What exactly is vapor lock? The weather is warming up now and last summer I had trouble with my small block Nova dying a various times when he engine ran a little hot. Is there anything I can do to prevent this?
R.S.
Jeff Smith: That’s a really good question that doesn’t really have a simple answer. There are multiple causes of vapor lock and just about as many hand-me-down cures like water-soaked clothes hangers. We prefer to be a bit more scientific.
Vapor lock is a condition that results when gasoline is heated, which causes it to vaporize. This problem is most commonly associated with carbureted engines. Once the fuel changes state from a liquid to a gas, a fuel pump can no longer move the fuel, which causes the engine to hesitate and stall. The engine will also be difficult to restart until the fuel has cooled. This is because engine-driven fuel pumps must pull fuel all the way from the rear of the car up to the pump and then pressurize the fuel between the pump to the carburetor. As we’ll see, the vapor lock occurs on the low pressure side of the pump, not the high-pressure side as most enthusiasts might think. It also does occur to fuel stored in the float bowls on some carburetors. We have to take a closer look at fuel to understand why this occurs.
As most enthusiasts know, liquid gasoline does not burn. Instead, it is designed to vaporize even at very low temperatures to facilitate combustion. But gasoline is a very complex liquid. Portions of gasoline are designed to vaporize easily at relatively low temperatures while other portions will remain a liquid even above 250 degrees F.
The percentage of gasoline that evaporates at a given temperature is called the distillation curve. So for an area like St Paul, MN where it gets pretty cold in winter, there will be a winter blend and a summer blend of gasoline. Winter blend gasoline contains a greater percentage of gasoline that will evaporate very easily at very low temperatures. But this winter fuel would vapor lock very easily if used in 100 degree summer heat, so the distillation curve is changed for summer, creating a fuel whose curve vaporizes at higher temperatures.
So now that you have an idea that gasoline evaporates at different rates, we’ll now introduce the concept that this amount of evaporation or vaporization changes with pressure. High pressure prevents gas from vaporizing while low pressure (a vacuum), enhances vaporization. Every liquid, including gasoline, has a physical trait that is called its vapor pressure. This is defined as the pressure exerted by the vapor escaping from a liquid in a closed system at a given temperature. Pressure is what squeezes molecules together, while lower pressure allows the molecules to separate – and more easily vaporize. With lower external pressure, the liquid’s boiling point becomes lower, allowing more of the liquid to become vapor. Gasoline is no different and will tend to remain a liquid when pressurized.
So now let’s take a typical engine-driven fuel pump for a carbureted application. As we mentioned, the pump must create low pressure on the suction side in order to use atmospheric pressure sitting on top of the fuel in the tank to push the fuel through the fuel line up to the inlet side of the pump. This means the fuel is now in a container with lower pressure, which increases the likelihood of more of the fuel turning to vapor. Once the fuel turns to vapor, the pump stops moving fuel. Cooling the fuel is the only way to make it all work again.
Things that can contribute to vapor lock on a carbureted car can be things like a poor vent in the tank or any kind of restriction on the inlet side that will require the pump to create higher vacuum in order to move the fuel into the pump. The usual recommendation that makes the most sense to combat vapor lock is to install an electric pump in the rear near the tank to help push the fuel to the mechanical pump — or just eliminate the mechanical pump altogether.
For this reason, the rear-mounted electric fuel pump has become a very common addition to performance cars, including carbureted engines. However, an electric fuel pump can also succumb to vapor lock issues, although this is more often associated with high output applications. The key to good electric fuel pump performance is to mount the pump as low as possible relative to the fuel level. This reduces the effort (high vacuum) on the inlet side required to pump fuel.
All new cars now use in-tank pumps for several good reasons. First, the pump is immersed in fuel which helps keep the pump cool. Even more importantly, with the pump sitting at or near the bottom of the tank, the weight of the standing column of fuel above the pump inlet pushes the fuel into the pump inlet. This may not sound all that important, but it’s critical to pump performance. Pumps are very good at creating output pressure, but generally are much less efficient at pulling fuel into the pump. So any effort that improves inlet efficiency will be rewarded with increased pump performance.
As an example, we had a friend who built a bad-boy turbocharged LS street engine that made around 850-900 horsepower. He used an Aeromotive A-1000 pump, which was more than capable of supplying all the fuel required — even a full boost. Unfortunately, he mounted the pump inside the trunk in the flat area above the rear axle. While the system was routed with a return back to the tank, the pump position was a serious error. This location required the pump to “pull” the fuel nearly 24 inches – two feet! – vertically just to get to the pump’s inlet. This required creating high vacuum on the inlet side of the pump. Our friend then coupled this design handicap with a very small fuel tank on a very hot, summer’s day.
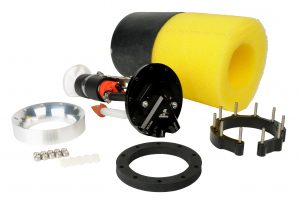
This is Aeromotive’s Phantom kit that uses a 340 lph (90 gallons per hour) at 43 psi. This is enough to feed a normally aspirated engine making in excess of 900 hp. Plus, these newest Stealth 340 pumps are E85 compatible.
At highway cruise, his LS engine was very fuel efficient. But while the engine required very little fuel, the pump was still running at maximum output. This circulated the unused fuel very quickly between the fuel tank and the engine. With each lap, the fuel absorbed heat from the pump and the engine. Soon enough, the high fuel temperature combined with very low pressure on the inlet side caused the fuel to vaporize – classic vapor lock. When that happened, the pump quit working. On a hot day, this occurred with maddening regularity. The solution was to replace the large single pump with a pair of smaller Stealth 340 pumps located at the bottom of the fuel tank. Running on one smaller pump at part throttle, the problems were eliminated. The second pump would kick on for the high hp runs.
While this is a high-horsepower example, the problem exists even on much milder engines when the pump is located where the fuel is subjected to high vacuum on the inlet side. The above solution we described for the Nova is essentially the Aeromotive Dual Phantom kit that will adapt to nearly any stock muscle car fuel tank.
Of course, for a typical street car, the dual Phantom kit would be overkill. A single Stealth 340 Phantom pump kit is available and can be ordered with a smaller 200 lph (liter per hour) pump for engines that only make 400-450 horsepower. These kits work exceptionally well for EFI systems like the new wave of self-learning EFI systems.
I hope this somewhat lengthy explanation gives you a better understanding of how vapor lock occurs and solutions that will prevent it from happening in the first place.
So, as you go higher into the mountains the air becomes thinner, or pressure is less,
vs. being at sea level!
1940 ford sedan stock, runs fine,all day long til shut it off , return to car 10min later won’t start