
The question is, does length matter? The answer is a BIG yes, especially if we are referring to intake runner length! You see, runner length plays a huge role in power production, and while everyone is quick to jump on the airflow bandwagon, the reality is that longer runners (that improve power) might actually flow less than their shorter counterparts.
Confused? Well, intake manifolds rely on something other than outright airflow, at least the airflow most of us understand from our flow bench measurements.
I mean, doesn’t more flow equal more power? Well, yes and no, as the airflow of one component doesn’t necessarily mean the total airflow through the motor has improved. Big heads combined with a stock intake and cam will offer little in the way of power gains, but, the same heads mixed with the right intake and cam, can produce impressive results. The same is true of intake runner length, as the length is tuned to optimize cylinder filling (through multiple forms of reflected pressure waves) in a given rpm range. Match this tuned efficiency range with head flow and the right cam, and you have the makings of a healthy performance motor.
To illustrate the effect (and importance) of runner length on the power curve, we set up a test on a late-model Mopar 5.7L Hemi. While runner length has the same effect on any motor, testing it on a Hemi made it that much cooler. Besides, we had a stack injection that made adjustments to the runner length simple and quick on the dyno. All we had to do was cut up some aluminum tubing, add some duct tape, a few hose clamps and bailing wire, and we were in business.
The upside of this test was that, along the way, we also got to compare the Gen 3 stack injection against a simple Mopar Performance single-plane intake.
Though the intake designs differed between the stack injection and the single plane, it was effectively a runner length test as well, as the short-runner, single plane was designed from the outset for high-rpm power production. By contrast, the long(ish) runners in the stack injection enhanced torque production lower in the rev range. As it turned out, the stack injection didn’t just offer more low-speed torque, but more power everywhere—but we’re getting ahead of ourselves!
Before we dive into the results (like you haven’t already), let’s first get to the Mopar Gen III Hemi test motor, then each of the intakes.
The Mopar Gen III Hemi Test Motor
Our 5.7L test motor wasn’t actually a 5.7L at all, but rather a 5.7L/6.1L hybrid of sorts. Though the 5.7L featured the stock 5.7L block, the strength was augmented slightly with the installation of a 6.1L crank and forged internals. After installation of the 6.1L crank, the iron, 5.7L block received forged pistons and rods from Wiseco and K1. To help with power production, the short block also received a mild Crane cam that featured .550 lift (intake and exhaust) and a 212/216-degree duration split.
Topping off the 5.7L was a set of stock (early 5.7L) heads treated only to a simple valve job. To get things started, the 5.7L was first fed by a MPI single-plane intake combined with 36-pound injectors and 4-hole, 4150 throttle body. For dyno use, the Hemi was run with 1.75-inch, long-tube headers and a set of 3-inch collector extensions. Tuned with the Holley HP engine management system, the little Hemi with the single plane produced peak numbers of 430 hp at 6,500 rpm and 391 lb.-ft. of torque at 5,200 rpm. Even with the mild Crane cam, the single plane and cavernous stock heads (260 cfm) allowed the Hemi to produce peak power at 6,500 rpm. After running the Mopar Performance intake, it was time to swap over to the stack injection setup and start adjusting the runner length.
Adding Stack Injection
After establishing the baseline with the Mopar Performance intake, off it came and on went the stack injection. The exotic induction system featured an individual throttle blade and full-radiused air horn for each cylinder. The full-radiused air horns were designed to maximize airflow to each cylinder.
Other nice features included a polished aluminum finish, a common vacuum/boost (MAP) port for all eight cylinders (to aid tuning), and a center-pivot linkage to help balance throttle openings. The system also featured billet fuel rails and a fuel pressure regulator, though we employed the unit on the dyno for our pressure regulation. We reused the 36-pound injectors run on the Mopar Performance intake, and after a little tuning, we were rewarded with peak numbers of 462 hp at 6,400 rpm and 418 lb.-ft. of torque at 5,300 rpm.
Not only did the peak power and torque numbers increase (always a good sign), but the power curve improved from top to bottom, from 3,000 rpm to over 6,000 rpm. The only thing better than more peak power is having more power everywhere! Apparently stack injection not only looks good, but it performs well too. We’ve run this same system on a much wilder Hemi combo and the induction easily exceeded 500 hp, so there is plenty left.
The question is now, what happens when we change the length of the runners?
Testing Runner Length
To test the effect of runner length, without having to redesign the intake, we simply added lengths of aluminum tubing to the stack injection. Yours truly made eight sections that increased the length by 2 inches, then 4 inches, then 6 inches.
After the first attempt, it became necessary to secure the new runners to the radiused air horns while not allowing the smaller diameter tubing to slide down and interfere with the throttle blades. Nothing a little tape, hose clamps and bailing wires (and zip ties) couldn’t cure!
After adding two inches, the peak torque increased to 427 lb.-ft., but peak power dropped to 454 hp. Increasing the length another 2 inches (total of 4) improved torque production to 432 lb.-ft., while another 2 inches (total of 6) pushed the peak torque to 443 lb.-ft.
In reality, the gains were more than just peak torque, as all but the longest runner added power through the majority of the power curve, at least up to 6,000 rpm. Only above 6,000 rpm did the original stack injection length offer more power. This indicates that the mild cam timing worked best when combined with the longer runner length, but even with wilder cam timing, the runners would still enhance power production in this rpm range. I guess length really matters!
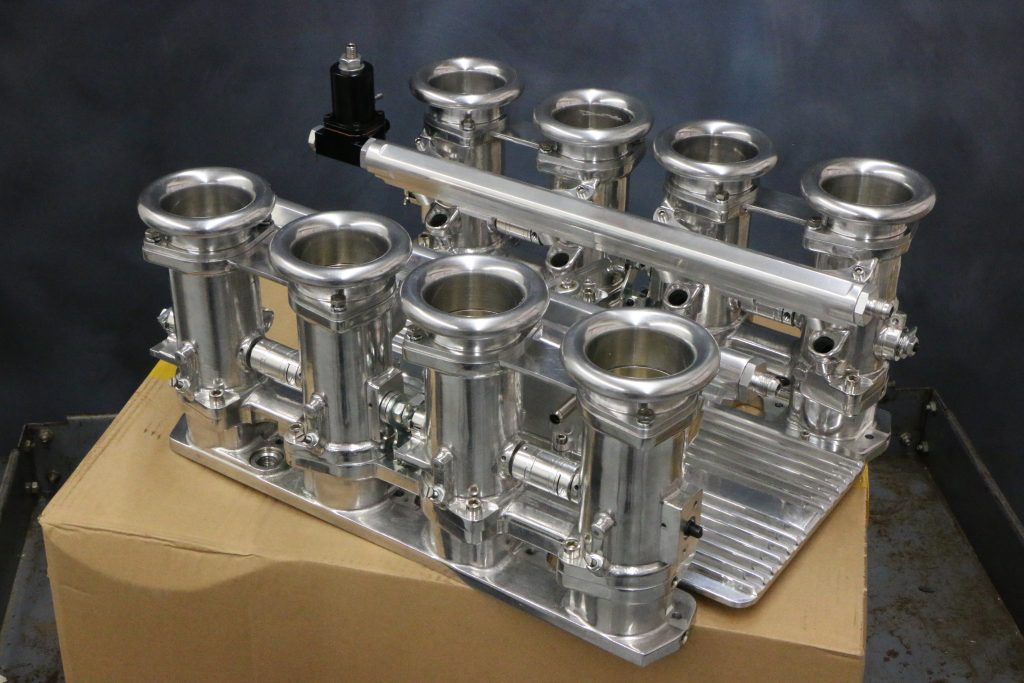
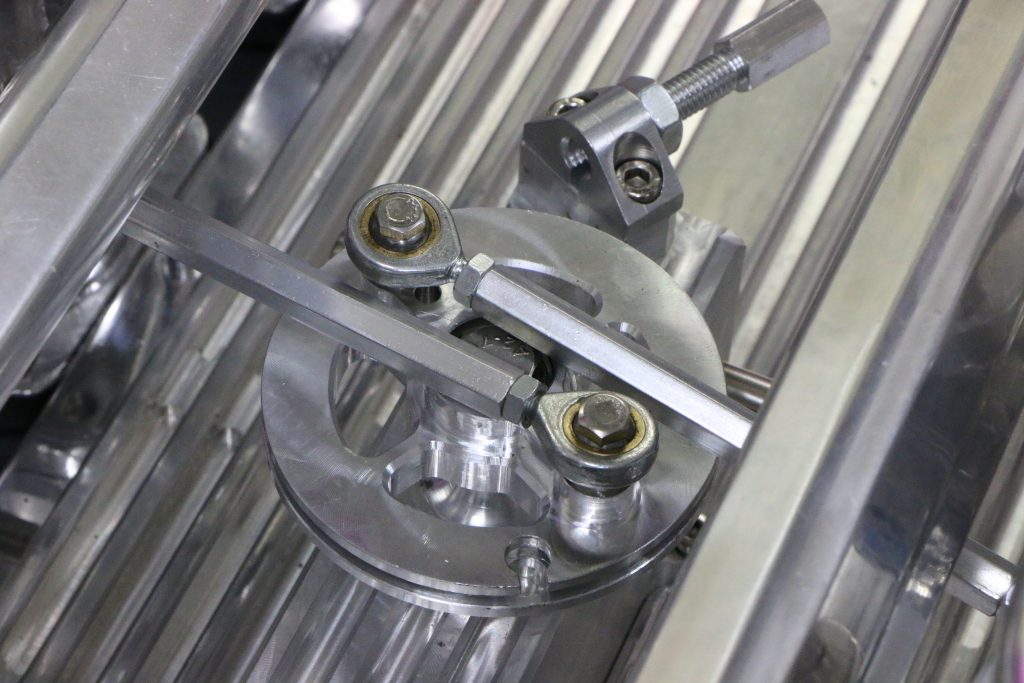
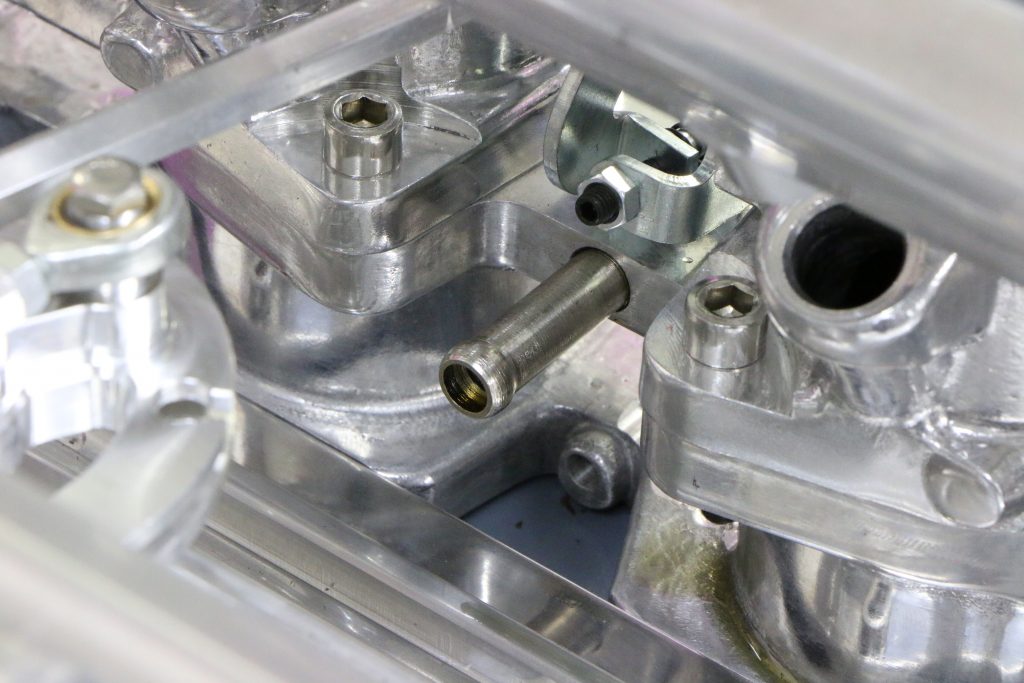
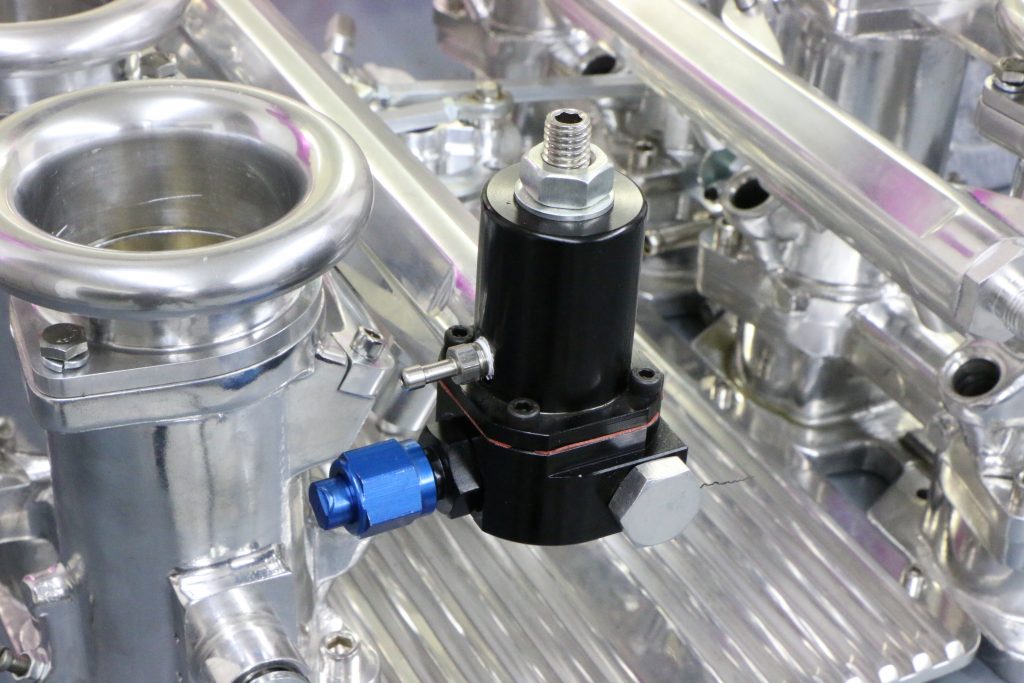
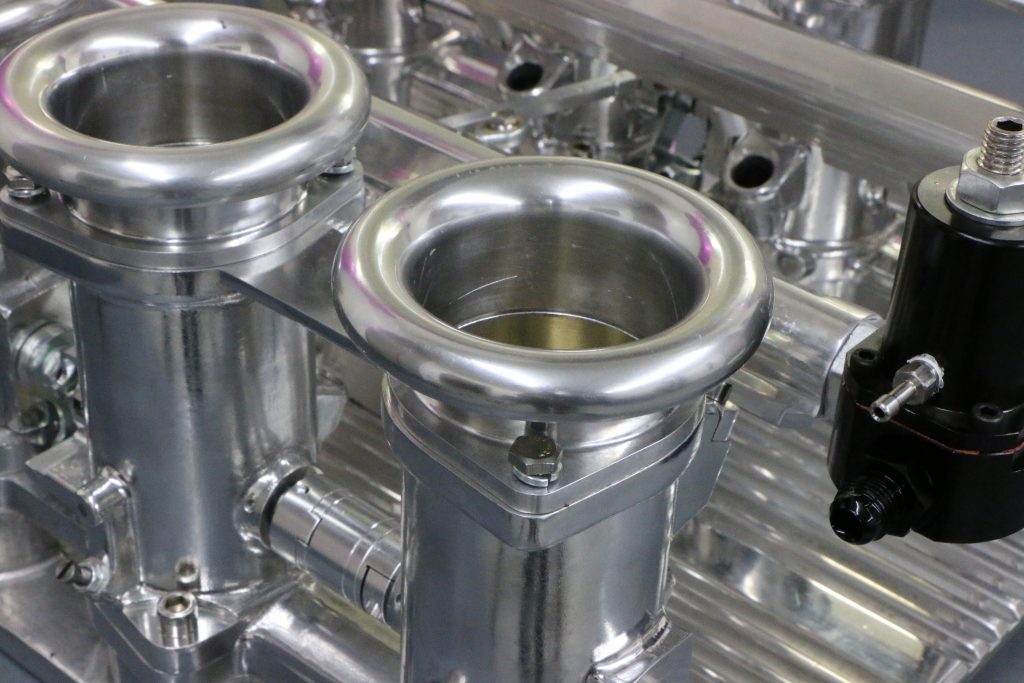
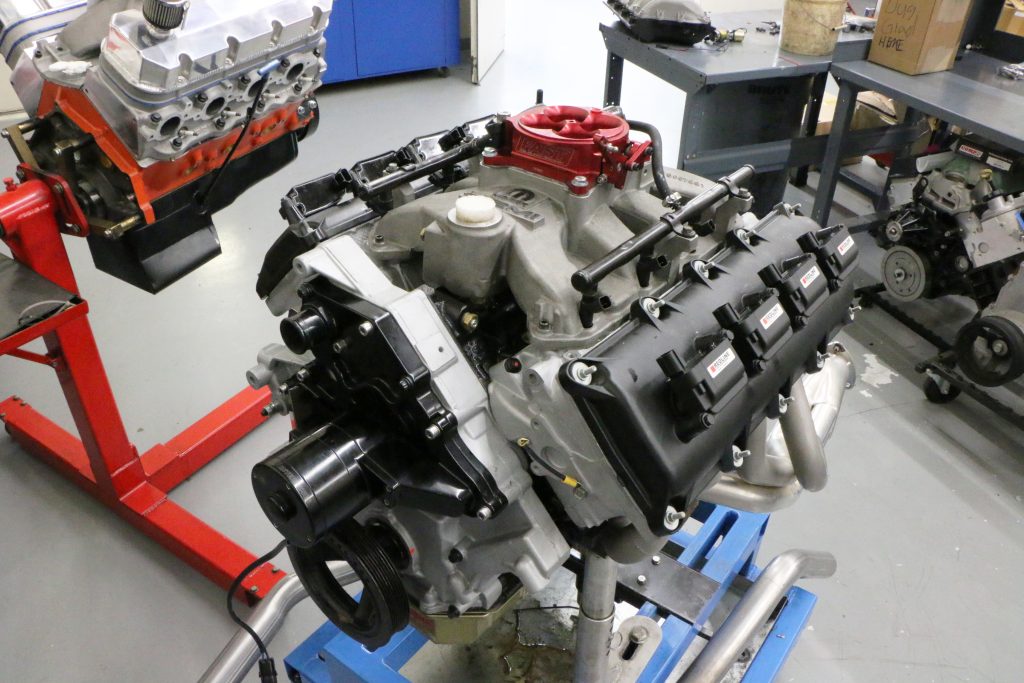
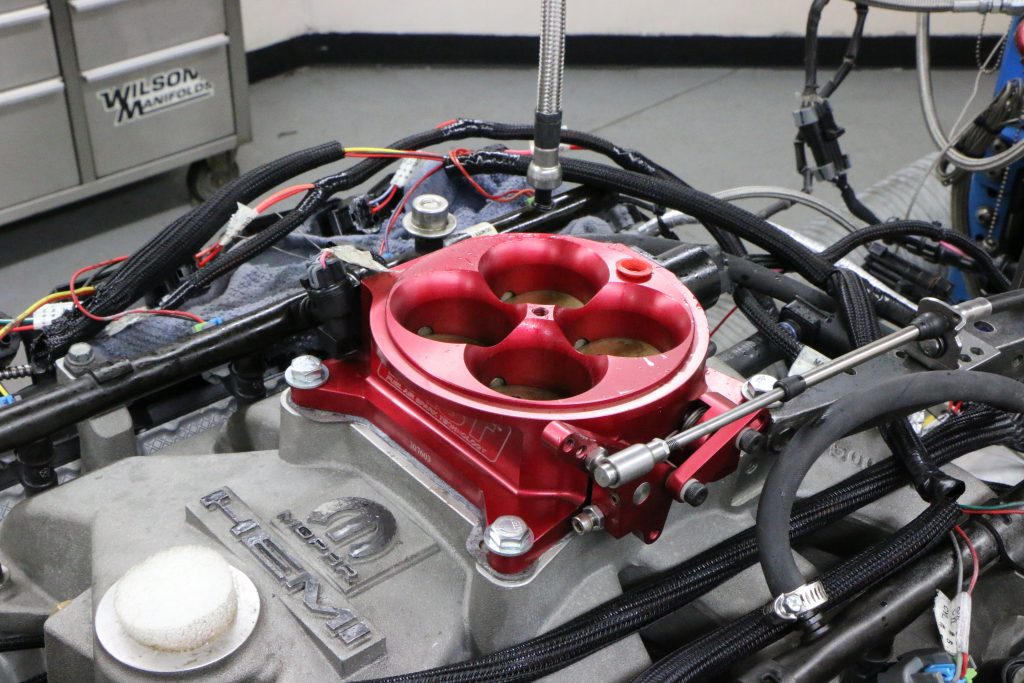
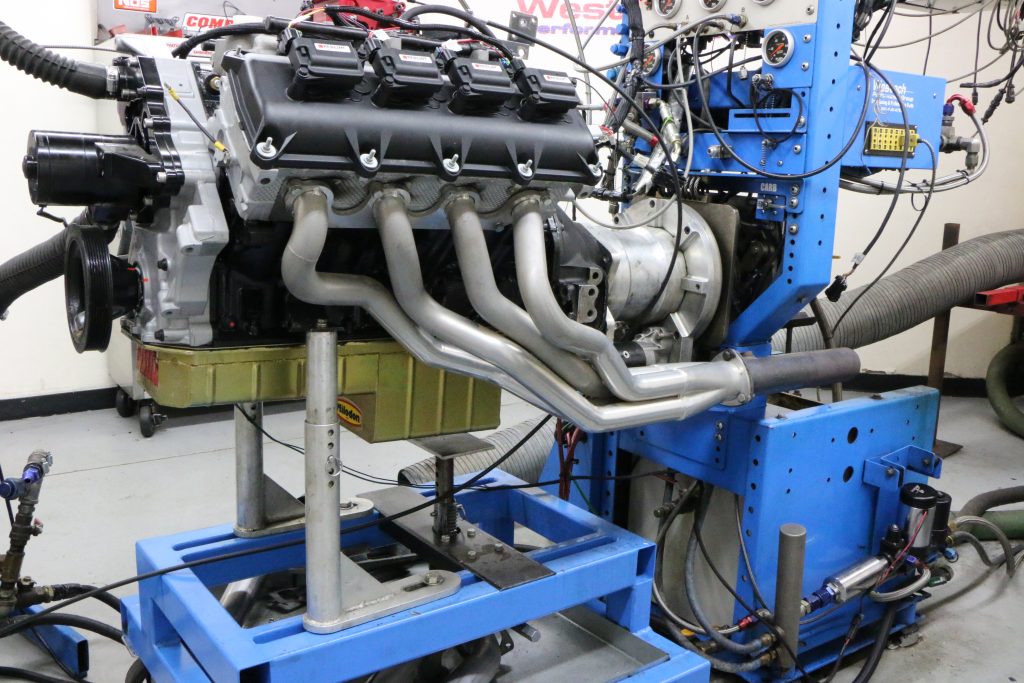
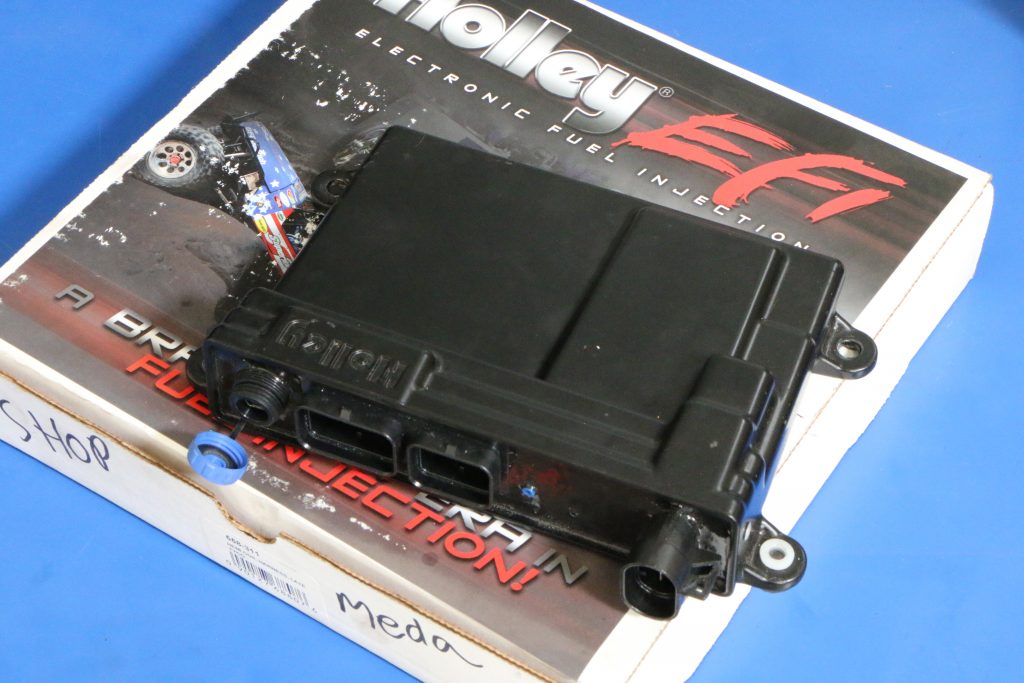
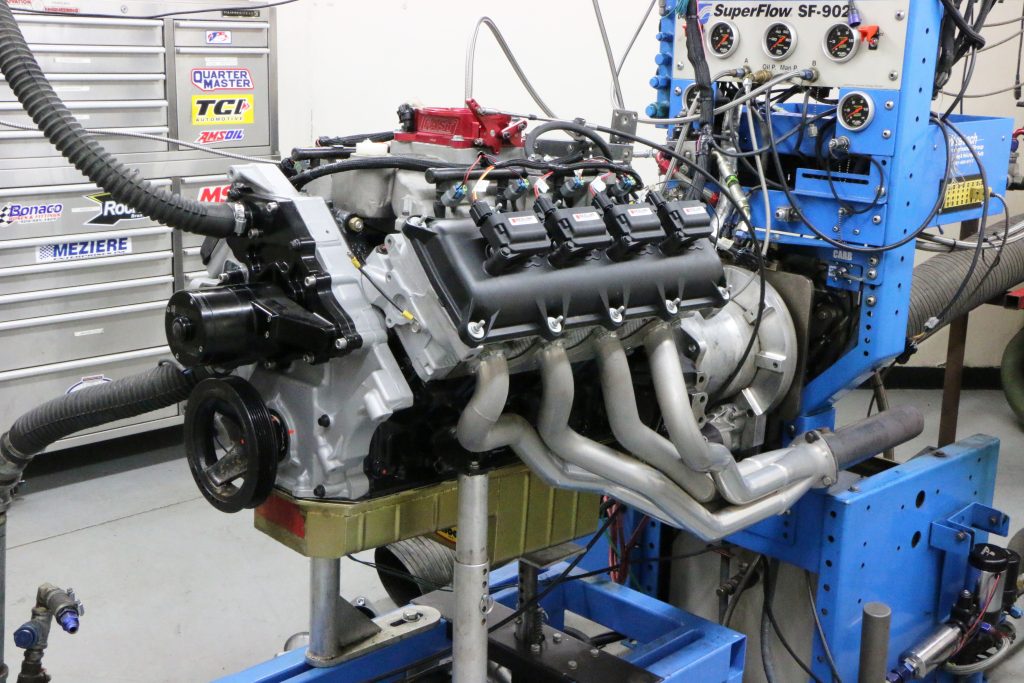
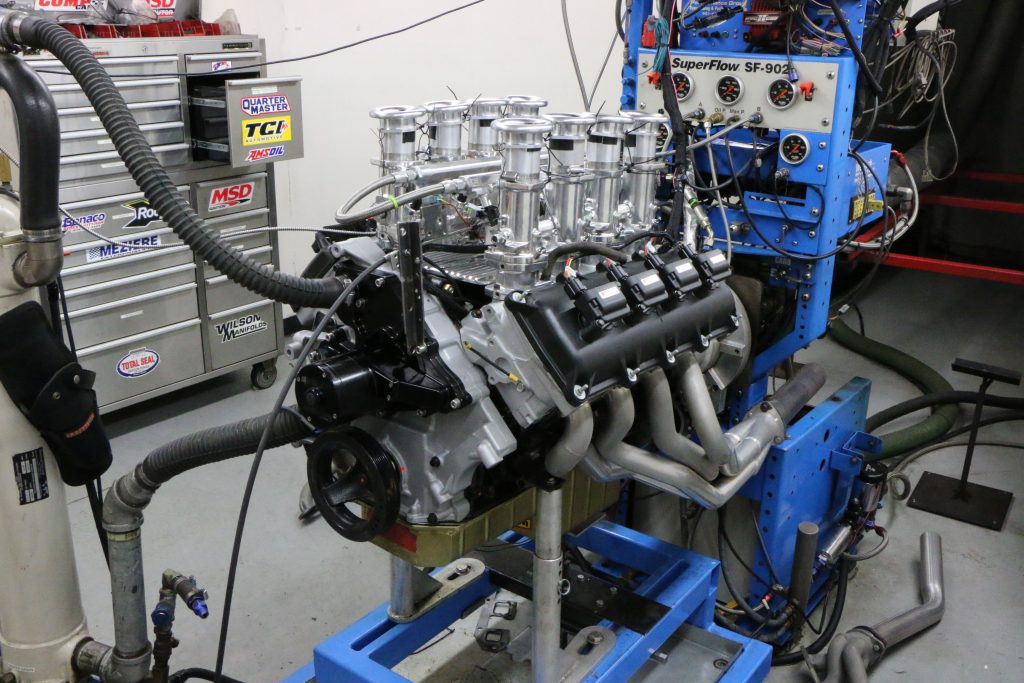
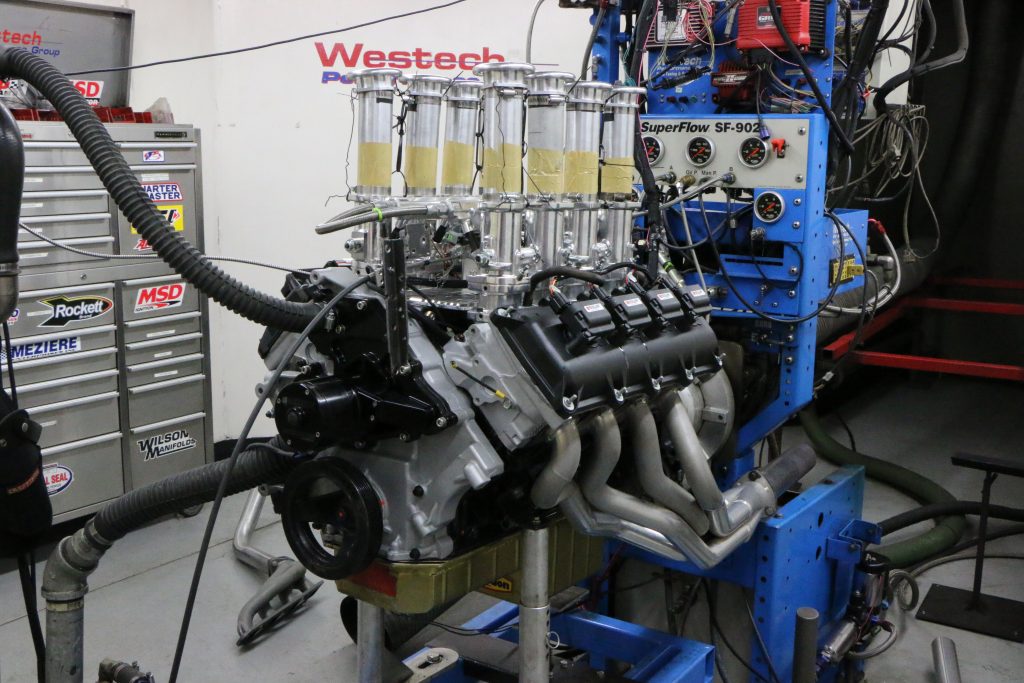
[…] The question is, does length matter? The answer is a BIG yes, especially if we are referring to intake runner length! You see, runner length plays a huge role in […] Read full article at http://www.onallcylinders.com […]
Richard you never leave a stone unturned in your methodical way of collecting data in the quest for fact based results. Now we have the long and short of it for optimal runner length.
The setup looks impressive and when properly tuned, should give the desired results. I will assume the quality control issues of the past have been corrected with their current products.
It’s always great to see your name as the author of technical articles for OAC. You provide a wealth of useful information in comparison to a few of the others that only come up with a paragraph or two. Thank You.
I can’t seem to find the mopar intake manifold you ran with the 4 barrel throttle body on it I’m building a 06 5.7 for boost and would very much appreciate it if you could help me out