Everyone has a car with at least one impossible to reach bolt or other fastener. In some cases, there could be a dozen or more of those cuss-word bolts.
We’ve all been there (band-aids, cuss-words and all).
Fortunately, there are some good solutions (actually a whole bunch of them) when it comes to dealing with impossible to reach fasteners. Here are a few solutions right out of my own tool cabinets:
Flex Head Ratchet: Flex head ratchets have been around for a long time. I have four of them in my tool collection. The 3/8-inch drive shown in the accompanying photo can be adjusted three ways in each direction (from straight). Couple this with an assortment of universal joints and specialty sockets, and it goes a long way toward reaching a grumpy nut or bolt.
Palm Drive Ratchet: Palm drive (also known as “finger” or “thumbwheel”) ratchets are pretty cool. You can’t really place a lot of torque on them, but they’re sure convenient for working fasteners in tight spots. The SK tools example shown in the photos is pretty conventional, but they’re also available with a gimble handle. That setup, which pivots on two planes, offers even more flexibility. You can get them in all sorts of drives.
Universal Joint Adapters: Universal adapters are relatively common. I have handful of them in various drives (1/4-3/8-1/2-inch). They allow you to rotate a socket to almost 90-degrees. Sometimes this allows you to get the socket on the fastener. Then you can take some “tilt” out of the mix so that it is possible to actually spin the nut or bolt with a ratchet. Over time, universal joints tend to loosen. Some will actually flop around. If that becomes a frustration for a specific situation, simply wrap the joint with a bit of tape. That’ll take some flex out of it.
Flex Head Sockets: You can get these in quite a few different configurations. Basically, flex head sockets are quite a bit shorter than a combination of a universal joint and a socket combination. Because of this, you can get them into a tighter spot.
Wobble Extensions: Some socket extensions are available with a wobble end. This allows a few degrees of offset on the socket at the extension. They’re available in all sorts of different lengths and sizes.
Knurled Extensions: Another cool extension that’s out there is the knurled model. Here, the socket extension has a large knurl on the body and another on the female end. This allows you to hand tighten a fastener without the ratchet or other handle attached. They too are available in a sorts of sizes and lengths.
Nut Drivers: Most everyone has a nut driver set, but for the few that don’t, they’re still important. It’s not a bad idea to add a socket driver handle, because they can give you a bit more versatility than a nut driver. As an example, you can use them to hand-turn something like a fIex head socket.
Ratcheting Box Wrenches: Racheting box ends work really well in tight quarters. They’re available in all sorts of configurations – flat, shallow offset, deep offset, with or without an open combination end, with or without flex heads, and so on. You can get them in different lengths and in all sorts of sizes.
In the end, the above is just a glimpse of what is available for time-saving tools – especially those that allow you to work on those impossible nuts and bolts. There are all sorts of other solutions found in the Summit Racing catalog. For a closer look at a few of them, check out the accompanying photos.
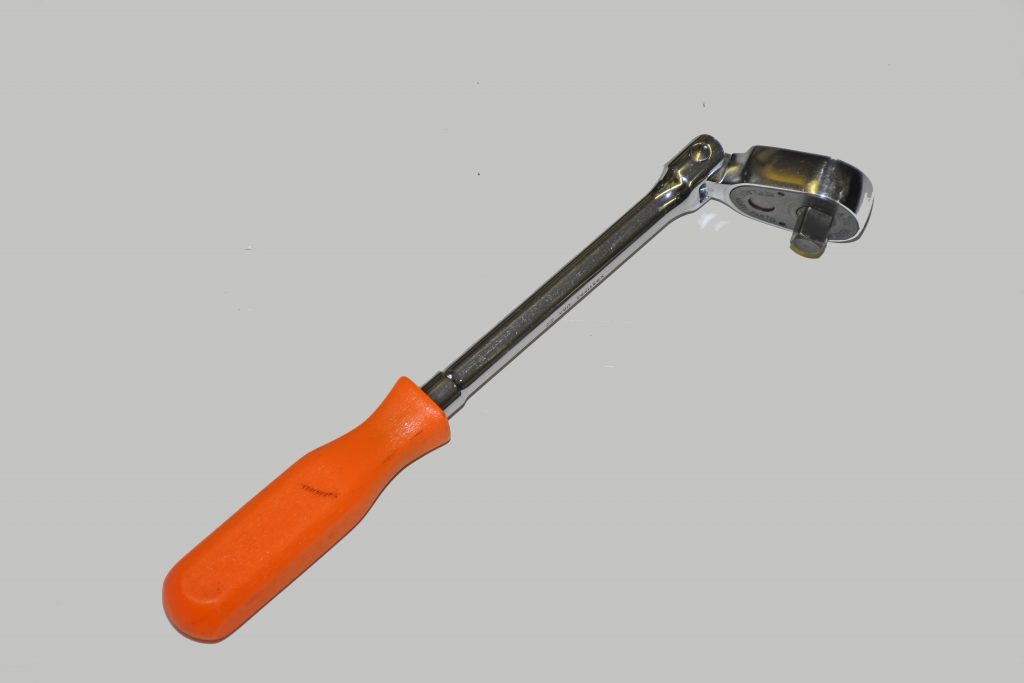
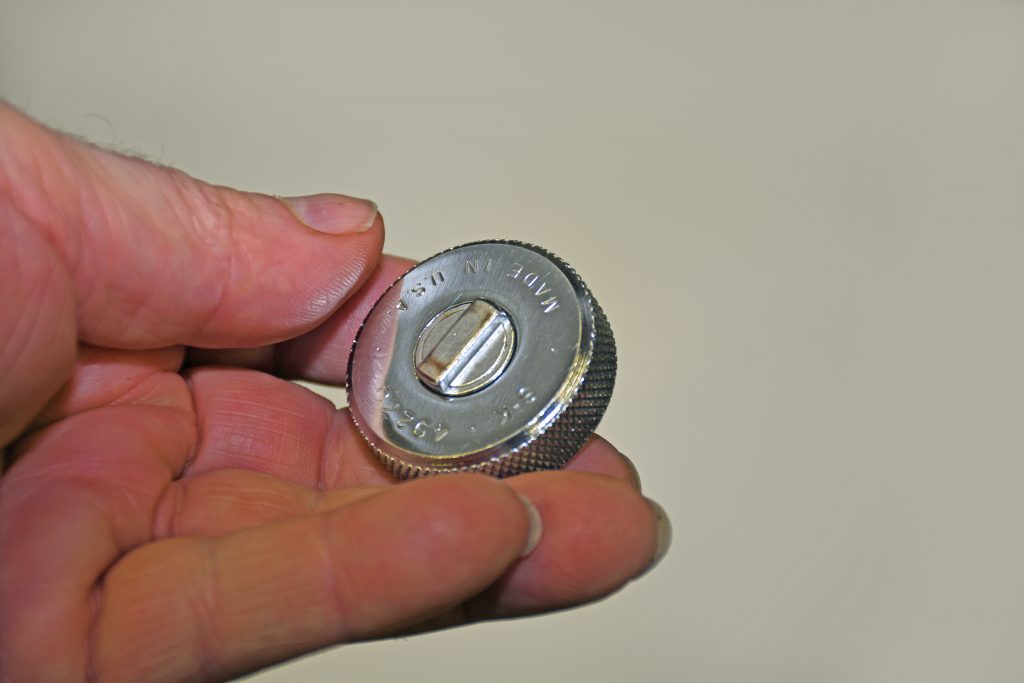
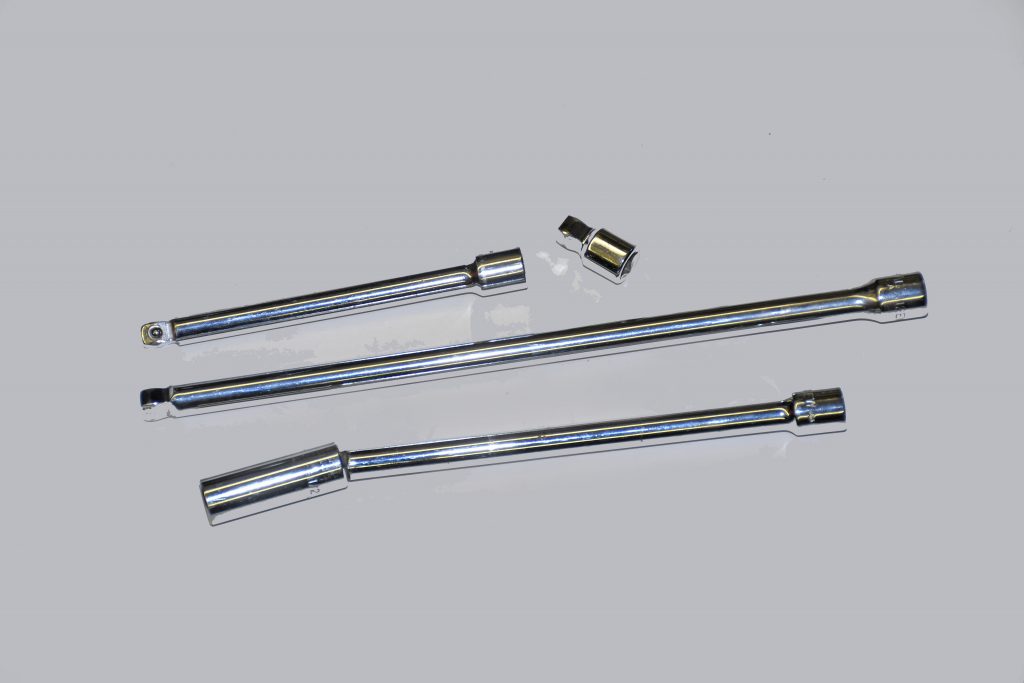
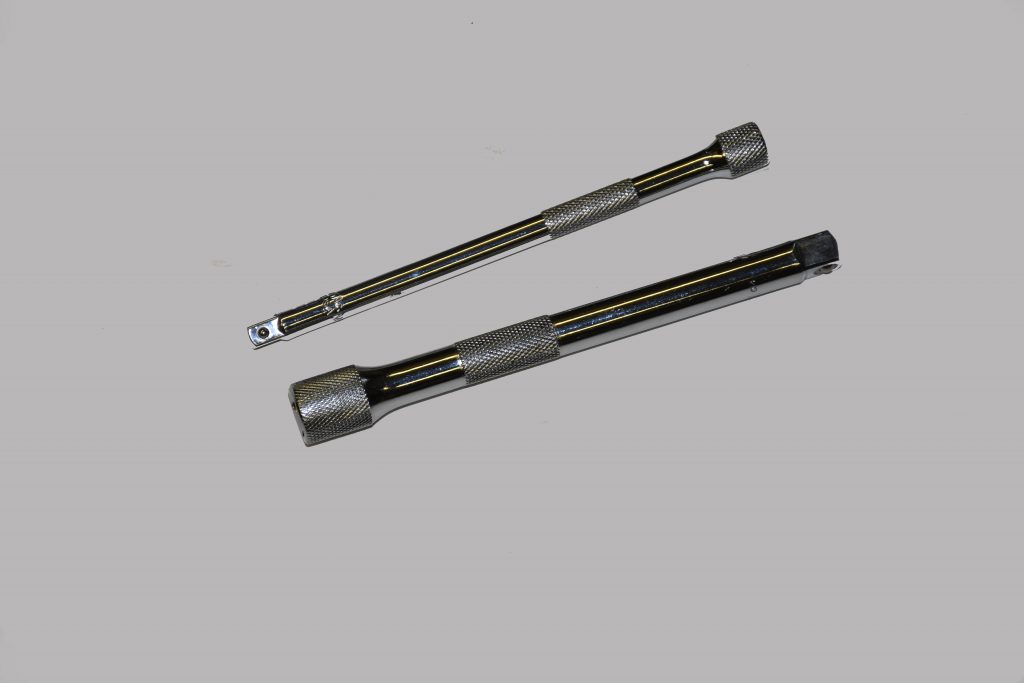
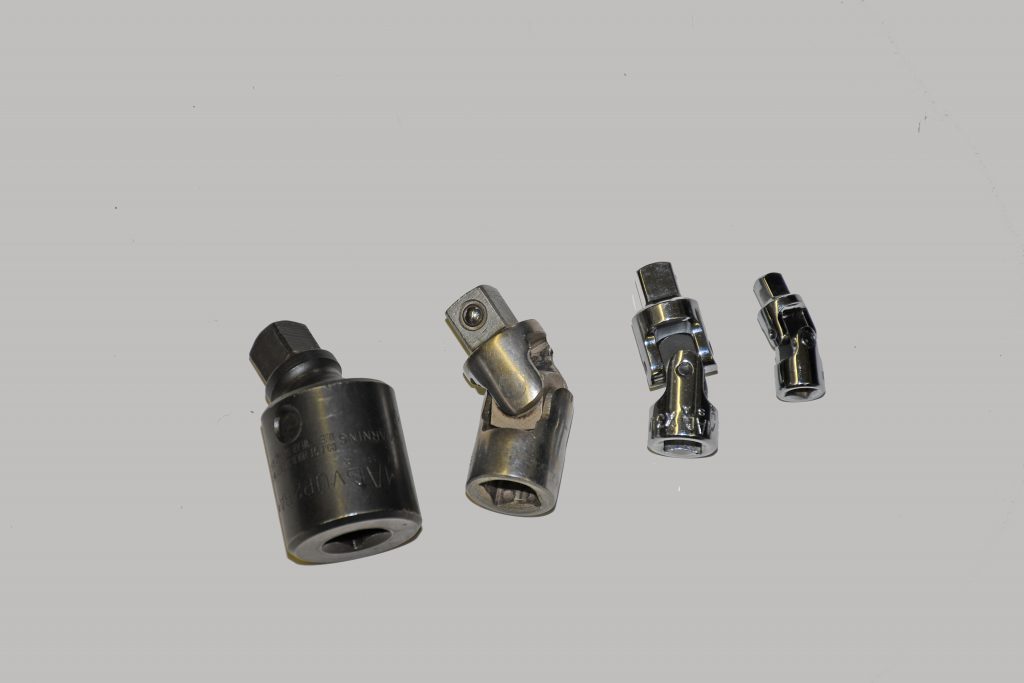
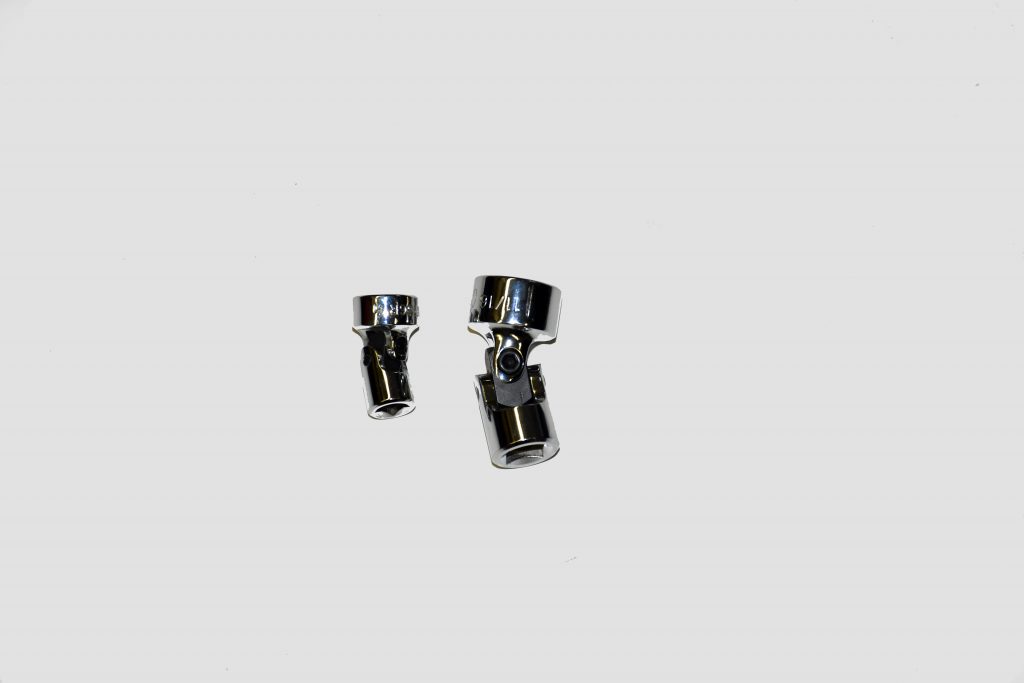
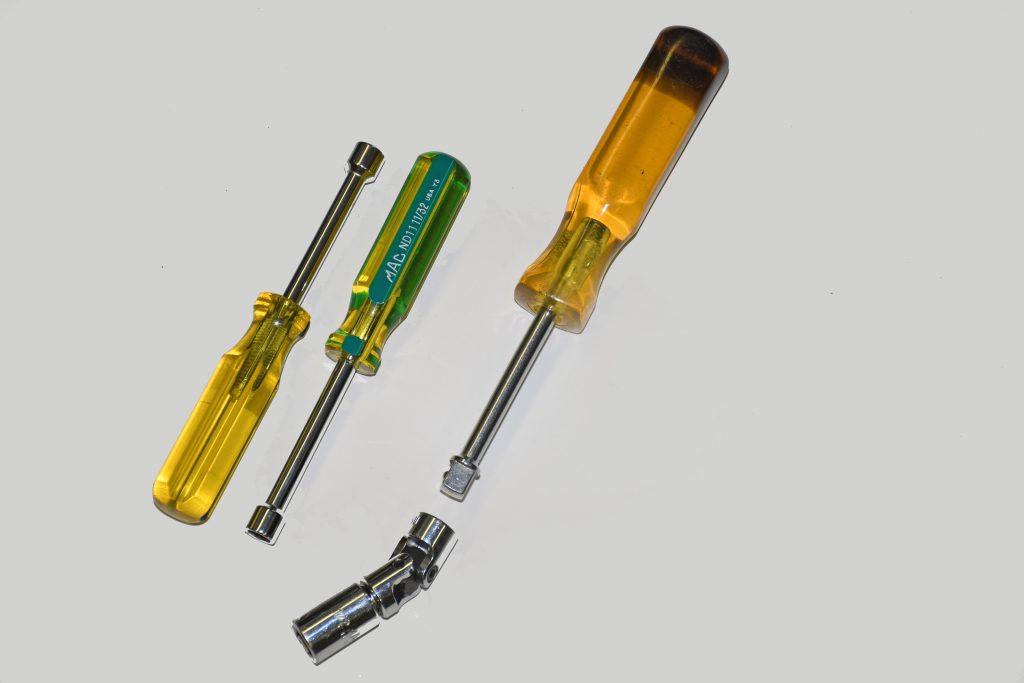
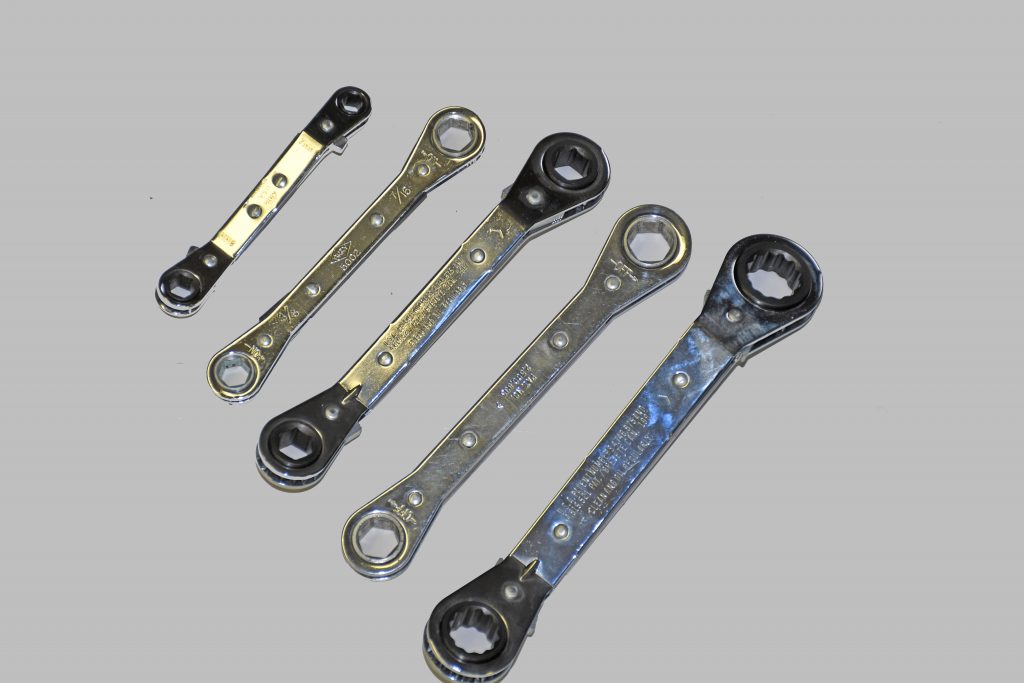
[…] Everyone has a car with at least one impossible to reach bolt or other fastener. In some cases, there could be a dozen or more of those cuss-word bolts. We’ve […] Read full article at http://www.onallcylinders.com […]
Great article….but what about the “homemade” tools that you can’t find in Normal Tool Catalogs? I had quite a few in my Toolbox.(should of Patented them) Also the one you listed, I’ve owned all of them and used them in a series of combinations talk about knuckle-busters! Got the job done.
KEEP ROCKING!
Hi Wayne Scraba, I’m writing you from Sudbury, Ontario canada. I have a problem you might solve for me. I rebuilding a 66 Dodge 500 series truck. It is the cab forward model. About a three ton truck, from your midwest. I have a clutch problem. I have replaced the master cylinder and the slave cylinder and the lines, but I cannot get enough stroke to move the fork forward, to press the fingers on the pressure plate. I don’t know what to do. One thing I figured out is I replaced the lines with 5/16 lines, when the original is 3/16. Also I used a flexible hose at the slave cylinder. (3/8) Would this make a difference? Also the master is a very small, single chamber cylinder. Your views would be appreciated. Thank you, Paul Kennedy
You already figured it out yourself. Switch back to orginal line size 🙂
[…] you can use a ratchet and sockets. Sometimes, a socket extension is required to entry a difficult-to-reach location. But prior to you do any of that, make a gap for that bolt. It doesn’t have a sharp tip like a […]
But none will solve this: threaded bolt, facing down, can get nut at bolt butVERY little room to get fingers to then turn. (No access from bottom). Need skinny extending tool that can HOLD all sizes of nut so nut can be put in position, then need a mechanical/electrical way to, from handle, start the head, with nut in position, to revolve both on/off.
Have you tried using a magnetic retrieval tool to start the bolt? I’ve done that a few times–find one with a good, strong magnet and–provided the bolt is magnetic too–you can use it to start the bolt and get it down finger-tight. Then, just follow up with a long-reach socket?
Tite Reach makes a tool for getting at hard to reach spots. You can get a set of low profile magnetic sockets along with it but the setup isn’t cheap. There are also things like old dist. wrenches that were designed to get at the clamp bolt and the flex cable screwdrivers for setting dwell. The ideas persist. In addition there are S shaped wrenches as well as U shaped ones and end wrenches that have funky angles for when you can only get a partial turn. Another outfit, Exo-fit, makes a double jointed ratcheting box end wrench setup that is similar to these and also you can use a ratchet that has a head that can be indexed to different angles if there is enough room to get it in there.