I’m a bit of a rookie when it comes to engines and would like to ask about internal versus external balance. Isn’t engine balancing all the same? I don’t understand the difference. Can you explain this for me? Thanks.
C. P.
In both cases, yes, the engine is fully balanced. The difference is where the additional mass is placed to balance the rotating assembly.
If you look at a typical V8 crankshaft, there are counterweights placed opposite each pair of connecting rod journals except in the center. These counterweights are used, as the term implies, to counter-balance the weight of the mass of the pistons, wrist pins, rings, and the upper portion of the connecting rod. Let’s use a small block Chevy as an example.
Engine Balance Evolution
When the original small block Chevy was first designed, it was only 265 cubic inches using a 3.50 inch bore and a short 3.00 inch stroke. Moving forward 15 years to 1970, the 350 Chevy engine expanded the bore to 4.00 inches and the stroke to 3.48 inches. All this weight was contained within the crankcase, except for a small counterweight located on the crankshaft flexplate/flywheel mounting flange.
This package was later termed an internally balanced engine.
Both added bore and stroke dimensions required an increase in the size and length (from crank centerline) of the crankshaft counterweights. Also in 1970, Chevy introduced the 400 cubic inch small-block with a much larger 4.125 inch bore and an even longer 3.75 inch stroke. There was not room inside the crankcase area between the oil pan rails to accommodate a larger counterweight so Chevy opted to add offset weight to both the harmonic balancer in the front and a similar offset weight to the flywheel/flexplate in the rear.
The 400ci small block Chevy became what later became known as an externally balanced engine.
The same type of situation occurred with the 454 compared to the 396/402/427 big block Chevys. The larger bore and longer stroke on the 454 demanded an external balance on the front and rear of the engine to properly balance the additional forces created by the larger mass located farther from the crank centerline .
Just to make this a little more confusing, when Chevrolet converted to a one-piece rear main seal on the traditional small block Chevy, the crankshaft flange also changed. This required a small weight be externally mounted on the flywheel / flexplate on these engines to compensate for eliminating the small weight on the end of the two-piece rear main seal crankshafts. The newer one-piece rear main seal engines are still considered internally balanced engines, but do require the proper offset weight added to the flywheel/flexplate.
It’s confusing and seemingly a contradiction in terms—but necessary.
This external balance is not limited to Chevrolet engines. Ford, for example, opted to externally balance their small-block Ford engines from the very beginning with the 221ci small block in the early 1960’s. And because Ford is famous for changing things, this external weight—expressed as 28.2 ounces of weight positioned one inch from centerline or 28.2 ounce-inches (oz.-in.)—changed in the 1980 and later V8 small-block engines to 50 oz.-in. So haphazardly swapping parts between these engines will result in a very badly vibrating rotating assembly.
Internal vs. External Engine Balance, Which is Better?
So the next question is whether internal or external balance is a better approach. The general consensus is that for a street-driven engine that sees normal duty there is no real difference in terms of accuracy of balance at speeds below 6,000 rpm. For a normal engine rebuild, it’s a good idea to have the entire assembly balanced to accommodate larger pistons, for example.
If the engine is internally balanced, a good machine shop will want your harmonic balancer and flexplate/flywheel to use when balancing to ensure that the entire assembly still works within the balance parameters. The same must be done when the engine is externally balanced since those components are critical.
For racing or high-rpm street engines, it is generally acknowledged that an internally balanced engine is preferable because those external weights at speed tend to generate significant forces that, while “balanced” still function like a rock on a long string creating a large force that can create main bearing wear issues at high rpm.
But for a normal street performance engine, this is not enough to warrant the additional cost involved to convert a factory externally balanced engine to internal balance. But in certain cases you can have a choice.
For example, the very popular 383ci small-block Chevy stroker combination was originally conceived using a 400ci small block 3.75 inch stroke crank in a 350 block. The main journals on the 400 crank were machined down to the 350 main size but the external balance was retained which meant you had to use a 400ci front balancer and flywheel/flexplate that used the 400’s external balance weights.
But now you can purchase a 383ci stroker rotating package from places like SummitRacing.com that offer an internally balanced crankshaft that has added the additional counterweights that will still fit inside the stock 350’s pan rails and crankcase.
There’s much more to this story but this should give you an idea of the basics of the forces generated with the rotating assembly in a V8 engine. As you might imagine, once you start to spin the engine at extreme engine speeds above 7,000 to 8,000 rpm—different forces begin to happen that affect the placement of the counterweights and what those forces do to main bearings. That’s probably fodder for a PhD dissertation and frankly beyond our knowledge base—but we know that it happens!
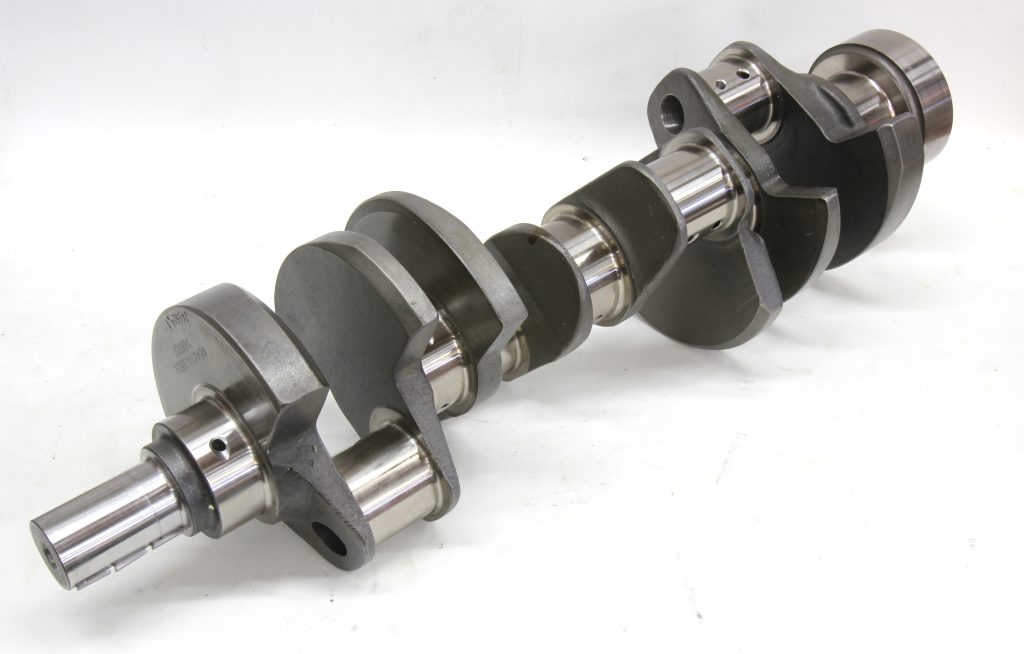
Comments