I’m still buying parts to assemble a 355-cubic-inch small block Chevy for my ’55 Chevy. My buddy was over this past weekend and told me that I should make sure to port-match the intake manifold to the heads. Is that something I should do? He says he read where that could be worth 10 horsepower or more. If that’s true, then I will certainly make the effort, but I thought I’d check that out before I do the work. Thanks
B.D.
Jeff Smith: Port matching the interface between the intake manifold and the intake port opening on the cylinder head is one of those classic mod stories that have appeared probably dozens of times in various magazines.
On the surface, this would appear to be an important part of any high performance engine build. This would seem especially important when the intake port opening is smaller than the manifold. This is even supported by flow bench testing where any obstruction or sharp edge at the port inlet results in major flow losses.
But this is one situation where the flow bench can lie to you.
I can give you a real-world example. We were testing intake manifolds at Westech for a story not long ago and one prototype manifold had a larger port exit than the intake port opening in the heads. This created a protruding ledge that was roughly 1/8-inch (0.125-inch) around the entire circumference of the port. The manifold designer was hesitant to test the manifold because he had experienced a large flow loss whenever there was a port obstruction like this. Both dyno operator Steve Brule and I offered that this was something that he didn’t have to worry about. The designer disagreed and that discussion meant we had to run the test. In this particular situation, we were using a 450-horsepower small block Chevy.
Our manifold designer buddy (whose name we will withhold to protect the innocent!), was convinced we’d see at least a 5-horsepower loss in power. Conversely, our position was that the engine wouldn’t know the difference and that the power would be the same. Or, perhaps the power might improve if this latest manifold was indeed better relative to the previous manifold with a smaller port opening. We quickly ran the test and the power curves for the two manifolds overlapped perfectly. The power was exactly the same for both manifolds with no difference in either torque or horsepower.
Here’s the explanation. If we were to plot the speed of the air travelling down an intake port, the highest speed would be in the center of the port. As the air moves closer to the port wall, the velocity begins to slow until it reaches the port wall where the speed is zero. The friction from the interface between the air and the port walls is what contributes to this effect. This is sometimes called the boundary layer effect. But you don’t have to take our word for this. We’ve included an image straight from NASA on how this works.
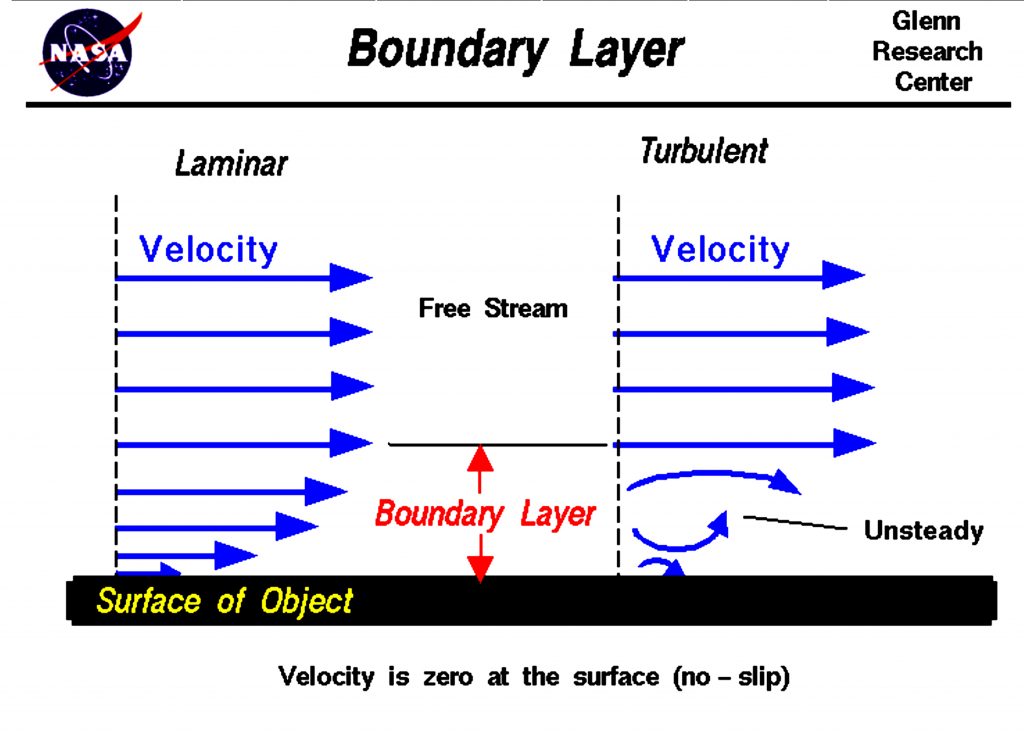
This NASA drawing illustrates how air velocity begins to taper off as the air gets closer to the surface of the port.
If the air is travelling very slowly at the walls of the manifold/intake port, it should be easy to see that even a 1/8-inch of ledge protruding into the port will have a minimal effect on port flow. The opposite is also true where the intake port is larger. The effect is essentially inconsequential. Would an NHRA Pro Stock or NASCAR engine builder allow this to happen? The answer is no, but for your average street engine builder, it’s an area of minimal concern.
This sounds crazy but we’ve seen big block Chevys where an oval port manifold was used on an engine with rectangle port heads and it seemed to run just fine. We’re not recommending that you do this, but in the case of an emergency, it certainly can be done.
One reason this port-matching modification continues to be popular is because the openings are easy to access. But if you’d rather maximize your time and effort, the smarter move is to spend all of your porting concern on the area within roughly ¾-inch on either side of the valve seat. That’s where a little bit of pocket porting work and radius work can have a measurable effect on power – if performed correctly. To illustrate this, we ran a test many years ago on a set of iron 1.94-/1.50-inch valve small block Chevy heads. We spent 8 hours doing pocket work on both the intake and exhaust ports just around the valve seat area. This was worth a solid 25 horsepower on a 350 horsepower engine. Not bad considering we did not increase the valve size.
So if you are going to spend some time on your cylinder heads, learn the techniques for pocket porting and spend your time there.
I would say that this is something that will worry you to know end (port matching), Say you go in and do the pocket work and not the ports. You know the feeling, why didn’t I do it? I was right there. WHY? WHY? WHY? Oh yeah I read an article that said it wasn’t really needed. Just do the pockets.
So you didnt match port the intake to the head. And didnt see a difference. (A decrease would have been expected)
Ok
But what if you had? (Could have resulted in an increase?)
when ya do a comparison like this you MUST cover all aspects. I agree that a 3rd run should have been made with matched ports. Now that run would have been the golden one info wise
The NASA reference here is a little misleading in the context of the subject. What the illustration fails to mention, intentionally or not, is the fact that a smooth surface, like that of a smooth polished intake, is where a boundary layer forms. Air gets lazy on a smooth surface (think of the water “cruzing” across your car windows while driving in the rain). This “boundary layer effect” is in effect at approximately 50-300 mph [I have witnessed this in jet planes during take off in the rain and fog]) after which the layer of low pressure is squeezed shut from the surrounding pressure. This is why it’s never good to port AND polish your heads (reduces midrange power [air in the ports can travel upwards of 400 miles per hour]). So the boundary layer you reference (especially if the heads have been done right) isn’t necessarily there. And turbulence, created by sharp edges (via a lack of port matching) and other uneven surfaces in the ports, can create unnecessary turbulence and impede the flow of air. (P.S. A dimpled surface will disrupt the boundary layer reducing turbulence and maximizing airflow.)
The important point is that air velocity at and near the wall is zero or near zero. Sure a slight ledge will create a flow loss, but the point is that it’s negligble when there are so many other restrictions that cost far more in terms of airflow. Whether there is velocity 1mm off the port wall isn’t important – I was only using this illustration as a way of explaining what is really happening inside the port. Highest velocity will always be at or near the center of the port – assuming no change in direction of the airflow.
I have been doing “alot” of reading on port matching, throttle body and diameter in reference to a my harley 2003 softail tc88 with all the bells and whistles on the rebuild. But I did not do port matching.
Your article is informative and will help me in future decisions.
Big thanks
Hi Jeff I have ported and polished my 3.0 liter Ford motor. Just wondering if polishing the chamber area to get rid of the rough finish will reduce the compression enough to affect engine performance. Just trying to reduce areas that could collect Carson deposit s
Mercruier marine built peanut port engines with rectangle port intake manifolds and they ran very well.
I guess it depends on if you believe the intake port sucks or the intake manifold pushes (atmospheric pressure). Most of us engine builders believe intake ports suck!!!
Dennis,
The physical reality is that intake ports do not suck. It’s a simple matter of pressure differential. When the intake valve opens and the piston is moving downward, this creates pressure that is much lower than atmospheric pressure because of the drastic increase in cylinder volume. This atmospheric pressure then pushes the air and fuel into the cylinder past the intake valve. It’s a simple process of pressure moving air from where the pressure is high to where it is low.
if the port a matched and larger, would that make the boundary level farther away from the center? increasing the flow at the center.
I have had guys sware by polishing the intake ports. But I Leave a surface of 80 grit tutsie roll, if you want more flow and have lots of time give port walls gulf ball dimple and you will gain as much as 10 present
This is true to an extent. A comment above is what I was think as well…..if it had been port matched, would it have gained as you used a “better” intake…..?
When head porters put heads on the bench….they use a string of clay around the port to eliminate turbulence……ok, so a small port condition doesn’t have a clay leader…..so it would stand to reason the airflow is somewhat disruptive……..
Also……in my life I have only seen one flow test where an intake is bolted to a head to flow test it…….nobody does this as far as I know and I often wonder why……it would be interesting to see real numbers matched vs. not-matched with an intake bolted to the head and flowed…….
But, you are 100% correct that the magic happens in the bowl area……..so if you are a bohemian garage guy like me, it is fun to take old castings that are in perfect shape and port them……..it is surprising how well they work afterward……but if they need any machining, just punt and buy modern stuff!!!!
This topic is very interesting to me as I have hard-to-find 1964 GTO heads that are unfortunately ported OVERLY large on the exhaust; the port exits are so large that production headers will not seal. Instead I have cast manifolds which will seal using thick gaskets. Thus I have the same situation described here but at the exhaust side. The results you guys saw at Westech seemingly support my hope that the stepped edge wouldn’t kill horsepower.
I’m a retired Research Engineer who made my living doing thermal-fluid simulations using Computational Fluid Dynamics (CFD). In such a flow as described in this discussion (a.k.a., Flow over a Forward Facing Step), the edge presented to the flow by the smaller openings creates a stagnation zone (the flow stops locally) at the stepped edge, and creates a sort of “sloped dam” in the flow over which a boundary layer forms, and the flow continues over the dam. This flow situation that I have tried to describe here is illustrated by example from the article cited below (I wasn’t able to cut and paste the image here…).
Thanks so much for your enlightening writeup!
Ref: Figure 2 in “POD-Based Data Mining of Turbulent Flows in Front of and on Top of Smooth and Roughness-Resolved Forward-Facing Steps.” January 2019, IEEE Access PP(99):1-1