direct injection, it is gaining more widespread adoption. For instance, the 2014+ Gen. 5 LT-series GM V8 features direct injection, as does the Ford Gen. 3 Coyote V8 introduced back in 2018.
Look around, and you’ll discover that many automakers have at least one direct injection engine in their lineup.
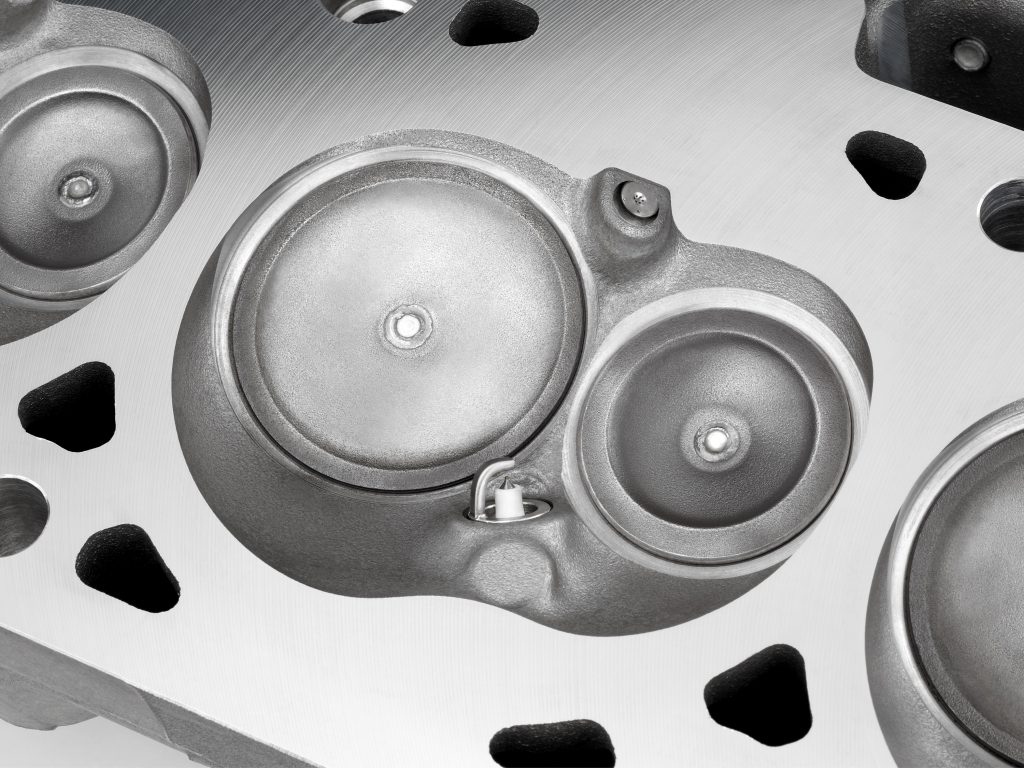
As the name implies, direct injection puts the fuel injector tip into the cylinder head, where it sprays fuel directly into combustion chamber.
Check out the picture above—that’s the underside of an aforementioned GM Gen. 5 LT V8 cylinder head. In this image you can see the spark plug tip protruding between the valves, but notice the injector nozzle on the opposite side too. While designs vary between manufacturers, this general setup means the fuel injector body itself has an extended nozzle tip, while the main body snaps into the cylinder head.
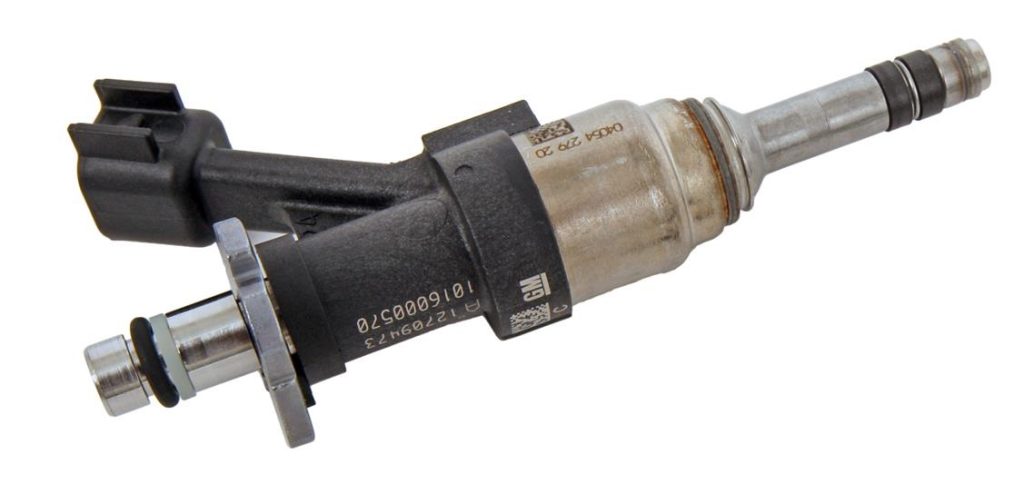
Direct injection has a handful of benefits that make it appealing for both an automaker and a performance enthusiast.
For starters, automakers like GDI because it can significantly improve tailpipe emissions, which helps hedge against ever-tightening environmental regulations. At the same time, direct injection can help fuel economy too, making it an attractive marketing feature to get buyers into dealership showrooms.
From a performance standpoint, GDI is capable of producing impressive power—and the tuner gets more precise control over the air/fuel mix. As an added bonus, spraying fuel inside the combustion chamber can reduce cylinder temperatures, which allows engine builders to run higher compression ratios and more aggressive ignition timing.
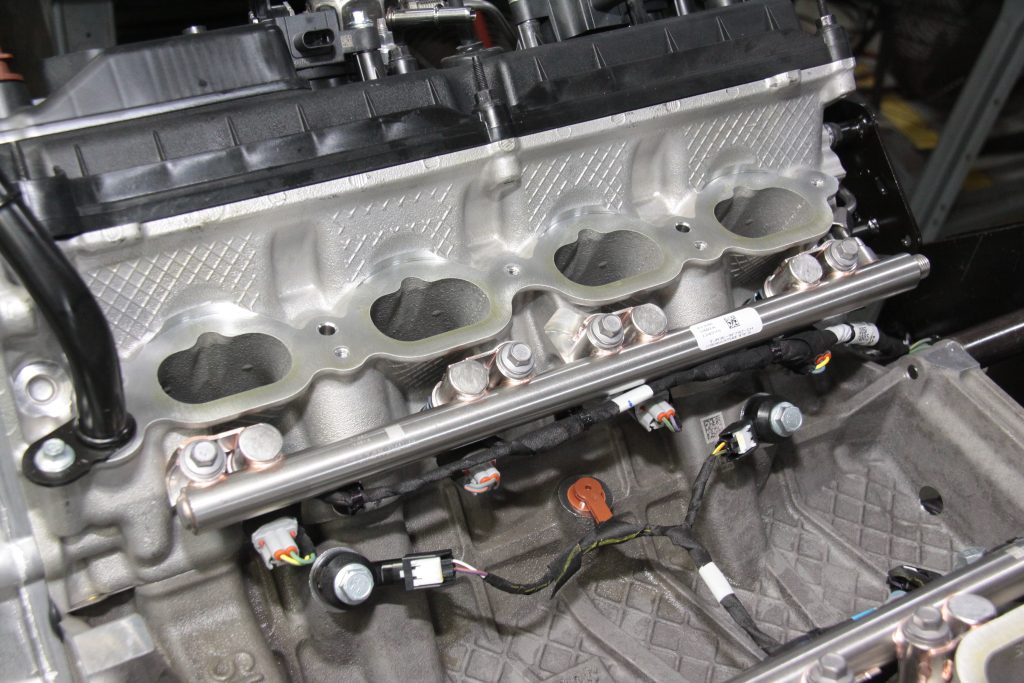
There are a handful of drawbacks with direct injection. From a technical standpoint, it requires far more fuel pressure than traditional port injection, which adds some complexity to the system.
For example, GDI engines often rely on two discrete fuel pumps. One in the tank to send fuel up to the engine at a relatively low pressure (like 40 to 60 PSI), and another pump on the engine itself to significantly increase the fuel pressure on the fuel rail. It’s not common to see a GDI fuel rail spec out to over 2,000 PSI—a pretty jaw dropping number considering a vintage carburetor engine only requires around five PSI.
Secondly, complaints of excessive carbon buildup on the injector nozzles were common during the initial wave of modern direct injection engines from the past 25 years or so. It seems that those issues are diminishing as GDI systems evolve however—pretty much what you’d expect from any tech adoption curve.
Throttle Body Injection
A while back, some genius gearhead engineers realized you could fit fuel injectors into a single module and give it the same footprint as the industry-standard Holley 4150 carburetor. Then, you can plunk the whole thing down atop the manifold on your old muscle car and enjoy the benefits of modern electronic fuel injection.
Obviously the actual EFI conversion process is a bit more involved than that, but these new throttle body setups made it easier than ever before to switch to modern electronic fuel injection. And the benefits echo that of the other two designs we’ve already discussed—tunability, fuel economy, and drivability.

Unlike direct injection, which shoots fuel directly into the combustion chamber, or port injection, which shoots fuel directly ahead of the combustion chamber intake port, a throttle body fuel injection system typically introduces fuel at the beginning of the intake plenum—very much like a traditional carburetor would.
In the systems we’re describing here, the throttle body (which controls the amount of air entering an engine) is combined with the fuel injectors in a single unit.
Many of these throttle body fuel injection systems are sold as kits, which include a proprietary controller that lets you adjust (or the ECU will automatically adjust) air and fuel ratios to ensure optimal performance—and that’s really where the magic lies.
In many ways, the throttle body itself was the easy part, performance aftermarket companies had to figure out how to create a support system that could calculate the proper amount of fuel to deliver. But figure it out they did, and now the initial ECU tuning process is often just answering a few easy questions on your specific engine.
In other words, you no longer need to be a computer engineer to get your car to run right.
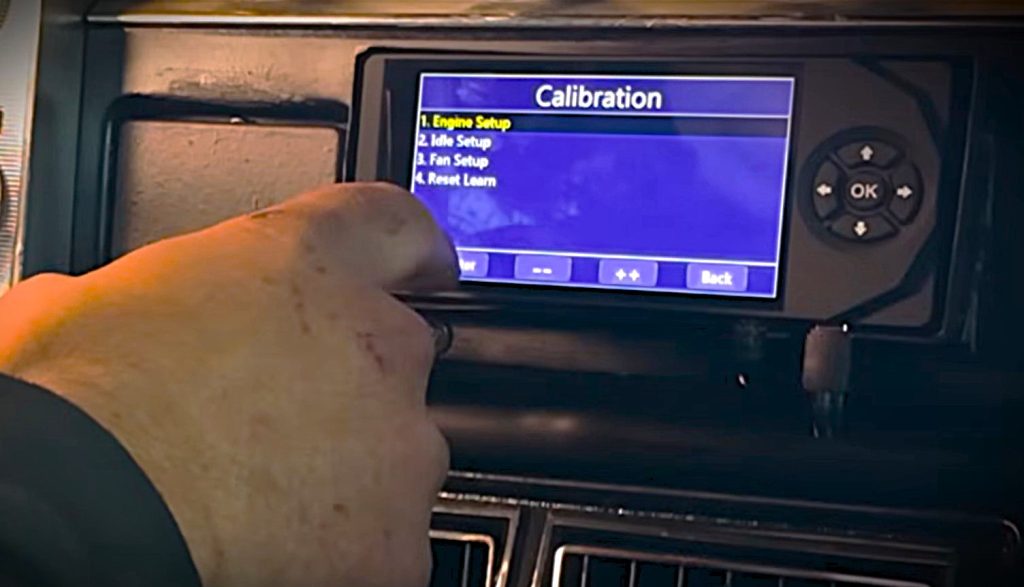
A throttle body injection conversion requires some ancillary modifications too, namely in the fuel system where you’ll need a new electronic fuel pump and some other upgrades to deliver a steady supply of high-pressure fuel, typically around 30 to 50 PSI.
If you’re thinking of switching from a carburetor to EFI, check out this video featuring the Summit Racing MAX-efi system to see what’s involved in the conversion:
Honorable Mention: Mechanical Fuel Injection
Although Chrysler introduced “Bendix Electrojector” electronic fuel injection back in 1958, let’s not overlook the fact that mechanical fuel injection has been around for quite a while too.
While plenty of other automakers experimented with mechanical fuel injection stretching back to the dawn of the automobile, our favorite example of those efforts are the “Fuelie” Chevrolets from the late 1950s and early 1960s.
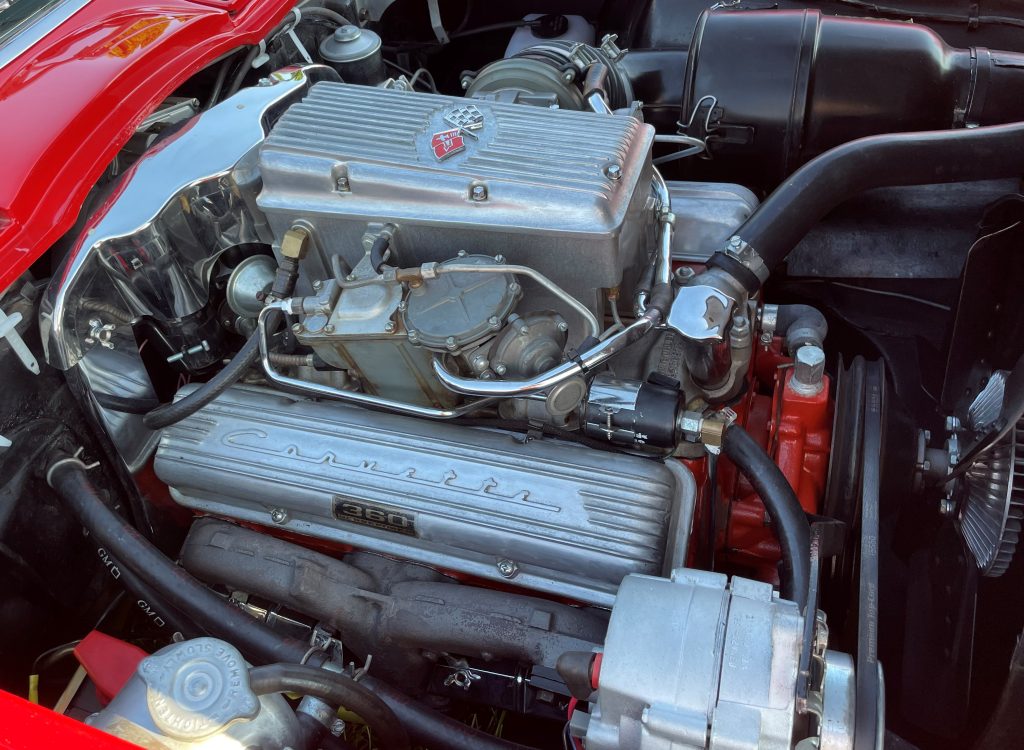
Dubbed the “Ramjet” in Chevy’s marketing literature, it was designed by GM’s Rochester Products Division and relied on a mechanical pump and vacuum to force fuel into the engine.
Chevy promoted it as a performance option and, though effective, it proved to be a tad too finicky for neighborhood mechanics and was dropped from the lineup in 1965.
Which Electronic Fuel Injection System Works Best?
There simply is no “best” answer here, because you have to consider the application.
Switching between fuel injection systems is often far too cumbersome and costly—which easily outweighs any performance benefit here. (On the other hand, there’s plenty of upside for converting from a carburetor to throttle body fuel injection.)
That said, if you’re experiencing headaches with your current setup, it’s often a result of a broken part, failed sensor, improper tune, or some other issue within the system, not the fault of the system itself.
All told, each fuel system described above has proven to be reliable, with the proper maintenance of course. From a performance perspective, fuel injection can be found in the top tiers of motorsports as well—heck, even the NHRA Pro Stock folks are using it in drag racing now!
***
Fuel injection is a complex and nuanced topic, so we have plenty of more resources to help you better understand how to service and upgrade your EFI system. Check out the links below to get started.
- 5 Things to Consider When Converting to Electronic Fuel Injection
- EFI 101: Mass Air vs. Speed Density
- How a Direct Injection Engine Affects Your Oil
- Will My New EFI System Work With My Setup?
- How Electronic Fuel Injection (EFI) Affects Cam Idle
- 3 Reasons to Consider a Self-Learning Fuel Injection System
- Fuel Pressure Ratings & How They Affect Your Engine
We also spoke with the fuel injection experts at Holley all about EFI conversions, troubleshooting, and general fuel system tech. Check out the whole interview in this episode of The OnAllCylinders Podcast:
Comments