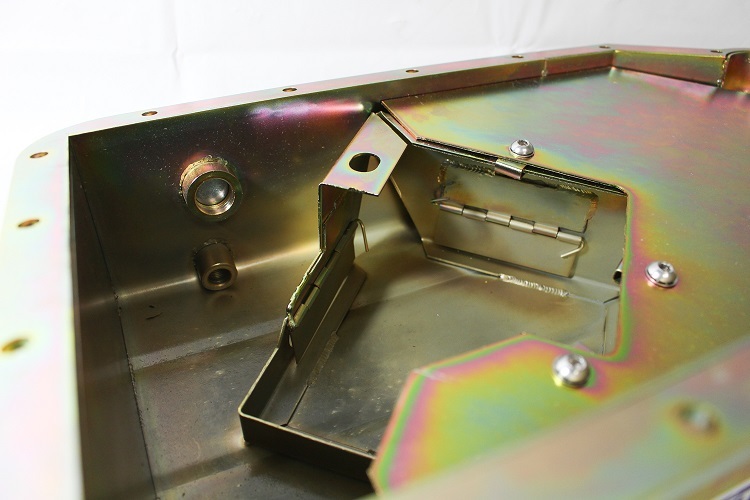
(Image/Deft Motion)
Editor’s Note: Author Jeff Behuniak is with Canton Racing Products, a company that specializes in manufacturing oiling and cooling products for racing applications, including oil pans.
…
A lot of people assume that an oil pan is just an oil pan.
The assumption is that it holds oil and that’s it. That simple and cheap is the way to go. The oil pan is often an afterthought until engine maintenance requires draining the oiling system.
However, for the most-dedicated auto enthusiasts, the oil pan and entire oiling system are treated like a matter of engine life and death.
Many enthusiasts know that there are three basic types of oil systems.
Beyond the three oil system types, there are specific ways to achieve a proper setup.
Today, we’re going to focus on the two most common oil pan materials—steel vs. aluminum—explain some key differences between them, and hopefully arm you with information that can help you choose an oil pan that will work best in your vehicle.
We will be talking mostly about fabricated performance oil pans which have been common in racing for more than 30 years. While casting oil pans is the best option for large automakers, the racing industry often requires shorter runs of pans designed for specific applications. Fabricating oil pans offers the flexibility to include features like trap doors, anti-slosh baffles, and power pouches to improve performance.
One of the most frequently asked questions we get about Canton Racing oil pans is whether to use steel or aluminum. Let’s talk about that.
Cost of Steel vs. Aluminum Oil Pans
Typically, cost is the most influential factor when choosing oil pan material. As a general rule, aluminum pans are about twice as expensive as steel pans.
The increased cost has a few different factors involved, including material, fabrication, and the welding skills required to make them.
Aluminum is typically about 50 percent more expensive than steel.

A Canton Racing aluminum oil pan.
How the pan is fabricated also influences final pricing. The most cost-effective way to build a performance oil pan is off of a stock core. Since most stock pans are stamped steel, building off of a steel core is a common practice and often preferred.
As for aluminum, when the stock pans are cast, the aluminum is often impure and porous—two conditions that can make welding difficult.
This drastically reduces the strength of the weld joints and overall integrity of the pan.
Welding to a cast pan with fabricated sheet aluminum also creates two very different-looking sections, which some people don’t like.
These factors make using a stock core in an aluminum application difficult and undesirable. Since building an aluminum pan off of a core is an ineffective option, billet rails and billet seals are often required to fully fabricate the oil pan rail. While this provides a great sealing surface, the billet pieces can be costly in both labor and material.
The second major cost factor is the advanced skill and care required to properly weld and fabricate aluminum. In addition to the increased skill it is also common to weld both inside and outside which doubles welding time.
Part of the advanced skill required to weld aluminum has to do with it being a softer metal and more prone to burn-through. When welding aluminum, the heat must be applied much more carefully and consistently than when welding steel.
The soft aluminum warps more easily than steel, requiring a more thorough jig and welding procedure to prevent warping. There is also a much higher waste factor due to the soft nature of aluminum. Whether it is due to burn-through or surface scratches, the possibility of damaging parts while welding is much higher with aluminum. All of this factors into the increased cost.
Weight, Thermal Conductivity & Strength of Aluminum vs. Steel Oil Pans
There are distinct advantages and disadvantages of choosing either material.
The largest advantage of an aluminum pan is the weight difference.
The rule of thumb that we use at Canton Racing is that an aluminum pan will save you about one-third of the weight of a similar steel pan. While any weight savings is usually good, some people argue that this weight savings is marginalized by the fact that it’s located beneath the motor.
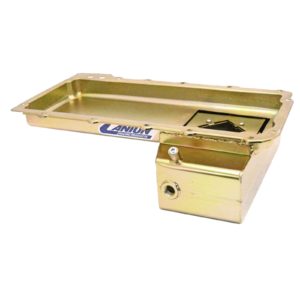
A Canton Racing steel oil pan.
Another advantage of aluminum is its superior thermal conductivity, allowing the oil pan to draw more heat from the oil. Typically, the surface area of the oil pan will be the determining factor in how much heat will dissipate. However, this is an advantage with a downside. Aluminum becomes much softer at higher temperatures, creating weaker material that might compromise the oil pan if struck hard.
Steel, on the other hand, can hold much-higher temperatures without losing rigidity.
This leads to aluminum’s most glaring issue.
The biggest disadvantage of fabricated aluminum pans is the structural integrity.
A cast-aluminum oil pan will likely crack if hit hard enough. In our experience, fabricated aluminum pans that take a hit usually have much more severe damage than we would expect from a steel pan.
Since aluminum is more malleable than steel, what might be considered minor damage to a steel pan can fatal to aluminum pans.
Additionally, a damaged aluminum pan is typically expensive to fix.
Compared to an aluminum pan, a steel pan holds its shape much better than aluminum and is often salvageable or repairable at the track.
In racing, you can’t win if you can’t finish. While there are distinct advantages to fabricated aluminum oil pans, it often makes sense to choose a steel oil pan.
Editor’s Note: This article originally appeared in The Canton Blog—an online publication owned by Canton Racing Products, delivering technical and how-to information about engine oil and cooling systems.
I build “Engines” not motors, I’ve dealt with aluminum & steel pans.They both have their “Pro’s & Con’s. The biggest set back with aluminum is availability, most aftermarket cast aluminum oil pan’s only cater to Chevy & Ford…… There’s a lot more engine’s out there! And the cost of a fabricated aluminum pan is very expensive, and I’ve had problems in the past with the aluminum pan’s as far as leaking due from heat expansion & contracting. If you’re going all out ” Racing” then go with aluminum,,,, you can afford it,But as far as a “daily ~ driver” or a “weekend ~ warrior” I’d stick with with the steel oil pan. If you’re worried about the oil temperature…. Install an oil cooler,or,a lager capacity oil pan(if you have the space)
I’ll stick with the stock/steel oil pan,(spray a couple coat’s of paint on it){ any color!} and you’re good to go!!!!!
MOTORHEAD~TY