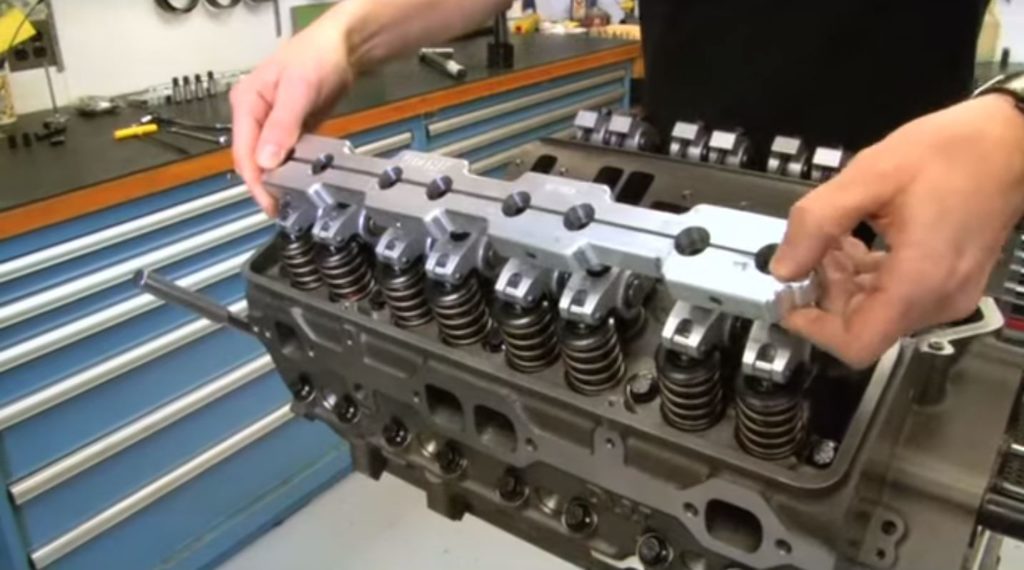
Image/YouTube – Dart
Under extreme, high-RPM operating stress, your engine’s valvetrain is subject to distortion and flex.
This can cause havoc with the valve operation, altering its geometry to cause poor performance or worse—engine damage.
That’s where valvetrain stabilizers (also known as stud girdles) come in.
As part of it’s “Dart University” program, in today’s video the folks at Dart walk you though the importance of valvetrain stability and the aftermarket solution for keeping your valve components secure.
A stud girdle clamps onto your engine’s rocker studs, essentially locking your rockers together to deliver the stability you need in a high-rpm performance engine.
But it’s not as simple as just slapping a girdle under your valve covers.
This video from Dart will show you how to install a few different types of girdles—which type you’ll need depends largely on which engine you have.
Properly installing a stud girdle allows you to still set valve lash and make the necessary adjustments for optimal valve operation.
The Dart video is less than four minutes and is a must-watch if you’re building a performance or race-bred engine.
Good video about a topic that’s especially important on engines with serious modifications. I’m running an extensively modified Ford 351 Cleveland with “high port” iron heads that were formerly used in Pro Stock competition. A solid roller cam and lifter setup that works well up to 8400 rpm’s so the valve train using titanium valves gets its share of abuse. To help keep the ARP 7/16” screw-in studs and Harland Sharp roller rockers in their proper place, I’m using a Jomar Stud Girdle and poly locks.
For anyone not familiar with stud deflection, just think of it in terms of a length of metal rod being held in place on one end and the other end being bent back and forth a tiny bit thousands of times per minute. The metal will fatigue eventually and snap in two. The results are usually catastrophic when a rocker arm stud breaks. A good stud girdle is cost effective insurance against this type of failure.