Is there any extra power to be had from removing the accessories or swapping out a heavy flywheel?
The data we have from this series of tests is actually broken down into two distinct types: parasitic loss and moment of inertia—through there may be some overlap.

Test Number One: Accessory Drive
For test number one, we decided to illustrate the power consumed (and therefore gained when removed) by the accessories. It should come as no surprise that running convenience items such as air conditioning and power steering both cost power. In effect, it takes power to drive what are essentially pumps.
The same can be said of the water pump (after all, it’s right there in the name) and alternator. This is especially true if an electrical load is placed on the alternator from high usage items like an electric fuel pump and/or thumpin’ stereo system.
For our test, we did not impose a load on the alternator, we simply free spun it, but the water pump and power steering pump were both pumping at full capacity, though the pump was not hooked to a steering rack. The test procedure was to first run the (stock truck) accessories, then replace them all with a Meziere electric water pump. In essence, we were outsourcing the power to drive the pump (from the dyno batteries), thus eliminating any losses.
The question before us was, how much power was it worth? A secondary question might also be is this something you could actually employ at the track?
Test Number Two: Flywheel
Instead of driving pumps and an alternator, test number two involved comparing a heavy flywheel assembly to a much lighter combo. The reason for the combo description is that, on the dyno, the flywheel was combined with a drive plate. The splined drive plate hub was used to transfer the power from the motor to the input shaft of the dyno (similar to the input shaft on a transmission).
The question before us was does the heavy steel flywheel and matching steel drive plate hurt power production?
To find out, we compared these hefty components to much lighter substitutes. Unfortunately, we didn’t have access to a lightweight, aluminum flywheel to test, so we did the next best thing. As luck would have it, all the junkyard LS motors we get come with something we usually just throw away. Since 99.5% of truck LS motors were attached to automatic transmissions, the motors all came with flexplates.
Lucky for us, we could easily attach a drive plate to the significantly lighter flexplate. For this test, the flex plate was merely doubling as a light flywheel, so save the comments about heavy torque converters (they don’t apply here).
After combining the 5.5 pound flex plate with the 11.2 pound aluminum drive plate, the combo tipped the (shipping) scale at just 16.7 pounds. This compares to 45 pounds for the 24 pound steel flywheel and 21 pound steel drive plate. All told, the changeover dropped 28.3 pounds, all of it reciprocating weight. It is also worth mentioning the O.D. of the aluminum drive plate measured 11.375 inches, while the steel drive plate checked in at 13.25 inches.
In the basic Moment of Inertia calculation (MOI = Mass x Radius Squared), the distance from the centerline being squared means changes in size can have more of an effect than changes in weight (mass). The aluminum drive plate changed both!
The Test Motor
To put these things to the test, we needed a suitable test motor. To that end, we reached for our 4.8L junkyard warrior. The iron block LR4 had started out life with a damaged cam, lifter, and rocker (let’s throw in a couple of pushrods just for good measure), but, was brought back to full (near that at any rate) health with some spare components left over from fellow junkyard warriors.
For this test, the LR4 was configured with a Truck Norris NSR cam from Brian Tooley Racing, a set of 1-7/8 inch, long-tube headers and Magnaflow mufflers, then finished off with a Hi-Ram Holley intake manifold. You might question the Hi-Ram (we would) on this application, but the motor was set to receive a (what else) junkyard Eaton M90 blower that required use of a Hi Ram. We figured why not get all the testing we can while the motor was up on the dyno, so the little BTR NSR cam got a big Holley intake. Holley also supplied the HP engine management system, while the 80 pound injectors came from the guys at Accel.
You can read all about that 4.8L Blower test in this article.
All testing on the accessories and flywheels was run on E85 fuel—again, we wanted to start with the same fuel we would be running the blower with. This combo did not need E85 fuel, though it did make a few extra horsepower when we swapped over from the 91 pump gas to the pump E85.
Test Results
The first order of business was to configure the 4.8L with the heavy flywheel, heavy drive plate, and (nearly) full accessories. Doing this allowed us to go step by step and minimize swap time and duplication.
Run first with the factory water pump, power steering pump and alternator (just free spinning), the 4.8L produced 385 hp at 6,600 rpm and 336 lb.-ft. of torque at 5,300 rpm.
The short(er) runner Hi-Ram intake allowed the mild BTR-cammed 4.8L to make power fairly high in the rev range. After running the accessories, they were replaced by a simple Meziere electric water pump.
The result of the removal of the accessories increased the power output from 385 hp and 336 lb.-ft. of torque to 404 hp at 6,700 rpm and 348 lb.-ft. of torque.
Now it was time to swap out the heavy flywheel and drive plate, since this run had also established a baseline for the flywheel test. After replacing the heavy steel flywheel and drive plate with the light flexplate and aluminum drive plate, the peak numbers jumped once again, this time to 411 hp at 6,800 rpm and 355 lb.-ft. of torque at 5,300 rpm.
The big question here is (unlike the accessories), did the flywheel test actually improve power, since gains only showed up under an acceleration (and not stationary load) test? Also, is a heavy flywheel sometimes beneficial to help launch a vehicle, since the rpm applied on the line was not yet being used to accelerate the vehicle?
Feel free to chime in or go check out the full video on the Richard Holdener YouTube Channel.







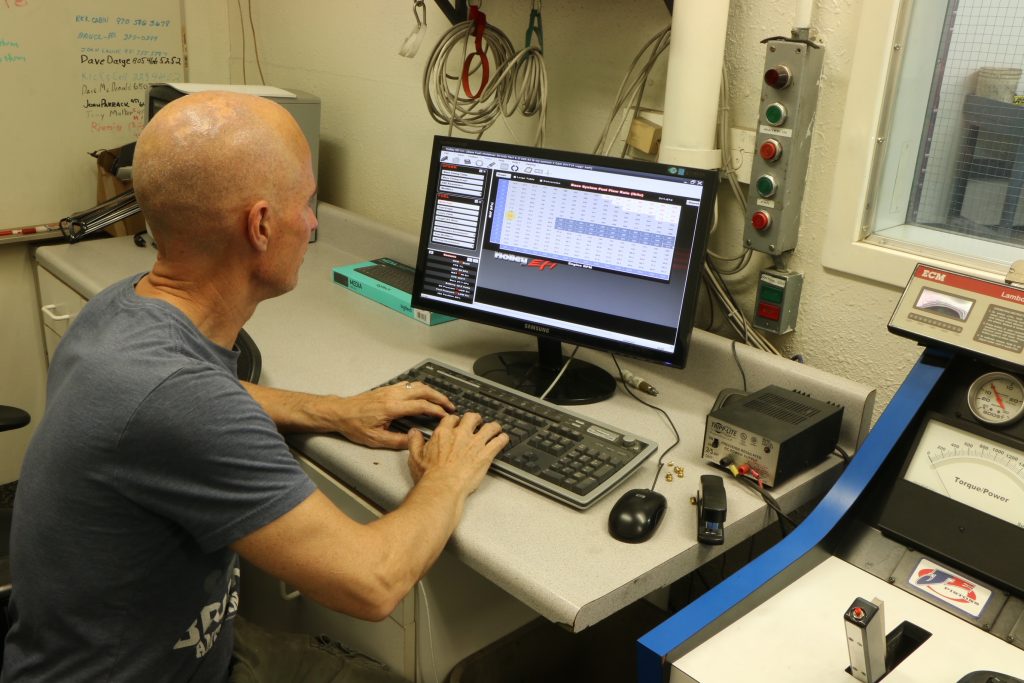










Hey Richard, a little off topic but I was testing a 351 Cleveland at home on a run stand and with a flex plate, the engine would not idle if you revved it and let it come back to idle and it would just shut down. My thoughts is that there was not enough inertia to keep the engine running. I then fitted a flywheel and it idled nicely, it was smooth and every time it just started and idled nice.
Regards
Mike Barker