Based on one of your answers in an earlier tech column, I found myself asking a lot of the same questions about running solid lifters on hydraulic roller camshaft after watching an episode of Engine Masters. I’ve seen a lot of conflicting info out there; which just adds to the confusion and leads to more questions. Is there an easy answer to this question?
J.S.
This question comes up occasionally when discussing hydraulic versus solid lifters in both flat tappet and roller applications. We’ll deal with this question from the roller lifter standpoint because that was the focus of your question.
The whole idea behind using a hydraulic lifter is to account for expansion of the engine as it warms up. This is why a mechanical lifter camshaft uses a given amount of lash or clearance between the rocker and valve tip since the engine will expand as it reaches operating temperature. We’ve included a chart that lists the difference in lash settings cold versus hot for a mechanical lifter camshaft.
Can You Run a Mechanical Roller Lifter on a Hydraulic Roller Camshaft?
So the question is whether you can run a mechanical roller lifter on a hydraulic roller camshaft. The short answer is yes—but there are many aspects to this question that need to be addressed in order to more accurately answer the question.
It’s not as simple as it may seem.
First of all, the only reason you might want to attempt this is because you feel your current hydraulic roller lifter is not doing its job. This may or may not be the fault of the lifter. The first question to address would be if the engine is experiencing loss of control—sometimes called valve float. It’s very possible that another component is exerting an unwarranted load on the system where the springs can no longer maintain the lifter in contact with the lobe.
This could be the result of inadequate valve spring pressure with weak valve springs or it could be that the overall weight of the valvetrain is excessive where the spring just doesn’t have sufficient capacity to control the system. Rocker ratio is another consideration because increasing ratio (from 1.5:1 to 1.6:1 for example) accelerates the valve much faster which can cause valve float.
Sometimes issues have to do with the lifter itself. Hydraulic lifters contain an area below the lifter piston that is filled with pressurized engine oil. Invariably, there will be a small amount of entrained air in the oil below the piston. Since air is compressible, this often results in a small loss of valve lift. This often creates a slight loss of power especially at higher engine speeds.
The most common hydraulic lifter issue is when there is a loss of valve control. This loss of control is often assumed to be lofting of the lifter off the nose of the lobe. This lofting creates clearance in the system and oil pressure will instantly push the lifter piston to the top of its travel inside the lifter. This causes the lifter to hold the valve open with an obvious loss of power.
This is referred to as the lifters “pumping up.”
The cure for this isn’t to change lifters but rather to modify the valvetrain to eliminate this loss of control.
Another loss of control is where the valve bounces off the seat on the closing side. This is usually attributed to low spring rate but can also be the result of an aggressive lobe closing rate perhaps exaggerated by an excessive rocker ratio.
Things to Consider Before Converting
If you are adamant about converting to a mechanical roller lifter on a hydraulic roller cam profile, there are some serous considerations that must be addressed. Mechanical roller lobes are designed with a clearance ramp. This is a short section in the lobe where the lifter is gently moved off the base circle to close up the designed-in lash. Hydraulic roller lobes do not have a clearance ramp so you must add a small amount of lash to the system. But this presents a problem.
Right off the base circle, hydraulic roller lobes immediately accelerate the lift curve while the mechanical roller employs that gentle clearance ramp to take up the lash. With lash on a hydraulic lobe, this means the mechanical roller lifter on a hydraulic roller cam will accelerate the lifter quickly yet there still needs to be lash in order to prevent holding all the valves open when the engine is cold. If this happens, the engine won’t start—or if it does, it may burn the exhaust valves because they are not fully seated and do not cool down.
One trick to establishing all of this is to set the lash cold at around 0.004 inch and then measure the lash again after engine is fully up to temperature. This will show you exactly how much your specific engine expands and how much lash you have when the engine is hot. Then too, you should measure again when the engine cools to ensure that it still has 0.004 inch lash. This may require several tests to ensure the numbers are consistent.
This is somewhat of a challenge to run this tight a lash because it’s no picnic to try to insert an extremely thin 0.004 inch feeler gauge between the roller and the valve tip. We won’t kid you—this is really difficult to do accurately because the feeler gauge is ridiculously thin and won’t want to slide in between the rocker and the valve tip.
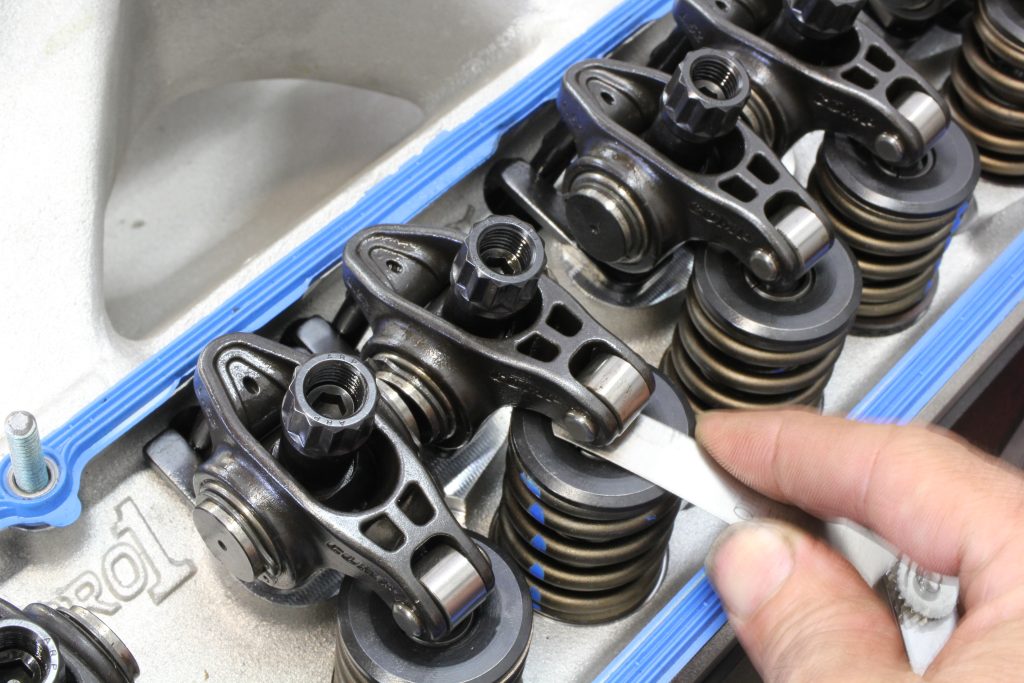
Why Do It?
This conversion from hydraulic to mechanical can make more power over a normal full travel hydraulic lifter. But this power improvement is nowhere close to 10 or 15 hp. It will likely be a single digit improvement.
If we did a comparison of a mechanical lifter to a high quality hydraulic like a Morel, Comp’s new cartridge technology Evolution hydraulic lifter or perhaps an Isky or a Johnson version, the difference in horsepower will probably be even less.
So then the question becomes why would you want to go through all this hassle just to pick up a tiny increment of power? One reason might be that you have to run a hydraulic lifter cam required for class rules. Even then, it might be smarter to instead use a high quality limited travel hydraulic roller lifter. This requires an explanation as to what a limited travel lifter is and why it can be a wise choice.
What is a Limited Travel Lifter?
A typical hydraulic roller lifter will offer something in the neighborhood of 0.100 to 0.120 inch of internal piston travel. This is the distance the piston inside the lifter body can move between the bottom and top of its bore. All hydraulic roller lifters employ what is called preload where the piston is pushed downward from its top travel position against the top spring clip. This preload is generally around 0.050 inch and is designed to account for expansion as the engine achieves operating temperature.
A reduced travel lifter cuts the piston travel inside the lifter to roughly 0.050 inch. This reduces the height of the oil chamber underneath the piston which reduces the amount of air entrained in the chamber so lift loss is minimal. This limited travel lifter also requires less preload—roughly around 0.015 to 0.020 inch, which is very tight. This also helps if the lifter does experience loss of control as it only holds the valve open the amount of the preload. Ideally, the valvetrain will be stable and this loss of control will never occur.
We queried Bob Cook of John Callies, Inc. about short travel lifters and he said that these are really designed for competition where the rules require a hydraulic roller tappet. He says Callies does not recommend these lifters for street use because they are really not designed to operate like a true hydraulic lifter. The travel is short enough that by the time the engine expands to operating temperature, nearly all the distance below the piston is taken up—turning the lifter effectively into a mechanical lifter.
The issue with converting to a mechanical roller lifer is that the amount of lash is really determined by the design of the lobe. Very fast accelerating lobes will be extremely difficult to set lash. You will need to set the lash nearly to zero cold in order to have some minor amount of lash under normal operating temperatures.
As mentioned, this will make the valvetrain noisy. Cook says that if your valvetrain is noisy, the lash is improperly set with excessive lash.
“If your engine is noisy, the lash is wrong” is how he put it.
As an example, he told us about a customer with an all-aluminum LS3 with cold lash set at very nearly zero and with a low-lash or tight-lash cam lobe. When the all-aluminum engine was fully at temperature, it would have between 0.012 and 0.014 inch of lash when the cold lash was near zero.
Ultimately, the answer to your question isn’t really about the lifter but rather about the aggressiveness of the hydraulic roller lobe design.
But if you are serious for a street engine, it would be smarter to just choose a tight lash solid roller cam profile that fits your parameters and then run a matching solid roller lifter. This eliminates the variable of the hydraulic cam not having a clearance ramp.
Crane Valve Lash Chart
Engine Material | Lash Adjustment |
---|---|
All Iron | Add 0.002” |
Iron w/Alum. Heads | Subtract 0.006” |
All Aluminum | Subtract 0.012” |
This chart shows the difference for setting lash cold versus a hot spec. For example, if you have a 0.020 inch hot lash spec for your camshaft, you can set the lash cold on an iron block with aluminum heads engine by setting the cold lash at 0.014 inch. |
Comments