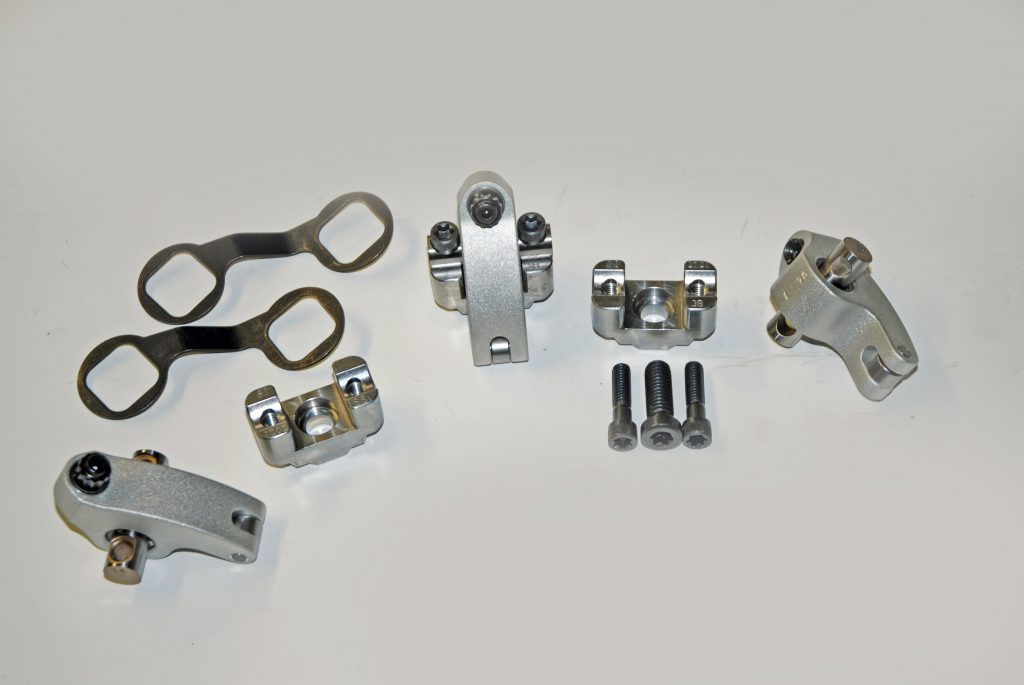
Tons of options are available when it comes to rocker arms for domestic V8 engines.
When examining today’s crop of roller rockers, it becomes clear that a considerable amount of research and development has occurred over the years — particularly when it comes to race applications. Where, at one time, it was sufficient to replace something like a stamped rocker with a rollerized example, now we’re dealing with shaft rocker setups complete with a wide range of upgrades and options.
The reasons for moving toward a shaft-mount rocker are many-fold. For example, in something like a small block Chevy application, the stock rocker has a relatively short pivot length. This means the arc it travels in is comparatively small, particularly in contrast to other pushrod engines (Jesel notes that a stock small block Chevy has a rocker pivot length of 1.40-inches. In comparison, a big block has a pivot length of 1.65-inches).
What this all means is the stock small block rocker arm tip more or less scrubs across the tip of the valve as it opens. This isn’t much of an issue at lower gross valve lifts such as those experienced with stock or mild camshafts (such as those used in production engines). But when you increase the lift dramatically (as seen in today’s race engines) and simultaneously increase the spring pressure you’re soon faced with another quandary — an increase in friction.
As it turns out, decades ago, Dan Jesel (the owner of Jesel Valvetrain Innovation) relocated the rocker studs away from the valves on a small block Chevy. The idea here was to incorporate big-block rocker arms in the mix (which made perfect sense considering the rat motor’s 1.7:1 rocker ratio).
But something else happened during the R&D: While checking the rotating torque of the engine, the small block fitted with big block rockers consumed 80 ft.-lbs. less torque to rotate when compared to a stock rocker small block. That’s a bunch.
Of course, relocating rocker studs isn’t an easy operation on any engine. But you can’t change the rocker pivot length and correct the rocker geometry unless you move the pivot point.
Instead of physically moving the rocker stud mount, it’s actually easier to start from scratch and build an entirely new rocker arm arrangement such as today’s shaft rocker.
That’s essentially how and why Jesel’s line of shaft rockers were born.
In the beginning, a gain in rocker ratio was a big part of the Jesel plan. But as mentioned above, a side benefit was the reduction of friction in the valvetrain. Fair enough — the reduction in friction is huge, however that isn’t the end.
It turns out that shaft rocker systems also offer a considerable amount of stability at high engine speeds. Again, using the familiar small block Chevy as the example, the pushrod, the rocker stud, and the valve are not always in line. This isn’t much of an issue with stock stamped rockers and low valve lifts. The reason is the stock stamped rocker can more or less compensate.
A conventional stud mount roller rocker replacement cannot “fix” the misalignment. The geometry can be (and regularly is) adjusted with a shaft setup. That’s the reason why shaft rockers prove more stable at higher engine speeds.
Much of Jesel’s research directed toward high-rpm operation is performed in conjunction with SpinTron equipment (basically, a high-tech valvetrain “dyno”). A SpinTron employs a high-powered AC electric motor to spin the crankshaft and valvetrain of the test engine while a high-tech laser camera (LVTS or “Laser Valve Train Tracking System”) tracks the valve motion and pushrod behavior. The data is transmitted to a computer in the form of a special graph. You can see the results live (on screen) as the engine spins. With the SpinTron, you can precisely identify, document and record crucial characteristics of the valvetrain such as valve bounce, lofting, spring harmonics, and pushrod deflection.
When using the SpinTron, the first step is to create a baseline valve trace by tracking the valve at a stable engine speed (typically 2,000-3,000 rpm). Then the operator (in this case, the folks from Jesel) increase the engine speed to the next rpm level. The SpinTron records and graphs each new valve trace over the baseline trace. This allows Jesel to compare valvetrain stability at various rpm levels, which is an ideal way to prove or disprove new products, theories and materials.
Sounds great, but the really neat part is the SpinTron performs these tests at speeds from 500-20,000 rpm.
A huge benefit of today’s shaft rockers is the increased reliability they offer when compared to an original stud mount rocker arm. Consider a simple vintage Chevy stamped steel, stud mount rocker. The folks from Jesel remind us that as the stud mount rocker slides up and down the stud, it takes up the valve lash before it opens the valve. Jesel uses the fabled old Duntov cam as an example.
Here, the called-for lash is 0.030-inch on both the intake and the exhaust.
In practice, that old Chevy has the rocker sliding up and down 0.030-inch on each stud, each time the valve opens. It wasn’t hard to run those old small blocks up to 7,000 rpm or so (higher if you were brave). The lash worked as a slide hammer. That meant that the original pressed-in studs were (often) pulled right out of the head.
The initial fix here was to use a roll pin to capture the stud. That eventually morphed into a screw-in stud arrangement. This allowed more valve spring pressure and of course, more rpm. The next thing that happened was bending and broken studs, which eventually led to stud girdles, which is right where we started.
In contrast to all of this is the shaft mount rocker, which simply rotates to take up the lash. It tends to make everything much more reliable in the valve train.
Jesel adds: “Because the longer pivot length in a shaft rocker doesn’t side-load the valve as much as a stud mount rocker, shaft rockers tend to be much easier on valve guides, valve seats and valve tips.”
The way a rocker arm assembly is mounted to the cylinder head is critical.
Essentially, the rocker arm must be secured to the cylinder head so that no movement is possible. In the case of a shaft rocker, the actual rocker arm along with the shaft must also be securely fastened to the mounting bar, again with no movement allowed.
That’s why Jesel came up with their unique “stand links” for their Sportsman series big block Chevy rockers (shown in the accompany photos). The setup for rat motors orientates the CNC-machined steel rocker stands and aligns the rocker roller squarely with the valve tip. Jesel also notes that the stand link also acts as a safety guide in the event of a loose bolt.
As you might have guessed, shaft rockers offer all sorts of different ratio choices.
The distance between the pushrod cup, the rocker shaft centerline and the roller tip determine the ratio of a rocker arm. In a shaft rocker setup, various pivot lengths can accept a big range of ratios from (approximately) 1.4:1 through to 2.25:1. That wide range of ratios simply isn’t practical (or possible in many cases) in a stud mount rocker.
How important is increased rocker ratio? Very!
It should be no surprise to astute engine builders that using a rocker arm to increase valve lift has its benefits. When you use the rocker arm to change lift figures, then you have access to an almost infinite means to fine-tune the valvetrain on a per-cylinder or per-valve basis. The reality here is, it’s a whole bunch easier to swap rockers than it is to swap complete camshafts.
To recap, perhaps the biggest benefit of a shaft rocker system has to be the considerable improvement it offers when it comes to the geometry of the valvetrain.
As pointed out earlier, in order to effectively make a change in the geometry, you’re pretty much forced to move the rocker’s pivot point. With a modern Jesel shaft rocker layout, the pivot can be moved further away from the valve which in turn allows for the longer rocker pivot length.
With some shaft rocker arm arrangements, it’s also possible for the manufacturer to lower the pivot point. This makes for a low pivot arc from half to full-valve lift. This is the point where valve spring pressures are the highest. The improvement in geometry eliminates much of the friction created by the rocker when it is dragged (scrubbed) across the valve tip. Needless to say, this also makes for gains in both power and of course, reliability.
Finally, one other potentially big benefit that is seldom taken into account is the ease of maintenance a good shaft rocker setup like the Jesel Sportsman provides.
Ponder something like valve lash with a conventional roller rocker arm system fitted with a stud girdle: First you loosen the stud girdle, and then you lash the valves. The girdle is re-tightened and finally most folks check the valve lash once more. If the studs are the least bit out of alignment, tightening the stud girdle changes the valve lash.
Now you have to start all over again (been there, done that). Not fun. But you also have to be extremely careful with clearances on some combinations — the rockers and girdle can touch, which obviously spells more (and bigger) trouble.
None of that monkey business is required with the Jesel Sportsman shaft rocker. You just set the lash and pretty much forget about it. In fact, there are some tools out there (we covered them an issue or so ago) that Summit offers that make setting lash on a Jesel rocker incredibly easy.
As you can see, a shaft rocker setup such as the Jesel Sportsman provides a wide range of valvetrain improvements. They’re so good and so reliable, I even use them on fast street cars (that’s the way we roll!).
For a closer look, check out the accompanying photos:
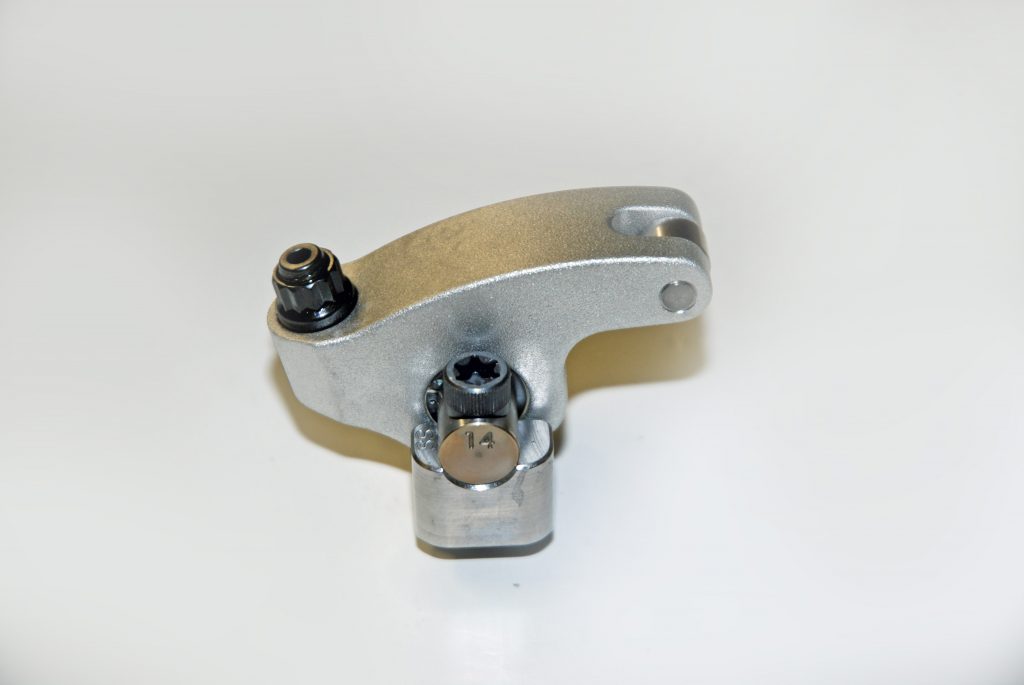
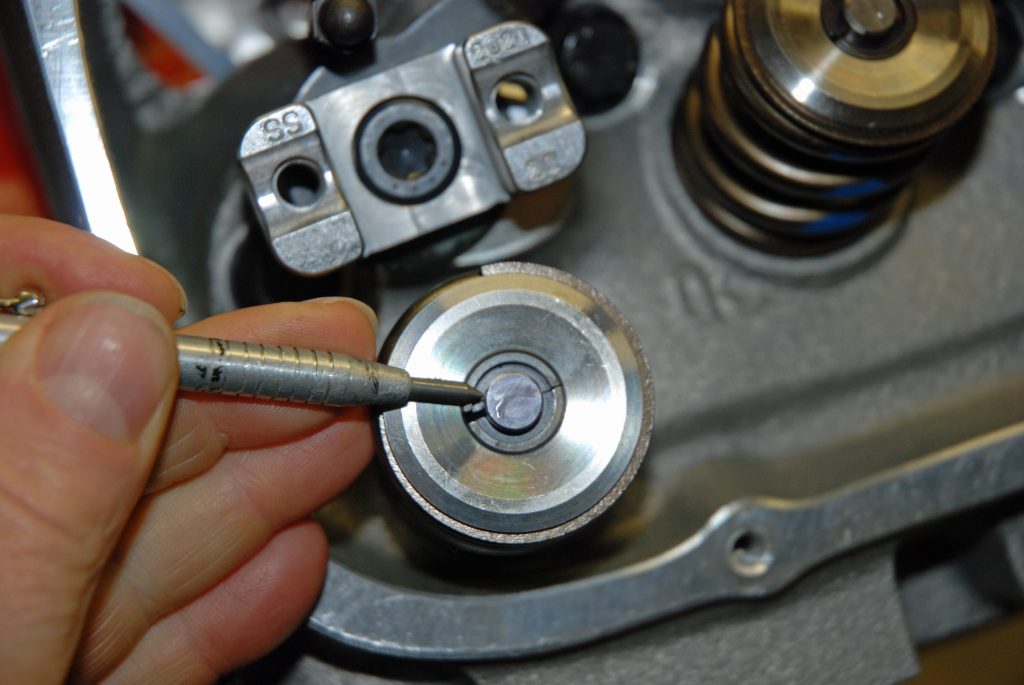
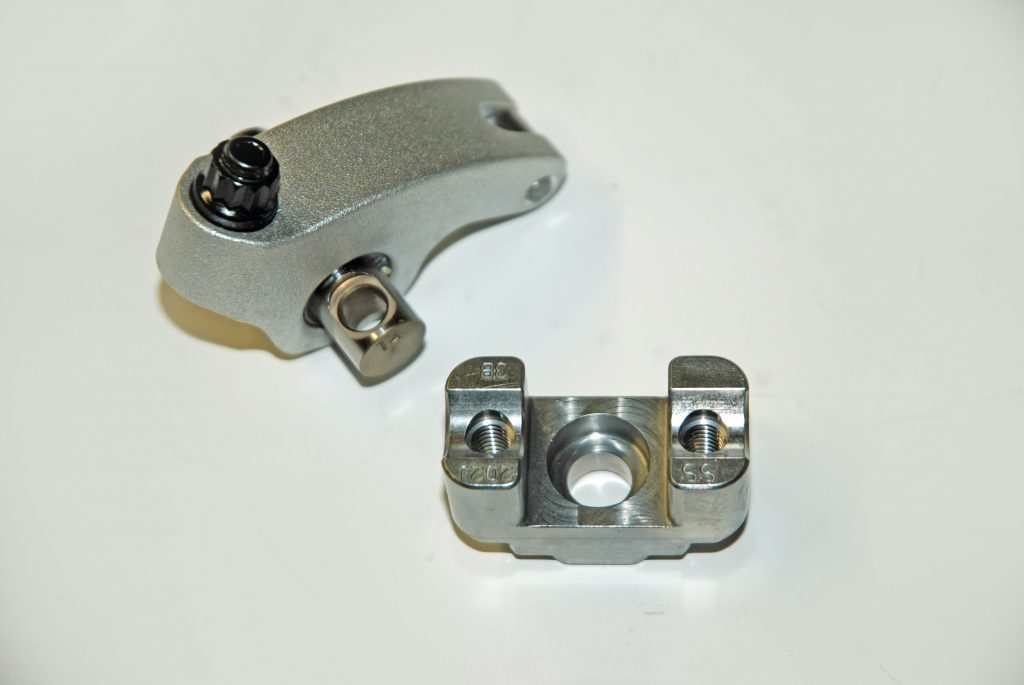
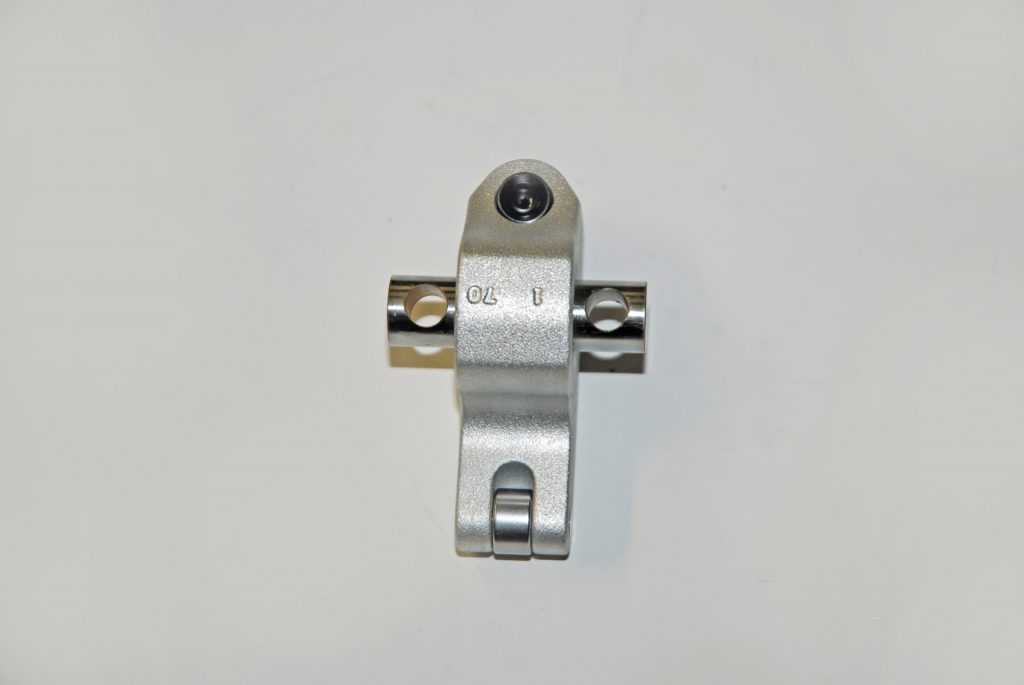
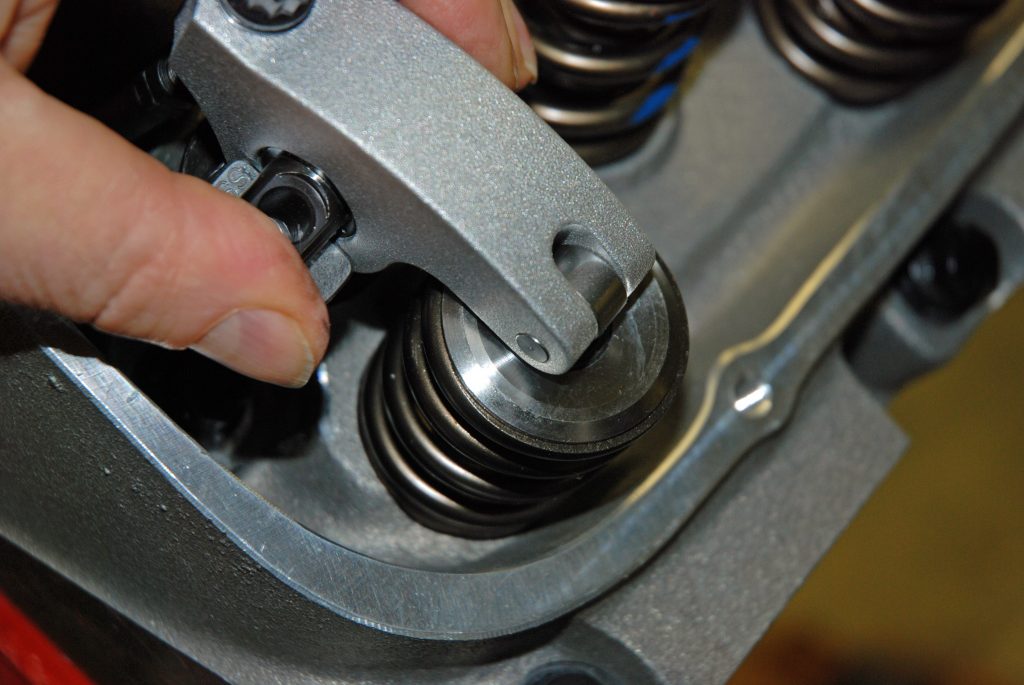

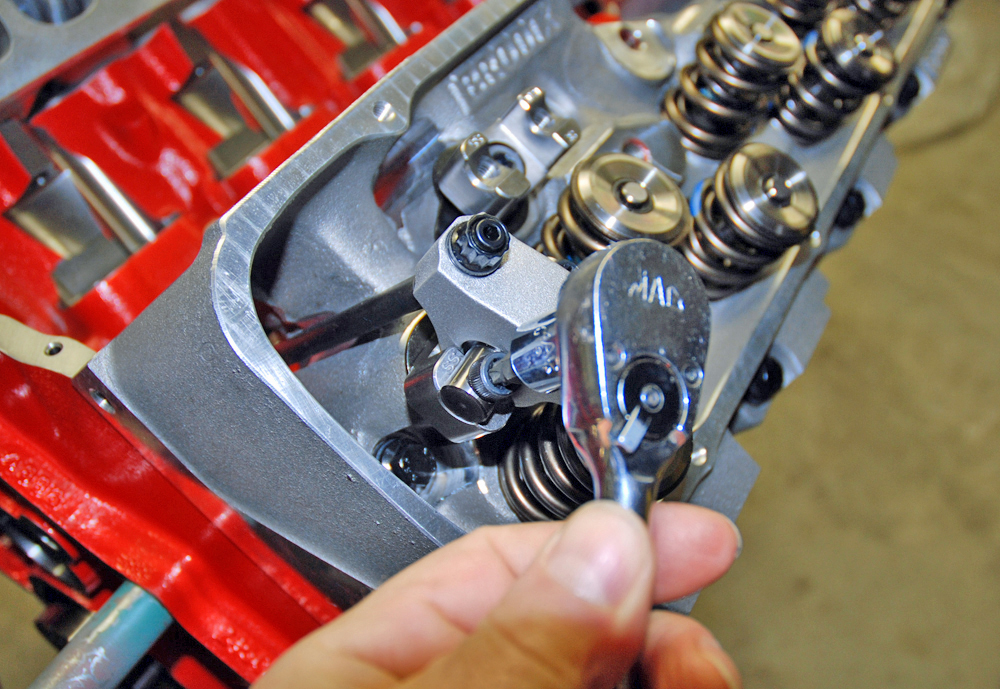
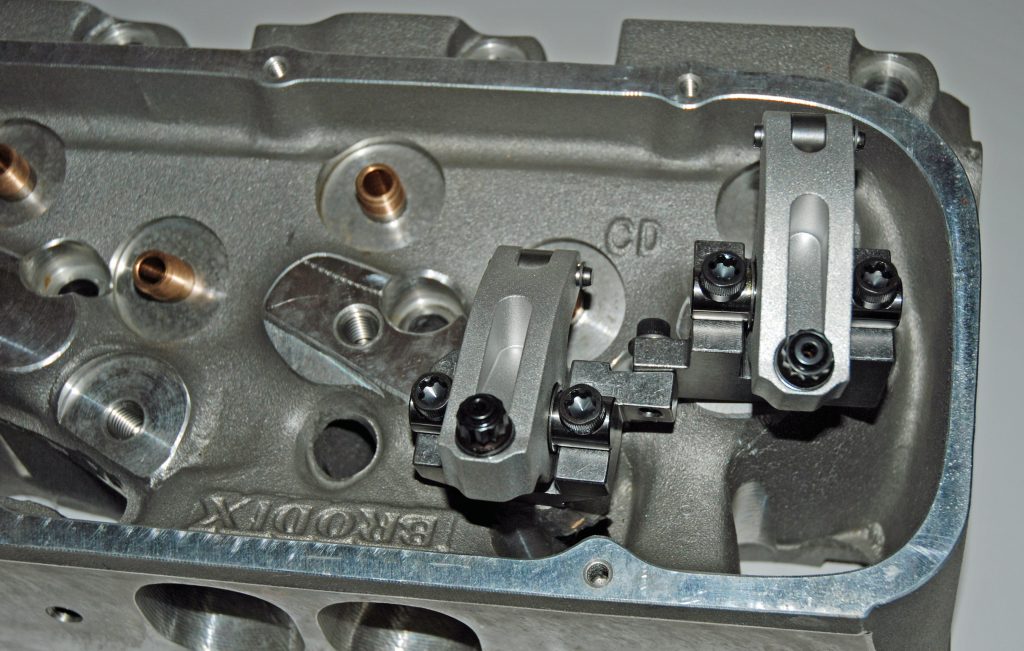
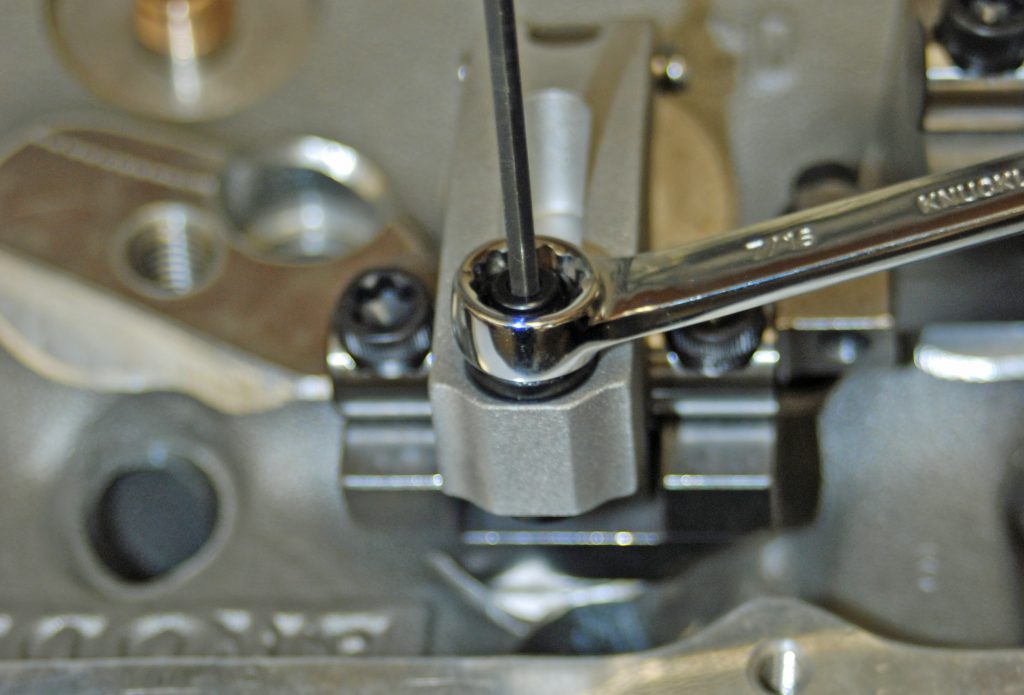
I must say that Wayne Scraba has a unique way of taking some of the most complex technical information and explaining it in such a clear and concise manner that even novice engine builders can feel confident in virtually any topic.
After 45 years of personal experience mostly with Ford Performance builds, I’m past the novice stage but with automotive technology advancing faster than ever, there’s something new to learn everyday.
While Mr.Scraba’s excellent writing as an Automotive Technical Journalist is sure to please the GM crowd, that’s more about majority rules so I fully understand it.
When it comes to superior valve train components, Jesel is the name that needs no introductions. I’ve been using the best roller rocker arms and stud girdle available for my builds centered around Ford’s 351 Cleveland heads. I’m probably going to be disappointed with my findings but now is a good time to see what Jesel has to offer for canted valve Cleveland heads.
And the beat goes on….
Thakx for article I was looking to improve power and stability I knew something was happening that I needed to learn.
Thank you Fergie